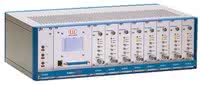
Fot. 1. Wielokanałowy kontroler capaNCDT 6500 do czujników pojemnościowych
Poza czujnikami kontaktowymi, obecnie powszechnie stosuje się metody bezkontaktowe do kontroli przemieszczenia, odkształceń, rozciągania, odległości, pozycji oraz innych wielkości geometrycznych. W zależności od zasady pomiarowej, czujniki bezkontaktowe oferują kluczowe, z punktu widzenia szybko rosnącej zautomatyzowanej produkcji i kontroli procesu, zalety. Czujniki te często mierzą szybciej, bardziej precyzyjnie i pewniej niż czujniki kontaktowe.
Dane pomiarowe są dostępne w czasie rzeczywistym, aby automatycznie regulować i nadzorować produkcję. Kontrola jakości przeprowadzana jest nie tylko w odniesieniu do gotowych produktów, lecz też procesów produkcyjnych. Jej celem jest podniesienie jakości produktu, zmniejszenie odpadów do minimum i obniżenie całkowitego kosztu produkcji.
Na wstępie została podkreślona łatwość "integracji czujnika". Można zadać pytanie, w jaki sposób użytkownik ma rozumieć ten termin? Z jednej strony odnosi się on do fizycznej integracji. Czy czujnik jest w stanie wytrzymać w środowisku o wysokim stopniu zabrudzenia, wszechobecnych smarach, narażony na ekstremalne fluktuacje temperatury i wibracje? Czy rozmiar i kształt czujnika może być dostosowany do indywidualnych warunków montażowych?
Z drugiej strony, odnosi się on do integracji danych: "inteligentne" czujniki z wbudowanym kontrolerem przetwarzają dane pomiarowe i przesyłają je do systemu kontroli. Interfejsy dla wyjścia czasu rzeczywistego, takiego jak Ethernet i EtherCAT, przyczyniają się do optymalizacji integracji danych w przepływie danych procesowych maszyny. W tym artykule przyjrzymy się bliżej systemom wiroprądowym i pojemnościowym oraz przedstawimy różnice pomiędzy nimi na przykładzie zastosowań w przemyśle.
CZUJNIKI WIROPRĄDOWE
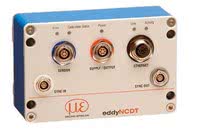
Fot. 2. Kontroler eddyNCDT 3100 do czujników wiroprądowych
Środowisko przemysłowe jest często brudne, zapylone, z dużą ilością wilgoci i smarów, a maszyny muszą być odporne na duże wahania temperatur. W istniejących aplikacjach często pozostaje bardzo niewiele przestrzeni montażowej dla czujników. Dlatego do pomiaru przemieszczenia, odległości i pozycji w takich warunkach, idealnie nadają się czujniki wiroprądowe, gdyż mogą być one zredukowane do bardzo niewielkich rozmiarów oraz są odporne na wysokie ciśnienie.
Czujniki te przeznaczone są do pomiarów względem elementów metalowych. Mierzone obiekty mogą mieć ferromagnetyczne oraz nieferromagnetyczne właściwości. Z uwagi na bezkontaktową zasadę pomiaru nie zużywają się mechanicznie.
Cewka, która jest wbudowana w czujniku, jest zasilana przez prąd zmienny o wysokiej częstotliwości. Pole magnetyczne cewki indukuje prądy wirowe w mierzonych, metalowych elementach, które w rezultacie powodują zmianę impedancji cewki. Zmiana ta powoduje wytworzenie sygnału elektrycznego, proporcjonalnego do odległości pomiędzy mierzonym obiektem a głowicą czujnika.
Wysokoczęstotliwościowe pole elektromagnetyczne emitowane przez cewkę czujnika z łatwością przenika przez niemetalowe materiały, umożliwiając pomiar nawet przy wysokim poziomie zabrudzenia (pyły i brud), ciśnienia lub smarów. Ta właściwość umożliwia też realizację pomiarów metalowych obiektów, które są pokryte tworzywem sztucznym np. w przypadku pomiaru grubości warstw lub podłoża. Czujniki wiroprądowe mogą być stosowane w wysokich temperaturach.
Rozszerzając zakres zastosowań czujników wiroprądowych, firma Micro-Epsilon opracowała technologię ECT (Embedded Coil Technology), która nie wymaga konwencjonalnie nawiniętej cewki. Zamiast tego dwuwymiarowa cewka jest osadzona w materiale nieorganicznym, co zapewnia stabilny kształt oraz temperaturę. Za pomocą tych czujników można uzyskać całkowicie nowe kształty geometryczne i wymiary.
Cała elektronika pomiarowa jest zintegrowana w czujniku. Co za tym idzie, czujniki ECT mogą być przystosowane do specjalnych warunków montażowych. Są też odpowiednie do zastosowań w bardzo wymagających aplikacjach, takich jak kontrola równoległości powierzchni ciężkich walców produkcyjnych czy pomiar prędkości wirowania łopat turbiny sprężarki w silniku wysokoprężnym.
CZUJNIKI POJEMNOŚCIOWE
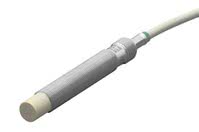
Fot. 3. Czujnik wiroprądowy eddyNCDT 3001 ze zintegrowanym kontrolerem
Ze względu na unikalną zasadę działania trójelektrodowego kondensatora z pierścieniem ekranującym, pojemnościowe czujniki przemieszczenia zachowują liniowość w odniesieniu do wszystkich metali. Czujnik działa jak elektroda; obiekt pomiarowy stanowi elektrodę przeciwstawną. Jeśli prąd zmienny przepływa przez kondensator czujnika przy stałej częstotliwości i amplitudzie, to amplituda napięcia zmiennego czujnika jest proporcjonalna do odległości mierzonego obiektu.
Pojemnościowy system pomiarowy - jako proces elektromagnetyczny - mierzy wszystkie metale ze stabilną czułością i liniowością. Czujniki pojemnościowe mogą mierzyć również materiały izolacyjne. Jednakże wymagane jest czyste środowisko pracy, gdyż jeśli w przestrzeni zostanie wykryty dodatkowy dielektryk, zniekształci to wyniki pomiarów.
Czujniki pojemnościowe są jedną z najprecyzyjniejszych technologii pomiarowych na rynku, pozwalając na osiągnięcie dokładności daleko poniżej jednego nanometra. Stosowane są wszędzie tam, gdzie wymagane są precyzyjne i stabilne wyniki, aby móc zmierzyć wibracje, odkształcenia i grubość.
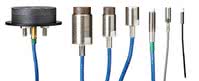
Fot. 4. Czujniki wiroprądowe z serii eddyNCDT
Jedną z aplikacji, gdzie zastosowano precyzyjne czujniki capaNCDT, jest produkcja płyt CD, które są wytwarzane metodą tłoczenia. Tłoczona forma jest otrzymywana w kilku krokach poprzez galwanizację. W pierwszym kroku tzw. father master (matryca ojciec) jest powlekana warstwą stopu niklowego na dysk krzemowy lub szklany, od którego jest następnie oddzielana i wykorzystywana do tłoczenia dysków. W przypadku większych nakładów kopii, w procesie galwanizacji tworzone są dodatkowe lustrzane odbicia, zwane matkami.
Aby kontrolować proces galwanizacji, czujniki pojemnościowe mierzą grubość i profil matrycy pomiędzy kolejnymi etapami produkcji. Jeden z czujników jest umieszczony nad, a drugi pod matrycą, która jest przesuwana pomiędzy czujnikami podczas pomiaru. Grubość matrycy jest obliczana na podstawie różnicy pomiędzy wartościami dwóch zmierzonych odległości. Celem określenia profilu grubości matryca jest obracana. Czujniki pojemnościowe mierzą odległość do matrycy z częstotliwością 2000 Hz i dokładnością do nanometrów.
WŁAŚCIWY WYBÓR

Fot. 5. Czujniki pojemnościowe z serii capaNCDT
Bezkontaktowe technologie pomiarowe oferują wiele korzyści, takich jak wysoka precyzja, kompaktowe wymiary czy szybkie przetwarzanie danych. Użytkownik może wybierać spośród różnorodnych technologii pomiarowych. Każda z nich ma swoje wady i zalety, które należy starannie rozważyć. Wymienione wyżej metody pomiarowe są odpowiednie do aplikacji, gdzie zakres pomiarowy ogranicza się do kilkudziesięciu mm.
Jednak gdy istnieje potrzeba realizacji pomiarów w zakresie do kilkuset milimetrów, zwykle stosuje się czujniki optyczne. Chcąc wybrać optymalne rozwiązanie do danej aplikacji, zwłaszcza w przypadku niestandardowych wymagań takich jak wyższa rozdzielczość, wytrzymałość czy specjalny sposób montażu, warto skonsultować się z doświadczonym specjalistą.
P.P.H. WObit E. K. J. Ober s.c.
www.wobit.com.pl