Oprócz podstawowej roli, jaką jest zmniejszenie tarcia, środki smarne, w zależności od składników użytych do ich produkcji, zapewniają dodatkowe korzyści. Są to przede wszystkim: uszczelnianie, zapobieganie rozwojowi korozji, przewodzenie ciepła (chłodzenie albo ogrzewanie powierzchni) i usuwanie zanieczyszczeń. Najlepiej sprawdzi się smar zapewniający adekwatną do danych potrzeb kombinację tych właściwości. Ponadto środki smarne mogą mieć różną konsystencję (ciekłą, stałą, półpłynną). Wybór zatem jest szeroki i przez to niełatwy, zwłaszcza że niewłaściwie dobrany smar może skrócić żywotność i zwiększyć prawdopodobieństwo awarii.
Klasyfikacja
Środki smarne obejmują: oleje o małej lepkości, oleje o dużej lepkości, smary oraz stałe środki smarne. Pierwsze zapewniają najmniejszy opór ruchu. Oleje o dużej lepkości tworzą grubsze warstwy, dzięki czemu są zalecane przy większych obciążeniach i niższych prędkościach. Generalnie oleje, dzięki temu że łatwo się rozprowadzają, nadają się do smarowania maszyn, w przypadku których demontaż jest trudny albo niemożliwy. Z drugiej strony nie są zalecane w tych, w których występują zabrudzenia, ponieważ te zmieszane z olejem zwiększają tarcie.
Smary mają konsystencję półstałą. Generalnie stosuje się je, gdy użycie oleju nie jest praktyczne albo wygodne. W związku z tym są używane w maszynach uruchamianych z przerwami, trudno dostępnych do częstego smarowania, pracujących w ekstremalnych warunkach (temperaturze, ciśnieniu, obciążeniach udarowych i z małą prędkością przy dużym obciążeniu). Oprócz tego, gromadząc się w szczelinach powiększonych przez zużycie, wydłużają żywotność elementów wcześniej smarowanych olejem. Stałe (suche) środki smarne z kolei najlepiej sprawdzają się w wysokich temperaturach.
Parametry olejów
W przypadku olejów wprowadzana jest dalsza klasyfikacja na trzy kategorie. Różnią się one właściwościami, z których najważniejsze w tytułowym zastosowaniu są: lepkość, temperatura płynięcia oraz temperatura zapłonu. Jeżeli chodzi o pierwszy parametr kluczowe znaczenie ma współczynnik lepkości, który charakteryzuje zmienność tej wielkości przy zmianie temperatury.
Im jest większy, tym środek smarny jest stabilniejszy w wysokich i niskich temperaturach, a im mniejszy, w tym większym stopniu temperatura wpływa na jego lepkość. Temperatura płynięcia jest najniższą, w której olej jeszcze nie zamarza. Ostatnia to z kolei temperatura, w której opary środka smarnego albo ich mieszanina z powietrzem mogą się zapalić. Jest to zatem wskaźnik zagrożenia pożarowego, jakie niesie ze sobą dany olej w czasie transportu i magazynowania.
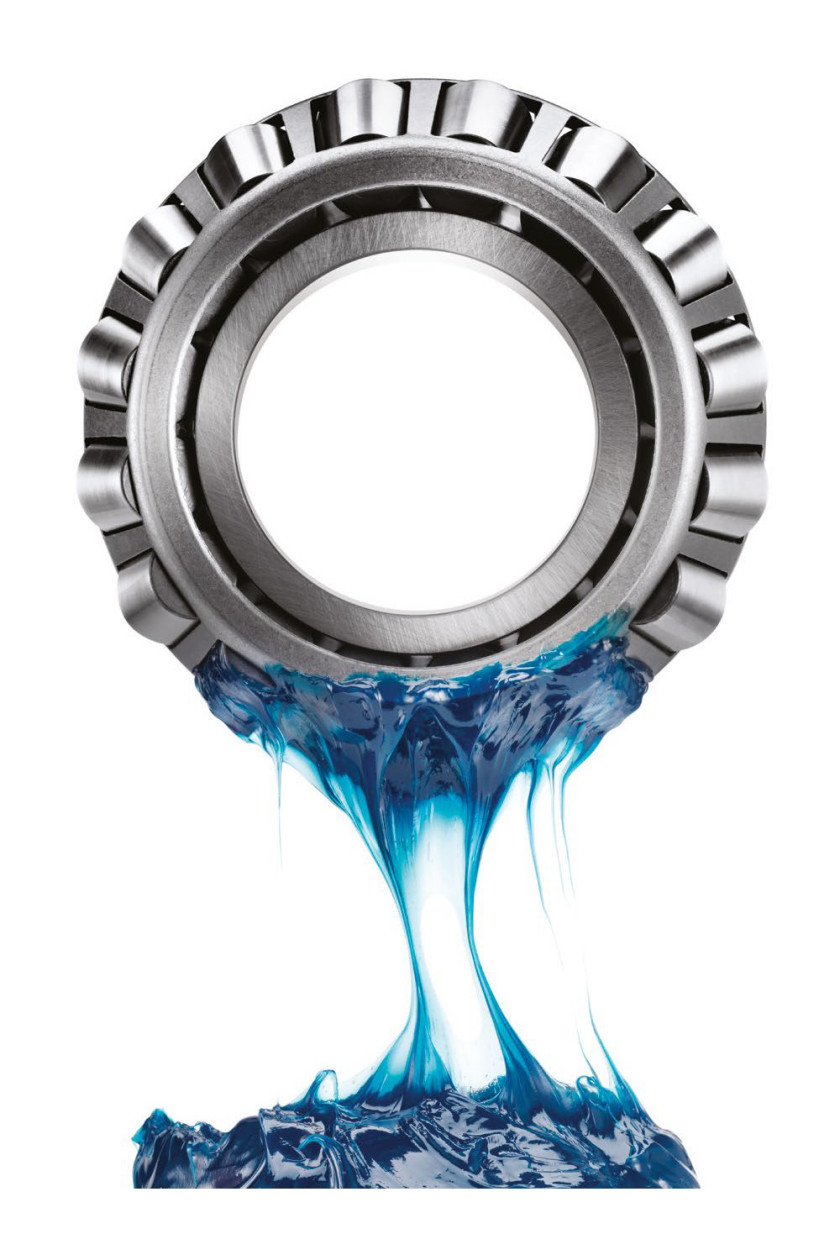
Co wyróżnia oleje syntetyczne?
Wyróżnia się następujące typy olejów: naturalne, mineralne, syntetyczne. Pierwsze pozyskuje się z roślin lub tłuszczów zwierzęcych. Ze względu na ich nietrwałość i utratę właściwości w wysokich temperaturach nie stosuje się ich do smarowania maszyn. Oleje mineralne są natomiast produktem przetwórstwa ropy naftowej. Są wrażliwsze na zmiany temperatury (ich wskaźnik lepkości wynosi typowo od 95 do 100, a w przypadku wysokorafinowanych olejów mineralnych do 120) i bardziej lepkie niż oleje syntetyczne i środki smarne o stałej konsystencji. Ich temperatura płynięcia mieści się w przedziale od –6°C do –60°C, ale typowo wynosi –20°C. Ponadto mają niską temperatura zapłonu, więc są łatwopalne.
Oleje syntetyczne opracowano jako alternatywę dla mineralnych, o właściwościach ulepszonych względem tych ograniczających stosowanie smarnych produktów naftowych. W przeciwieństwie do mineralnych, syntetyczne więc: nie zawierają zanieczyszczeń, dzięki czemu nie tworzą osadów, mają wyższy wskaźnik lepkości (powyżej 120), temperatura ich płynięcia mieści się przeważnie w przedziale od –30°C do –50°C, a ze względu na wysoką temperaturę zapłonu, są słabo palne. Z drugiej jednak strony są droższe i mają słabsze właściwości smarne niż oleje mineralne. Rekompensują to różne dodatki.
Dodatki
Oleje przemysłowe, w których bazowym środkiem smarnym są oleje mineralne albo syntetyczne, zawierają różne dodatki. Wyróżnia się kilka ich typów, w zależności od tego, które właściwości oleju wzmacniają. Przykładem są dodatki, które zabezpieczają powierzchnie kontaktowe przed przedwczesnym zużyciem i utlenianiem, dodawane m.in. do olejów przeznaczonych do użytku w ekstremalnych temperaturach. Stosuje się również środki, które tworzą dodatkotarciu w przypadku bardzo dużych obciążeń, przykładowo w przekładniach. Niektóre dodatki zmniejszają tarcie i poprawiają wskaźnik lepkości, zwiększając stabilność oleju w ekstremalnych temperaturach. Środki obniżające temperaturę płynięcia polepszają płynność olejów w niskich temperaturach. Dodatkiem są także inhibitory utleniania, dzięki którym oleje zachowują właściwości smarne nawet w ekstremalnych warunkach pracy. W przypadku kontaktu chronionej powierzchni z wodą i zawilgocenia stosuje się inhibitory korozji. Dyspergatory i detergenty z kolei rozdrabniają zanieczyszczenia i oczyszczają powierzchnie kontaktowe, co zapobiega tworzeniu się na nich osadów i rdzy, nawet jeżeli dłuższy czas się względem siebie nie przemieszczają. Środki przeciwpienne z kolei zapobiegają powstawaniu piany, której pęcherzyki zmniejszają skuteczność smarowania. Może się ona wytworzyć przykładowo na skutek reakcji zachodzących między różnymi dodatkami.
Smary
Smary to półstałe produkty dyspersji środka zagęszczającego w oleju, uzupełnione o składniki nadające im specjalne właściwości. Olej bazowy i dodatki odpowiadają za właściwości smarne, zagęszczacz natomiast pełni funkcję ośrodka, w którym utrzymują się olej oraz pozostałe składniki. Nadaje on smarowi półstałą konsystencję. Zagęstnik uwalnia olej i dodatki dopiero w reakcji na czynniki zewnętrzne, jak ruch, wibracje lub temperaturę. Bazowym środkiem smarnym jest olej mineralny albo syntetyczny. Zagęszczaczem są przeważnie mydła metaliczne na bazie m.in. litu, sodu, wapnia. Wybierając smar, pod uwagę należy wziąć jego właściwości.
Taką jest łatwość jego pompowania pod ciśnieniem. Wodoodporność z kolei charakteryzuje niezmienność właściwości smarnych przy kontakcie z wodą. Ważna jest też konsystencja smaru, która zależy od rodzaju i iloilości użytego zagęszczacza oraz lepkości oleju bazowego. Charakteryzuje ją penetracja, która wyraża głębokość zanurzenia znormalizowanego stożka w próbce smaru. Im jest większa, tym jest płynniejszy. Kolejny parametr to temperatura kroplenia, czyli najniższa, po podgrzaniu do której smar zachowuje swoją konsystencję. Powyżej temperatury kroplenia zaczyna płynąć.
Istotne są też: odporność na utlenianie, wysokie i niskie temperatury. Smary popularne w przemyśle to: aluminiowy (często stosowany w maszynach spożywczych), wapniowy (o niskiej temperaturze kroplenia), litowy (łatwy do pompowania, o temperaturze kroplenia około +180°C), polimoczniokowy (o temperaturze kroplenia powyżej +240°C), sodowy (o temperaturze kroplenia +200°C, tani, zabezpiecza przed korozją).
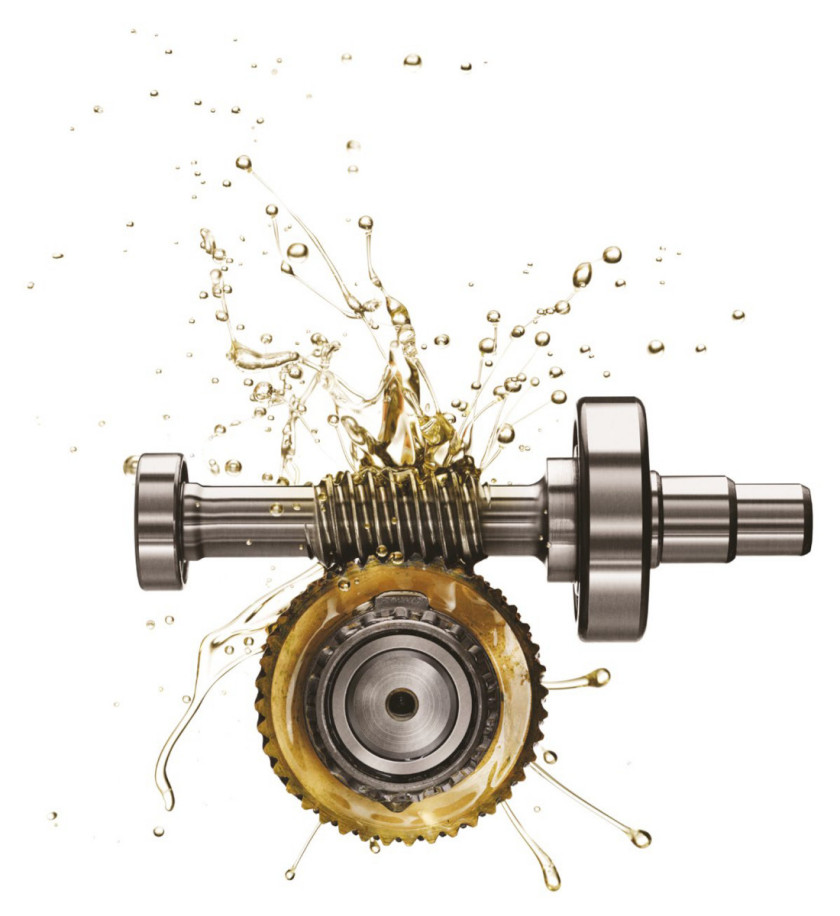
Smary stałe (suche)
Tytułowe środki smarne wypełniają lukę w dziedzinie smarowania w zastosowaniach, w których smary płynne i półpłynne są niepraktyczne albo nieodpowiednie. Przykładowo są zalecane, jeżeli nawet w ekstremalnych warunkach wymagane jest, żeby powierzchnie kontaktowe były skutecznie oddzielone, a środek smarny pozostawał na swoim miejscu. W związku z tym smary suche są często używane, gdy na powierzchnie ślizgowe wywierany jest duży nacisk w warunkach tarcia granicznego i mieszanego, przy bardzo małych prędkościach albo gdy środek smarny powinien zachować skuteczność w szerokim zakresie temperatur (lotnictwo, technologie kosmiczne i wojskowe, przemysł samochodowy). Smarowanie suche smarami stałymi jest również wymagane w środowiskach agresywnych, w wysokiej próżni, m.in. w reaktorach jądrowych i generalnie wówczas, gdy należy unikać zanieczyszczenia olejami lub smarami. Popularne materiały suchych smarów to: dwusiarczek molibdenu, teflon, grafit, azotek boru, fluorek wapnia, fluorek ceru, dwusiarczek wolframu. Najpopularniejsze są pierwsze trzy.
Główne zalety i ograniczenia dwusiarczku molibdenu to: doskonała przyczepność, szeroki zakres temperatur pracy, ochrona przed korozją ciernią, zapobieganie poślizgom, duża obciążalność, higroskopijność, utlenianie. Grafit wyróżniają: doskonałe właściwości smarne w obecności wilgoci, ochrona przed korozją ciernią, stabilność temperaturowa, mały współczynnik tarcia w wysokiej temperaturze. Nie można go używać w wysokiej próżni. Teflon z kolei zapewnia poślizg, jest odporny i obojętny chemicznie, ma mały współczynnik tarcia przy małym obciążeniu, ale jednocześnie niską temperaturę topnienia i małą przewodność termiczną.
Smarowanie w praktyce: łożyska
Wybór odpowiedniego do potrzeb środka smarnego to pierwszy krok dla zapewnienia wydajnej i bezawaryjnej pracy ruchomych części maszyn. Równie ważne jest jego właściwie zaaplikowanie, począwszy od przygotowania części do smarowania, przez dobór ilości smaru, po jego rozprowadzenie. Zalecenia w tym zakresie przedstawiamy na przykładzie łożysk – niewłaściwie smarowanie to jedna z głównych przyczyn awarii i przedwczesnego zużycia tych komponentów.
Najpierw trzeba zadbać o czystość łożysk – suche i bez zabrudzeń powierzchnie kontaktowe łożysk i bieżni są lepiej zwilżalne. Usuwając resztki zużytego smaru, unika się także reakcji chemicznych pomiędzy nim a nowo aplikowanym środkiem. Z czyszczenia można ewentualnie zrezygnować, jeżeli nowo kupione łożyska zostały już przez producenta smaru kompatybilnego chemicznie z tym, którego chcemy użyć. Po wyczyszczeniu łożyska, jeśli nie zostaną od razu nasmarowane, należy na czas magazynowania zabezpieczyć cienką warstwą smaru albo powłoką antykorozyjną.
Odpowiednia ilość smaru gwarantuje, że powierzchnie kontaktowe będą chronione przez zakładany czas eksploatacji. Nieprawidłowe jest zarówno nadmierne smarowanie, jak i niedosmarowanie. W drugim przypadku niedostateczna ilość smaru nie zabezpiecza przed tarciem na styku łożysk i bieżni. Nadmiar smaru, o ile poza obszarem kontaktu nie ma miejsca na jego gromadzenie się, zwiększa natomiast tarcie wewnętrzne. Wymagana ilość środka smarnego zależy od konstrukcji i prędkości roboczych. W jej określeniu pomocne są dane katalogowe łożysk.
Łożyska zawsze należy smarować czystym, świeżym środkiem, w czystym, suchym otoczeniu. W przypadku małej ilości smaru można skorzystać ze strzykawki – łatwo wtedy kontrolować ilość środka, zaś cienka końcówka ułatwia aplikację i zwiększa jej dokładność. W przypadku większych łożysk używa się smarownic.
Ważna jest też właściwa procedura docierania, podczas której smar jest równomiernie rozprowadzany wokół elementów łożyska i formowany jest pierścień smarowy, który zapewnia uwalnianie oleju bazowego w odpowiedniej ilości. Prawidłowo wykonane docieranie usuwa także nadmiar smaru. Trzeba je wykonywać zgodnie z instrukcją producenta. Ważne, żeby w czasie docierania łożyska obracały się w tym samym kierunku, co docelowo. Najlepiej jest też przeprowadzać je w miejscu ich pracy.
Nasmarowane łożyska powinno się oddać do użytku. Jeżeli mają zostać zmagazynowane trzeba je zabezpieczyć przed wpływem otoczenia, na przykład owijając w papier antykorozyjny, i umieścić w czystym, suchym miejscu.
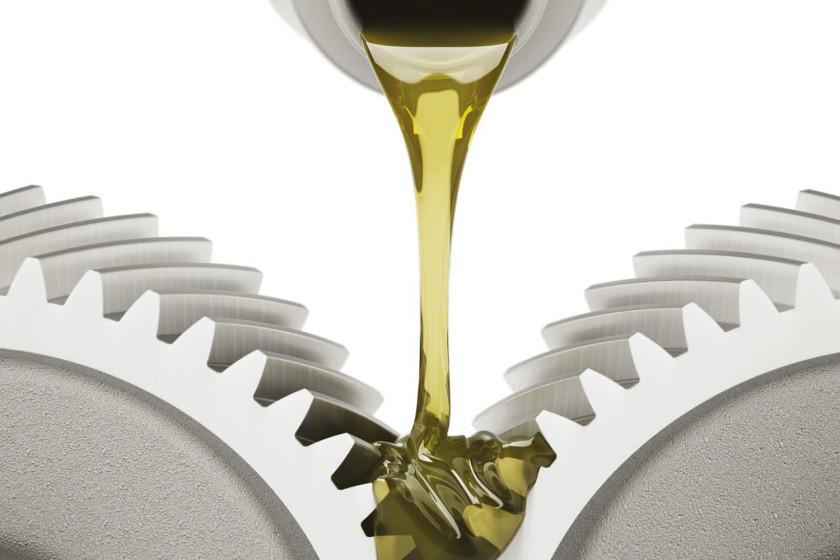
Smarowanie ręczne vs automatyczne
Automatyczne (scentralizowane) systemy smarowania nakładają środki smarne równocześnie w wielu miejscach maszyny za pośrednictwem układu przewodów, pompy oraz kontrolera, dozując stałe ilości smaru w stałych odstępach czasu podczas pracy urządzenia. Zapewnia to równomierny dopływ środka smarnego do podzespołów, które wymagają smarowania a poza tym smar zamknięty w zbiorniku zasilającym pompę jest chroniony przed zanieczyszczeniem. Chociaż takie rozwiązanie nie zastąpi regularnych przeglądów, ma wiele zalet w porównaniu ze smarowaniem ręcznym.
Automatyczne systemy smarowania odciążają oraz poprawiają bezpieczeństwo pracowników, zwolnionych z obowiązku aplikacji smaru, zwłaszcza w trudno dostępnych maszynach i ich komponentach. Ponadto dzięki temu, że smar jest nakładany podczas pracy maszyny, nie ma konieczności wyłączania jej w tym celu, co oznacza mniej przestojów. Dodatkowo, jeżeli w czasie aplikacji środka smarnego łożyska się obracają, zostaje on lepiej rozprowadzany i dokładniej je pokrywa. Smarowanie jest również najskuteczniejsze, gdy smar jest dozowany w małych, jednako odmierzonych ilościach, w stałych, odpowiednio dobranych odstępach czasu. Unika się oprócz tego dzięki temu nadmiernego i niedostatecznego smarowania. To nie tylko pozytywnie wpływa na skuteczność smarowania, ale też zapobiega wyciekom i marnotrawstwu środków smarnych. To zapewnia nie tylko oszczędność, ale i pozytywnie wpływa na środowisko. Generalnie scentralizowane systemy smarowania, które wpisują się w prewencyjną strategię utrzymania ruchu, wydłużają żywotność maszyn oraz zmniejszają koszty ich konserwacji.
Automatyczne systemy smarowania
Wyróżnić można kilka konfiguracji systemów centralnego smarowania. Każda ma zalety i wady, które sprawiają, że w pewnych zastosowaniach sprawdzi się lepiej niż w pozostałych. Generalnie dzieli się je na dwie kategorie: jedno- i dwu-(wielo-)liniowe. W pierwszych wykorzystuje się jedną linię główną, łączącą pompę z rozdzielaczami i dozownikami, natomiast dwuliniowe składają się z dwóch linii używanych naprzemiennie do zwiększania i obniżania ciśnienia.
Jednoliniowe są łatwe do zaprojektowania, zainstalowania, utrzymania, modyfikacji, rozbudowy. Zazwyczaj pracują przy wysokim ciśnieniu płynu i mogą być używane ze smarem lub olejem. Nie sprawdzają się jednak z gęstymi smarami, w bardzo niskich temperaturach, przy bardzo długich liniach między pompą a dozownikami. Dwuliniowe nadają się do pompowania na duże odległości z wieloma punktami smarowania na dużym obszarze, pod dużym ciśnieniem, lepkich smarów oraz w ekstremalnych temperaturach. Nie są jednak opłacalne w mniejszych systemach smarowania.
Popularne są też systemy wykorzystujące rozdzielacze progresywne. Wyróżniają je liczne opcje sterowania, ale te duże wymagają skomplikowanego układu przewodów. Korzysta się oprócz tego z systemów smarowania mgłą, w których olej jest natryskiwany w strumieniu powietrza. Dodatkowo chłodzą one obiekt smarowania. Oprócz typu automatycznego systemu smarowania przy jego wyborze należy też zwrócić uwagę na to, czy jego częścią jest filtr środka smarnego, czy wyposażono go w manometr pozwalający na szybką wizualną kontrolę ciśnienia oraz czy zaimplementowano jakiś mechanizm powiadamiania o tym, że nastąpiła przerwa w dopływie środka do smarowanych części.
Monika Jaworowska