Podobnie jak liniowy system transportowy XTS firmy Beckhoff, także XPlanar jest czymś więcej niż tylko kolejnym systemem napędowym: to kompletne, elastyczne rozwiązanie do transportu produktów. W przeciwieństwie do XTS oferuje jednak możliwość ruchu w dwóch osiach, co znacznie rozszerza zakres pozycjonowania i szeregowania karetek, uzupełniając go m.in. o możliwość wyprzedzania i synchronicznego przejazdu. To właśnie "lewitujące" karetki są najmocniejszą stroną systemu XPlanar: dzięki możliwości unoszenia się nad płytami bez dotykania ich powierzchni poruszają się one bowiem bezgłośnie i nie podlegają typowemu dla tych komponentów zużyciu.
Pełna elastyczność ruchu
Jak każdy system transportowy, także XPlanar ma za zadanie przenosić produkty z punktu A do B, tj. z jednej stacji roboczej do drugiej. Jednak w przeciwieństwie do tradycyjnych układów liniowych w jego przypadku stacje te nie muszą być rozlokowane w jednej linii, a nawet w określonej kolejności. Produkt jest bowiem transportowany tylko do tych stacji, które biorą udział w danym procesie produkcyjnym. Ruch w dwóch płaszczyznach ma jednak także i inne zalety, jak choćby możliwość wyprowadzenia danej karetki ze strumienia produktów czy tworzenia specjalnych „poczekalni” optymalizujących przebieg procesów wytwórczych. Co więcej, karetki wolniejsze mogą być wyprzedzane przez szybsze, co pozwala na realizację kilku kroków obróbczych jednocześnie. Każda karetka stanowi osobną oś sterowaną indywidualnie, ale w razie potrzeby jej ruch może zostać zsynchronizowany z ruchem innych karetek.
Dzięki sześciu stopniom swobody karetki mogą nie tylko dostarczać detale na określone stanowiska obróbcze, ale także wprowadzać je bezpośrednio do stacji i obracać w trzech płaszczyznach, zapewniając możliwość wielostronnej obróbki/ kontroli każdego wyrobu. Co więcej, każda może również realizować ruch w górę, w dół i po skosie. Funkcja przechyłu okazuje się szczególnie przydatna w sytuacji, gdy trzeba przyspieszyć ruch pojemnika wypełnionego po brzegi cieczą bez rozlania znajdującej się w nim substancji.
XPlanar: Bez zbędnych elementówSystem XPlanar cechuje się modułową architekturą składającą się wyłącznie z lewitujących ruchomych płytek, modułów silników, połączonych siecią EtherCAT G oraz komputera przemysłowego Beckhoff wraz z oprogramowaniem TwinCAT3. Komputer przemysłowy jest połączony z pierwszą płytą XPlanar, a następnie z modułami silników (XPLANAR) w topologii liniowej siecią Ethercat G. W efekcie całkowicie wyeliminowano dodatkowe elementy infrastruktury jak zasilacze czy specjalistyczny sprzęt sieciowy. Zgodnie z filozofią sterowania firmy Beckhoff bazującej na systemach PC Based, sterowanie odbywa się za pośrednictwem centralnego komputera przemysłowego, przenosząc wszystkie aspekty kontroli ruchu lewitujących paletek do oprogramowania TwinCAT 3 kontrolującego także pozostałe elementy maszyny. Ułatwia to koordynację systemu XPlanar z innymi komponentami instalacji, przeprowadzanie diagnostyki i optymalizację maszyny. Dzięki temu nowe funkcjonalności systemu można łatwo zintegrować z istniejącymi instalacjami, aktualizując oprogramowanie centralnego systemu sterowania. ![]() |
Modułowa konstrukcja
Mimo wykonywania złożonych ruchów system XPlanar cechuje się prostą konstrukcją i łatwością obsługi. Jego uruchomienie wymaga w praktyce podłączenia tylko dwóch przewodów – komunikacyjnego (EtherCAT G) i zasilającego. Całość elektroniki została zabudowana bezpośrednio w poszczególnych modułach, dzięki czemu mogą one od razu realizować swoje funkcje, a jednocześnie nie zajmują wiele miejsca: odległość między powierzchnią roboczą a konstrukcją nośną płyty napędowej wynosi zaledwie 4 cm.
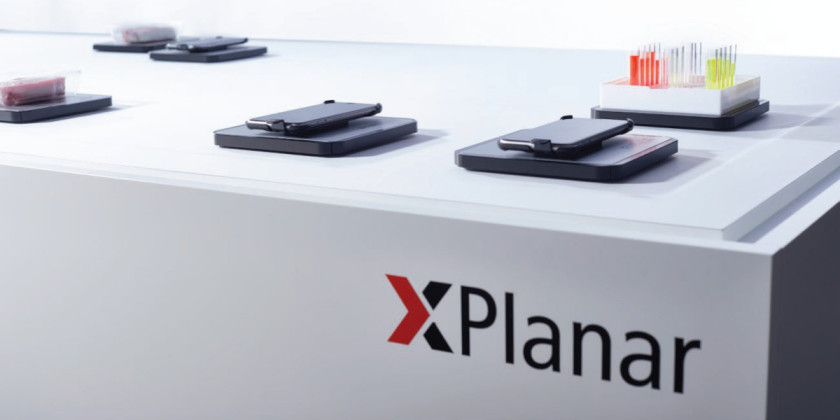
Każda z płyt o wymiarach 24×24 cm została pomyślana tak, by stanowić uniwersalną bazę, na podstawie której można zbudować niemal każdy system transportowy. W przyszłości ich asortyment zostanie uzupełniony o wariant umożliwiający obrót karetek o 360°. Same karetki dostępne są w kilku wersjach wymiarowych, różniących się dopuszczalnym obciążeniem. Najmniejsza, o bokach 95×95 mm, może unieść produkt o masie do 0,4 kg. Największa – o wymiarach 275×275 mm – bez problemu poradzi sobie z obciążeniem do 6 kg.
Mimo rozbudowanej konstrukcji obsługa systemu XPlanar jest bardzo prosta – a to dzięki zintegrowanemu oprogramowaniu TwinCAT, w którym każda karetka zobrazowana została jako odrębna oś serwo o sześciu stopniach swobody. Ponieważ w praktyce tak duży zakres ruchu nie zawsze jest potrzebny, system TwinCAT oferuje również możliwość ograniczenia jego złożoności. W takiej uproszczonej wersji każda karetka przedstawiona jest jako jednowymiarowa oś z możliwością rozszerzenia o inne płaszczyzny ruchu, np. w celu podniesienia, opuszczenia lub przechylenia karetki po dotarciu do stacji obróbczej. Aby zorganizować transport detalu, wystarczy więc zdefiniować trasę, po której ma poruszać się karetka, co znacznie ułatwia proces obsługi systemu.
Możliwości aplikacyjne
Elastyczność systemu XPlanar polega także na tym, że transport produktów może być realizowany nie tylko wzdłuż jednej, ale też równolegle na wielu trasach – z możliwością swobodnego przemieszczania karetek między nimi. Co istotne, funkcjonalność ta nie utrudnia obsługi systemu, a to dzięki modułowi TwinCAT Track Management, który zapewnia proste sterowanie złożonymi ruchami, takimi jak wyprzedzanie wolniejszych karetek czy kolejkowanie w „poczekalni”. Obsługę ułatwia zresztą także konstrukcja płyt napędowych umożliwiająca budowę niemal dowolnej liczby równoległych tras, w tym torów obejściowych i łączników z innymi strefami linii produkcyjnej. Aby przenieść karetkę z jednego toru na drugi, wystarczy w module Truck Management wywołać komendę zmiany trasy – bez definiowania szczegółowych reguł włączenia się do ruchu czy unikania kolizji. Co więcej, narzędzie oferuje także możliwość swobodnego przemieszczania karetki z punktu do punktu bez konieczności pokonania zdefiniowanej wcześniej trasy. Program automatycznie wysyła karetkę do określonego współrzędnymi punktu, samodzielnie dbając o to, by nie doszło do jej kolizji z pozostałymi elementami systemu.
Dążenie do zapewnienia maksymalnej elastyczności znalazło także wyraz w konstrukcji samych płyt napędowych. Płyty te można dowolnie ze sobą zestawiać, tworząc układy w pełni odpowiadające wymogom danej aplikacji – zarówno pod względem kształtu, jak i umiejscowienia (na podłodze, ścianie lub suficie). System można np. zaprojektować tak, aby pozostawić wolną przestrzeń na stacje robocze lub poprowadzić wokół poszczególnych stacji. Przekłada się to na redukcję kosztów organizacji transportu oraz zwiększenie dostępnej przestrzeni w hali produkcyjnej. Co więcej, system XPlanar można także w każdej chwili rozbudować przez dodawanie kolejnych płyt napędowych, aby np. uzupełnić go o dodatkowe stacje obróbcze lub usprawnić transport detali przez optymalizację toru na zakrętach.
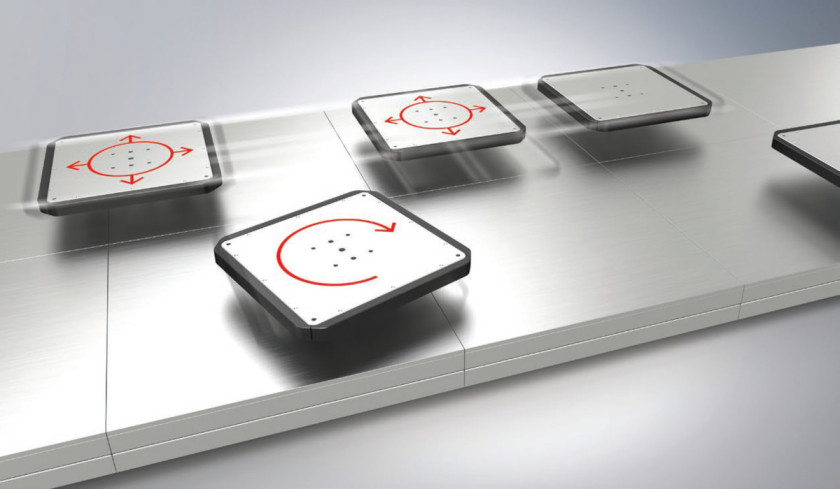
Pełna elastyczność pracy
Dzięki wymienionym funkcjonalnościom system XPlanar oferuje zupełnie nowe możliwości budowy maszyn i linii produkcyjnych. Opcji tych jest tak wiele, że firma Beckhoff postanowiła pomóc użytkownikom w jak najlepszym wykorzystaniu potencjału nowego rozwiązania, oferując – podobnie jak to było w przypadku systemu XTS – gotowe zestawy startowe. Składają się one z sześciu lub dwunastu płyt napędowych zabudowanych na konstrukcji nośnej, czterech karetek oraz małej szafy sterowniczej wyposażonej w wydajny komputer przemysłowy z oprogramowaniem i niezbędnymi elementami zasilania. Zestawy takie dają integratorowi możliwość przetestowania działania systemu w realnych warunkach produkcyjnych. A firmie Beckhoff pozwalają szybko reagować na zapytania i zgłoszenia użytkowników.
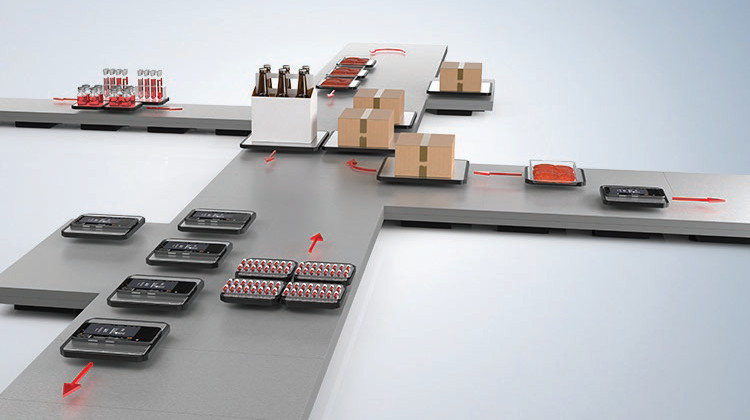
System XPlanar może być z powodzeniem stosowany do obsługi niemal wszystkich maszyn i linii produkcyjnych – pod warunkiem że waga i wymiary produktu umożliwiają efektywny transport z użyciem karetek. Tylko wówczas da się w pełni korzystać z funkcji elastycznego pozycjonowania karetek. Jego zalety docenią jednak przede wszystkim te branże, w których szczególne znaczenie mają czystość, łatwość czyszczenia, brak emisji zanieczyszczeń oraz cicha praca – a więc m.in. sektor spożywczy, farmaceutyczny, laboratoria oraz producenci półprzewodników (środowisko próżniowe). W razie potrzeby system można też dodatkowo pokryć szkłem albo folią z tworzywa sztucznego lub stali, która przyspiesza i ułatwia czyszczenie poszczególnych komponentów.
Perspektywy rynkowe
Opisywany system rozwiązuje wiele problemów związanych z transportem wyrobów na liniach produkcyjnych.
Przykładem niech będzie sektor spożywczy, a konkretnie produkcja słodyczy. Jeden z wytwarzających je koncernów od lat zmagał się z problemem zróżnicowania poszczególnych partii produktów. Niektóre z nich nieznacznie różniły się m.in. barwą polewy czekoladowej. I być może nie byłoby to powodem do zmartwień, gdyby nie fakt, że takie zróżnicowane produkty trafiały niekiedy do jednego opakowania. Przy produkcji sięgającej stu czekoladek na minutę wszelkie konwencjonalne metody sortowania okazywały się nieefektywne. Zadanie to można alternatywnie powierzyć robotom – z tym że kosztowałoby to sporo czasu, ograniczało prędkość linii i zredukowało w znacznym stopniu dostępną przestrzeń montażową. Dużo bardziej efektywnym rozwiązaniem jest zastosowanie indywidualnie sterowanych karetek, z których każda transportuje jedną pralinkę. Karetka taka na końcu linii produkcyjnej ustawia się odpowiednio do koloru polewy. W innym scenariuszu karetka transportująca pudełko czekoladek mogłaby automatycznie zbierać tylko te z nich, które cechują się takim samym kolorem. Oba warianty są zacznie szybsze i zajmują mniej miejsca niż np. wspomniany system bazujący na robotach.
Drugim najbardziej perspektywicznym odbiorcą systemu są laboratoria. System XPlanar oferuje im możliwość automatyzacji badań z zachowaniem wysokiej elastyczności doboru procedur. Co prawda większość próbek badana jest na obecność tych samych substancji, jednak rosnąca różnorodność zleceń sprawia, że laboratoria muszą być także przygotowane do przeprowadzania nietypowych analiz. System XPlanar ma tę zaletę, że oferuje opcję masowej analizy próbek i selektywnego wyboru niektórych z nich. Transportowane na karetkach, mogą w prosty sposób zostać wyprowadzone z toku produkcji lub zastąpione innymi próbkami. Funkcja ta ma istotne znaczenie także z punktu widzenia kontroli jakości.
Branży kosmetycznej system XPlanar umożliwia zaś indywidualizację produkcji pod kątem konkretnego klienta – np. rozlewanie perfum do spersonalizowanych flakonów oraz etykietowanie i pakowanie według specyfikacji odbiorcy.
XPlanar oraz XTS
Choć system XPlanar realizuje podobne funkcje jak liniowy system transportowy XTS, różni się od niego tym, że płyty napędowe nie są wyposażone w szynę prowadzącą do sterowania ruchem karetek, co przekłada się na większą elastyczność owego ruchu. Jednocześnie jednak ów element mechaniczny stanowi największą zaletę XTS. W porównaniu z polem magnetycznym sterującym „lewitującymi” karetkami zapewnia bowiem znacznie większą dynamikę ruchu na zakrętach, a w przypadku zakrętów pod dużym kątem – także większą prędkość pod obciążeniem. Stąd też wybór danego typu systemu powinien wynikać ze specyfiki danej aplikacji. Oba rozwiązania idealnie się uzupełniają.
Beckhoff Automation Sp. z o.o.
Żabieniec
ul. Ruczajowa 15
05-500, Piaseczno, Polska
tel.: +48 22 750 47 00
info@beckhoff.pl
www.beckhoff.pl
Więcej na www.beckhoff.pl