- Oferujemy kompleksowe rozwiązania dla producentów pojazdów oraz dostawców usług transportowych w czterech obszarach technologicznych, takich jak sterowanie ruchem pojazdów, zintegrowane bezpieczeństwo, zautomatyzowana jazda oraz elektromobilność. Technologia ZF umożliwia pojazdom "widzenie, myślenie i działanie" (ang. "see, think, act") – mówi Wojciech Jasiński, starszy automatyk obróbki maszynowej w ZF.
W 2017 roku powstała w gliwickim zakładzie koncepcja wprowadzenia automatyzacji linii, mająca na celu zwiększenie produkcji i poprawę jakości. Celem automatyzacji była także poprawa efektywności i podniesienie wskaźników produkcyjnych. Poprawa jakości wynikać miała ze zwiększenia sterylności procesów produkcyjnych.
- Zachowanie wysokich standardów czystości części jest priorytetem w produkcji elektrycznych układów wspomagania, gdyż nawet najmniejsze zanieczyszczenia mogą prowadzić do zwarcia układów PCB. Sama myjnia komponentów wymagała zwiększenia wydajności oraz niezawodności procesów. Nasz wybór padł na myjnię tunelową, w której mycie i suszenie podzielone jest na kilka etapów. Myjnia ta zapewnia uzyskanie takiego samego czasu cyklu pracy przy liczbie maszyn zredukowanej do dziewięciu – mówi Wojciech Jasiński.
W procesie wyboru dostawcy zdecydowano się na rozwiązania oferowane przez firmę NOYEN. Podczas projektowania zautomatyzowanej linii myjącej wykorzystane zostały rozwiązania Siemensa: Solid Edge do modelowania 3D, Teamcenter do przepływu dokumentacji oraz TIA Portal.
Pierwszy element instalacji – myjnia – zamówiony został już w lutym 2018 r. W zautomatyzowanej linii wykorzystana została myjnia z serii NOYEN Ekspert zapewniająca wymaganą wysoką klasę czystości. Następnie dostarczane były: system paletyzacji, myjka do przekładek, system transportu wraz z automatyzacją pierwszej obrabiarki i automatycznym znakowanie kodu DMC na odlewach. Automatyzacja pierwszej obrabiarki odebrana została w połowie 2020 r. Podczas wdrożenia do najważniejszych wyzwań należało m.in. zapewnienie możliwości rozbudowy i modułowości. Ta część realizacji, dotycząca działu obróbki, stanowiła najistotniejszą część projektu.
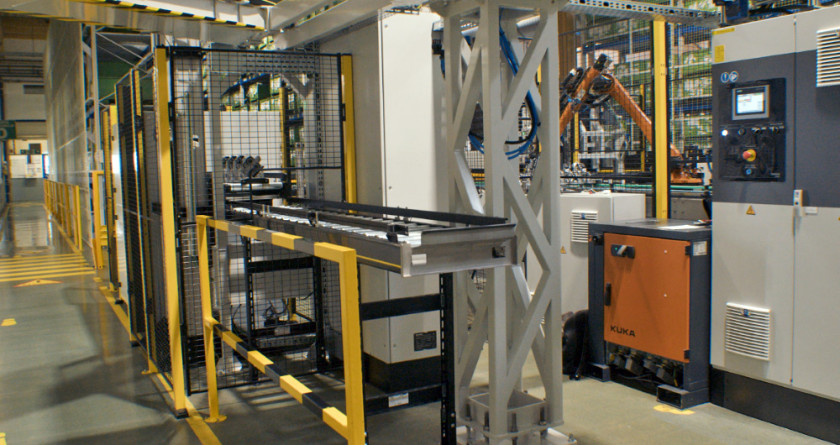
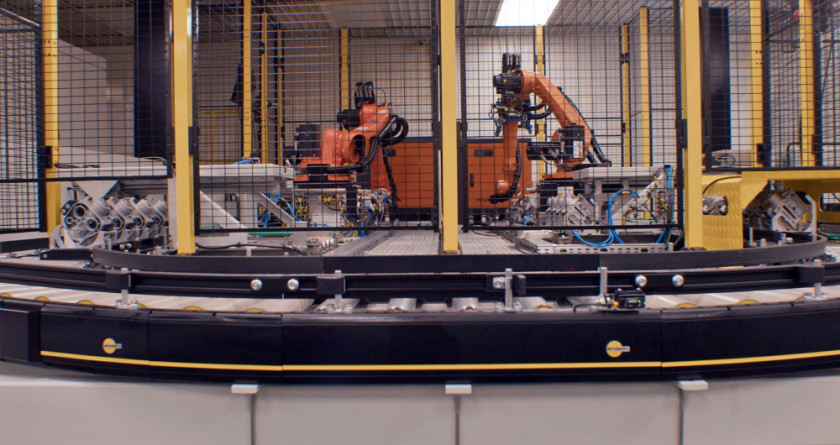
Sterowanie całej linii realizowane jest poprzez zaawansowany sterownik SIMATIC S7-1500F. Wizualizacja procesu oraz wprowadzanie nastaw jest możliwe dzięki komputerowi panelowemu SIMATIC panel PC. Wymiana danych pomiędzy poszczególnymi urządzeniami automatyki bazuje na standardzie Profinet, w warstwie fizycznej wykorzystywane są urządzenia sieciowe SCALANCE.
Dzięki zmianom w procesie linia wytwarzania może być obecnie obsługiwana w sposób optymalny przez zaledwie jednego operatora, zamiast trzech. Wpłynęło to na obniżenie kosztów produkcji, dzięki czemu ZF jest w stanie oferować swoje produkty – systemy hamulcowe – w bardziej konkurencyjnych cenach. Wraz z automatyzacją poprawiła się również elastyczność produkcji przejawiająca się w uniezależnieniu działania całej linii od pojedynczej awarii. Dzięki wdrożeniu rozwiązania składającego się z jednej maszyny CNC i jednego robota dla każdego stanowiska wszystkie maszyny mogą pracować z obwodem bezpieczeństwa, którego rozpięcie (otwarcie osłon) nie wpływa na pracę pozostałych urządzeń.
Zwiększyła się także wydajność transportu oraz wydajność myjni i stopień czystości opuszczających ją detali. Nowa myjnia gwarantuje spełnienie wysokich wymagań czystości, jakości powierzchni po myciu oraz parametrów dotyczących suszenia. W procesie pakowania dodany został profilometr laserowy, który sprawdza charakterystyczne wymiary każdej części. Kontroluje on między innymi, czy wszystkie operacje zostały wykonane oraz czy nie doszło do uszkodzeń narzędzi.
W wyniku wdrożenia automatyzacji nastąpił wzrost wydajności produkcji. Obecnie wskaźnik OEE (Overall Equipment Effectiveness) dla pracy automatycznej jest wyższy niż przed wdrożeniem. Wynosi on 95%, co stanowi poprawę o 10 punktów procentowych w porównaniu do wcześniejszej pracy manualnej.
Obecnie realizowany jest etap uruchamiania następnych maszyn w całym systemie oraz planowane są kolejne etapy inwestycji. W fazie koncepcji znajduje się m.in. dodanie do procesu komparatora pomiarowego w obszarze myjni i paletyzacji. Rozważana jest także koncepcja automatyzacji procesu pobierania odlewów z opakowań dostawcy i ich załadunek na paletę transportową. Zostały już przeprowadzone próby w tym zakresie.
Źródło: Siemens