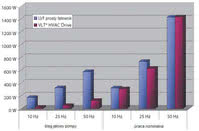
Rys. 1. Porównanie zużycia energii dla wykorzystania standardowego napędu oraz przetwornicy VLT firmy Danfoss
Pompy, wentylatory i kompresory są zazwyczaj niewidoczne, jednak w wielu instalacjach przemyslowych odgrywają ogromną rolę. Muszą one dzień po dniu niezawodnie pracować, gdyż bez wypełnianych przez nie zadań procesy technologiczne, takie jak np. dozowanie, napowietrzanie, produkcja chłodu, wentylacja i klimatyzacja byłyby zakłócone, a również nasze życie byłoby o wiele trudniejsze. Wszystkie te dziedziny zastosowań wymagają perfekcyjnie działających pomp, wentylatorów i podobnych im urządzeń.
Od lat ceny energii rosną, a wraz z tym zainteresowanie możliwościami ograniczenia zużycia prądu w zastosowaniach przemysłowych. Redukcja kosztów całkowitych i oszczędzanie energii są dziś aktualne jak nigdy, przede wszystkim z powodu tych drastycznie rosnących kosztów. A ceny rosną dalej! Właściciele i użytkownicy są w związku z tym zainteresowani rozwiązaniami pozwalającymi na oszczędne gospodarowanie energią zarówno w procesach technologicznych podczas produkcji, jak i w instalacjach wodociągowych i wentylacyjnych hal produkcyjnych oraz w budynkach biurowych.
Kluczowym rozwiązaniem umozliwiającym podniesienie efektywności energetycznej procesów technologicznych stanowi wykorzystanie przetwornic częstotliwości. Są one obecnie najefektywniejszym rozwiązaniem, pozwalającym poprzez regulację obrotów szybko i znacznie obniżyć zużycie energii.
REGULACJA OBROTÓW POMP I WENTYLATORÓW
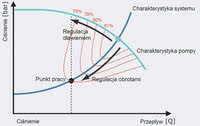
Rys. 2. Na schemacie krzywej charakterystyki obok charakterystyki pompy i instalacji przedstawione są również granice współczynnika sprawności. Zarówno przy regulacji dławieniem, jak i regulacji obrotami punkt pracy przesuwa się poza optimum współczynnika sprawności
Pompy i wentylatory nadają się wyśmienicie do uzyskania oszczędności energii. Dla wentylatorów i pomp wirnikowych, a więc maszyn przepływowych z charakterystyką mechaniczną zależną od kwadratu prędkości, zużycie energii zmniejsza się bowiem w trzeciej potędze wraz ze zmniejszaniem się obrotów. Rozpowszechnionym rozwiązaniem dla tych urządzeń jest więc wyposażenie ich w nowoczesne przetwornice częstotliwości i w ten sposób optymalne dopasowanie ich prędkości do aktualnego zapotrzebowania.
Ogromne pole do oszczędności daje typowo stosowany model projektowania takich systemów. W większości przypadków pompy i wentylatory stosowane w rozwiązaniach technicznych zaprojektowane są dla tzw. worst case, czyli dla przypadku najwyższego obciążenia największego zapotrzebowania wydajności. Przykładowo urządzenia klimatyzacyjne dobrane są tak, aby sprostać zadaniu w najgorętszy dzień w roku, w którym muszą pracować pod największym obciążeniem. Zgodnie z tym w pozostałym czasie pracują tylko z częściowym obciążeniem.
Analogicznie sprawa ma się dla urządzeń zapewniających stałe ciśnienie dostarczanej wody czy innych procesów technologicznych o zmiennej wydajności zależnej od pory roku, dnia czy warunków otoczenia - np. temperatury. Tu właśnie przetwornice częstotliwości pokazuja największe zalety ich zastosowania. Za tego rodzaju rozwiązaniem przemawia również fakt, że spadające ceny sprawiają, iż przetwornice stają się coraz bardziej atrakcyjną inwestycją. Uwaga jednak - nie wszystkie pompy i wentylatory nadają się do regulacji obrotów.
REGULACJA OBROTÓW JAKO CZYNNIK OSZCZĘDNOŚCI
Aby uniknąć niespodzianek w kwestii regulacji obrotów przy pompach i wentylatorach użytkownik powinien w fazie projektowania uwzględnić fakt, że wraz ze zmianą obrotów zmienia się również punkt pracy, a tym samym stopień sprawności maszyny przepływowej. W celu uniknięcia nieekonomicznych rozwiązań konieczne jest przed podjęciem decyzji o inwestycji sprawdzenie wszystkich aspektów, zarówno w wymiarze technicznym, jak i komercyjnym oraz logistycznym.
Aby regulacja obrotów pomp oraz wentylatorów miała sens ekonomiczny, użytkownik powinien wybrać przetwornicę częstotliwości nie tylko według najkorzystniejszej ceny, lecz wg oferty bazującej na analizie funkcjonalności i sprawności rozwiązania w całym okresie żywotności urządzenia.
STOPNIEŃ SPRAWNOŚCI MASZYN PRZEPŁYWOWYCH
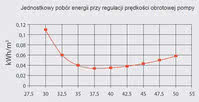
Rys. 3. Krzywa pokazuje zużycie energii wybranej pompy przy regulacji obrotami. Mniej więcej przy 32 Hz pojawiają się dodatkowe straty pompy, które przewyższają oszczędności. W przedstawionej instalacji optymalna energetycznie częstotliwość wynosi zgodnie z tym 38 Hz. Jeśli pompa nie byłaby regulowana obrotami, bilans energetyczny byłby znacznie gorszy
W wielu aplikacjach i starszych systemach stosuje się obecnie regulację pracy pomp i wentylatorów z wykorzystaniem klap, zaworów motylkowych albo trójdrożnych. Jeśli regulacja pompy wirnikowej odbywa się przy pomocy zaworu motylkowego, to poprzez dławienie przepływu przesuwa się punkt roboczy maszyny wzdłuż linii charakterystyki pompy. W porównaniu do znamionowego punktu pracy pompy dochodzi tutaj tylko do minimalnej redukcji ilości zużywanej energii.
Przy regulacji pompy za pomocą zmiany obrotów punkt pracy przesuwa się wzdłuż linii charakterystyki instalacji. Zapotrzebowanie na energię znacząco zmniejsza się w porównaniu z regulacją dławieniem, jak już wyżej wspomniano, w trzeciej potędze. I tak wentylator przy np. połowie prędkości obrotowej potrzebuje tylko jednej ósmej mocy. Takie zachowanie odnosi się do wszystkich maszyn przepływowych z kwadratowym przebiegiem charakterystyki w stosunku do obrotów.
Na schemacie krzywej charakterystyki (rys. 1) obok charakterystyki pompy i instalacji przedstawione są również granice współczynnika sprawności. Zarówno przy regulacji dławieniem, jak i przy regulacji obrotami punkt pracy przesuwa się poza optimum współczynnika sprawności. Na rysunku 2 pokazano zużycie energii wybranej pompy przy regulacji obrotami. Mniej więcej przy 32 Hz pojawiają się dodatkowe straty pompy, które przewyższają oszczędności.
W przedstawionym urządzeniu optymalna częstotliwość osiągana jest przy 38 Hz. Jeśli pompa nie byłaby regulowana obrotami, bilans energetyczny byłby znacznie gorszy. Jak już opisano systemy techniczne muszą być bardzo często zaprojektowane na obciążenia szczytowe. Siłą rzeczy - im dłuższy okres eksploatacji - tym w analizie profilu obciążenia układu wyższy udział pracy z częściowym tylko obciążeniem. Fakt ten uwzględniają ostatnio producenci maszyn przepływowych.
Projektują częściowo swoje agregaty tak, że optimum sprawności jest osiągane przy około 70% wydajności. Z tego powodu podczas modernizacji istniejących urządzeń albo przy pracach koncepcyjnych nad nowymi urządzeniami, użytkownicy powinni, wybierając maszyny przepływowe, zwracać uwagę na to, gdzie leży optimum sprawności i dostosować wybór do profilu obciążenia odpowiadającemu danej aplikacji, sprawdzając, czy wybór takich urządzeń dla ich instalacji ma sens.
DALSZA OPTYMALIZACJA PUNKTÓW PRACY - UKŁADY KASKADOWE
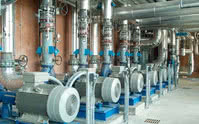
Rys. 4. Dla instalacji, w których pracują systemy wielopompowe, optymalnym rozwiązaniem są układy kaskadowe. Zapewniają one najlepszy stopień sprawności, redukują zużycie i koszty energii, jak również utrzymują równomierne obciążenie poprzez zmianę pompy prowadzącej
Ze współpracy urządzenia przepływowego i przetwornicy wynika pewien zakres obrotów, w którym system oszczędza energię. W tym zakresie maszyna powinna pracować większość czasu. Jeśli różnica pomiędzy maksymalnym zapotrzebowaniem na moc i średnim obciążeniem częściowym jest zbyt duża, to użytkownik musi poszukać innego rozwiązania. W tych przypadkach użytkownik potrzebuje rozwiązania do efektywnego energetycznie sterowania pracą kilku urządzeń.
Przykładem są instalacje podwyższania ciśnienia albo dystrybucji wody, wielostopniowe dmuchawy wież chłodniczych, instalacje pompowe wody wtórnej układów chłodniczych albo pompowe systemy ciepłownicze. Istnieje wiele powodów do zastosowania systemów o takiej konstrukcji. Najważniejszym jest optymalne ustawienie punktu pracy w zależności od zapotrzebowania systemu na moc. Przy dużym zakresie regulacji, w przypadku zastosowania tylko jednej pompy zaprojektowanej do wymogów sytuacji worst case, może to skutkować sprawnością pracy pompy wynoszącą przykładowo 10 do 20 procent, gdy tymczasem system wielopompowy charakteryzuje się stopniem sprawności najczęściej w zakresie powyżej 70%.
Z tego powodu sensowne jest zastosowanie układu kaskadowego. Często koszty inwestycji w modernizację istniejących systemów zwracają się po krótkim czasie. Przy kaskadzie pompowej regulowana obrotami pompa pokrywa podstawowe zapotrzebowanie na przepływ. Jeśli zużycie wzrasta, przetwornica włącza po kolei dalsze pompy. Pompy pracują tylko w zakresie ich optymalnej sprawności. Układ regulacji pomp dba zawsze o najlepsze wykorzystanie systemu pod względem energetycznym. Ten sam system może być analogicznie zastosowany przy regulacji wentylatorów. Odpowiednie regulatory kaskadowe można zamówić jako dedykowane moduły aplikacyjna dla przetwornicy częstotliwości.
ZASIĘGNĄĆ PORADY SPECJALISTY
W celu uzyskania optymalnego rozwiązania, dającego maksymalną efektywność energetyczną, użytkownik musi w każdym przypadku ocenić, jakie zalety i wady ma określone rozwiązanie techniczne. Należy przy tym uwzględnić fakt, że wraz z jakością technicznego rozwiązania rośnie jego cena. Ponieważ w dzisiejszych czasach prawie niemożliwa jest szczegółowa znajomość wszystkich technicznych urządzeń, a do tego wzrasta również złożoność współdziałania wszystkich komponentów, warto w razie potrzeby zasięgnąć rady eksperta i wraz z nim wyjaśnić wszystkie zalety i wady możliwych rozwiązań.
Tadeusz Minksztym
Danfoss Napędy Elektryczne VLT
www.danfoss.com