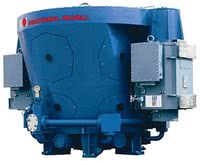
Fot. 1. Pompa płuczkowa, 6-tłokowa
Integralnym elementem szybów i platform wiertniczych są specjalne pompy, które dostarczają płuczkę wiertniczą umożliwiającą prowadzenie odwiertów. Pompy te stabilizują ciśnienie płuczki, która wywiera przeciwciśnienie na ściany otworu wiertniczego, zmniejsza tarcie przewodu wiertniczego, chłodzi świder i wynosi zwierciny.
W ramach omawianej aplikacji stworzono system detekcji przecieków w nowoczesnych, sześciotłokowych pompach płuczkowych, takich jak przedstawiona na pierwszej fotografii. Pompy te mają po 6 tłoków, zaworów dolotowych oraz zaworów wypływowych.
Tłoki są poruszane przez obracającą się, asymetryczną krzywkę. W celu realizacji aplikacji zaprojektowano własny, opatentowany system wykrywania przecieków, zbudowany w oparciu o sterowniki CompactRIO firmy National Instruments. Korzystając z akcelerometrów, monitoruje on wszystkie zawory danej pompy.
ZAUTOMATYZOWANY SYSTEM MONITOROWANIA
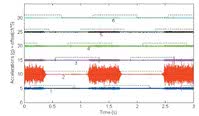
Rys. 2. Wibracje powstające w sytuacji, gdy przecieka zawór D2
Przeciekające zawory w pompach tłokowych są często wykrywane po długim czasie od wystąpienia usterki, gdy trudno już jest utrzymać stabilne ciśnienie płuczki wiertniczej. Taka sytuacja niestety wiąże się z powstaniem mniejszych lub większych uszkodzeń systemu wiertniczego.
Po stwierdzeniu zaistnienia poważnego przecieku, standardowa metoda jego lokalizacji polega na nasłuchiwaniu odgłosów dochodzących z poszczególnych stron pompy w trakcie jej pracy. Procedura ta jest jednak mało precyzyjna i bardzo trudno jednoznacznie określić miejsce przecieku, a tym bardziej odróżnić przeciek zaworu wlotowego od przecieku zaworu wylotowego.
Kolejnym problemem jest zagrożenie dla zdrowia człowieka, jakie powstaje w momencie manualnej detekcji i lokalizacji przecieków. Pompy płuczkowe mają zazwyczaj bardzo dużą moc, a ciśnienie na ich zaworach wylotowych dochodzi nawet do 350 barów.
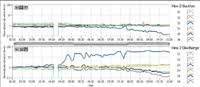
Rys. 3. Zmiana poziomu wibracji w czasie wraz z postępowaniem uszkodzenia zaworu D2
Dodatkowe oprzyrządowanie, znajdujące się często w pomieszczeniach z pompami, również pracuje bardzo głośno, w efekcie czego natężenie dźwięku w tych miejscach może przekroczyć 100 dBA, co stanowi zagrożenie dla słuchu pracowników analizujących stan pomp.
Problematyczny jest też fakt, że przecieki w zaworach bardzo szybko się powiększają, a proces ich ręcznego wykrywania, szczególnie gdy samo wystąpienie przecieku nie jest pewne, trwa dosyć długo i pozostawia mało czasu na wymianę zaworu. Dopiero zdalny zautomatyzowany system wykrywania przecieków rozwiązuje powyższe problemy.
WYKRYWANIE PRZECIEKÓW DZIĘKI WIBRACJOM
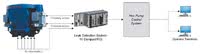
Rys. 4. Topologia omawianego systemu
Autorzy omawianej aplikacji odkryli możliwość lokalizowania przecieków za pomocą akcelerometrów w trakcie prowadzenia projektu monitorowania wibracji sześciotłokowych pomp płuczkowych. Wibracje rejestrowano w różnych miejscach szybu wiertniczego: zarówno na pompie, jak i na jej rurze wylotowej.
Ponadto mierzono ciśnienie na wlocie i wylocie, a także szybkość przepływu płuczki w różnych warunkach pracy pompy. Wibracje próbkowano z częstotliwością 25 kHz, co kilka minut tworząc 5-sekundowe nagrania. W jednym z przypadków zauważono, że wibracje znacznie zmieniły się w ciągu 15 minut, co - jak się okazało - było symptomem powstawania przecieku.
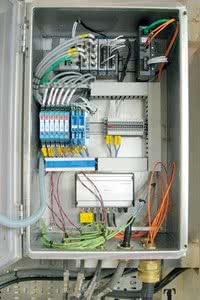
Fot. 5. Skrzynka z gotowym systemem
Po dokonaniu tego odkrycia przeprowadzono kolejne testy, aby sprawdzić możliwość wykrywania przecieków poprzez analizę wibracji. Na drugim rysunku przedstawiono wibracje zarejestrowane na wszystkich sześciu blokach zaworów w sytuacji, gdy drugi zawór wypływowy (D2) ma poważny przeciek.
Numery przy poszczególnych liniach reprezentują kolejne akcelerometry zamontowane przy blokach zaworowych o tym samym oznaczeniu. Liniami przerywanymi oznaczono stan pracy poszczególnych bloków zaworów - ich przebieg stworzono na podstawie sygnałów z czujników zbliżeniowych. Pozwalają one na łatwą interpretację zarejestrowanego sygnału wibracyjnego.
Gdy linie te mają stan wysoki, zawory zasysające danego bloku są zamknięte. Obniżenie poziomu linii przerywanych oznacza zamknięcie zaworów wypustowych następujące w momencie powracania odpowiadających im tłoków. Na wykresie da się też zauważyć, że wibracje spowodowane wyciekiem są nieco opóźnione względem wykresów otwarć i zamknięć zaworów.
Przesunięcie to wynosi około 25 ms i wynika z bezwładności zaworu oraz z faktu, że ściśliwość cieczy wymusza dodatkowy, skończony czas skoku tłoka przy kompresji i dekompresji płuczki w cylindrze. Analiza spektralna zarejestrowanych próbek wibracji wskazuje, że przeciek powoduje powstawanie silnego, szerokopasmowego szumu o częstotliwości od 3 kHz do częstotliwości Nyquista równej w tym przypadku 12,5 kHz (połowie częstotliwości próbkowania - 25 kHz). Łączny poziom szumu w trakcie przecieku zwiększał się o 30 dB.
SYSTEM DETEKCJI PRZECIEKÓW
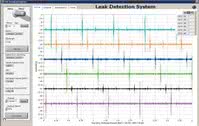
Rys. 6. Ekran użytkownika z zarejestrowanymi przebiegami w przypadku braku przecieków
W oparciu o zaprezentowane ustalenia opracowano system detekcji przecieków 6-tłokowych pomp płuczkowych w postaci samodzielnego modułu, w który można doposażyć obecne instalacje, tak jak to zilustrowano na rysunku 4.
W uproszczeniu składa się on z: akcelerometrów (po jednym na blok zaworów), czujnika zbliżeniowego mierzącego prędkość ruchu i fazę położenia tłoków pompy, czujnika ciśnienia wylotowego, wbudowanego systemu monitorującego (wykonanego w oparciu o sterowniki CompactRIO wraz z modułami do akwizycji sygnałów analogowych i zasilania akcelerometrów - NI 9234) oraz napisanego w
Rys. 7. Ekran użytkownika z zarejestrowanymi przebiegami w przypadku przeciekającego zaworu D3