CELE MODERNIZACJI
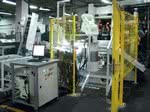
Fot. 1. Stanowisko automatycznego podawania detali
Powodami modernizacji było osiągnięcie następujących celów:
- skrócenie czasu przezbrajania oraz serii produkcyjnej,
- uzyskanie wyższego współczynnika OEE (Overall Equipment Eff ectiveness),
- zwiększenie powtarzalności procesu (jako wymóg utrzymania wymaganej jakości),
- zapewnienie możliwości produkcji większego asortymentu wyrobów,
- szybkie i stosunkowo proste uruchamianie produkcji nowych detali.
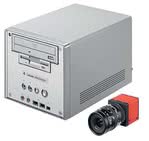
Fot. 2. System wizyjny visionPowerbox
W ramach opisywanego wdrożenia wykonano modernizację stanowiska maszyny obróbczej z wykorzystaniem systemu wizyjnego oraz robota. Tworzenie aplikacji podzielono na dwa etapy.
Pierwsze zadanie obejmowało remont kapitalny maszyny w zakresie jednostek obróbczych, wymiany sterowania nimi, wymiany układu hydraulicznego i przystosowania do pracy z robotem przemysłowym.
Drugie zadanie miało na celu wdrożenie zrobotyzowanego systemu do automatyzacji podawania detali do maszyny obróbczej z systemem detekcji wizyjnej.
WYKONANIE WDROŻENIA
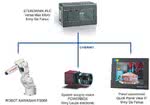
Rys. 1. Schemat układu sterowania
Modernizacja maszyny obróbczej oraz integracja robota z systemem wizyjnym została wykonana przez firmę Carlift Service Sp. z o.o. z Ostrowa Wielkopolskiego. Po zebraniu założeń aplikacji wytypowano następujące elementy systemu:
- sterownik GE Fanuc Versa Max Micro do sterowania stanowiskiem obróbczym (wyposażony w wejścia/ wyjścia dyskretne, Ethernet oraz panel operatorski QuickPanel View 6”),
- robot przemysłowy K awasaki FS006 z kontrolerem FD71,
- system wizyjny visionPowerbox firmy Leuze electronic, której przedstawicielem w Polsce jest firma Balluff Sp. z o.o.
Po określeniu wymaganej dokładności detekcji system wyposażono
DZIAŁANIE APLIKACJI

Rys. 2. Rozmieszczenie elementów stanowiska
Praca aplikacji polega na automatycznym podaniu detalu z zasobnika przez transporter w pole pracy systemu wizyjnego. Po wykonaniu zdjęcia wyznaczane są punkty charakterystyczne detalu. Informację o ich pozycji i orientacji są przesyłane do robota z wykorzystaniem interfejsu Ethernet TCP/IP. Wstępna kalibracja obrazu pozwala na przesłanie współrzędnych zorientowanych w układzie współrzędnych robota.
Po spełnieniu warunków brzegowych, robot pobiera detal i umiejscawia go w gnieździe obróbczym. Przed tą operacją następuje odebranie wcześniej przetworzonego detalu i przekazanie go do transportu detali gotowych.
Aplikacja sterująca jednostkami maszyny obróbczej oparta jest na sterowniku PLC GE Fanuc Versa Max i zarządza aplikacją, komunikując się pomiędzy urządzeniami z wykorzystaniem sieci Ethernet. Program nadzoruje pracę maszyny, uruchamiając w odpowiedniej kolejności jednostki i napędy frezerskie wiercące lub gwintujące. Panel operatorski, oprócz funkcji informacyjnej, steruje też aktywacją i dezaktywacją jednostek obróbczych. Wykorzystane wraz z nim oprogramowanie w przejrzysty i łatwy sposób umożliwia ich wybór i sterowanie pracą.
Omawiana aplikacja została wykonana pod kątem szybkiego przezbrajania pod produkcję nowych detali oraz, dzięki elastyczności systemu wizyjnego, udostępnia narzędzia umożliwiające łatwe wprowadzanie nowych wyrobów.
OSIĄGNIĘTE REZULTATY
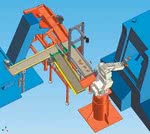
Rys. 3. Podajnik automatyczny - widok z góry
Zastosowanie w aplikacji systemu wizyjnego visionPowerbox firmy Leuze electronic pozwoliło na zautomatyzowanie procesu podawania detalu do maszyny obróbczej. Bezobsługowość tej operacji ma główny wpływ na wzrost powtarzalności i wydajności procesu, przy zachowaniu wysokiej jakości wyrobów. Jest to doskonały przykład uzasadniający wykorzystanie elementów wizyjnych w zastosowaniach przemysłowych. Na skutek wykonanego wdrożenia uzyskano korzyści takie jak:
- skrócenie czasu przezbrojenia oraz serii produkcyjnej,
- uzyskanie wyższego współczynnika OEE głównie przez zwiększenie niezawodności maszyny,
- zwiększenie mocy produkcyjnych oraz ich pełniejsze wykorzystanie,
- łatwiejsze uruchomienie produkcji nowych detali,
- zmniejszenie zapasów magazynowych przy jednoczesnym zwiększeniu niezawodności dostaw,
- obniżenie kosztów jednostkowych,
- polepszenie wizerunku firmy w oczach klientów.
Paweł Ulichnowski
Dyrektor Działu Rozwoju firmy Carlift Service Sp. z o.o.
Wojciech Roczon
Produkt Manager Balluff Sp. z o.o.