Wózki AGV (Automated Guided Vehicles) służą do bezobsługowego transportu elementów, np. pomiędzy stanowiskami montażu oraz strefami magazynowania. Takie rozwiązania stosowane są już od kilkudziesięciu lat, natomiast ze względu na stosunek czasu pracy wózka do czasu ładowania oraz gabarytu akumulatorów perspektywa autonomicznej jazdy wózka nie była zachwycająca. Postęp technologiczny sprawił, że obsługa wózka została ograniczona do minimum, a rozwiązania z zastosowaniem wózków AGV stały się atrakcyjne finansowo.
Tak jak w przypadku robotów, wózki AGV umożliwiają zastąpienie człowieka w pracach monotonnych oraz powtarzalnych, ale również wymagających uwagi ze strony operatora, związanej z bezpieczeństwem innych osób. Zastąpienie człowieka autonomicznym wózkiem nadal pozostawia podstawowe zagrożenie, jakim jest jego ruch. Z pomocą dla producentów i integratorów przychodzi norma typu C z 1999 roku, PN-EN 1525 "Wózki jezdniowe - Bezpieczeństwo - Wózki bez operatora i ich układy", która opisuje punkt po punkcie, jak powinien wyglądać bezpieczny, autonomiczny system transportu.
Norma PN-EN 1525 dzieli metody zabezpieczania wózków AGV w zależności od stref, w jakich wózek pracuje, na strefę zamkniętą oraz strefę wspólną. Zgodnie z definicją, strefa zamknięta to fizycznie wydzielona strefa dla ruchu wózka z dostępem wyłącznie upoważnionych osób. Taka strefa powinna składać się z wygrodzenia na całej trasie wózka oraz drzwi, bramy lub ruchomej osłony umożliwiającej dostęp do tej strefy. Element dostępowy powinien mieć następujące cechy:
- być otwierany tylko na zewnątrz,
- być otwierany tylko z zewnątrz kluczem,
- być otwierany od wewnątrz bez użycia klucza,
- w momencie otwarcia zatrzymywać wszystkie ruchy wózków w strefie zamkniętej,
- samo zamknięcie nie powinno ponownie uruchamiać wózków.
Strefa wspólna to strefa, w której odbywa się zarówno ruch wózka, jak i pieszych oraz pojazdów prowadzonych przez operatorów.
W przypadku zastosowania strefy zamkniętej należy spełnić przede wszystkim zalecenia normy PN-EN 1525, które opisane zostaną w cechach wspólnych obu stref. Główną różnicą pomiędzy strefą zamkniętą a wspólną jest wykrywanie osób na drodze jazdy. Norma PN-EN 1525 stanowi jasno, że w przypadku pracy w strefie zamkniętej nie jest wymagane stosowanie środków wykrywania personelu. Należy tutaj być jednak bardzo ostrożnym, ponieważ znane są przypadki uruchomienia wózka z personelem znajdującym się wewnątrz strefy zamkniętej, co doprowadziło do poważnych wypadków ze względu właśnie na niedziałające środki wykrywania personelu.
Stosując strefę wspólną, należy przede wszystkim spełnić wymagania dla środków do wykrywania osób na drodze jazdy wózka. Środki te powinny mieć między innymi następujące cechy:
- powinny działać przynajmniej powyżej pełnej szerokości wózka i ładunku w każdym kierunku jazdy,
- powinny umożliwić zatrzymanie wózka przez układ hamulcowy przed kontaktem z osobą, z uwzględnieniem stanu podłogi,
- powinny wykrywać części ciała możliwie najbliżej podłogi, przede wszystkim ze względu na ryzyko zmiażdżenia stóp.
Dodatkowo należy przeprowadzić cały proces testów, weryfikujących działanie środków wykrywania personelu na głównych kierunkach jazdy. Jeżeli osoba po pojawieniu się w strefie detekcji opuszcza drogę przejazdu wózka, to jego praca może zostać wznowiona po 2 s opóźnieniu wypełnionym ostrzeżeniami, takimi jak migające światło lub sygnał akustyczny.
Częstym błędem przy wprowadzaniu wózków samojezdnych do pracy w zakładach jest pominięcie zabezpieczeń dla ruchu obrotowego, jeżeli wózek takowy ruch wykonuje. W takim przypadku należy zapewnić boczne zabezpieczenia dla ruchu obrotowego oraz przeprowadzić badania z odpowiednimi próbkami testowymi. Norma nie precyzuje, jakiego rodzaju powinny to być zabezpieczenia.
Bardzo ciekawym zaleceniem normy jest zalecenie mówiące o tym, że gdy nie jest możliwe zastosowanie środków wykrywania personelu w każdym kierunku jazdy (np. wózki wyposażone w widły), maksymalna prędkość wózka powinna zostać ograniczona do 0,3 m/s, a wózek powinien mieć możliwość zatrzymania go na dystansie 600 mm.
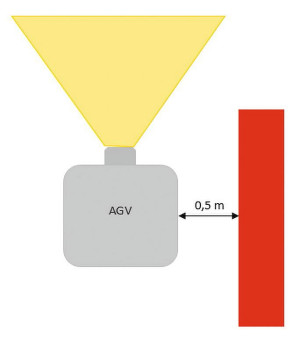
Oznacza to, że stosując ograniczenia prędkości, możliwe jest całkowite pominięcie środków wykrywania personelu. Dodatkowym ogólnym wymaganiem przy zabezpieczaniu stref wspólnych jest zachowanie odpowiednich odstępów bezpieczeństwa o szerokości 0,5 m oraz wysokości 2,1 m pomiędzy częściami wózka, ładunku oraz przyczep a przyległymi konstrukcjami stałymi wzdłuż drogi (rys. 1).
Jeżeli istnieją miejsca, gdzie nie jest możliwe zapewnienie 0,5 m odstępu, taki obszar jest uznawany za strefę zagrożenia. Przed wjazdem do takiej strefy powinno nastąpić zmniejszenie prędkości wózka do 0,3 m/s oraz powinien zostać włączony dźwiękowy sygnał ostrzegawczy.
Norma PN-EN 1525 opisuje również ogólne cechy, jakie powinien spełniać wózek samojezdny bez względu na strefę pracy. W normie zawarto opis cech mechanicznego układu hamulcowego wózka, tj. wpływ rozłączenia zasilania na pracę hamulca, pochylenie robocze a utrzymanie wózka w pozycji czy też działanie podczas utraty kontroli nad prędkością i sterownością wózka.
Kolejnym punktem są cechy urządzeń sterujących, ich umiejscowienie oraz funkcjonalność. Jeżeli chodzi o proces ładowania akumulatora, to norma mówi jedynie o konieczności zabezpieczenia ludzi przed przypadkowym kontaktem z przyłączami ładowania wózków. Automatyczne układy ładowania powinny być tak skonstruowane, że przyłącza ładowania są aktywne tylko wtedy, kiedy wózek jest do nich podłączony.
Podczas dobierania maszyny do rodzaju ładunku należy wziąć pod uwagę sposób podtrzymania ładunku tak, aby zachowana była stateczność całego urządzenia. Oznacza to, że ładunek nie może się przemieszczać z pierwotnego miejsca w każdych warunkach eksploatacyjnych, biorąc pod uwagę również moment zatrzymania awaryjnego oraz przenoszenia ładunku.
W przypadku posiadanych przyczep, przed uruchomieniem wózka powinien zostać wyemitowany 2 s sygnał akustyczny. Przynajmniej przez 5 s prędkość rozruchu powinna wynosić do 0,3 m/s, a sprzęgi przyczep powinny mieć czarno-żółte lub czerwono-białe oznakowanie ostrzegawcze.
Norma PN-EN 1525 ze względu na datę powstania ma nieaktualne odniesienia do wymagań dla układów sterowania (powołanie na PN-EN 954-1, aktualnie obowiązuje PN-EN ISO 13849-1) oraz do wymagań dla zatrzymania awaryjnego (powołanie na PN-EN 418, aktualna PN-EN ISO 13850). Mimo to norma dosyć precyzyjnie opisuje oczekiwania względem układu sterowania związanego z bezpieczeństwem. W załączonej tabeli przedstawiono wymagania w zależności od wpływu danej funkcji na stateczność wózka oraz środki wykrywania personelu.
Oprócz wymagań dla układu sterowania norma PN-EN 1525 zawiera również wytyczne związane ze sprawdzaniem i przekazaniem wózka. Każde z wymagań opisanych wyżej odnośnie do zabezpieczeń dla wózka AGV powinno zostać sprawdzone i potwierdzone przez producenta. Nie podano szczególnych wymagań odnośnie do kwalifikacji osoby sprawdzającej, powinna to być jedynie osoba kompetentna.
Weryfikacja powinna polegać na:
- sprawdzeniu konstrukcji, czyli dokumentacji konstrukcyjnej wózka na zgodność z wymaganiami dla m.in. układu hamulcowego, sterowania, obsługi ładunku,
- badaniu typu przeprowadzonego na próbce z serii produkcyjnej, dotyczącego testów funkcjonalnych układu hamulcowego, pomiaru sił oraz spełnienia wymagań dla środków wykrywania personelu,
- badania standardowego, czyli badania przeprowadzonego na każdym wózku dla sprawdzenia, czy działa poprawnie.
Odnośnie do instrukcji użytkowania producent jest zobowiązany do dostarczenia instrukcji obsługi i konserwacji. Dokumentacja powinna zawierać takie elementy, jak opis całego systemu, informacje na temat eksploatacji wózków, obsługi i konserwacji oraz miejsca pracy. Wymagania te pokrywają się z wymaganiami z punktu 1.7.4.2 załącznika I dyrektywy maszynowej 2006/42/WE, jednak ze względu na konkretny typ maszyny są bardziej precyzyjne.
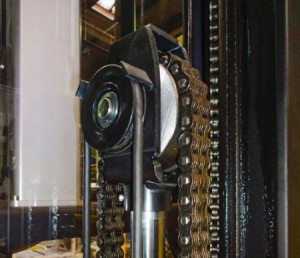
Jednym z problemów związanych z pełną oceną ryzyka jest brak informacji o sposobie zabezpieczenia elementów ruchomych napędów wózka (rys. 2).
O ile w standardowych wózkach widłowych takie rozwiązania są akceptowalne ze względu na operatora sterującego pojazdem, o tyle w wózkach samojezdnych konieczne jest zabezpieczenie takich stref. Należy w takim przypadku skorzystać z ogólnych norm, bazując na PN-EN ISO 12100. Kolejnym problemem jest odległość wózka w trakcie ruchu od konstrukcji stałych.
Zapewniając bezpieczną odległość 0,5 m, bazujemy na aktualnym stanie infrastruktury zakładu. Bardzo łatwo może dojść do sytuacji, w której pracownik pozostawi wzdłuż trasy wózka elementy takie jak np. palety, tworząc w ten sposób strefę zgniecenia. Samo wprowadzenie procedur w takim przypadku może nie być wystarczające.
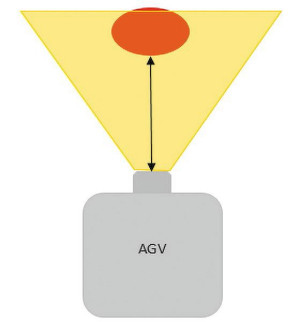
Norma PN-EN 1525 nie odnosi się również do odległości pomiędzy miejscem zatrzymania wózka od wykrytego obiektu (rys. 3).
W zależności od gabarytów pojazdu i ładunku, jaki transportuje, należy dobrać odpowiednią odległość na podstawie PN-EN 349.
Należy pamiętać, że pełnej ocenie ryzyka nie podlega wyłącznie sam wózek i jego zabezpieczenia, ale również cała trasa przejazdu oraz związane z nią zagrożenia.
Jeżeli chodzi o sam sposób prowadzenia wózków, nie ma szczególnych wymagań w tej kwestii. Na rynku dostępne są wózki AGV sterowane za pomocą taśmy magnetycznej lub taśmy refleksyjnej czy za pomocą przewodu elektrycznego umieszczonego w podłożu. Rozwiązaniem najbardziej nowoczesnym jest nawigacja laserowa odbłyskowymi tarczami umieszczonymi na ścianach. Wózek AGV ma skaner laserowy, który odbierając odbitą wiązkę laserową, oblicza kąt i odległość mijanych tarczy.
W artykule opisano przede wszystkim wymagania dla fizycznego zabezpieczenia ludzi przed zagrożeniami wynikającymi z ruchu wózków samojezdnych. Przeprowadzając pełny proces oceny ryzyka, należy zawsze patrzeć na maszynę całościowo, z uwzględnieniem jej pełnej dokumentacji. Stosując zalecenia normy PN-EN 1525 zharmonizowanej z dyrektywą maszynową, otrzymujemy sporą elastyczność w zakresie systemu bezpieczeństwa, co pozwala dostosować się zarówno do wymagań procesów, jak i całej infrastruktury zakładu.
W zależności od potrzeb można zastosować zabezpieczenia wyłącznie z ograniczeniem prędkości lub z wykorzystaniem środków wykrywania personelu, ale możliwe jest też łączenie ze sobą obu tych rozwiązań, co czyni transport bezobsługowy elastycznym systemem. Warto jednak pamiętać, że podczas oceny ryzyka nie należy opierać się wyłącznie na omówionej normie. Nadal obowiązują standardowe wymagania zawarte m.in. w PN-EN ISO 12100, PN-EN 349 czy też PN-EN ISO 14120.
Pomijając aspekty finansowe, rozwiązania w przemyśle oraz logistyce z zastosowaniem wózków AGV mocno ograniczają odpowiedzialność pracownika za bezpieczeństwo. W momencie przypadkowego pojawienia się osoby na trasie wózka nie liczy się na reakcję kierowcy - to system ma być tak skonstruowany, aby w odpowiedni sposób zatrzymać pojazd.
Norma PN-EN 1525 ze względu na rok wydania posiada wiele uogólnień oraz odniesień do nieaktualnych wymagań. Aktualnie trwają prace normalizacyjne nad normą PN-EN ISO 3691-4 "Wózki jezdniowe- Wymagania dotyczące bezpieczeństwa i sprawdzanie - Część 4: Wózki jezdniowe bez operatora i ich systemy", która ma zastąpić obecną normę. W dostępnym drafcie pojawiły się już nowe warunki dotyczące między innymi prędkości granicznych czy wymagania dla układów sterowania wg normy PN-EN ISO 13849-1, natomiast data publikacji nowej normy planowana jest na maj 2020 r.
Paulina Tyszko
inżynier bezpieczeństwa funkcjonalnego
ELOKON Polska