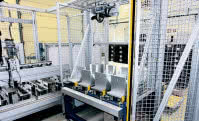
Fot. 1. Przykład systemu bezpieczeństwa umożliwiającego łatwy dostęp do stref regulacji i konserwacji maszyny
Opierając się na obserwacjach rynku oraz wieloletnich doświadczeniach, można odnieść wrażenie, że elementy bezpieczeństwa często traktowane są jako element, który spowalnia proces i utrudnia pracę operatora. Natomiast w rzeczywistości budowa systemu bezpieczeństwa opiera się często na najprostszych elementach, takich jak przekaźniki bezpieczeństwa, styczniki i przyciski zatrzymania awaryjnego.
Jest to rozwiązanie niedrogie i przy właściwym podłączeniu w łatwy sposób spełniające wymagania dyrektywy maszynowej. Używanie takich prostych systemów może powodować jednak realne spowolnienie procesu produkcyjnego, przestoje maszyny oraz długi serwis przy uszkodzeniach samych elementów.
Odpowiednie dobranie elementów systemu bezpieczeństwa może przynieść odwrotny skutek i sprawić, że maszyna będzie bezpieczna, łatwa w serwisie, a sam układ minimalnie wpłynie na długość procesu wykonywanego przez maszynę. Musi się to jednak wiązać z uczestnictwem osób odpowiedzialnych za układ bezpieczeństwa już na etapie koncepcji i projektowania maszyny tak, aby rozwiązania technologicznie współgrały z systemem bezpieczeństwa.
Dobrym przykładem może być tutaj system podawania materiału przez robota przemysłowego. Źle zaprojektowany układ będzie miał jedno miejsce załadunkowe, co spowoduje, że proces będzie zatrzymywany przy każdym wjeździe materiału, który robot ma później odłożyć. Dobrze zaprojektowany system będzie miał dwa miejsca załadunkowe zabezpieczone np. kurtynami świetlnymi z systemem ich zawieszenia (muting). Spowoduje to, że proces będzie mógł przebiegać w sposób ciągły i nie spowolni produkcji.
Od razu nasuwa się myśl, że to drugie rozwiązanie będzie droższe. Jest to tylko częściowo prawdą. System taki, jak już wspomniano, nie będzie wymagał przestojów w trakcie normalnej pracy maszyny, co przełoży się na większą wydajność i łatwiejsze zaplanowanie produkcji. W perspektywie kilku lat pracy takiej maszyny może mieć to znaczący wpływ na bilans kosztów takiego rozwiązania.
Takich przykładów jest dużo więcej. Obecnie systemy bezpieczeństwa mogą być wyposażone we wszelkiego rodzaju techniki bezpiecznego monitorowania pracy napędów: prędkości bezpiecznej, szybkiego zatrzymania czy samej kontroli zatrzymania. Wyobraźmy sobie wejście do strefy niebezpiecznej, zabezpieczonej drzwiami z ryglowaniem, w której należy wykonać regulacje.
Przy prostym układzie bezpieczeństwa wejście do strefy najczęściej spowoduje wyłączenie napędów poprzez odłączenie zasilania styczników, falowników czy serwonapędów. Może to powodować długie czasy ponownego rozruchu maszyny. Wykorzystując droższe rozwiązania, dające możliwość kontroli napędu w sposób bezpieczny, skrócimy ten okres poprzez zmniejszenie czasów zatrzymania napędów i unikanie błędów systemów sterujących napędem.
Miejsca w maszynie, które wymagają częstych ingerencji operatora, można zabezpieczyć systemem optycznym, tj. kurtyną świetlną lub skanerem bezpieczeństwa. Przykładem dobrego zastosowania skanera może być hala produkcyjna, gdzie pracują roboty montujące elementy. Nie musimy ich wtedy zabudowywać skomplikowanym systemem wygrodzeń, które często ograniczałyby swobodę pracy takich robotów a system dodatkowego pola ochronnego sprawi, że wchodząc w dany obszar, nie musimy przerywać pracy wszystkich robotów w danej strefie.
Warto pamiętać, że sercem każdego układu bezpieczeństwa jest system logiczny. Obecnie rynek oferuje wiele sterowników bezpieczeństwa, które mogą oprócz nadzorowania systemów bezpieczeństwa, sterować także całym procesem produkcyjnym, zastępując tym samym zwykły sterownik PLC.
Używając takiego rozwiązania, tu również możemy zyskać bardzo wiele: zmniejszamy np. liczbę samych sterowników, a co za tym idzie - skracamy czas programowania takiej maszyny, redukujemy miejsce w szafach sterowniczych itp. Łatwiej jest nam także nadzorować taki system, poprzez dużą ilość informacji przekazywanych do systemu wizualizacji. Sterowniki takie mogą sieciowo przekazywać informacje do innych "wysp", co redukuje liczbę przewodów.
Nawet małe maszyny możemy już wyposażyć w proste, ale programowalne przekaźniki bezpieczeństwa. Ich możliwości bardzo często nie odbiegają od większych przedstawicieli tej grupy. Wyposażyć je możemy w moduły rozszerzeń, komunikację sieciową, a błędy i status systemu pokazywać na panelach operatorskich. Rozwiązania takie stają się opłacalne już przy kilku użytych funkcjach bezpieczeństwa i stanowią ciekawą alternatywę dla prostych przekaźników bezpieczeństwa.
Coraz częściej spotkać możemy także nowoczesne układy wejściowe, takie jak np. przyciski zatrzymania awaryjnego połączone sieciowo czy systemy ryglowania ze zintegrowaną kontrolą i wizualizacją stanu pracy takiego elementu. Każde z takich rozwiązań może, mimo swojej wyższej ceny na początku, przynosić korzyści w postaci szybkiego serwisu takich urządzeń, czy łatwiejszej obsługi.
Dokładniejsza diagnostyka oraz coraz mniejsza ilość elementów mechanicznych w wielu produktach bezpieczeństwa to także, oprócz większej niezawodności, większe bezpieczeństwo operatora i pracowników utrzymania ruchu. Warto o tym pamiętać, wybierając rozwiązanie dla projektowanej maszyny.
PODSUMOWANIE
Jak widać na powyższych przykładach, ważne jest, aby każdy, kto jest związany z przemysłem maszynowym, czy to od strony producenta, czy od strony zamawiającego, wiedział, że dobrze dobrany układ bezpieczeństwa może wpłynąć pozytywnie na pracę, serwis i obsługę maszyny, a tym samym na zmniejszenie kosztów.
Rozwiązanie droższe na początku może się zwrócić już po kilku miesiącach pracy poprzez wydajniejszą pracę, a przecież czas to pieniądz! Należy także pamiętać, że dobrze działający układ bezpieczeństwa, który nie sprawia problemów, to niższa szansa na manipulowanie elementami bezpieczeństwa przez personel obsługujący takie maszyny.
Radosław Berdak
Pilz Polska
www.pilz.pl