ODCHUDZANIE INSTALACJI
W pierwszej kolejności pojawia się wniosek: wzrost liczby urządzeń podłączonych do sieci wymusza wzrost liczby połączeń między urządzeniami. Mimo bardzo dynamicznego rozwoju połączeń bezprzewodowych (idealnych do integracji urządzeń mobilnych), w przemyśle cały czas podstawą są połączenie przewodowe (elektryczne lub światłowodowe). Dlatego obserwuje się bardzo dynamiczny wzrost ilości okablowania do transmisji danych. Instalowane są nowe czujniki monitorujące stan urządzeń i procesów (sygnały analogowe lub wolnozmienne cyfrowe). Rozproszone systemy sterowania wymieniają informacje między sobą. Nadrzędne sterowniki dbają o bezpieczeństwo i ciągłość produkcji całej fabryki. Taka liczba przewodów transmisyjnych wymaga, najlepiej jeszcze na etapie projektowania zakładu, przewidzenia miejsca na dodatkowe trasy kablowe oraz szafy sterownicze. W celu ograniczenia przestrzeni zajmowanej przez przewody zmniejsza się przekroje ich żył roboczych. Jeżeli kiedyś standardem przewodu czujnikowego było 0,75 mm², to obecnie jest to 0,25 mm² Pozwala to oszczędzić około 30% szerokości koryta i zmniejszyć wagę instalacji nawet o połowę.
Wartym wspomnienia zjawiskiem jest zmniejszanie liczby żył, niezbędnej do prowadzenia transmisji. O ile w protokołach typu "bus" osiągnięto już ten cel – systemy magistralowe funkcjonują na 2 żyłach, to w Ethernecie Przemysłowym cały czas standardem są przewody cztero- lub dwuparowe. A przecież można przesłać sygnał Ethernet dwoma żyłami. Korzysta z tego większość z nas, mając w domach Internet szerokopasmowy dostarczany w jednej z technologii DSL zwykłym kablem telefonicznym. Aktualnie trwają prace nad nowym standardem Ethernetu Przemysłowego, który będzie wykorzystywał tylko jedną parę żył.
BEZ EKRANU ANI RUSZ
Niezależnie od rodzaju transmitowanego sygnału (analogowo czy cyfrowo), większość przewodów z danymi trafia do tego samego koryta kablowego. Leżą obok siebie przewody z protokołami HART, ProfiBus czy ModBus. Niejednokrotnie specyfika urządzeń wymusza ułożenie przewodów do transmisji danych w bezpośredniej bliskości przewodów siłowych, np. w prowadnicach kablowych. Niesie to ryzyko wzajemnego zakłócania się sygnałów. Z tego powodu zdecydowana większość nowo instalowanych przewodów transmisyjnych to przewody ekranowane. Dla połączeń, które muszą pozostać giętkie (ramiona robotów, manipulatorów, plotery) stosuje się ekrany z plecionek lub owijek z cienkich drucików miedzianych. Dla połączeń nieruchomych można zastosować przewody ekranowane folią aluminiową – daje to kolejne kilka procent oszczędności na wadze i przestrzeni zajmowanej przez instalację elektryczną. Warto wspomnieć, że przewody z założenia przeznaczone do pracy w instalacjach przemysłowych (np. ProfiBus, Industial Ethernet) są konstruowane z maksymalnym zabezpieczeniem przed zakłóceniami, czyli z dwoma ekranami. Ekran z folii aluminiowej chroni sygnały przed zakłóceniami wzajemnymi (wysoka częstotliwość), a ekran z plecionki miedzianej chroni przed zakłóceniami o niższych częstotliwościach, pochodzących od np. kabli falownikowych.
A MOŻE 2 W 1?
Nie zapomnijmy, że urządzenia odbierające/wysyłające dane potrzebują zasilania w energię. Część z nich może mieć zasilanie bateryjne lub z małych ogniw fotowoltaicznych, ale do większości należy doprowadzić energię elektryczną… kablem. To generuje konieczność ułożenia kolejnych i kolejnych przewodów, na które potrzeba przestrzeni w korytach kablowych. Problem ten można obejść na dwa sposoby, w zależności od mocy zasilanego urządzenia. Przy małych mocach, do ok. 25W na pomoc przychodzi standard PoE+ (Power over Ethernet). Jest to technologia, dzięki której zwykły kabel ethernetowy kategorii 5 lub wyższej staje się jednocześnie kablem zasilającym urządzenie, do którego jest podłączony. Jeżeli nasze urządzenie pracuje w standardzie Ethernet (czujnik z przetwornikiem, kamera IP, switch, itp.) i obsługuje standard PoE+, nie musimy do niego ciągnąć osobnego kabla zasilającego. Zasilanie odbywa się dwoma parami skrętek, pod napięciem 50 V. Głównym ograniczeniem tej technologii jest zasięg, równy długości pojedynczego przewodu Ethernet, czyli 100 m i relatywnie mała moc. Trwają prace nad kolejną wersją standardu PoE (IEEE802.3bt), kiedy przy wykorzystaniu wszystkich 4 par skrętki będzie można obsługiwać urządzenia o mocy około 70 W, co rozszerzy funkcjonalność systemu na kolejne grupy urządzeń (kamery obrotowe, routery, terminale POS, itp.)
Dla większych mocy lub odległości stosuje się inne rozwiązanie – przewody z żyłami o różnym przekroju, w których grubsze żyły odpowiedzialne są za zasilanie, a cieńsze za transmisję danych. Pomysł nie jest nowy, wykorzystuje się go od lat w serwonapędach, gdzie pary żył o mniejszych przekrojach były odpowiedzialne za zabezpieczenie termiczne silnika oraz sterowanie hamulcem. Tradycyjna konfiguracja żył w takim przewodzie to np. 4G16 + (2×2×1), gdzie 4G16 oznacza trzy żyły fazowe plus czwarta żyła żółto-zielona (PE) o przekrojach 16 mm2 podłączone do zacisków silnika, a 2×2×1 to dwie pary sterujące o przekrojach 1 mm² (rys. 1). Aby zminimalizować zakłócenia, pary żył sterowniczych są osłonięte ekranem. Mimo, że sterowanie / przesył danych odbywa się dodatkowymi żyłami, nie ma to praktycznie wpływu na średnicę całego przewodu, gdyż cieńsze żyły układają się w wolnej przestrzeni między grubymi żyłami siłowymi.

Jeszcze bardziej różnorodną budowę mają przewody od enkoderów, które są zasilane prądem stałym DC. Dlatego w tych przewodach mamy zazwyczaj tylko 2 żyły o większym przekroju i dużo par cieńszych.
Doświadczenie zdobyte przy konstruowaniu przewodów typu serwo wykorzystano przy nowym standardzie sterowania serwonapędów – Hiperface DSL, który integruje w jednym przewodzie wszystkie sygnały niezbędne do funkcjonowania serwonapędu – zasilanie, sterowanie hamulcem i sprzężenie zwrotne z enkoderem. Przykładowa budowa takiego przewodu to 4G4+(2×1)+(2×0,34). Dzięki takiemu rozwiązaniu, zamiast dwóch osobnych przewodów (silnikowy i enkoderowy), wystarczy tylko jeden. Cóż za oszczędność miejsca!
Idea przewodów, w których połączono zasilanie i transmisję danych, rozszerza się o kolejne konstrukcje. W czasach dynamicznego rozwoju Ethernetu Przemysłowego należy zwrócić uwagę właśnie na przewody Ethernet z dodatkowymi żyłami zasilającymi o przekroju aż 1,5 mm² (rys. 2). Takim przewodem można zasilić i wysterować np. odległą wyspę zaworową, serwozawór czy sterownik, bo dostępna moc przy np. 24 V to ponad 300 W × 2 linie zasilające.
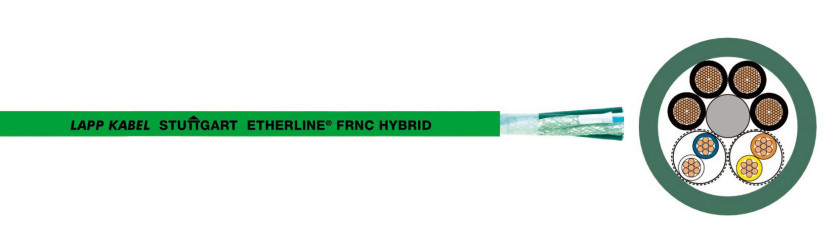
DUŻO PRZEWODÓW, MAŁE OBUDOWY
Rosnąca liczba przewodów stworzyła kolejny problem: konieczność wprowadzenia dużej liczby przewodów do obudów (puszek połączeniowych, szaf sterowniczych). W zanieczyszczonym środowisku hali przemysłowej nie można zrobić tego przez duże otwory w podłodze czy ścianie szafy. Wejścia do obudowy muszą być szczelne. Tradycyjnym rozwiązaniem są dławnice kablowe, ale dla cienkich przewodów transmisyjnych (przemysłowy przewód ethernetowy ma średnicę od 6 do 9 mm) należy stosować dławnice o gwincie montażowym M16. Nawet rozmieszczając je bardzo blisko siebie (pomijając niewygodę montażu i wątpliwą estetykę), osiągnie się niewielką gęstość wprowadzania przewodów.
Rozwiązaniem są wielowpusty kablowe, gdzie odległości między przewodami są na poziomie kilku milimetrów. Uzyskana za ich pomocą gęstość montażu jest około 2× większa niż za pomocą dławnic kablowych (rys. 3). Szczelność takich przepustów, dzięki zastosowaniu membrany żelowej, to IP68, czyli tyle co najlepszych dławnic kablowych. Oczywiście ten sposób montażu nie zabezpieczy przewodów przed wyrwaniem z obudowy tak dobrze jak dławnica kablowa, ale szafy sterownicze są umieszone zazwyczaj w miejscach oddalonych od ruchomych elementów maszyn, czy pracujących ludzi.
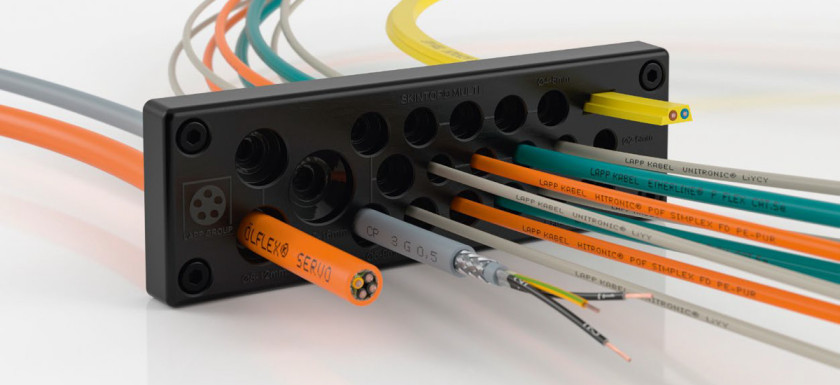
SZYBKIE PRZEZBRAJANIE MASZYN
Jedną z podstawowych cech fabryki realizowanej zgodnie z ideą Przemysłu 4.0 jest wysoka elastyczność produkcji, rozumiana jako zdolność do produkowania różnorodnych wersji tego samego produktu lub wręcz różnych produktów przy bardzo krótkim czasie potrzebnym na przezbrajanie maszyn. Cecha ta rozumiana jest także jako łatwość rozbudowy i modernizacji poszczególnych linii produkcyjnych w momencie dostępności np. nowszego, bardziej wydajnego osprzętu. Wąskim gardłem takich modernizacji jest okablowanie, którego modyfikacja (przełożenie/wymiana istniejących przewodów, dołożenie i podłączenie nowych) zajmuje relatywnie dużo czasu i wiąże się z ryzykiem popełnienia błędów przy podłączaniu dziesiątek, jeżeli nie setek, żył.
Odpowiedzią na te niedogodności są przewody zakończone złączami. Mogą to być złącza zamontowane przez pracowników utrzymania ruchu, ale też gotowe, zarobione fabrycznie przewody przyłączeniowe. Standardem w branży są np. gotowe paczkordy ethernetowe. Warto pamiętać, że w zastosowaniach przemysłowych, stary, poczciwy standard złączy RJ45 jest wypierany przez szczelne, odporne na uszkodzenia złącza M12 (kodowanie D lub kodowanie X) (rys. 4). Infrastruktura sterowania oparta na koncentratorach sygnałów (puszki I/O) i okablowanie paczkordowe jest dużo łatwiejsza do modernizowania i przebudowy.
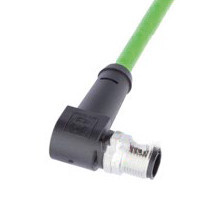
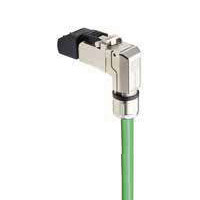
I znowu stajemy przed dylematem, jak wprowadzić takie oryginalne przewody ze złączami do wnętrza obudowy, w której znajduje się np. sterownik. Są co najmniej trzy różne rozwiązania. Pierwsze sprawdzi się w przypadku potrzeby wprowadzenia pojedynczych przewodów. Jest to specjalna, nieco większa od typowej, dławnica kablowa M25 z odpowiednim uszczelnieniem do cienkich przewodów. Wystarczy przełożyć przewód ze złączem przez dławnicę, na samym przewodzie założyć rozciętą uszczelkę i skręcić całość. Drugi sposób to zastosowanie złącza pulpitowego lub przelotowego, wystawionego na zewnętrznej ścianie obudowy. Daje to nam możliwość podłączania przewodów bez potrzeby otwierania obudowy. Trzeci sposób to, podobnie jak dla przewodów bez złączy, wielowpust montowany na powierzchni obudowy. Aby mógł obsługiwać przewody z zarobionymi złączami, klipsy uszczelniające są dwuczęściowe i wyciągane z ramki montażowej. Dzięki temu można wprowadzać przewody elektryczne, pneumatyczne i światłowody ze złączami o wymiarach nawet 30 na 90 mm. Szczelność połączenia na poziomie IP64 jest wystarczająca do większości zastosowań przemysłowych (rys. 5).
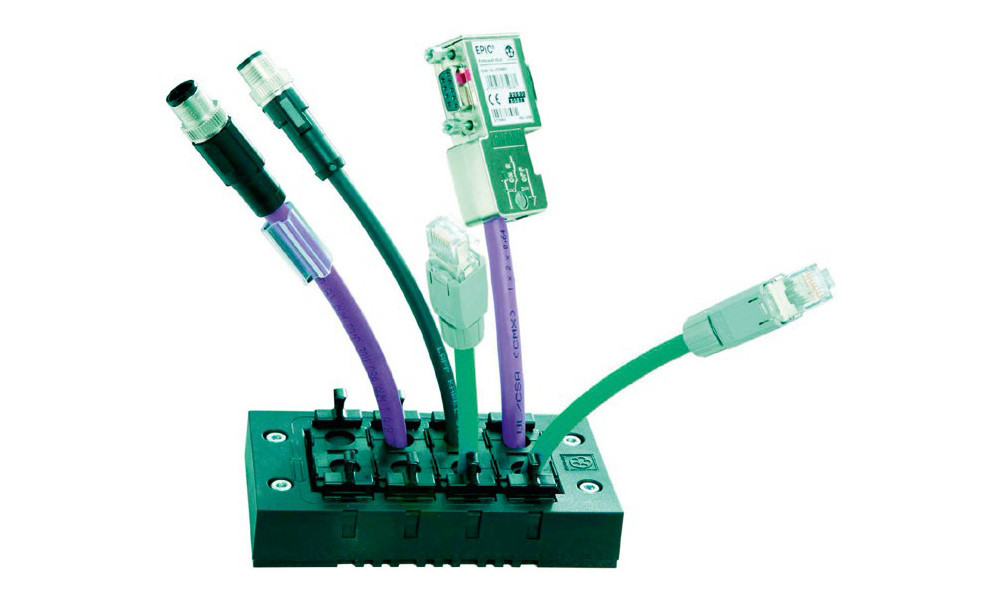
PODSUMOWANIE
Czwarta rewolucja przemysłowa na pewno wpłynie na wygląd instalacji elektrycznych w zakładach. Wzrośnie liczba przewodów do transmisji danych, przy jednoczesnym zmniejszaniu ich wymiarów i masy. Podstawą będą przewody ekranowane, coraz częściej wyposażone w gotowe do przyłączenia złącza. Należy się spodziewać nowych standardów połączeń, realizujących kilka funkcji jednocześnie (zasilanie i transmisja danych). Zmiany w okablowaniu wpłyną na sposoby montażu i wprowadzania przewodów do obudów, które stają się coraz bardziej kompaktowe. Wszystkie powyższe zmiany są od lat znane na rynku, czyli odpowiedzią na rewolucję przemysłową jest ewolucja systemów okablowania.
Mariusz Pajkowski
z-ca dyrektora ds. technicznych
Lapp Kabel
www.lappkabel.pl