Zanim wybierzemy silnik, należy rozstrzygnąć kilka kwestii. Odnieść się należy przede wszystkim do wymagań danej aplikacji. Kluczowe parametry to moment obrotowy oraz prędkość. By wybrać silnik zapewniający te wymagane, nie wystarczy sugerować się jego mocą wyjściową. Ze względu na zależność tych trzech wielkości istnieje bowiem wiele kombinacji momentu obrotowego oraz prędkości, które zapewnią taką samą moc wyjściową. Silniki o podobnej mocy mogą zatem mieć zupełnie różne możliwości, jeżeli chodzi o wprawianie konkretnego obciążenia w ruch. Dlatego wymagania w tym zakresie powinny się pokryć z charakterystyką momentu obrotowego w funkcji prędkości silnika. Bezwładność obciążenia jest następną kwestią, która wymaga analizy. Generalnie przyjmuje się, że nie powinna przekraczać 10-krotności bezwładności wirnika, inaczej dostrojenie silnika będzie trudne. W praktyce wszystko jednak zależy od specyfiki modelu silnika i warunków aplikacji.
Zanim rozważymy powyższe kwestie, trzeba podjąć decyzję podstawową, określając typ silnika. Wybór w tym zakresie oznacza zazwyczaj kompromis – w przypadku tytułowych kategorii silników generalnie między lepszymi parametrami, a ceną. Takie uogólnienie, chociaż jest dobrym punktem wyjścia i trzeba mieć świadomość tej głównej różnicy, zwykle jednak nie wystarczy. By właściwie zdecydować, pod uwagę trzeba również wziąć szereg innych cech silników krokowych i serwosilników.
Silniki krokowe
Silniki krokowe (skokowe) zbudowane są z wirnika z magnesami trwałymi i stacjonarnego stojana z nawiniętymi uzwojeniami (rys. 1). Prąd, który płynie przez uzwojenia stojana, wytwarza pole magnetyczne, które oddziałuje z polem magnetycznym wirnika, wytwarzając moment obrotowy. Silniki krokowe mają dużą liczbą biegunów, zwykle kilkadziesiąt. Każdy biegun jest sekwencyjnie zasilany – procesem tym steruje kontroler silnika. Dzięki temu wirnik obraca się w serii kroków (skokowo). Silniki krokowe generują zatem ruch przyrostowy. W związku z tym, że biegunów jest tak dużo, wydaje się on jednak ciągły.
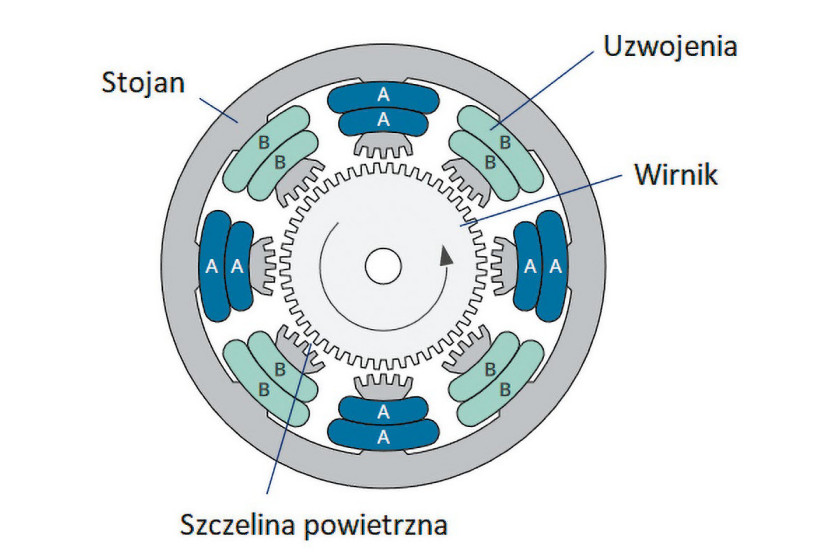
Sygnał sterujący jest poleceniem krokowym i kierunkowym, a położenie wału jest określane przez liczbę skoków. Silniki tego rodzaju działają w pętli otwartej. Oznacza to, że do sterownika nie jest przekazywana informacja zwrotna o aktualnym położeniu wału. Kontroler nie może zatem zmienić nastaw, żeby zniwelować ewentualną odchyłkę od zadanej pozycji. To pozwala ograniczyć koszt (początkowy, jak i konserwacji) oraz stopień skomplikowania, ponieważ nie jest potrzebny czujnik mierzący przemieszczenie, jak enkoder czy resolwer.
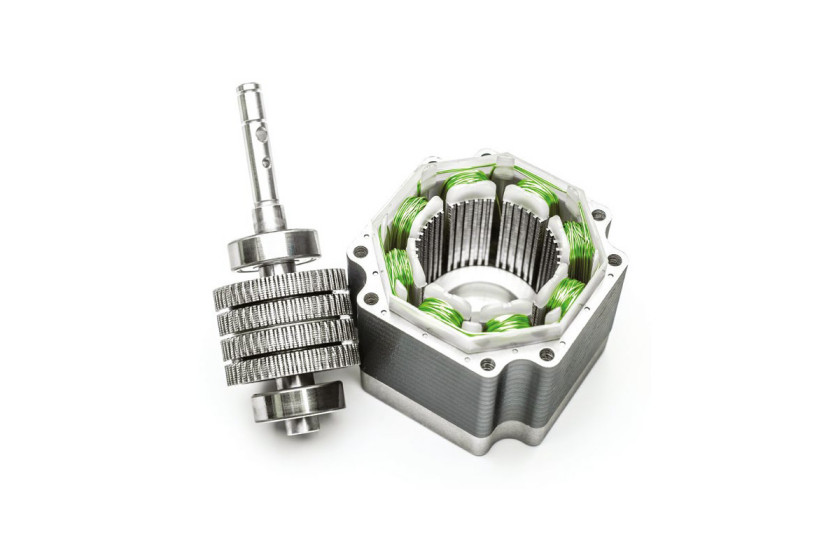
Prędkość i moment silników krokowych
Dzięki temu generalnie silniki krokowe są kompaktowe i ekonomiczne. Są także łatwe w obsłudze. Jest to jednak uzyskiwane kosztem precyzji pozycjonowania. By ją poprawić, oferowane są silniki krokowe z zamkniętą pętlą, które łączą zalety klasycznych silników krokowych z korzyściami ze sprzężenia zwrotnego, ale w niższej cenie niż serwonapędy.
Prędkości silników skokowych są ograniczone. Zazwyczaj działają optymalnie przy 1200 obr./min i niższych szybkościach. I choć duża liczba biegunów pozwala im wytwarzać maksymalny moment obrotowy przy zerowej prędkości, spada on znacząco wraz z jej wzrostem – jeżeli na przykład dany model silnika zapewnia moment obrotowy 3 Nm przy 1 obr./min, niczym niezwykłym nie jest jego spadek do zaledwie 0,5 Nm przy 1200 obr./min.
Rozwiązaniem jest dodanie reduktora. Przykładowy, o przełożeniu 10:1, w połączeniu z silnikiem krokowym o prędkości 1200 obr./min, zwiększy moment obrotowy o rząd wielkości, jednocześnie jednak zmniejszy szybkość do 120 obr./min. Trzeba to uwzględnić, odnosząc się do wymagań danej aplikacji.

Serwosilniki
Serwosilniki również zbudowane są z wirnika z magnesami trwałymi i stojana z uzwojeniami (rys. 2). Analogicznie jak w silnikach krokowych, prąd płynący w uzwojeniach stojana wytwarza w nich pole magnetyczne oddziałujące na wirnik w celu wytworzenia momentu obrotowego. Serwosilniki mają jednak znacznie mniej biegunów niż silniki skokowe. Poza tym pracują w zamkniętej pętli ze sprzężeniem zwrotnym, będąc komponentem serwonapędów.
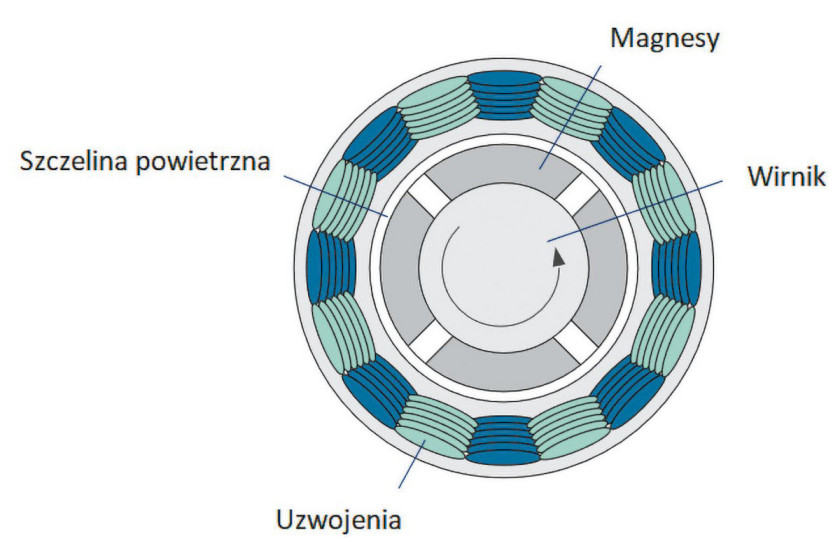
Oprócz serwosilników na te ostatnie składają się sterownik i serwowzmacniacz (napęd). Kontroler i napęd współpracują, aby wyznaczyć nastawy silnika – za to zwykle odpowiada sterownik, a potem według nich go wysterować, co jest funkcją serwowzmacniacza. Dokładniej zadaniem napędu jest wzmocnienie sygnału sterującego (wartości zadanej), który jest dostępny na wyjściu sterownika, do wartości wymaganej do zasilenia silnika. To ostatnie w serwowzmacniaczu realizuje przemiennik częstotliwości. W tej sekcji napędu przemienne napięcie wejściowe zostaje najpierw wyprostowane w mostku diodowym, a następnie wygładzone i przekształcone w falowniku w napięcie przemienne o zmiennej amplitudzie oraz częstotliwości, zasilające silnik.
Prędkość i moment serwosilników
Serwosilniki działają przy znacznie większych prędkościach niż skokowe, typowo rzędu nawet kilku tysięcy obr./min. Dzięki temu mogą być używane z reduktorami w celu uzyskania znacznie większych momentów obrotowych przy wciąż użytecznych prędkościach. Oprócz tego zapewniają stały moment obrotowy w całym użytecznym zakresie prędkości – jeżeli zatem gwarantowany jest moment obrotowy 1,2 Nm przy 10 obr./min, to taki sam będzie osiągalny także i na przykład przy 3000 obr./min.
W przeciwieństwie do silników krokowych serwosilniki nie wytwarzają momentu trzymającego. Dzięki pracy w pętli zamkniętej jednak sterownik/napęd może wysterować silnik w taki sposób, by utrzymać zadane położenie obciążenia.
W serwosilnikach zwykle wykorzystuje się magnesy z metali ziem rzadkich, podczas gdy w silniki krokowe częściej wbudowuje się "zwykłe", tańsze magnesy. Dzięki temu serwosilniki pozwalają uzyskiwać większy moment obrotowy przy mniejszych rozmiarach silnika.
Generalnie serwosilniki, ponieważ przewyższają krokowe pod względem prędkości, jak i momentu obrotowego, zapewniają większe przyspieszenie. Wyróżnia je poza tym precyzja pozycjonowania.
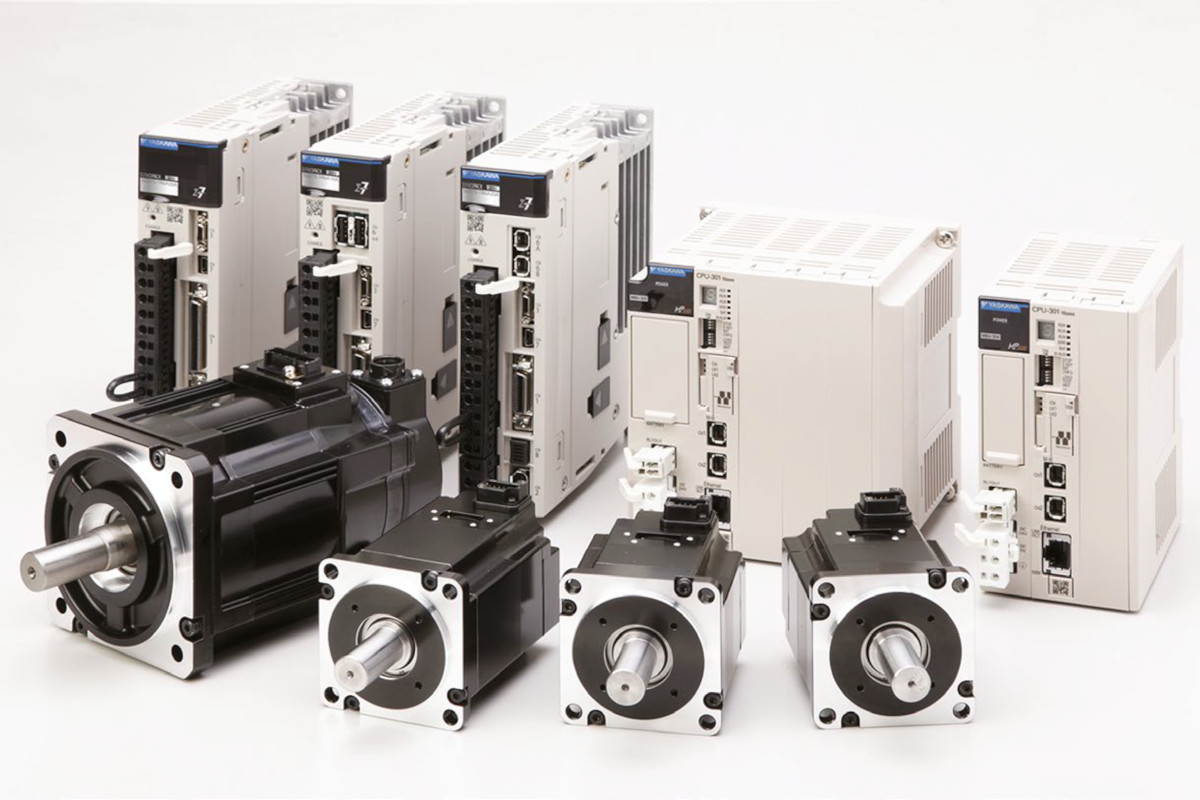
Jaki silnik wybrać?
Jak pisaliśmy na początku, wstępne rozstrzygnięcie między tytułowymi typami silników sprowadza się do oceny, czy możemy poświęcić precyzję sterowania dla mniejszych kosztów, wybierając silnik skokowy czy odwrotnie, decydując się na serwosilnik. Ponadto serwosilniki są lepszym wyborem, jeżeli potrzebujmy silnika o prędkości powyżej kilku tysięcy obr./min i dużym momencie obrotowym. Jeśli jednak wymagane są prędkości rzędu kilkuset obr./min albo mniej i mały moment obrotowy, wybierając je, ryzykujemy przewymiatechnika rowanie. Poza tym serwosilniki mogą zazwyczaj generować chwilowy moment obrotowy nawet kilkakrotnie większy niż ten ciągły. Zapewnia to rezerwę mocy potrzebną do kompensacji zmian obciążenia bez przewymiarowania. Jeżeli zatem obciążenie jest nieprzewidywalne i może wymagać dodatkowego momentu, silnik krokowy nie jest najlepszym wyborem. Jakie jeszcze kwestie powinno się wziąć pod uwagę w praktyce, wybierając między serwosilnikiem a silnikiem krokowym, wyjaśniamy na przykładzie obrabiarek CNC.
Jaki silnik w obrabiarce CNC?
Silniki krokowe i serwosilniki są częścią napędów osi oraz narzędzi skrawających maszyn CNC. O tym, który typ silnika będzie w danym przypadku lepszy, decyduje kilka kwestii.
Kluczową jest rozmiar plotera CNC. Jeśli chcemy skonfigurować taki o niewielkich gabarytach i małym obszarze roboczym, silnik krokowy może być lepszy niż serwosilnik. Generalnie przyjmuje się, że te pierwsze, jako typowo mniejsze i lżejsze, lepiej sprawdzają się w przypadku ploterów o maksymalnym obszarze cięcia trochę ponad metr na metr (4’ × 4’), choć w celu obniżenia ceny wyposaża się w nie też te w wersji podstawowej o większych obszarach cięcia (na przykład metr na dwa metry, 4’ × 8’ czy półtora metra na trzy, 5’ × 10’). W przypadku większych stołów, aby zapobiec wyginaniu się suwnic, stosuje się masywniejsze konstrukcje i wówczas odpowiedniejsze są większe i cięższe serwosilniki.
Jeżeli obrabiane przedmioty mają się cechować dużą precyzją wykonania, też preferowane są oczywiście serwosilniki, ewentualnie silniki krokowe pracujące w zamkniętej pętli. Ze względu na łatwiejsze programowanie i niższy koszt w silniki skokowe są z kolei wyposażane maszyny CNC o podstawowej funkcjonalności, na przykład na potrzeby wykonywania prototypów czy szkolenia osób początkujących w technologii obrabiarek.
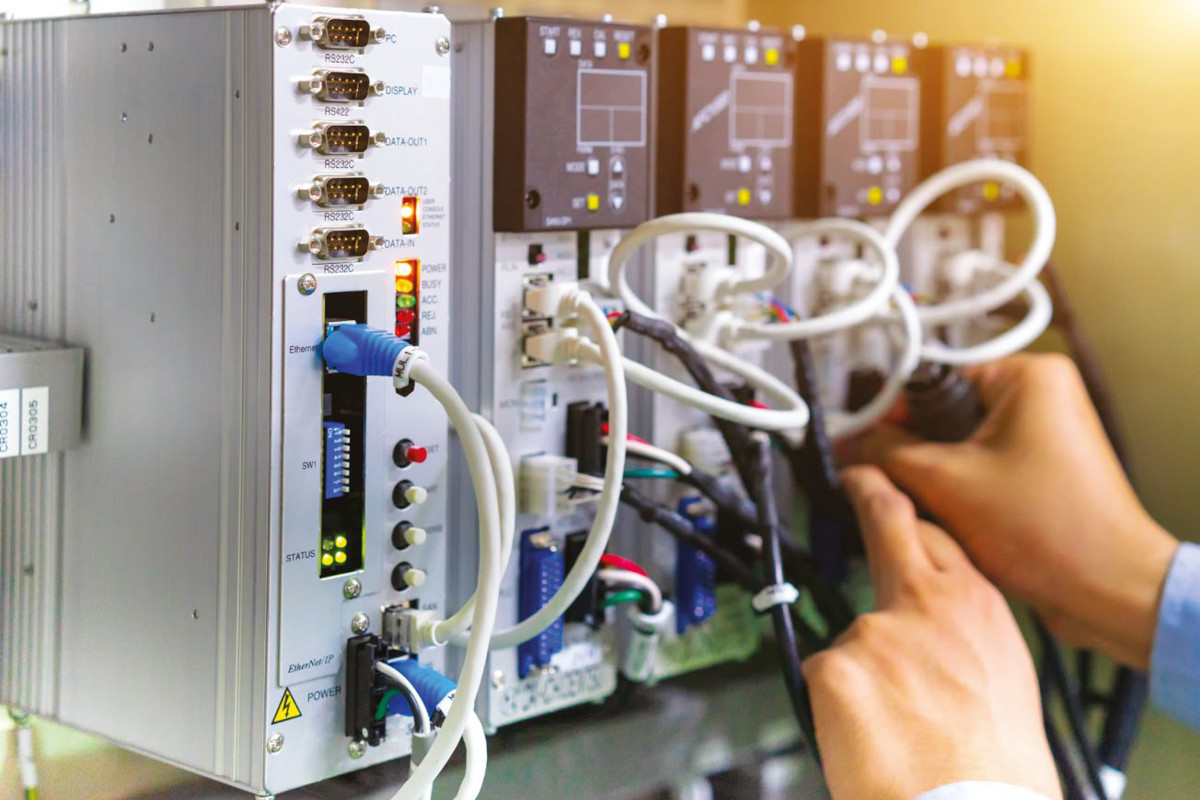
Jeżeli używane są ciężkie wrzeciona, ze względu na większe momenty obrotowe lepiej sprawdzą się serwosilniki. Zapewnią także większą prędkość, jeśli maszyna ma masywne suwnice. Dzięki lepszej wydajności przy dynamicznych obciążeniach serwosilniki lepiej sprawdzą się przy różnych materiałach i ustawieniach cięcia. Kolejną ważną kwestią jest czas potrzebny na wykonanie cięć. Generalnie w porównaniu z silnikami krokowymi serwosilniki są w stanie szybciej przyspieszać i się zatrzymywać. Chociaż różnice w szybkości są rzędu milisekund, może mieć to znaczenie, mniejsze przy wykonywaniu części, które mają szybki bieg i minimalną liczbę zmian kierunku cięcia i większe w przypadku detali wymagających częstej zmiany kierunku wrzeciona.
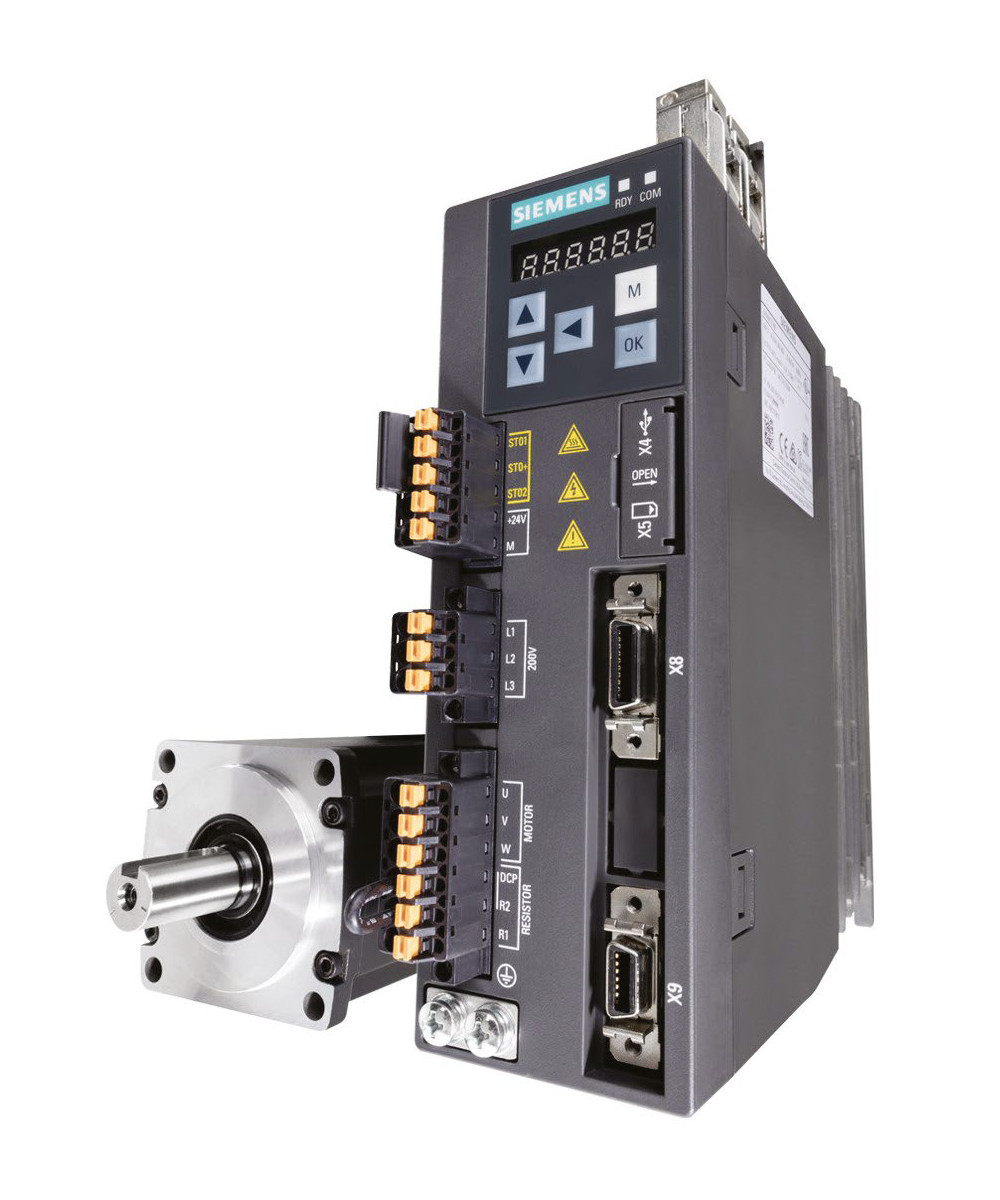
Istotny jest również moment trzymający. Należy go wziąć pod uwagę, zwłaszcza jeżeli trzeba utrzymać obciążenie w kierunku pionowym, na przykład w przypadku wrzeciona na osi Z i szczególnie wtedy, gdy używane są śruby kulowe. Tarcie wewnętrzne w tych ostatnich jest bowiem niskie i można je napędzać wstecznie. To oznacza, że ciężar wrzeciona może pociągnąć śrubę kulową z powrotem w dół. Żeby zapobiec wstecznemu napędzaniu elementów ruchomych przez ich obciążenie, silnik musi zapewnić wystarczający moment trzymający. Chociaż sugeruje to wybór silnika krokowego, można również rozważyć serwosilnik. Mechanizm sprzężenia zwrotnego w tym przypadku wykrywa każdą zmianę położenia wału i natychmiast koryguje jego położenie. W praktyce zatem oscyluje on w zadanej pozycji, ale oscylacje te są niewielkie, o ile serwonapęd został prawidłowo dostrojony. W przeciwnym razie mogą wystapić wibracje.
Silniki krokowe mogą pracować nieco głośniej w porównaniu z serwosilnikami. Choć w przypadku maszyn CNC nie jest to dużym problemem, aby temu zaradzić, warto wybrać sterownik obsługujący mikrokrokowanie. Te nie tylko pomaga zmniejszyć hałas, ale dodatkowo zapewnia płynny ruch wału przy niskich prędkościach i eliminuje drgania.
Monika Jaworowska