Degradacja jakości regulacji z wykorzystaniem PID
| Technikaźródło Siemens PID są już od kilkudziesięciu lat standardem przemysłowym i wciąż najczęściej wykorzystywanym typem regulatorów. Są one stosunkowo proste do uruchomienia, uniwersalne i dobrze znane automatykom. Korzystając z nich należy jednak mieć świadomość możliwej degradacji jakości regulacji w czasie, co związane jest zwykle ze zmianami parametrów rzeczywistego układu regulowanego.
Na rys. 1 został przedstawiony schemat układu regulacji. W omawianym przypadku wartość zadana określa pożądany poziom sygnału wyjściowego układu. Sygnał wyjściowy jest mierzony przez czujnik i w sprzężeniu zwrotnym zostaje przekazany na wejście układu. Różnica sygnałów yREF i y, określana mianem uchybu, podawana jest na wejście regulatora, który na jej podstawie oblicza odpowiedni sygnał regulujący proces. Sygnał ten przesyłany jest do urządzenia wykonawczego, które zapewnia pożądane działanie obiektu regulacji.
Algorytm regulacji PID
Podstawowa idea działania regulatora PID znana jest wszystkim automatykom. Regulator ten składa się z trzech bloków – pierwszym i najczęściej wykorzystywanym jest blok proporcjonalny, wzmacniający sygnał uchybu, co pozwala na sprowadzenie sygnału wyjściowego w pobliże wartości zadanej. Ponieważ sama regulacja proporcjonalna uniemożliwia dokładne śledzenie wartości zadanej i tym samym całkowitą likwidację uchybu w stanie ustalonym, drugi element regulatora PID stanowi układ całkujący (integrator), który w sposób ciągły całkuje sygnał uchybu. Osiąga się dzięki temu taki sam efekt, jak przy wysokim współczynniku wzmocnienia w oddzielnym regulatorze proporcjonalnym, jednak bez utraty stabilności. W momencie gdy sygnał uchybu zrównuje się z zerem, wyjście sekcji proporcjonalnej także jest równe zero, jednak wyjście integratora ze względu na stałą czasową może w dalszym ciągu mieć znaczącą wartość i wciąż oddalać się od wartości zadanej, ale w przeciwnym kierunku.
Im szybciej wzrasta uchyb tym większe jest przeregulowanie, co może prowadzić do niestabilności. Dłużej trwa też ustalenie się sygnału wyjściowego na odpowiednim poziomie. Dlatego trzecim elementem regulatora PID jest część różniczkująca, która zmniejsza czas potrzebny sygnałowi wyjściowemu na powrót do wartości zadanej. Ogranicza ona także początkowe przeregulowanie i ma efekt stabilizacyjny, dzięki tłumieniu oscylacji. To pozwala ustawić większą wartość współczynnika wzmocnienia, niż w przypadku oddzielnego regulatora proporcjonalnego i zmniejsza czas odpowiedzi układu na zaburzenia.
Spadek jakości w czasie
Przez lata wykorzystywania regulatorów PID zaobserwowano, że w przypadku braku ingerencji w ich nastawy, jakość regulacji spada co pół roku średnio o kilkadziesiąt procent. Oznacza to, że po roku bez obsługi technicznej nastąpić może nieakceptowalna strata jakości regulacji w stosunku do momentu wykonania układu lub jego ostatniej konserwacji.
Takie zachowanie układu regulacji wynika m.in. z faktu, że rzeczywisty proces zmienia się w czasie, natomiast jego model, w odniesieniu do którego dobierane były nastawy regulatora PID, pozostaje stały. Ten ostatni stanowi bowiem tylko matematyczną reprezentację zachowania procesu. Dlatego wymaga się, aby był on jak najbardziej uproszczony przy jednoczesnym wystarczającym odwzorowywaniu zachowania się procesu w czasie. Z tego powodu oraz w wyniku zastosowanej metody regulacji adaptacyjnej nie uwzględnia się zmienności jego parametrów, a także częściowo pomija się dynamikę. Natomiast rzeczywisty proces jest często wyższego rzędu lub charakteryzuje się nieliniowością, czego wynikiem jest zmiana charakterystyk, w zależności od punktu pracy.
Model procesu może być opisany przez takie parametry jak np. współczynnik wzmocnienia, czas opóźnienia oraz stała czasowa. Wzmocnienie procesu (k) to współczynnik określający zmianę sygnału wyjściowego w stosunku do zmiany sygnału sterującego. Im jest ono większe, tym bardziej sygnał regulowany będzie reagował na zmianę sygnału. Czas opóźnienia (T0) określa okres oczekiwania przed zmianą sygnału wyjściowego. Opisuje on więc szybkość reakcji na zadane sterowanie. Stała czasowa (T) jest natomiast miarą pojemności procesu i określa po jakim czasie od ustania opóźnienia sygnał wyjściowy osiągnie 0,632 jego wartości końcowej po skokowej zmianie sygnału sterującego.
Procesy rzeczywiste
Jak wspomniano wcześniej, parametry procesu rzeczywistego ulegają zmianom, więc następuje pogłębianie się w czasie różnicy pomiędzy wartościami rzeczywistymi, a jego założonym modelem. Przykładowymi czynnikami, które mogą zmienić wzmocnienie, opóźnienie oraz stałą czasową procesu mogą być: zużycie elementów napędowych w wyniku zmian tarcia lub korozji, wymiana elementów urządzenia, zmiana punktu pracy, uszkodzenie, czynniki zakłócające pracę elementów, takie jak zanieczyszczenia, czy choćby nowe procedury operacyjne.
Na rys. 2 przedstawiono charakterystykę dynamiczną modelu procesu niskiego rzędu, która pomaga powiązać jego parametry z pogorszeniem się jakości regulacji w czasie. Jest on dużo prostszy niż matematyczne modele wyższych rzędów, jednak może być wystarczająco precyzyjny do osiągnięcia dobrej jakości. Wykres zawiera przykładową charakterystykę dynamiczną dla umiarkowanej wartości współczynnika wzmocnienia k oraz charakterystyki, które są wynikiem wpływu wymienionych czynników na zachowanie rzeczywistego procesu, przy braku ingerencji w nastawy regulatora.
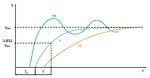
Innymi słowy jeśli z jakiegokolwiek powodu wzmocnienie rzeczywistego procesu, czas opóźnienia, stała czasowa lub ich kombinacje zmienią się w sposób istotny, układ zamknięty może być w skrajnym przypadku niestabilny, natomiast najczęstszym skutkiem będzie utrata jakości.
Sytuacja w przemyśle
Niezależne badania dowodzą, że w większości procesów jedynie niewielki odsetek pętli regulacyjnych ma właściwie dobrane parametry. Nawet jeśli statystycznie jedna czwarta pętli regulacyjnych działa lepiej po przejściu z regulacji ręcznej na automatyczną, niekoniecznie uzyskują one maksymalną wydajność. W pozostałych przypadkach regulator zamiast poprawiać, pogarszał jakość regulacji procesu.
Nieodpowiednia regulacja może mieć tym czasem wpływ na oscylacje wielkości procesowej, wzrost czasu regulacji i przeregulowanie, ale też większy pobór energii i surowców, co skutkować może zwiększaniem się kosztów. Może to też, w przypadku konkretnej aplikacji, wiązać się przykładowo z przekroczeniem dopuszczalnej temperatury w procesie produkcyjnym czy innymi zakłóceniami. Celem optymalizacji jest minimalizowanie tych problemów oraz maksymalizacja wydajności, jakości produkcji oraz szybkości reakcji na zmiany następujące w procesie. Najczęściej stosowane w takich sytuacjach metody doboru nastaw regulatorów polegają na kolejnych próbach i błędach lub też metody analityczne, takie jak Zieglera-Nicholsa. Istnieją również zaawansowane narzędzia informatyczne, z których dwa opisane zostały w kolejnym rozdziale.
Utrzymanie odpowiedniej wydajności
W celu osiągnięcia zadowalającej jakości układu regulacji istotne jest zapewnienie korekcji nastaw regulatora PID w przypadku zaistnienia jakiejkolwiek zmiany w pętli regulacyjnej. Na rynku istnieją gotowe rozwiązania, które mogą zostać zastosowane w tym celu. Jednym z nich jest oprogramowanie PlantTriage firmy ExperTune (www.expertune.com/planttriage.html), które dokonuje ponad 40 oddzielnych pomiarów dla każdej pętli regulacyjnej wykorzystywanej na obiekcie. Wszystkie pomiary są archiwizowane w celu późniejszego wyznaczenia trendów każdej mierzonej wielkości. Wyniki mogą być przeglądane jeśli zaistnieje taka potrzeba i są dostępne za pośrednictwem mechanizmu OPC. Oprogramowanie to zapewnia także m.in. wykrywanie oscylacji i diagnostykę. Wszystkie pomiary dokonywane są w trakcie pracy urządzeń.
Drugim, konkurencyjnym rozwiązaniem jest oprogramowanie Matrikon Control Performance Monitor (www.matrikon.com/control-monitoring.aspx), które zapewnia dobór parametrów układu regulacji, modelowanie oraz testowanie wydajności, gromadzenie i analizowanie danych, dzięki czemu gwarantuje w długim okresie wzrost wydajności układu regulacji PID.
Powyższe oprogramowanie pozwala inżynierowi na dostęp do raportów przez przeglądarkę internetową, co umożliwia obserwację elementów wymagających dokonania korekcji w celu maksymalizacji zysku ekonomicznego. Ponadto oprogramowanie to jest przydatne do planowania obsługi serwisowej – zbiera dane, wykonuje obliczenia statystyczne oraz dostarcza graficzną reprezentację danych do całkowitej i efektywnej analizy procesu. Warto dodać, że funkcjonalność pozwalającą na utrzymanie odpowiedniej jakości regulacji zawierają także niektóre duże, modułowe pakiety oprogramowania.
Grzegorz Michałowski