W przypadku kontroli jakości elementów o złożonych kształtach wymagane jest zazwyczaj zastosowanie systemu z wieloma kamerami zainstalowanymi szeregowo lub równolegle, które dokonują akwizycji obrazów oraz ich analizy pod kątem różnych kryteriów - kształtu elementów, cech ich powierzchni, itd. System Sova-VIS 16 firmy Gefasoft Automatisierung und Software GmbH, który sprawdza jakość dyfuzorów poduszek powietrznych, nie jest wyjątkiem.
Są to krytyczne dla bezpieczeństwa elementy poduszek samochodowych, które mają postać miseczek o średnicy około 60 milimetrów i wytwarzane są w różnych wersjach. Na etapie produkcji należy je poddać szczegółowej kontroli stanu powierzchni wewnętrznych oraz zewnętrznych, a także innych parametrów.
WYMOGI DOTYCZĄCE TWORZONEJ APLIKACJI
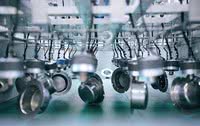
Fot. 1. Dyfuzory, jako krytyczne elementy pomiędzy poduszką powietrzną a generatorem gazu, muszą być sprawdzane szybko, dokładnie i z maksymalną niezawodnością
Opisywany system cechuje się dużą różnorodnością wykonywanych zadań. Podczas gdy niektóre procesy kontrolne wymagają pozyskania tylko jednego obrazu, w innych konieczne jest zastosowanie zaawansowanych systemów oświetleniowych i akwizycja bardzo wielu obrazów. Zadaniem szczególnie krytycznym jest inspekcja wewnętrznych ścian dyfuzorów, które należy sprawdzać pod kątem występowania nawet najmniejszych niedoskonałości, które mogą mieć rozmiary zaledwie kilkudziesięciu mikrometrów. Aby uzyskać wymaganą rozdzielczość obrazów, wykorzystuje się tutaj kamery liniowe, zaś sam proces skanowania trwa około dwóch sekund.
Gdyby wszystkie stacje kamery zostały umieszczone nad tradycyjnym systemem przenośnikowym, takim jak np. obrotowy stół indeksujący, stacja z kamerą o najdłuższym czasie akwizycji warunkowałaby długość cyklu pracy całego systemu, w praktyce ograniczając jego przepustowość. Dzięki elastyczności XTS szybciej działające stacje kontrolne mogą być obsługiwane z większą prędkością, podczas gdy wolniejsze - a tych zostało zainstalowanych więcej - mogą być jednocześnie uzupełniane kolejnymi komponentami.
"Bardzo różne czasy akwizycji obrazów w różnych obszarach systemu Sova-VIS 16 sprawiły, że zaczęliśmy myśleć o maszynie wyposażonej w elastyczny, asynchroniczny system transportowy, który pozwoliłby nam wydajnie wykonywać zadania inspekcyjne. XTS firmy Beckhoff z niezależnie sterowanymi napędami doskonale wpasował się w te wymagania.
Pomimo obecności wolniejszych stacji kontrolnych udało nam się osiągnąć średni czas cyklu wynoszący 1,9 sekundy! XTS umożliwił nam także wdrożenie rozwiązania na powierzchni znacznie mniejszej niż w przypadku innych, porównywalnych rozwiązań" - stwierdził Georg Schlaffer, kierownik ds. marketingu w Gefasoft.
![]() ![]() Fot. 2. Moduły XTS z górnymi oraz dolnymi trzpieniami przemieszczają dyfuzory w orientacji "kapelusz" oraz "kubek"; widoczna jest zębatka wykorzystywana do obracania elementu przed kamerą liniową |
"Z powodu dużego popytu na produkowane części, klient końcowy określił wymogi co do cyklu na poziomie poniżej dwóch sekund. Ponieważ dwa etapy kontroli trwały prawie po 4 sekundy, stacje te musiały zostać zduplikowane i zrównoleglone. System XTS zapewnił nam elastyczność i prostotę wdrożenia. Inne rozwiązania, tj. z transporterami i przenośnikami opartymi na paskach lub łańcuchach, wymagałyby stworzenia znacznie bardziej złożonego układu, były wolniejsze, a do tego zajmowały więcej miejsca", dodaje Christian Schärtl, dyrektor techniczny w firmie.
PONAD DZIESIĘCIOMETROWY TOR JEZDNY
Wykorzystanie wielu stacji kontrolnych spowodowało, że całkowita długość toru XTS wynosi około 11 metrów oraz jeździ po nim 30 karetek. Ponieważ elementy ruchome są stosunkowo ciężkie, linia została wyposażona w specjalny system naprowadzania wykonany przez Hepco. Ciężar pojedynczej karetki z wyposażeniem to około 4 kg, co wynika z konieczności zastosowania modułów do podnoszenia i obracania dyfuzorów. Te ostatnie muszą być precyzyjnie obracane przed kamerami oraz umieszczane w dwóch pozycjach ("kapelusz" i "kubek"), tak aby można dokonywać ich inspekcji od dołu i od góry.
![]() ![]() Fot. 3. Widok całego systemu oraz zdalnych we/wy i serwonapędów |
Podczas tworzenia aplikacji od samego początku celem było wykorzystanie jednego układu kontrolnego i pełna automatyzacja wykonywanych wcześniej ręcznie procesów. Zakres tych ostatnich obejmował czynności od pobierania elementów z palety do ich układania w stosie lub sortowania za pomocą robota.
Odrzucono przy tym pomysł rozłożenia zadań kontrolnych na wiele etapów, który by były wykonywane z użyciem różnych maszyn. Oprócz konieczności złożonego transportu i zwiększonych wymagań co do zajmowanej przestrzeni, taki system byłby po prostu zbyt drogi. "Dzięki XTS możemy elastycznie integrować dodatkowe stanowiska wzdłuż linii produkcyjnej. Sprawia to, że system jest również gotowy do wymagań, które pojawią się w przyszłości", zwraca uwagę Georg Schlaffer.
Czym jest XTS?
Obejmuje to transport produktów, dostosowywanie ich rozkładu na linii, przyspieszanie i spowalnianie ruchu, a także chwytanie i przenoszenie elementów. Nieregularny przepływ produktów jest wychwytywany i korygowany w taki sposób, aby docierały one do kolejnej stacji roboczej w stałych odstępach czasowych i ze stałą prędkością. Budowa systemu XTS składa się z modułowego napędu liniowego w pełni zintegrowanego z układem zasilania i pomiaru przemieszczenia, prowadnic jezdnych, modułów ruchomych (karetki) oraz komputera przemysłowego z oprogramowaniem TwinCAT. Napędy nie mają części ruchomych, zaś do uruchomienia sytemu jest wymagane jedynie podłączenie źródła zasilania i sterownika poprzez sieć EtherCAT. Modułowe napędy liniowe zawierają cewki elektromagnetyczne oraz inne elementy funkcjonalne, z kolei ruchome karetki wyposażone są w powierzchnie magnetyczne, co pozwala na generowanie sił nośnych. Dzięki temu rolki karetek - o trudno ścieralnej powierzchni wykonanej ze specjalnego tworzywa sztucznego - mogą poruszać się po prowadnicy z dużymi prędkościami (do 4 m/s bez strat dokładności pozycjonowania). Mechaniczny enkoder o wysokiej dokładności przekazuje dane o pozycji elementu do modułu napędowego. Karetki samodzielnie przyspieszają, hamują oraz synchronizują się, poruszając po odcinkach prostych oraz zakrzywionych. Mogą one pozycjonować się w absolutnym układzie współrzędnych lub względem siebie nawzajem, możliwe jest też ich grupowanie i łączenie w trakcie ruchu. Możliwości adaptacji do linii technologicznej Omawiany system stosowany może być do różnorodnych, w tym skomplikowanych zadań transportowych. To, co było wcześniej niemożliwe lub wymagało zastosowania kilku napędów, obecnie zrealizować można z wykorzystaniem jednego, modułowego rozwiązania. Wymiary geometryczne - długości i promienie - określane są na podstawie wybranych elementów. Do tego zastosowana może być praktycznie dowolna liczba karetek na typowych torach przy zachowaniu relatywnie niskich kosztów projektowania i konstrukcji. Warto zwrócić również uwagę na fakt, że system cechuje się niewielkim zużyciem energii, co jest ważne w przypadku jego długoterminowego użytkowania. |
PROCES INSPEKCJI KROK PO KROKU
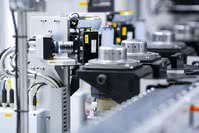
Fot. 4. System XTS umożliwił firmie Gefasoft zoptymalizowanie kontroli jakości cylindrycznych części metalowych
Komponenty, po ich odtłuszczeniu, są dostarczane na paletach do maszyny. Chwytak pobiera pojedyncze części i przekazuje je do XTS. Aby zapewnić właściwą orientację elementów, moduł chwytaka wyposażony jest w kamerę, która wykrywa kąt położenia dyfuzora, a także jego typ. Każdy dyfuzor ma wytłoczony numer partii, który jest sprawdzany na pierwszej stacji inspekcyjnej.
Po odczytaniu identyfikatora partii system sprawdza wnętrze dyfuzora. Wymaga to jego obrócenia w urządzeniu przesuwającym z pozycji "kapelusz" do pozycji "kubek", tj. z otworem skierowanym do góry. Aby to zrobić, części są pobierane z urządzenia poruszającego za pomocą chwytaka, obracane o 180° i umieszczane z powrotem na module przesuwającym. W międzyczasie wewnętrzny trzpień zostaje cofnięty, tak aby wycentrowany element spoczywał na kołnierzu. Aby sprawdzić wewnętrzną powierzchnię detalu, jest on następnie obracany (okręcany) wokół kamery liniowej (skanera liniowego).
"Prawdopodobnie największym wyzwaniem było to wynikające z ograniczonego miejsca. Kamera i cztery źródła światła musiały zmieścić się wewnątrz części, której wewnętrzna średnica wynosi jedynie 60 mm. Aby rozwiązać ten problem, musieliśmy zaprojektować zintegrowany moduł kamery z oświetlaczami, który niejako zanurza się w elemencie.
Ponadto konieczne było użycie szybkiego kontrolera dla takiego systemu oświetleniowego. Przesunięcie jednostki do elementu i wykonanie obrotu zajmuje ponad dwie sekundy - aby uzyskać czas cyklu całej linii wynoszący 1,9 sekundy, musieliśmy zainstalować dwie takie jednostki", komentuje Christian Schärtl.
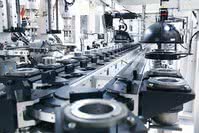
Fot. 5. Dyfuzory przechodzą przez stanowiska kontroli optycznej, z których niektóre występują w wersjach podwójnych
Po stanowiskach obrotowych znajduje się stanowisko do kontroli materiałowej oraz służące do sprawdzania jakości podstawy dyfuzora. Ostatnia stacja z kamerami w pierwszej liniowej sekcji systemu XTS odpowiada za kontrolę kołnierzy elementów pod kątem występowania wad. Sumarycznie pierwsza sekcja ma sześć modułów z kamerami, aczkolwiek biorąc pod uwagę podwójne skanery liniowe oraz stacje obrotowe, sumarycznie jest to dziewięć pozycji.
Po przejściu przez 180-stopniowy zakręt toru XTS, elementy trafiają do kolejnych stacji inspekcyjnych, a także znakowarek. Komponenty są obracane do orientacji "kapelusz", a następnie dwie liniowe kamery sprawdzają ich powierzchnie zewnętrzne. Po tym następuje kontrola górnej strony kołnierza.
Następnie sterowana z kamery drukarka atramentowa oznacza wadliwe komponenty, zaś znakowarka laserowa - części poprawne, bez stwierdzonych wad jakościowych. Na końcu drugiej liniowej sekcji XTS znajduje się szybki robot Stäubli TP80, który odbiera części z przenośnika i przekazuje je do dalszych etapów procesu.
Informacje o wdrożeniu i systemie XTSwww.gefasoft-regensburg.de/en |
Beckhoff Automation
www.beckhoff.pl