Systemy MES stanowią historycznie rodzinę produktów programowych zorientowanych na zarządzanie produkcją, których zadaniem jest wypełnienie przestrzeni informacyjnej pomiędzy poziomem produkcji a warstwą IT. Główne zadania przez nie spełniane to:
- zarządzanie realizacją procesu produkcji, monitorowanie ilościowe i jakościowe,
- kolekcjonowanie danych produkcyjnych z możliwością odtworzenia genealogii produktu na każdej z faz produkcyjnych,
- synchronizacja w czasie rzeczywistym i wymuszanie realizacji procesów produkcyjnych z uwzględnieniem dostępności surowców, półproduktów i gotowych produktów,
- koordynacja z systemami ERP realizacji zleceń produkcyjnych,
- analiza danych produkcyjnych (wydajnościowa, jakościowa, ilościowa).
W przypadku gdy decydujemy się na wdrożenie MES, istotnym wyzwaniem z punktu widzenia gotowości zakładu do implementacji systemu jest szczegółowe i usystematyzowane opisanie wszystkich funkcji związanych z technologią produkcji. Takie podejście pozwoli na efektywne wdrożenie rozwiązania na zasadzie ewolucyjnej, nie stanowiąc zbyt dużego wyzwania dla kierownictwa i personelu pracowniczego zakładu.
DLACZEGO SYSTEM ZARZĄDZANIA PRODUKCJĄ?
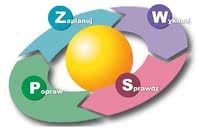
Rys. 1. Cykl Deminga (źródło: Wikipedia)
Istnieje kilka zasadniczych przyczyn, dla których firmy decydują się na implementację systemów zarządzania produkcją. Jedną z nich jest osiągnięcie krytycznej wielkości udziału w rynku. Jak wiadomo, możliwość zwiększania sprzedaży jest ograniczana wzrostem kosztów produkcji. Stąd też firmy starają się skupić na ograniczaniu tych ostatnich, a do tego często potrzeba narzędzi takich jak MES. Pozwalają one na pełną analizę produkcji pod kątem jakościowym i ilościowym, jak również na efektywne zarządzanie jej realizacją.
Z moich obserwacji wynika, że tego typu kompleksowe wdrożenia są realizowane głównie w firmach o długiej obecności na rynku, często o zasięgu ponadkrajowym lub globalnym. Przedsięwzięcia te są wówczas dobrze zdefiniowane pod względem celów biznesowych, nierzadko stanowią fragment szerszego programu obejmującego wiele powiązanych ze sobą zakładów produkcyjnych.
Decyzje o wdrożeniu wybranych modułów MES często są następstwem działań podjętych w zakresie optymalizacji produkcji, takich jak programy Lean Manufacturing, Kaizen czy Six Sigma. Strategie te w mniejszym lub większym stopniu wykorzystują cykl Deminga do realizacji kolejnych kroków poprawy.
Istotnym elementem cyklu jest liczbowe potwierdzenie wyników wprowadzanych ulepszeń. Wiąże się to z koniecznością wykonywania ciągłej analizy danych produkcyjnych. Właśnie ten czynnik zachęca służby odpowiedzialne za implementacje strategii optymalizacji do sięgnięcia po moduły MES wspomagające pozyskiwanie i analizę danych produkcyjnych.
SPOSOBY WDRAŻANIA SYSTEMÓW
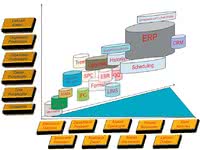
Rys. 2. Brak jednorodnej platformy programowej w typowym zakładzie przemysłowym
Bardzo często rozpoczyna się od wdrażania modułów takich jak te odpowiedzialne za monitorowanie zużycia energii czy też liczenie współczynników efektywności produkcji OEE (Overall Equipment Efficiency). Z moich obserwacji wynika że decyzje o wyborze rozwiązania wypełniającego tę lukę tylko sporadycznie wiążą się ze świadomym wyborem platformy, która pozwoli na przyszłościową integrację wielu modułów funkcjonalnych związanych z zarządzaniem zakładem.
W efekcie jednak zamiast modułu będącego elementem jednorodnej struktury MES pojawiają się zamknięte struktury programowe, które nie mogą być w żaden sposób uzupełnione o kolejne elementy systemu zamykającego się w jednorodnym środowisku.
Poszczególne funkcje systemów MES można najogólniej sklasyfikować w dwóch grupach:
- Zarządzanie danymi - funkcje pasywne związane bezpośrednio z takimi modułami jak: monitoring mediów, liczenie OEE, raportowanie jakości i ilość produkcji. Wymagają one odrębnej analizy i poprzez wnioskowanie wspomagają proces zarządzania. Moduły te same w sobie nie przynoszą żadnych oszczędności, ale odpowiednie wykorzystanie informacji z nich uzyskiwanych może takowe zapewnić.
- Zarządzanie procesem - funkcje aktywne, które bezpośrednio ingerują w proces, wymuszając jego przebieg, procedury, zużycie surowców, definiując zasoby urządzeń i ludzi. Do nich należą takie funkcje jak szeroko rozumiany tracking, tworzenie EBR (Electronic Batch Record) czy walidowanie on-line odstępstw w procesach produkcyjnych. Elementy te mają bezpośredni wpływ na podniesienie efektywności produkcji, znacznie ułatwiając zarządzanie procesem produkcyjnym.
Na rynku polskim pierwsza z grup wiedzie wyraźny prym. Fakt ten wiąże się z decyzjami, które są raczej wynikiem wchodzących regulacji lub potrzeb raportowania niż chłodnej kalkulacji ekonomicznej i nastawienia na podwyższanie efektywności produkcji.
Firmy decydują się na pomiary OEE czy monitorowanie mediów na zasadzie tworzenia benchmarków, które ułatwiają realizację procesów decyzyjnych w zakresie eliminacji źródeł strat i optymalizacji technologii produkcji. Właśnie w takim momencie powinna pojawić się decyzja o rozpoczęciu budowy systemu MES jako platformy modułowej ustanawiającej określony, jednolity standard pozwalający w przyszłości na pełne zarządzanie zakładem produkcyjnym.
WYBÓR SYSTEMU MES
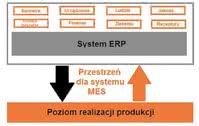
Rys. 3. Luka w ciągłości informacyjnej w zakładzie produkcyjnym
Platforma zbudowana w oparciu o spójne moduły programowe zastępuje cały wachlarz różnorodnego oprogramowania, często już wycofanego z rynku lub wymagającego zaangażowania dodatkowych sił IT w celu tworzenia niestandardowych powiązań, które pozwolą na płynny przepływ informacji. Z takimi sytuacjami mamy do czynienia w zakładach produkcyjnych, gdzie świadomość osób dotycząca konieczności systemowego panowania nad procesem produkcyjnym jest ugruntowana, a poszczególne moduły funkcjonalne były kolekcjonowane na zasadzie niezależnych decyzji prowadzących do utworzenia niejednorodnych i trudnych do utrzymywania w sprawności technicznej struktur.
Innym czynnikiem przyspieszającym decyzję o wprowadzeniu systemów zarządzania produkcją są uwarunkowania i regulacje prawne, które często wymuszają konieczność wprowadzenia sprawniejszych rozwiązań systemowych - zwłaszcza tam, gdzie asortyment i zmienność produkcji wymaga sporego zaangażowania personelu. Tego typu aplikacje pojawiają się w zakładach, w których wymagane jest sięganie do genealogii produktu i tworzenia EBR.
Naturalną decyzją, która następuje po implementacji funkcji związanych z genealogią produktu, jest wprowadzenie zarządzania poszczególnych etapami produkcji (tracking). Znacznie ułatwia ono zachowanie zasad GMP, jednocześnie silnie wpływając na wzrost efektywności produkcji.
Kolejnym elementem wpływającym na decyzję o konieczności wprowadzenia systemu MES jest doświadczenie wynikające z implementacji systemów planowania ERP (Enterprise Resource Planning). Systemy te pozwalają na precyzyjne planowanie produkcji pod warunkiem ciągłego dostarczania w czasie rzeczywistym informacji z poziomu produkcyjnego. Systemy ERP pozbawione tego elementu efektywnie wykorzystują tylko część swoich możliwości.
Taki obraz często pojawia się w polskich zakładach produkcyjnych. Zlecenia produkcyjne przekazywane są na stanowiska pracy w postaci papierowych zestawień, a efekty ich realizacji są kolekcjonowane w postaci papierowych raportów, które następnie są poddawane analizie i te wyniki są ponownie ręcznie wprowadzane do systemu ERP.
JAK ZAPEWNIĆ CIĄGŁOŚĆ PRZEKAZYWANIA INFORMACJI?
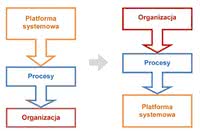
Rys. 4. Procesy decyzyjne zachodzące podczas wdrażania systemu klasy MES
Istnieje kilka możliwości wypełnienia omawianej luki i zapewnienia ciągłości łańcucha informacji przekazywanej między tymi poziomami. Jednym z nich jest uzupełnienie istniejącego systemu ERP o stacje klienckie współpracujące z oprogramowaniem middleware, zapewniające synchronizacje przesyłanych zleceń i raportów. W ten sposób wyeliminowany zostaje nośnik papierowy jako medium pośrednie. Rozwiązania takie pozwalają na dwukierunkowe przekazywanie informacji, ale wymagają od operatorów sporego zaangażowania. Nie mają one jednak pełnej funkcjonalności MES, jak również nie pozwalają na komunikację w czasie rzeczywistym z poziomem maszyn i urządzeń.
Uzupełnieniem powyższego typu rozwiązania jest system SCADA, który ze swej natury przeznaczony jest do sterowania z poziomu operatora procesem i nadzorem nad jego parametrami. Ten z kolei często rozszerzany jet o historiany stanowi dodatkowe źródło informacji o procesie. SCADA jest wtedy wykorzystywany jako system do zbierania i gromadzenia danych, zapewniając komunikację z poziomem maszyn.
W niektórych przypadkach służy on również jako system raportowy wspierany bardziej lub mniej zaawansowanymi zewnętrznymi programami, które umożliwiają analizę i raportowanie. Tego typu rozwiązania spotykane są w zakładach produkcyjnych, w których dział IT mocno zaangażowany jest w implementację systemów ERP, starając się uzupełnić ich funkcjonalność o cechy typowe dla MES.
Zdecydowanie należy też wyznaczyć wyraźną linię odgraniczającą systemy wizualizacji procesów (SCADA/HMI) od funkcji przynależących do systemów MES. Te pierwsze stworzone zostały jako wsparcie dla operatora i stanowią doskonałe narzędzie do sterowania procesem technologicznym. Systemy MES pełnią zupełnie inną funkcję polegającą na zarządzaniu procesem produkcyjnym w zakładzie, wypełniając lukę informacyjną dla systemów planowania. W ten sposób MES jest platformą programową wspierającą poziom zarządzania w zakładzie produkcyjnym i będącą niezbędnym narzędziem do optymalnego organizowania produkcji i jej procesów.
RACJONALNE WDRAŻANIE MES
Podsumowując, najczęściej popełnianym błędem przy budowie systemów MES jest bardzo silna presja na wybór platformy technologicznej z przesunięciem na drugi plan problematyki związanej z organizacją produkcji i procesami zachodzącymi w zakładzie. Odwrócenie tego rozumowania i skupienie się na analizie organizacji i opisie procesów technologicznych doprowadzi w efekcie do dobrego zdefiniowania celów, a wybór platformy będzie zasadniczo elementem drugorzędnym, wynikającym z postawionych zadań.
B&R Automatyka Przemysłowa
www.br-automation.com/pl/