Jak widać – pierwszym krokiem przed przystąpieniem do jakichkolwiek działań jest pozyskanie danych, na bazie których stworzone zostaną procedury optymalizacji. Poważnym pretendentem do roli uniwersalnego standardu wymiany danych w zakładach przemysłowych jest OPC UA, opracowywany i usprawniany od ponad 10 lat przez OPC Foundation tak, by realizować wymagania IIoT, M2M i Industry 4.0. Standard ten może zostać zaimplementowany na różnych systemach operacyjnych, dowolnej platformie sprzętowej i przy użyciu wielu języków programowania, również w aplikacjach wykorzystujących cloud computing.
Integracja danych
Integracja danych z urządzeń zainstalowanych na maszynach, a obsługiwanych przez lokalne układy sterowania, z systemami nadrzędnymi i dalej z systemami MES i ERP, powinna być wykonywana w sposób w pełni zautomatyzowany i niewidoczny dla użytkownika. Koszt wdrożenia systemu obsługującego wymianę danych nie może przekraczać oczekiwanych korzyści, więc ważne jest zastosowanie rozwiązań wymagających jak najmniejszych nakładów na sprzęt, oprogramowanie oraz czas potrzebny na konfigurację.
Istnieje duże prawdopodobieństwo, że poprawa efektywności w zakładzie przemysłowym będzie przeprowadzana metodą prób i błędów, ponieważ trudno określić, które działania będą miały pozytywny wpływ na wyniki finansowe. Wymagana jest więc elastyczność w przetwarzaniu i interpretacji rejestrowanych danych, możliwość wyznaczania nowych wskaźników efektywności i adaptacji do zmieniającej się sytuacji w zakładzie i rosnącej wiedzy na temat przyczyn nieoptymalnej pracy. Opracowanie uniwersalnego modelu komunikacji wydaje się rozwiązaniem optymalnym z punktu widzenia kosztów wdrażania systemów służących poprawie efektywności zakładu. Integracja danych często jest niełatwym zadaniem ze względu na obecność na rynku znacznej liczby dostawców systemów automatyki, stosujących różne standardy komunikacji.
Jeśli w zakładzie przemysłowym zachowywana jest standaryzacja w zakresie na przykład sterowników PLC, układów I/O i napędów dostarczanych przez jednego producenta, komunikacja pomiędzy tymi urządzeniami zwykle jest ułatwiona dzięki możliwości zastosowania standardowego dla urządzeń danego producenta protokołu komunikacji. Łatwiej też wypracować dobre praktyki w zakresie adresacji urządzeń i nazewnictwa zmiennych. W praktyce nie jest możliwe zastosowanie jednego protokołu komunikacji, ponieważ pewna liczba urządzeń nie będzie obsługiwać standardowego protokołu preferowanego w zakładzie. Mogą to być na przykład liczniki energii lub inne urządzenia pomiarowe. W zakładzie przemysłowym, w którym dane ze wszystkich urządzeń miałyby być dostępne w systemach MES lub ERP, zawsze będzie występować konieczność konwersji przynajmniej części danych na inny protokół komunikacji. Docelowym rozwiązaniem jest możliwość przekazywania danych z czujników, napędów, itp. bezpośrednio do systemów, które będą wykorzystywać zebrane dane za pośrednictwem jak najmniejszej liczby urządzeń pośrednich, które są kosztowne i wymagają konfiguracji. Dotyczy to również wymiany danych pomiędzy maszynami (na przykład wchodzącymi w skład jednej linii produkcyjnej). W idealnej sytuacji dane powinny być dostępne dla wszystkich uprawnionych do ich przetwarzania odbiorców, zarówno na poziomie zakładu przemysłowego (wymiana danych między maszynami), jak i na poziomie zarządzania produkcją (przesyłanie danych np. do systemu MES).
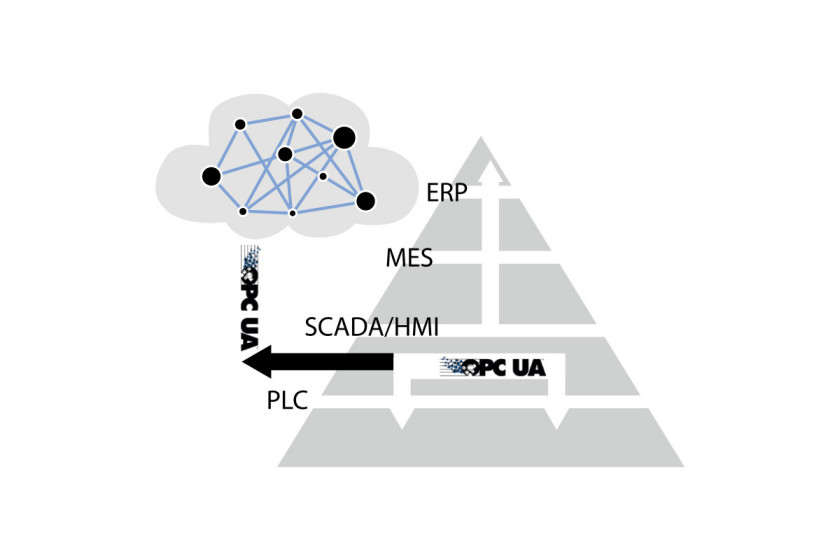
Można wyobrazić sobie model, w którym konfiguracja komunikacji i przypisywanie zmiennych będzie ograniczać się tylko do wybrania konkretnej nazwy z rozwijanej listy, zamiast żmudnego przepisywania adresów rejestrów, przypisywania nazw zmiennych i pilnowania kolejności adresowania przy konwersji pomiędzy kolejnymi protokołami. Krokiem w tę stronę jest zastosowanie w OPC UA modelu obiektu, wprowadzenie klas i metod. Dzięki architekturze zorientowanej na usługi wykorzystywane są tylko te funkcje, które są aktualnie potrzebne.
Celem jest sytuacja, w której sukcesem nie jest poprawna konfiguracja, integracja i uruchomienie systemu, ale realizacja postawionych mu zadań w jak najkrótszym czasie, przy jak najniższych nakładach finansowych i z możliwie najlepszym skutkiem. Przesunięcie w tło i minimalizacja zadań związanych z projektowaniem, realizacją i uruchomieniem systemu na rzecz zwiększonej pracy nad osiągnięciem wymaganego rezultatu jest jednym z podstawowych problemów dostawców rozwiązań Przemysłu 4.0.
Architektura PubSub
Jednym z podstawowych założeń IIoT jest wymiana danych pomiędzy wieloma inteligentnymi urządzeniami z zastrzeżeniem, że nie muszą to być urządzenia mające dużą moc obliczeniową, na przykład inteligentne czujniki. Konsekwencją ograniczonej mocy obliczeniowej jest konieczność minimalizacji zużycia pamięci i mocy procesora. W 2018 roku OPC Foundation opublikowała specyfikację modelu wymiany danych Publish-Subscribe (PubSub), w której w odróżnieniu od architektury klient/serwer nie jest wymagane utrzymywanie stałego połączenia, co pozwala na zmniejszenie zużycia pamięci. W architekturze PubSub wiadomości są rozgłaszane do całej sieci, a urządzenia lub programy, które mają je wykorzystać, subskrybują się na dany typ wiadomości. To dobre rozwiązanie w sytuacji, w której jedna aplikacja gromadzi dane z wielu publikujących je urządzeń. Obsługiwane są protokoły MQTT, AMQP lub UDP. Zachowana jest kompatybilność z modelem klient/serwer.
Standard TSN
Niedoskonałości klasycznego Ethernetu w zakresie niezawodności i determinizmu doprowadziły do powstania pewnej liczby standardów Ethernetu przemysłowego. Niestety technologie te, opracowywane przez niezależnych od siebie dostawców systemów automatyki, nie są ze sobą kompatybilne. Współczesne przemiany w podejściu do rejestracji i obsługi danych z maszyn zmuszają do integracji systemów różnych producentów. Konwersja danych jest związana z opóźnieniami w transmisji, obniżoną niezawodnością i jest kosztowna ze względu na konieczność stosowania dodatkowego sprzętu i oprogramowania oraz poświęcenia czasu potrzebnego na konfigurację komunikacji.
Rozwiązaniem może stać się TSN (Time-Sensitive Networking) – opracowywany przez IEEE nowy uniwersalny standard przemysłowego Ethernetu o dużej niezawodności, nastawiony na determinizm i dostarczanie komunikatów w określonym z góry czasie z niewielkim opóźnieniem i bez strat. Jest to istotne w zastosowaniach przemysłowych, gdzie synchronizacja w czasie danych pochodzących z różnych urządzeń może mieć kluczowe znaczenie dla prowadzonego procesu. Zastosowanie TSN do transmisji danych za pomocą OPC UA ma stanowić sposób na umożliwienie komunikacji w systemach IIoT pomiędzy urządzeniami różnych producentów, niezależnie od platformy sprzętowej i stosowanego oprogramowania. Użycie modelu PubSub umożliwi tworzenie systemów działających w czasie rzeczywistym. Standard TSN ma zachowywać kompatybilność ze standardowym Ethernetem, dzięki czemu możliwe będzie wykorzystanie istniejących sieci.
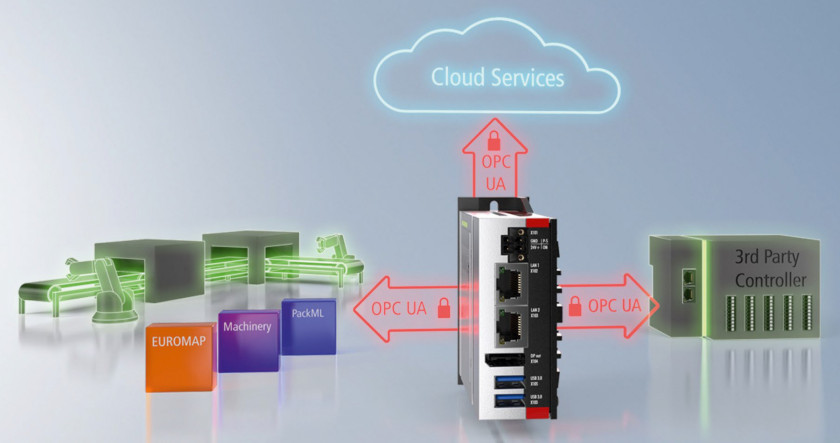
Integracja z systemami Industry 4.0
Posiadanie danych i możliwość przesyłania ich w bezpieczny sposób to jednak dopiero początek. Do pełnego wykorzystania gromadzonych informacji potrzebne są narzędzia do ich przetwarzania i prezentacji w formie umożliwiającej wykorzystanie zdobytej wiedzy. Mogą być to na przykład systemy informatyczne klasy ERP lub MES oraz przemysłowe systemy diagnostyczne lub eksploatacyjne.