Roboty współpracujące - coboty
Widok robotów współpracujących (cobotów) w zakładach produkcyjnych oraz na targach branżowych już nie dziwi. Ich wyróżnikami są: lekka konstrukcja, kompaktowa budowa, zaokrąglone krawędzie, ukryte okablowanie i nieco inne oprzyrządowanie niż w przypadku tradycyjnych robotów.
Odmienna jest też funkcjonalność. Roboty te wyposażone są w szereg rozwiązań pozwalających na detekcję i reagowanie na kolizje z operatorami oraz elementami otoczenia, do tego wykonują one wolniejsze ruchy niż maszyny tradycyjne, co również podyktowane jest względami bezpieczeństwa.
Są one wreszcie łatwe do zaprogramowania i mogą pracować wspólnie z człowiekiem. Wszystko to zmienia sposoby ich wykorzystania w stosunku do tradycyjnych maszyn, pozwalając na tworzenie zupełnie nowych scenariuszy robotyzacji.
Korzyści związane z "cobotyzacją"
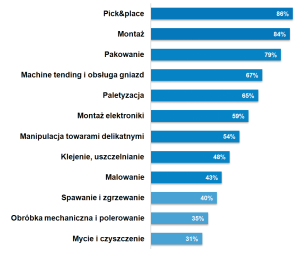
Dlaczego coboty, a nie tradycyjne roboty przemysłowe? Pytanie to zadaliśmy w celu uzyskania listy głównych powodów wrażania cobotów, a także ich cech, które odróżniają je od tradycyjnych robotów przemysłowych. W odpowiedziach pojawiały się przede wszystkim możliwości bezpośredniej współpracy z człowiekiem, a dokładniej: bezpiecznej współpracy.
Z racji braku konieczności stosowania wygrodzeń i wydzielania stref bezpiecznych, coboty stanowią też dobre rozwiązanie w przypadku niewielkiej ilości dostępnego miejsca. Roboty współpracujące "w szczególności stosowane są w tych obszarach, gdzie nie ma miejsca na instalację klasycznych systemów bezpieczeństwa dla robotów" - stwierdza przedstawiciel Fanuc Polska.
Coboty są "mobilne", tj. można je relatywnie łatwo przenieść do nowego zadania w innej części zakładu, a także łatwe w programowaniu. To ostatnie należy rozumieć jako brak konieczności konfiguracji przez specjalistów-robotyków - cobota można bowiem nauczyć sekwencji ruchów poprzez prowadzenie jego ramienia.
Dzięki temu są one wielozadaniowe i praktycznie nie generują dodatkowych kosztów przy zmianie wytwarzanego asortymentu lub nawet zmianie aplikacji. To ostatnie jest kluczowe przy wytwarzaniu krótkich serii produkcyjnych, o czym często mówi się w kontekście Industry 4.0.
Coboty to technologia coraz bardziej dojrzała, której historia komercyjna ma ponad 10 lat (licząc od pierwszego komercyjnego robota współpracującego Universal Robots). Chociaż idea stojąca za nimi jest niezmienna, maszyny te podlegają ciągłym unowocześnieniom. W tym zakresie respondenci wskazywali m.in.:
- dodawanie do cobotów nowych czujników dotyku i systemów zwiększających bezpieczeństwo obsługi,
- dalsze usprawnienia w zakresie programowania, systemy wykorzystujące sztuczną inteligencję,
- wprowadzanie nowych rodzajów manipulatorów, tworzenie oferty systemowej w zakresie osprzętu,
- rozwój możliwości komunikacji bezprzewodowej i głosowej z robotami,
- integracja kamer wizyjnych,
- zwiększanie zasięgu oraz wydajności przy zachowaniu bezpieczeństwa współpracy z ludźmi.
|
Nie tylko korzyści
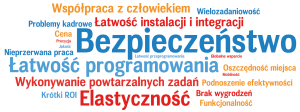
Pytanie, które stanowiło naturalne uzupełnienie tego o korzyści związanych z cobotami, dotyczyło minusów wdrożeń robotów współpracujących. W tym przypadku pojawiały się odpowiedzi, które wybrzmiewały już w analizie dotyczącej tradycyjnej robotyki przemysłowej. Przede wszystkim dotyczyły one obaw związanych z miejscami pracy.
Redukcja etatów dotyczyć ma "głównie stanowisk niewymagających kwalifikacji wyższych niż podstawowe", czemu dodatkowo sprzyja wzrost precyzji i wydajności pracy cobotów. Dostawcy tych ostatnich, podobnie jak producenci tradycyjnych robotów, wskazują tu oczywiście szereg aplikacji, gdzie robotyzacja prowadziła do tworzenia nowych miejsc pracy (np. poprzez zwiększenie wydajności produkcji i potrzebę jej rozbudowy o dodatkową kadrę).
Niemniej jednak - i nie ma się co oszukiwać - maszyny w wielu przypadkach po prostu ludzi zastępują lub są instalowane ze względu na braki kadrowe. Jest to zresztą prawidłowość powtarzająca się już od czasów pierwszej rewolucji przemysłowej, kiedy krosna tkackie i maszyny parowe postrzegane były przez robotników jako ich bezpośrednie zagrożenie. Prawda jest pewnie gdzieś pośrodku, aczkolwiek, przedstawiając wyniki bieżącego badania, zaznaczamy, że na pierwszym miejscu znalazły się właśnie kwestie pracownicze.
Drugą z grup najczęstszych wskazań była ta dotycząca bezpieczeństwa. Kluczową cechą cobotów jest możliwość ich pracy bez wygrodzeń, w bezpośrednim sąsiedztwie ludzi. Z tego powodu jednym z głównych pytań potencjalnych klientów jest: "czy na pewno są one bezpieczne?".
Biorąc pod uwagę fakt, że producenci cobotów wyposażają je w szereg funkcji bezpieczeństwa, ograniczają prędkość ruchu, itd. - można stwierdzić, że nowa generacja robotów jest rzeczywiście bezpieczna. Dodatkowo istnieją w tym zakresie normy ISO 10218-1 oraz ISO/TS 15066, jest też dyrektywa maszynowa, z którą roboty muszą być zgodne.
|
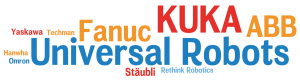
Z drugiej jednak strony coboty to cały czas maszyny o sporym ciężarze i poruszające się w przestrzeni wykraczającej poza ich podstawę. Znane są też przypadki cyberataków na systemy zrobotyzowane. Stąd też zdroworozsądkowym podejściem wydaje się zachowanie ograniczonego zaufania - analogicznie jak do każdej innej maszyny.
Cobotów bać się nie należy, ale warto pamiętać, co podkreśla Dariusz Kowalski z firmy Pilz, że "nie ma bezpiecznych robotów - bezpieczne mogą być aplikacje". Innymi słowy, myśląc o systemie zrobotyzowanym (a właściwie "scobotyzowanym"), trzeba brać pod uwagę cobota, jego chwytak, przemieszczane detale, warunki otoczenia, itd. - i w tym kontekście rozpatrywać zachowanie bezpieczeństwa.
Trzecia z grup uwag dotyczyła kwestii konfiguracji i obsługi. Choć producenci cobotów dbają o możliwość ich łatwego programowania, okazuje się, że użytkownicy wymagają szkoleń, podnoszenia kompetencji pracowników i wspierania tych ostatnich w programowaniu. Krzywa uczenia się jest o wiele mniej stroma niż w przypadku tradycyjnych robotów, które de facto programować musi specjalista.
Tak więc, o ile coboty rzeczywiście mogą być w zakładzie łatwo dostosowywane do różnych zadań i każdorazowo konfigurowane/programowane przez pracowników, o tyle nie dzieje się to aż tak szybko, jak reklamują to dostawcy tych maszyn. Dodatkowo występować mogą obawy o potencjalne uszkodzenia kosztownego sprzętu, które producenci starają się zmniejszać, udostępniając wirtualne narzędzia treningowe. Tak robi m.in. Universal Robots, zapewniając darmowy dostęp do swojej akademii szkoleniowej (
Zbigniew Proch
RENEX
- Jak widzi Pan przyszłość i teraźniejszość robotów współpracujących?
Roboty kolaboracyjne, czyli maszyny zdolne do bliskiej współpracy z ludzkim operatorem, które budowane są z myślą o maksymalnym ograniczaniu ryzyka spowodowania kontuzji człowieka czy kolizji z delikatnymi częściami, pojawiają się w ofertach kolejnych producentów robotów. Wydawać by się mogło, patrząc na presję ich wytwórców, że czeka nas przyszłość w fabrykach pełnych robotów "bez klatek".
Po początkowym zachwycie rynku nad tymi rozwiązaniami okazuje się jednak, że szybkość, siła i precyzja, które oferują nam klasyczne roboty są nie do przecenienia w kontekście obniżania kosztów produkcji przy jednoczesnym wzroście wydajności. Roboty współpracujące dają się z powodzeniem stosować w pewnych zadaniach, ale nie uważam, aby w najbliższym czasie mogły zastąpić klasyczne maszyny.
Dziś wyścig trwa i trudno powiedzieć, czy roboty kolaboracyjne dorównają wydajnością tradycyjnym konstrukcjom, czy też systemy bezpieczeństwa klasycznych robotów obniżą ryzyko we współpracy z człowiekiem do akceptowalnego poziomu.
Wielkość rynku i popularne marki
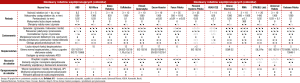
Sprzedaż cobotów rzadko kiedy stanowi główny obszar działalność firmy - tak jest jedynie w czterech przypadkach bieżącej statystyki. Większość ankietowanych dostawców, których poprosiliśmy o oszacowanie procentowej sprzedaży cobotów w ich całych obrotach, podawała typowo wartości wynoszące od kilku do dziesięciu procent. Innymi słowy - roboty współpracujące typowo stanowią uzupełnienie szerszej oferty dystrybucyjnej.
Dokładne wartości dotyczące sprzedaży realizowanej przez dostawców cobotów są nieznane. O ile globalny rynek robotów na bieżąco analizuje International Federation of Robotics, publikując coroczne duże raporty na ten temat, o tyle o cobotach wiemy relatywnie niedużo. Liderem branży jest duński Universal Robots, którego udziały w rynku - zdaniem przedstawicieli agencji BIS Research Analysis - wynoszą 60%.
Z danych podawanych przez samego UR wynika, że skumulowana liczba sprzedanych przez spółkę cobotów wyniosła do 2014 roku 3600 sztuk, zaś do końca 2018 roku przekroczyła 27 tys. egzemplarzy. Kolejne firmy na rynku to głównie dostawcy tradycyjnych robotów, którzy z czasem również rozszerzyli swój asortyment o coboty.
W branży działa też amerykański Rethink Robotics, pionier robotów współpracujących w USA. Firma zbankrutowała jesienią 2018 roku, zaś jej własność intelektualną wraz z prawami do znaków towarowych przejęła niemiecka HAHN Group. Ta ostatnia w styczniu 2019 podała informację, że planuje rozwijać markę i wprowadzać na rynek nowe produkty.
Na temat Universal Robots pisaliśmy nie bez powodu, bowiem firma wytypowana została jako najbardziej rozpoznawalny producent robotów współpracujących w Polsce. Praktycznie ex aequo sklasyfikowany został niemiecki dostawca robotów przemysłowych KUKA Roboter. Kolejne dwa miejsca rankingu popularności zajęły firmy Fanuc oraz ABB, czyli liderzy sektora tradycyjnej robotyki przemysłowej, zaś na dalszych miejscach znalazły się m.in.: Staubli, Yaskawa, Hanwha i Rethink Robotics.
Mówiąc o rynku, warto wspomnieć o dostawcach osprzętu i akcesoriów do robotów. Przykładowym jest OnRobot, który oferuje osprzęt (chwytaki oraz czujniki) do robotów współpracujących i tradycyjnych.
Tego typu firm jest więcej, czego dowodzi sukces uruchomionego trzy lata temu przez Universal Robots programu UR+. Jego celem było stworzenie "ekosystemu" firm zewnętrznych, które oferują produkty współpracujące z cobotami. Dzisiaj showroom UR+ zawiera około 130 certyfikowanych produktów, zaś w programie uczestniczy blisko 400 firm.
|
Przykładowe maszyny i ich ceny
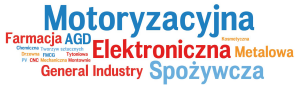
Myśląc o "typowym" robocie współpracującym, trzeba się przygotować na wydatek od 100 tys. zł w górę. Biorąc jako przykłady coboty wymienione w opublikowanym w magazynie APA badaniu rynku (wydanie z maja 2019, raport znaleźć można też na stronie AutomatykaB2B.pl), jednym z tańszych modeli jest CR-7IA/L firmy Fanuc, którego cena netto deklarowana przez firmę Alnea Robotics wynosi 80 tys. zł.
Z kolei za 25 tys. euro (około 107 tys. zł) dostępny jest Hanwha HCR-5 (w ofercie CoRobotics), a za kolejne 10% więcej, tj. 117 tys. zł, można nabyć w AB-Micro model UR5e firmy Universal Robots. W tabeli były też maszyny droższe - np. HC10 od Yaskawa Motoman to wydatek netto 42,5 tys. euro (około 181 tys. zł), zaś LBR iiwa 7 R800 firmy KUKA kosztuje 70 tys. euro (300 tys. zł).
Z tego, co udało się nam dowiedzieć, około 35 tys. euro kosztował robot Sawyer produkowany przez Rethink Robotics, zaś dwuramienny YuMi od ABB to szacunkowo wydatek ponad 40 tys. euro (około 170 tys. zł). Rozrzut cenowy jest spory, dodatkowo wymienione roboty mają też różne cechy (udźwig, zasięg, wyposażenie, itd.), przez co statystyka ma jedynie charakter informacyjny.
Powyższe zestawienie bazuje na danych pozyskanych z ankiet, aczkolwiek ceny cobotów znaleźć też można w opublikowanym przez Robotiq "Collaborative Robots Buyer’s Guide". Przykładowe koszty zakupu w dolarach (USD) to: ABB YuMi - 40 tys., AUBO i5 - 18 tys., Comau Aura (duży robot współpracujący o nośności 110 kg) - 80 tys., Fanuc CR-4iA - 45,7 tys., Fanuc CR-35iA - 87 tys., Franka Emika (cobot z osprzętem) - 12 tys., Kawasaki Duaro - 25 tys., Staübli TX2-60 - 40 tys. oraz Universal Robots UR10 - 40 tys.
Ceny dotyczą rynku amerykańskiego, aczkolwiek dają one dodatkowe wyobrażenie o kosztach zakupu. Do tych ostatnich trzeba zazwyczaj doliczyć koszt specjalistycznego osprzętu robota.
Więcej o robotach współpracujących!Jako rozszerzenie bieżącej analizy polecamy lekturę opublikowanego w APA w październiku 2017 roku kompendium " Wykorzystywane są one do przewozu różnych komponentów oraz innych ładunków i, podobnie jak roboty współpracujące, mają dzisiaj transformacyjny wpływ na przemysł. Pozwalają na zmiany procesów w obszarze intralogistyki oraz magazynowym i stają się coraz bardziej dostępne kosztowo. Przemysł produkcyjny i logistyka magazynowa![]() Roboty mobilne występują w wielu rodzajach, jeżeli chodzi o sposób transportowania ładunków, nośność, możliwości manewrowania czy metody nawigacji. Generalnie wyróżnić tu można AGV pojedynczego załadunku, które mają postać platformy, na której umieszcza się paletę, pojemnik lub bezpośrednio transportowany towar, a także pojazdy holownicze. O ile te pierwszej są zwrotniejsze, bardziej kompaktowe i sprawdzają się na krótkich i średnich dystansach, o tyle wersje holujące transportować mogą wiele przyczep i na większe odległości - w dużych magazynach, pomiędzy budynkami, itd. Występują też odmiany łączące obydwa rodzaje transportu. Główne zastosowanie AGV jest jasno zdefiniowane - jest nim automatyczny transport towarów. Tego typu aplikacja może być rozszerzona o automatyczne pobieranie i odkładanie towarów (pojemników, palet, itd.), zaś transport odbywać się może w obrębie magazynu lub pomiędzy magazynem a obszarem produkcji.
Warto dodać, że prawdopodobnie najpopularniejszym sposobem wdrażania AGV jest metoda "najpierw wypróbuj, później rozbudowuj". Ma ona dwuetapowy przebieg - najpierw odbiorca decyduje się na wdrożenie pilotażowe, gdzie sprawdza działanie AGV w realnych warunkach, tj. we własnych procesach, później podejmuje decyzję o rozbudowie posiadanego parku robotów. Tak dzieje się szczególnie w firmach mniejszych oraz tych, które wcześniej nie korzystały ze zautomatyzowanego transportu. Z drugiej strony blisko 40% odbiorców podczas planowania wdrożeń od razu stawia na system złożony z wielu wózków AGV. Przykładem jest branża automotive, która roboty mobilne zna i ma bardzo konkretne potrzeby intralogistyczne z nimi związane. Czasami też sama aplikacja wymaga wdrożenia od razu kilku wózków, które zastępują tradycyjne przenośniki. Jakie AGV i za ile?![]() Asortyment dostępnych na rynku robotów mobilnych jest coraz szerszy, zaś u dostawców AGV znajdziemy wózki o nośności od kilkudziesięciu kilogramów do 1 tony i większe. Jakie wersje są u nas w kraju najpopularniejsze? Na pytanie to nie ma jednoznacznej odpowiedzi, bowiem w redakcyjnym badaniu rynku pojawiły się zarówno wskazania: "poniżej 100 kg", "w granicach 200-500 kg", jak też "raczej do 1 tony". Jeden z respondentów stwierdził: "najczęściej odbiorców interesuje zakres od 200-500 kg, ale 1 tona cieszy się także dużym zainteresowaniem". Z kolei cytując innego: "popularne są roboty mobilne o udźwigu 100 i 200 kg, ale w logistyce magazynowej [jest to] bliżej 1000 kg". Ostatni z komentarzy stanowi ważne wskazanie, bowiem rzeczywiście rodzaj stosowanego robota jest silnie powiązany z aplikacją, a pośrednio też z branżą. Przykładowo w zastosowaniach w farmacji, przemyśle lekkim, wdrożeniach w centrach logistycznych - typowe nośności będą nieduże. Inaczej jest w przemyśle metalowym i generalnie przemyśle ciężkim, a także często motoryzacji, gdzie zazwyczaj stosowane są większe roboty mobilne. Ceny AGV są bardzo zróżnicowane, zależnie od nośności, parametrów technicznych, marki i innych czynników. Przykładowo Weasel firmy SSI Schäfer kosztuje od 10 tys. euro netto, Formica 1 marki Aformic to wydatek około 40 tys. euro, zaś AVG firmy KUKA kosztuje 90 tys. euro. Z kolei wózek mobilny ES Smart polskiej firmy Europa Systems to wydatek od 130 tys. zł. Innymi słowy, początkiem zakresu jest około 50 tys. zł, zaś końcem - 500 tys. zł lub więcej.
AGV w kontekście Industry 4.0![]() Na robotach mobilnych montowane są różnego rodzaju adaptery, podajniki rolkowe czy przenośniki, które pozwalają na pobieranie i odkładanie detali, przenoszenie palet i generalnie automatyczną współpracę robota z magazynem i linią produkcyjną. Na AGV można też zamontować cobota lub wręcz kupić tego typu gotowy system, co stanowi bardzo uniwersalne rozwiązanie produkcyjno-logistyczne. AGV, po kilkudziesięciu latach ich rozwoju, to nowoczesne, "inteligentne" i często też autonomiczne maszyny. Ich producenci wyposażają je w zaawansowane czujniki (skanery laserowe, kamery), co, w połączeniu z odpowiednim układem sterowania, zapewnia nawigację w rzeczywistym, zmieniającym się środowisku oraz możliwość dynamicznej rekonfiguracji i zmian profilu ruchu. Respondenci wskazywali też na wykorzystanie rozwiązań sztucznej inteligencji, które de facto służą głównie zwiększaniu autonomizacji ruchu. Roboty mobilne zapewniają wreszcie możliwość śledzenia produkcji i zadań logistycznych. Ich dostawcy oferują zazwyczaj oprogramowanie do zarządzania zautomatyzowanym transportem z wykorzystaniem floty wózków. Taki software często też ma interfejs do systemu nadrzędnego - np. WMS (Warehouse Management Systems) czy MES/ERP (Manufacturing Execution System / Enterprise Resource Planning). Takie połączenie zapewnia automatyczną kontrolę wykonywania zadań, a także elastyczność w ich ustalaniu, zależnie od potrzeb i bieżących priorytetów. Wpisuje się ono też w koncepcję Przemysłu 4.0, która zakłada wymianę danych oraz integrację systemów produkcyjnych i zarządzania.
Obawy dotyczące bezpieczeństwa i niezawodności![]() Pomimo wielu korzyści, wdrożenia robotów mobilnych mają też minusy. Obawy pracowników dotyczące AGV są pokrewne tym cytowanym w rozdziale dotyczącym cobotów. W odpowiedziach ankietowych najczęściej wymieniane były kwestie bezpieczeństwa. Wózki samojezdne wyposaża się w czujniki i inne zabezpieczenia, w części przypadku poruszają się one też po ustalonych trasach. Pomimo to oraz pomimo jak najlepszego przygotowania całej koncepcji systemu, nie można wykluczyć wpływu wydarzeń losowych - pojawiania się na trasie ludzi, przedmiotów i innych pojazdów. Nieodzowną cechą AGV jest ingerencja w przestrzeń magazynu czy hali fabrycznej, stąd też bezpieczeństwo zawsze będzie jednym z głównych tematów podejmowanych przez dostawców w rozmowach z klientami. Roboty mobilne są daleko bardziej krytycznymi elementami instalacji produkcyjnych niż coboty, bowiem odpowiadają za dostarczanie komponentów, odbiór produktów i inne zadania intralogistyczne. Ich nieplanowane zatrzymania mogą negatywnie wpływać na wydajność produkcji, stąd też wiele obaw odbiorców dotyczy właśnie kwestii awaryjności - znalazła się ona na drugim miejscu!
We wcześniejszych rozdziałach porównywaliśmy AGV z tradycyjnymi przenośnikami. O ile wielu respondentów stwierdziło, że roboty "z powodzeniem zastępują tradycyjne systemy transportowe", o tyle pojawiły się też głosy, że "nie są tak wydajne jak przenośniki". Jak to zwykle bywa w praktyce - to zależy. Zależy od aplikacji, od przenoszonego towaru, zależy od zakładu. W odpowiedziach wybrzmiały również uwagi dotyczące "zabierania miejsc pracy", czyli redukcji zatrudnienia w obszarze magazynów i produkcji. Pojawiły się też kwestie problemów z wdrożeniem, czego przykładem jest pytanie jednego z odbiorców "czy będziemy umieli to wdrożyć i czy dostaniemy support techniczny od producenta?". Można sądzić, że ten rodzaj problemów rozwiązywany jest przez inżynierów wsparcia samego dostawcy, których obecność jest obowiązkowa podczas wdrażania projektów z robotami mobilnymi.
AGV w polskich realiach![]() W ocenie badanych przez nas dostawców branżowych krajowy rynek AGV jest zróżnicowany, jeżeli chodzi o dostępne roboty mobilne i popularność konkretnych marek. Bazując na odpowiedziach ankietowych (przy czym nie należy ich traktować jako informacji o udziałach firm w rynku czy też liczbie sprzedawanych jednostek), najpopularniejszym u nas producentem jest duński Mobile Industrial Robots. W zestawieniu praktycznie ex aequo znalazły się też: rodzimy producent robotów mobilnych i innego rodzaju systemów robotycznych oraz mechatronicznych, którym jest WObit, oraz japoński Omron. Ten ostatni, po przejęciu kilka lat temu firmy Adept Technologies, systematycznie rozszerza ofertę w zakresie AGV, regularnie prezentując swoje roboty mobilne również na targach branżowych w Polsce. Omawiane zestawienie zawiera również kilka innych popularnych marek - m.in. KUKA Roboter, SEW-Eurodrive (prawdopodobnie jako jedyna firma wytwarza wózki mobilne zasilane bezprzewodowo), a także polską markę RB Poland. Warto tutaj również wskazać innych polskich producentów AGV, takich jak VersaBox, Octant oraz Myzer.
Drugim ze wskazań było: ogólnie zastosowania w magazynach i logistyce. Branże wymieniane rzadziej, ale wyróżniające się na tle pozostałych, to: produkcja elektroniki, sektor spożywczy i napojowy oraz FMCG. Liczba wskazań z nimi związanych była jednak kilkakrotnie mniejsza niż dla motoryzacji czy magazynów.
Cała branża automatyki. Twoje pytania.
Poszukuję produktu lub usługi
Chcę skontaktować się z firmą
Mam pytanie ogólne
Zapytania ofertowe
Unikalny branżowy system komunikacji B2B
Znajdź produkty i usługi, których potrzebujesz
Katalog ponad 7000 firm i 60 tys. produktów
|