Diagnostyka drgań źródłem ochrony w produkcji wody
| Wydarzenia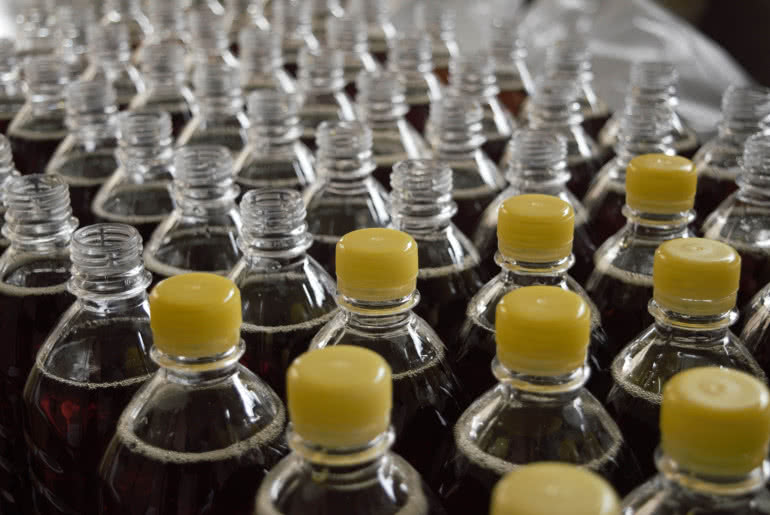
Choć w zakładach produkcyjnych z branży spożywczej i napojowej nie można całkowicie zapobiec zużywaniu maszyn i ich części, to można zaplanować ich konserwację lub naprawę. Dodatkowo, dzięki diagnostyce drgań, da się szybko wykryć potencjalne uszkodzenia. Podpowiadamy, jak przy stosunkowo niewielkiej inwestycji w nowoczesne czujniki drgań można unikać kosztownych awarii w fabryce, co finalnie ma również pozytywny wpływ na dobrą jakość produktu i środowisko.
Tylko w samym 2020 roku Polacy przeznaczyli na napoje bezalkoholowe 16,8 mld złotych. To jednak mniej o ponad 680 mln zł w porównaniu do roku wcześniej. Spadek wartości rynku o 4 punkty procentowe oznaczał jednocześnie obniżenie się sprzedaży w litrach, czyli wolumenu o 6 procent i spadek łącznej liczby sztuk sprzedanych produktów o 10 procent. Reasumując, w Polsce kupiono o 640 mln sztuk napojów mniej niż w 2019 roku. Tak wynika z danych NielsenIQ przytaczanych na początku tego roku.
Wprowadzenie podatku cukrowego w 2021 roku oznaczało dalszy trend spadkowy, zwłaszcza w przypadku rynku gazowanych napojów słodzonych, nieco lepiej potencjał popytowy prezentował się w przypadku butelkowanej wody mineralnej czy napojów izotonicznych. Producenci zaczęli także poszukiwać innowacyjnych i nowoczesnych rozwiązań systemowych, które mogłyby przynieść na tym polu intensywny rozwój w ulepszaniu produktów i dodatkowe oszczędności dla budżetów. A Przemysł 4.0. przynosi szeroką gamę nowinek technologicznych dla automatyki przemysłowej.
Źródło zmiany
Polscy przedsiębiorcy i zakłady rozlewnicze ulokowane na terenie naszego kraju wyraźnie szukają innowacyjnych rozwiązań i nowoczesnych zastosowań, które mogą wspierać linie produkcyjne. Inspiracją są tutaj między innymi systemy stosowane w fabrykach za naszą zachodnią granicą. Z roczną sprzedażą około 765 milionów litrów Hassia Group jest jednym z największych producentów wód mineralnych w Niemczech, oferując wody mineralne i napoje bezalkoholowe pod różnymi markami. Tylko w głównym zakładzie w Bad Vilbel w Hesji sześć linii rozlewniczych pracuje równolegle na trzy zmiany.
Potężne napędy transportują butelki na setki metrów przez poszczególne stacje - od płuczki, napełniacza, zakręcarki, po etykietowanie i pakowanie. Gdy butelki przechodzą z jednego przenośnika taśmowego na drugi, i uderzają o szynę prowadzącą lub o siebie, powstają punktowe obciążenia udarowe, które ostatecznie powodują silne, nieregularne wibracje na napędzie dla setek butelek. Łożyska przekładni i silnika muszą być zatem monitorowane, aby w odpowiednim czasie przewidzieć limit zużycia i móc przeprowadzić konserwację.
– Aby uniknąć przestojów spowodowanych nieplanowanymi awariami maszyn, warto zastosować stałą elektroniczną diagnostykę wibracyjną podczas butelkowania. Inżynierowie z Niemiec przyznają, że inwestycja zwróciła się już w fazie pilotażowej, bo wszelkie uszkodzenia napędu zostały zidentyfikowane i naprawione w odpowiednim czasie, zapobiegając w ten sposób nieplanowanym przestojom systemu i finansowym stratom – mówi Jacek Łobodziec, Inżynier ds. Aplikacji / Branża spożywcza, prezes firmy ifm electronic z siedzibą w Katowicach, która specjalizuje się w czujnikach i systemach dla produkcji.
Czujniki przyszłości
Czujniki umożliwiają diagnostykę drgań nawet w miejscach, do których ze względów bezpieczeństwa nie można dotrzeć podczas pracy. Dawniej monitoring prowadzony był ręcznie - do maszyny wysyłano ludzi, zadaniem których było osłuchiwanie pracy silnika, co było jednak czysto subiektywnym odczuciem.
– Trzy osoby słuchające stetoskopem napędu, silnika czy skrzyni biegów. Każda z nich odbierająca coś zupełnie innego. Podsłuchiwanie miało również główną wadę: słuchając kilka razy, zawsze warunki pracy były zmienne. Można było nasłuchiwać maszyny podczas jej obracania, ale nie w trakcie operacji butelkowania i napełniania. Są też instalacje, chociażby przy maszynie do usuwania etykiet, gdzie pracują wały, silniki i przekładnie, do których nie można dostać się podczas ich pracy – wyjaśnia Gerhard Simon, kierownik ds. utrzymania ruchu w firmie Hassia-Mineralquellen w Bad Vilbel.
Firma postawiła więc na pionierskie rozwiązanie dla diagnostyki wibracyjnej maszyn, oferowane przez koncern ifm electronic pod nazwą efector 800. Innowacyjne czujniki wykorzystano w jednym z systemów PET wielokrotnego użytku, gdzie w narzędzia wyposażono między innymi myjkę do butelek, maszynę do deetykietowania, odkręcacze czy strefę wypełniania i płukania. Czujniki w odpowiednim czasie rozpoznają, że osiągnięto granicę zużycia elementów danego bloku silnika czy skrzyni biegów.
Wartość alarmu
System składa się z czujników drgań oraz jednostek analizujących, monitorujących do 32 wskaźników obiektów, w maksymalnie 4 różnych punktach pomiarowych, do których podłączony jest czujnik. Te są wkręcane bezpośrednio do silnika lub bloku przekładni za pomocą specjalnych otworów. W trybie ciągłym rejestrują drgania na nieobrotowych powierzchniach maszyn. Działają na zasadzie pomiaru pojemnościowego, a dzięki specjalnej strukturze mikromechanicznej są wolne od zakłóceń.
Zintegrowany autotest zapewnia dodatkowe bezpieczeństwo, natomiast lampki sygnalizacyjne oraz wyjścia przełączające zgłaszają alarm wstępny lub główny. Operator sam może ustawić wartości graniczne (żółte linie dla alarmu wstępnego i czerwone linie dla głównego), a wszelkie zachowania wibracyjne można wizualizować na komputerze w sterowni. Inżynierowie sami mogą też wyznaczać i definiować poziomy, po przekroczeniu których konieczne jest na przykład smarowanie lub wymiana komponentów na linii produkcyjnej.
Już pierwszy test praktyczny w niemieckiej fabryce krótko po instalacji systemu dał wymierny efekt. – Po kilku tygodniach odnieśliśmy pierwsze sukcesy, gdy diagnostyka wibracyjna wykryła zbliżający się przestój systemu z powodu zakłóceń mechanicznych. Żółte lampki sygnalizacyjne uruchomiły alarm wstępny. Następnie maszyna została dokładnie sprawdzona przez weekend i stwierdzono, że gwiazda transferowa, w której butelki są przenoszone z płuczki do napełniacza, miała łożysko o zwiększonym luzie. Dodatkowo wał napędzający płuczkę i blok zaczynał tracić krągłość, co powodowało wibracje w całym systemie. Udało nam się naprawić usterkę w odpowiednim czasie i tym samym zapobiec dużej awarii systemu i przestoju w środku produkcji, co przy pracy na trzy zmiany miałoby oczywiście fatalne konsekwencje i pociągnęłoby za sobą ogromne koszty – dodaje Gerhard Simon.
Maszynowa precyzja
Czujniki drgań zamontowane na napędach wykrywają nawet najmniejsze drgania. Oprócz wyświetlania stanu wibracji za pomocą lampki kontrolnej na miejscu, jednostka oceniająca może być również połączona w sieć z centrum sterowania.
– Kompleksowy cel działania całego systemu czujników i akcesoriów to możliwość stałego śledzenia procesów konserwacji online. Monitoring za pomocą diagnostyki wibracyjnej to także szansa na dokumentację danych i analizę, które zdarzenie lub uszkodzenie spowodowało przestój w parku maszyn i co trzeba zrobić, aby zoptymalizować system. Ewidencjonowanie tych czynności potwierdza, że inwestycja w system diagnostyczny się opłaciła – tłumaczy Jacek Łobodziec.
Przykład praktycznego wykorzystania niezawodności procesu poprzez stałą diagnostykę drgań został już wyróżniony w certyfikacji powszechnie stosowanej w przemyśle spożywczym i corocznym audycie International Featured Standards. W raporcie podkreślono, że dzięki monitorowaniu zakładu za pomocą tak innowacyjnych systemów, dział utrzymania ruchu ma również wpływ na bezpieczeństwo i jakość produktów. W przypadku przestoju w zakładzie, linię produkcyjną trzeba bowiem opróżnić, aby w przypadku naprawy uniknąć m.in. zanieczyszczenia butelek. Sama naprawa, choć zajmuje tylko 30 minut, może spowodować nieplanowany przestój do 2 godzin, co skutkuje już niepotrzebnymi kosztami. Technologia czujników zapobiega pojawianiu się takich czynników.