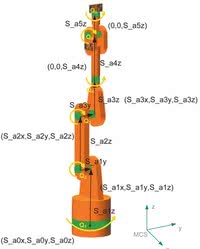
Fot. 1. Funkcje monitorowania pracy robota mogą być wykorzystywane do różnorodnych systemów kinematycznych bez konieczności ich wielokrotnego certyfikowania
Najpowszechniejszymi typami robotów są wersje o szeregowej strukturze kinematycznej z kilkoma osiami ruchu, w przypadku których jako napędy wykorzystywane są serwosilniki. Firma B&R podjęła się zadania zwiększenia bezpieczeństwa pracy robotów do takiego stopnia, by mogły one pracować bezpośrednio w sąsiedztwie ludzi - bez wygrodzeń, osłon czy innych zabezpieczeń.
Wymagania dotyczące bezpieczeństwa pracy robotów, a także zabudowy tych urządzeń w miejscach pracy ludzi opisane są w części 1 i 2 normy ISO 10218. Norma ta określa m.in. maksymalne dopuszczalne obciążenia dla ludzkiego ciała, a zgodność z nią ma zapewnić ochronę ludzi przed wpływem zagrożeń ze strony systemów zrobotyzowanych.
BEZPIECZEŃSTWO GWARANTOWANE PRZEZ TÜV
W aplikacjach zrobotyzowanych elementy robotów przemysłowych poruszają się zwykle po złożonej drodze, wykonując skomplikowane ruchy. Bezpieczne monitorowanie prędkości powinno więc obejmować nie tylko pojedyncze osie, ale też cały system robota, w szczególności jego punkt centralny, a więc nadgarstek z narzędziem.
W 2011 roku firma B&R zrobiła pierwszy krok ku rozszerzonemu bezpieczeństwu robotów, tworząc funkcję SLS (Safely-Limited Speed), która odpowiada za kontrolę pracy napędów robota. Jest ona zawarta w bibliotece SafeROBOTICS, która obejmuje bloki funkcji i parametrów opatrzone certyfikatem TÜV i przeznaczone do użytku w środowisku programistycznym funkcji bezpieczeństwa, którym jest SafeDESIGNER.
Bloki funkcyjne służą do programowania aplikacji sterowania wykorzystywanych w sterownikach SafeLOGIC. Te ostatnie odczytują dane dotyczące położenia i prędkości poszczególnych osi, a następnie za pomocą oprogramowania obliczana jest rzeczywista prędkość narzędzia i porównywana z określonymi wartościami bezpiecznymi.
|
SAFEMC, CZYLI BEZPIECZNE STEROWANIE NAPĘDAMI
W napędach wyposażonych w SafeMC, a więc opracowaną przez B&R funkcję bezpiecznego sterowania, odczyt danych bezpieczeństwa i zadania bezpieczeństwa realizowane są bezpośrednio przez napęd. Transmisja jest realizowana również w bezpieczny sposób za pomocą protokołu openSAFETY, który działa niezależnie od wykorzystywanej sieci komunikacyjnej.
Przykładowo jeden z systemów zrealizowanych przez firmę Schlatter Industries bazuje na serwonapędach ACOPOSmulti firmy B&R. SafeMC jest zintegrowanym komponentem standardowym wszystkich tego typu serwonapędów i zapewnia czas wykrywania błędów oraz reakcji na nie wynoszący 7 ms, czyli mniej więcej 10 razy krótszy niż w przypadku zadziałania przekaźnikowych obwodów bezpieczeństwa. Dzięki temu odległość pokonywana do czasu zatrzymania narzędzi skraca się stukrotnie.
W pierwszej wersji rozwiązania SafeROBOTICS moduł oprogramowania do monitoringu wykorzystywał blok parametrów modelu kinematycznego, który mógł być skonfigurowany dla wszystkich powszechnie używanych typów robotów. Wadą tego podejścia była konieczność certyfikacji aplikacji bezpieczeństwa dla każdego typu robota oddzielnie. Aby zaoszczędzić klientom kosztów i problemów z tego wynikających, firma B&R opracowała znacznie wydajniejsze rozwiązanie w oparciu na standardowym bloku parametrów modelowania kinematycznego. Dzięki temu używane mogą być standardowe bloki parametrów dla każdej możliwej konfiguracji łańcucha kinematycznego liczącego aż do 11 osi, bez względu na wartości, jakie je opisują.
WIĘKSZA SWOBODA I WYGODA
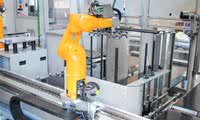
Fot. 2. Modele kinematyczne zawarte w tabelach dla parametrów standaryzowanych można wczytać do sterownika bezpieczeństwa; mogą one odzwierciedlać każdy szeregowy łańcuch kinematyczny liczący maksymalnie jedenaście osi
Jedną z wielu zalet przedstawianego rozwiązania jest fakt, że każda aplikacja bezpiecznego sterowania wymaga tylko jednokrotnej certyfikacji. Jednocześnie możliwe jest wykonywanie aplikacji o wielu osiach sprzężonych mechanicznie.
Wśród zaawansowanych funkcji SafeROBOTICS znajduje się nowy blok funkcji służący do obsługi dodatkowych stopni swobody w układach złożonych. Blok ten sprawdza prawidłowość zapisanych parametrów. Dzięki temu funkcja SLS jest łatwa w użyciu, zwłaszcza gdy użytkownik korzysta z gotowych bloków parametrów dla standardowych typów robotów dostarczanych przez producentów tych maszyn.
OPTYMALNE WSPARCIE UŻYTKOWNIKA
Użytkownik określa, który rodzaj sterowania najlepiej spisuje się w jego aplikacji, tj. czy będzie to sterownik robota dostarczony przez producenta łańcucha kinematycznego, czy zintegrowany w nadrzędnym systemie sterowania. Jest to możliwe dzięki użyciu standardu openSAFETY, który jest protokołem open source i działającym niezależnie od typu magistrali sieciowej.
Do konfiguracji potrzeba tylko danych dotyczących położenia elementów maszyn istotnych z punktu bezpieczeństwa, a także napędów mogących reagować zgodnie z funkcjami bezpieczeństwa. Komponenty napędowe, takie jak np. ACOPOSmulti z funkcją SafeMC, stanowią optymalny wybór do tych zadań, co wynika z ich zintegrowanych funkcji bezpieczeństwa i wydajności. Nigdy przedtem, od czasu powstania pierwszego robota sześcioosiowego, a więc już 40 lat temu, wspólna praca ludzi i maszyn nie była równie prosta!
B&R Automatyka Przemysłowa
www.br-automation.com