NIEWSPÓŁOSIOWOŚĆ I JEJ SKUTKI
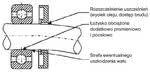
Rys. 1. Konsekwencje niewłaściwej współosiowości wałów
Niewspółosiowość elementów maszyn może wynikać z niewłaściwego ustawienia maszyny, błędów konstrukcyjnych, nieprawidłowej obróbki mechanicznej elementów, odkształceń cieplnych, pęknięć, osiadania fundamentów itp. Pojawia się ona także w trakcie eksploatacji maszyn, podczas której maszyna ulega zużyciu, fundamenty osiadają, a elementy maszyny ulegają deformacji. Utrata współosiowości wałów i korpusu powoduje niebezpieczeństwo nadmiernego obciążenia łożysk, wałów, uszczelnień i sprzęgieł, co w ostatecznym rezultacie może powodować ich zniszczenie. Wyróżnić można następujące rodzaje niewspółosiowości:
- niewspółosiowość zesprzęglonych wałów maszyn,
- niewspółosiowość osi stojaków łożyskowych z osią wału,
- niewspółosiowość korpusów z osią wirnika,
- koła pasowe nie znajdują się w jednej płaszczyźnie.
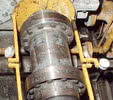
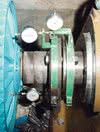
Rys. 2. Przykłady zastosowania czujników zegarowych do osiowania wałów: a – sprzęgło krótkie, b – sprzęgło z przekładką.
Niewspółosiowości może towarzyszyć:
- wzrost poziomu drgań,
- wzrost mimośrodowości wirników,
- przytarcie wałów o uszczelnienia,
- nieprawidłowa praca sprzęgieł,
- szybsze zużycie łożysk,
- pogorszenie sprawności niektórych maszyn na skutek powiększenia luzów.
Przestoje maszyn wirnikowych spowodowane wymienionymi przyczynami można w znacznym stopniu wyeliminować dzięki starannemu ustawieniu ich wałów (osiowaniu). Około 50% uszkodzeń maszyn wirujących można przypisać błędom w ich ustawianiu. Ustawienie prawidłowe gwarantuje przestoje krótsze i następujące w dłuższych odstępach czasu, niezbędne do przeprowadzenia planowanej obsługi i napraw. Dlatego operacja ustawiania maszyn jest jedną z najważniejszych na etapie montażu i podczas remontu maszyny.
OSIOWANIE Z WYKORZYSTANIEM LASERA
W 1983 roku w Niemczech pojawił się pierwszy laserowy przyrząd Optalign do ustawiania maszyn, który wyraźnie zwiększył dokładność tej operacji. Wcześniej dok ładne ustawianie sprzęgniętych maszyn potrafi li wykonać z powodzeniem tylko fachowcy mający duże doświadczenie w obsłudze czujników mechanicznych. Korzystanie z tych czujników wymaga precyzyjnego ich instalowania oraz właściwej interpretacji wyników pomiarów.
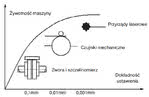
Rys. 3. Dokładność ustawiania maszyn
Kolejne czynności wykonywane przy użyciu czujników mechanicznych mogą być przyczyną błędów, nawet jeżeli ustawianie maszyn wykonuje personel o dużym doświadczeniu. Przy rządy z czujnikami mechanicznymi wymagają stosowania mechanicznych mostków mocowanych do ciężkich uchwytów, których zwis musi być dokładnie zmierzony i uwz ględniony w dalszych obliczeniach.
Takie ustawianie ma szyn wymaga nie tylko doświadczenia, ale również znajomości zależności trygonometrycznych, by odczytane z czujników wartości odnieść do łap maszyny. Ponadto, każde ustawianie jest czasochłonne przy jednoczesnym dużym zaangażowaniu oprzyrządowania (często różnego dla różnych zespołów maszyn).
Wprowadzenie systemów laserowo-optycznych pozwoliło na całkowite zrezygnowanie z czujników mechanicznych. Ustawianie maszyn stało się bardzo dokładne, proste, szybkie i tanie. Systemy laserowe opierają się na bezdotykowych pomiarach za po mocą nieszkodliwego promienia laserowego. Nie jest potrzebne mechaniczne połączenie między punktami pomiarowymi na obu wałach.
Punkty te „łączy” promień lasera, co eliminuje możliwość powstania błędów spowodowanych zwisem prętów pomiarowych, zacinaniem się czujników mechanicznych lub pomyłkami w obsłudze. Dwa pierwsze elementy, lekkie i poręczne, mocowane są łatwo do wałów maszyn i łączone przewodem z układem mikroprocesororowym (obecnie są produkowane systemy bez przewodowe oparte o Bluetooth).
Podczas obrotu wału wykazującego kątowe i równoległe przesunięcia, odbity promień lasera zmienia swój kierunek, a zatem i miejsce trafienia w detektorze. Na podstawie danych przekazywanych automatycznie mikroprocesor oblicza poziome i pionowe wartości korekcji, które są wyświetlane na ciekłokrystalicznym ekranie z dokładnością do 1/100mm.
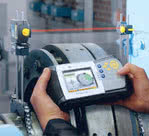
Rys. 4. Przykładowy zestaw laserowy stosowany do osiowania wałów zesprzęglonych maszyn
W zależności od stopnia uciążliwości i warunków montażowych osiowanie wałów maszyn metodą laserową stanowi średnio 20% czasu potrzebnego do ustawiania maszyn metodą tradycyjną z wykorzystaniem czujników mechanicznych.
Oprócz ustawiania zespołów maszyn, system laserowy może służyć do szybkiego sprawdzenia prawidłowości wyosiowania wałów eksploatowanych maszyn. Często podczas eksploatacji maszyn zachodzi podejrzenie o rozosiowanie zespołu pracujących maszyn. Za pomocą systemu laserowego można bardzo szybko wykryć tę nieprawidłowość.
SYSTEM LASEROWY ZREWOLUCJONIZOWAŁ…
…ustawianie i sprzęganie wielu maszyn pod względem dokładności, szybkości, wygody i kosztów. Osiowanie maszyn metodą laserową ma następujące zalety:
- możliwość wyznaczenia wzajemnego położenia rzeczywistych osi obrotu wałów dwóch lub więcej współpracujących ze sobą maszyn, niezależnie od kształtu półsprzęgieł,
- możliwość osiowania wałów dla dużej odległości między tarczami sprzęgieł (sprzęgła z wałem pośrednim), np. 10 lub 20m,
- możliwość uzyskania precyzyjnych wyników pomiarów już po wykonaniu 1/6 obrotu przy dowolnym kierunku obrotu i z dowolnego położenia wyjściowego,
- łatwość przeprowadzania pomiarów (niepotrzebne są pojedyncze odczyty, a wartości mierzone przekazywane są bezpośrednio do komputera, na którego ekranie wyniki są przedstawiane grafi cznie),
- możliwość zastosowania uniwersalnych uchwytów do szybkiego montażu systemu na wałach lub sprzęgle w czasie około 5 minut,
- brak prętów pomiarowych wykluczający potrzebę obliczania i uwzględniania w obliczeniach ich zwisów,
- brak wpływu luzu połosiowego wałów na wynik końcowy ustawienia,
- możliwość osiowania wałów również przy rozłączonym sprzęgle z zastosowaniem np. metody multipoint i wykorzystaniu wbudowanej poziomicy optoelektronicznej,
- możliwość przeprowadzenia pomiarów na wałach, które nie mogą być obracane poprzez zastosowanie specjalnych uchwytów ślizgowych,
- możliwość wykrywania tzw. miękkiej (kulawej) łapy nieleżącej w jednej płaszczyźnie z pozostałymi i usunięcia skutków tej wady,
- możliwość wyświetlenia na ekranie odchyłek kątowych i równoległych na sprzęgłach oraz porównania z zawartymi w przyrządzie tabelami tolerancji dopuszczalnymi dla sprzęgieł o określonej średnicy i prędkości obrotowej,
- brak konieczności stosowania czujników zegarowych w czasie koniecznych przemieszczeń maszyny (na ekranie komputera w sposób ciągły jest pokazany kierunek i wielkość korekty),
- możliwość wprowadzenia danych uwzględniających rozszerzalność termiczną maszyny gwarantujący, że uzyska ona prawidłowy stan ustawienia po osiągnięciu temperatury pracy,
- krótki czas potrzebny na przeszkolenie personelu obsługi dzięki łatwemu przeprowadzaniu pomiarów, – możliwość szybkiego wydrukowania protokołu pomiarowego.
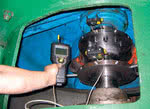
Rys. 5. Widok ogólny osiowania wałów na sprzęgle pompy posadowionej pionowo
USTAWIANIE MASZYN METODĄ LASEROWO-OPTYCZNĄ W ELEKTROWNI OPOLE
Elektrownia Opole jako jedna z pierwszych w Polsce (1991 rok) zastosowała system laserowy Optalign do ustawiania maszyn. Corocznie sprawdza się współosiowość lub osiuje tą metodą około 200 różnego rodzaju i wielkości maszyn wirnikowych.
Czas ustawiania zespołu wynosi od około 20 minut do 2 godzin w zależności od stopnia rozosiowania, uciążliwości i warunków montażowych (sprzęgła krótkie, sprzęgła z przekładką). Stanowi to średnio 20% czasu potrzebnego do ustawiania maszyny metodą tradycyjną opartą na czujnikach mechanicznych. Zaoszczędzono w ten sposób czas przy jednoczesnym uzyskaniu bardzo dużej dokładności.
Po ustawieniu zespołów maszyn przesu nięcia kątowe i równoległe sprzęgieł wynoszą od 0 do 0,04mm, co istotnie polepsza pracę maszyn i ogranicza ich awaryjne przestoje. Do szybkości, wygody i dokładności ustawiania maszyn przy użyciu lasera szybko przekonały się zespoły montażowe, które bardzo szybko zaniechały metod tradycyjnych. Warto wspomnieć o ustawianiu pomp posadowionych pionowo (rys. 5).
Ich ustawianie za pomocą czujników zegarowych było utrudnione i czasochłonne ze względu na niewygodny dostęp do wału. System laserowo-optyczny w łatwy i szybki sposób umożliwił ustawienie tych maszyn z końcowymi przesunięciami kątowymi i równoległymi do 0,03mm.
W tym przypadku dzięki systemowi laserowemu uzyskuje się in formacje o wielkości podkładek korekcyjnych w dowolnym punk cie obwodu podstawy silnika. W kilku przypadkach wy kryto błąd fabryczny połączenia zamkowego silnika z tu leją dystansową pompy, uniemożliwiający poprawne ustawienie.
Tuleje należało odesłać do przetoczenia. System laserowo-optyczny okazał się bardzo przydatny przy ustawianiu osiowych wentylatorów spalin AN-30e6 (rys. 5) i osiowych wentylatorów podmuchu AP-1-22/12 wyposażonych w sprzęgła zębate z wałem pośrednim o dłu gości ok. 6m (wentylatory spalin) i 3m (wentylatory powietrza).
Znaczna odległość między wałami ustawianych maszyn, luzy sprzęgieł zębatych oraz duże masy silników (około 6000kg) ogromnie utrudniały ustawianie tych zespo łów za pomocą czujników mechanicznych. Prawie tygodnio wa próba ustawiania jednego z tych zespołów metodą tra dycyjną nie przyniosła zadowalających rezultatów, toteż zdecydowano się wyosiować zespół za pomocą laserowego przyrządu.
Ponieważ zespoły były znacznie rozosiowane i promień laserowy podczas obrotu wału wychodził poza zakres dete ktora (laser i pryzmat zamontowane w odległości ok. 6m od siebie dla wentylatorów spalin i 3m dla wentylatorów pod muchu), przystąpiono do ustawiania wstępnego według na stępującego schematu:
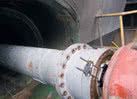
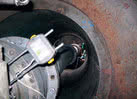
Rys. 6. Wentylator spalin z wałem pośrednim w trakcie laserowego osiowania
1) Pomiary na sprzęgle pierwszym; za notowanie otrzymanych wartości poprawek (rys. 7a),
2) Pomiary na sprzęgle drugim; zanotowanie otrzymanych wartości poprawek (rys. 7b),
3) Odpowiednią wartość poprawek do ustawienia otrzymano przez dodanie wyników kroku A i B.
Po wykonaniu tych kroków korygowano położenia silni ków według sumy wartości korekcyjnych z pomiaru dla sprzę gła pierwszego i drugiego. Po tych operacjach promień la sera podczas obrotu wału znajdował się już w obrębie detektora i ustawienie można było skorygować bardzo dokładnie (rys. 7c).
Dziś dzięki funkcji rozszerzenia zakresu pomiarowego procedura ta została wyeliminowana, a osiowanie zespołów maszyn mocno rozosiowanych bardzo uproszczone. Każdy z czterech wentylatorów ustawiano w ciągu około 4 godzin. Czas ten wynikał przede wszystkim z oczekiwania na przesunięcia i podnoszenie masywnych silników przez grupę montażową, która była do tego nieprzygotowana (brak śrub korekcji poziomej).
Sam czas pomiaru był bardzo krótki. Wentylatory ustawiono z dokładnością 0,9 i 0,22 mm/cm wału pośredniego dla przesunięć równoległych wałów oraz 0,04 i 0,02mm dla przesunięć kątowych wałów wentylatora i silnika. W przypadku wentylatorów spalin uwzględniono poprawkę na rozszerzalność cieplną.
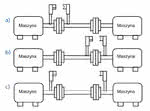
Rys. 7. Przebieg ustawiania wstępnego: krok pierwszy – pomiar na sprzęgle pierwszym (a), krok drugi – pomiar na sprzęgle drugim (b), krok trzeci – laser i pryzmat za montowane bezpośrednio na wałach wentylatora i silnika (c)
Oprócz ustawiania nowych zespołów maszyn system la serowy służy w Elektrowni Opole do szybkiego sprawdzania prawidłowości wyosiowania wałów pracują cych zespołów (średni czas sprawdzania wynosi ok. 15 min). Często podczas eksploatacji zachodzi podejrzenie o rozosiowanie zespołu pracujących maszyn. System laserowy Optalign bar dzo szybko wykrywa tę nieprawidłowość.
PODSUMOWANIE
Systemy laserowe zrewolucjonizowały ustawianie i sprzęganie maszyn pod względem dokładności, szybkości, wygody i kosztów. Ograniczenie kosztów ustawiania, wy nikające z krótkiego czasu i dużej dokładności tej opera cji, procentuje w Elektrowni Opole obniżeniem kosztów eksploatacji maszyn.
Józef Dwojak
Pruftechnik-Wibrem
www.pruftechnik.com.pl