OKRESOWY PRZEGLĄD KURTYN JAKO WYMÓG FORMALNO-PRAWNY
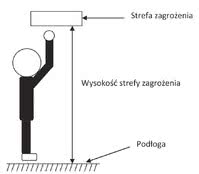
Rys. 1. Dostęp górnymi kończynami do strefy zagrożeń znajdującej się na pewnej wysokości
Stan techniczny maszyny, w której zainstalowana jest kurtyna, może z czasem się zmieniać. Szybkość tego procesu zależy od wielu czynników, do których można zaliczyć: wykorzystanie produkcyjne urządzenia, intensywność użytkowania czy środowisko, w którym zainstalowana jest maszyna i jego wpływ na jej stan techniczny.
Problem z tym związany został uwzględniony w przepisach prawa obowiązującego w Polsce. Kodeks Pracy (Dział X - BHP, rozdział I - Podstawowe obowiązki pracodawcy) zawiera informacje, że za stan bezpieczeństwa i higieny pracy odpowiedzialność ponosi pracodawca.
Jest on zobowiązany chronić zdrowie i życie pracowników przez organizowanie pracy w sposób zapewniający bezpieczne i higieniczne warunki pracy oraz reagować na potrzeby z tym związane, a także dostosowywać działania podejmowane w celu doskonalenia istniejącego poziomu ochrony zdrowia i życia pracowników. Pracodawca powinien również wziąć pod uwagę zmieniające się warunki wykonywania pracy.
Wszelkie informacje o zagrożeniach dla zdrowia i życia na poszczególnych stanowiskach i przy wykonywanych pracach, w tym o zasadach postępowania w przypadku awarii i innych sytuacji zagrażających zdrowiu i życiu pracowników oraz działaniach ochronnych i zapobiegawczych w celu wyeliminowania lub ograniczenia zagrożeń, powinny być przekazane pracownikom.
Wymagania dotyczące maszyn i urządzeń technicznych też zostały sprecyzowane - powinny one zapewniać bezpieczne i higieniczne warunki pracy poprzez zabezpieczenie pracownika przed urazami, działaniem niebezpiecznych substancji chemicznych, porażeniem prądem elektrycznym, nadmiernym hałasem, drganiami mechanicznymi i innymi szkodliwymi oraz niebezpiecznymi czynnikami.
Proces akcesji Polski do Unii Europejskiej wymagał wdrożenia do prawa lokalnego przepisów ustanowionych przez Parlament Europejski lub Radę UE. Wiązało się to z wprowadzeniem poszczególnych dyrektyw europejskich do prawa polskiego na podstawie odrębnych krajowych ustaw czy rozporządzeń.
Jedną z takich dyrektyw jest dyrektywa 2009/104/WE (Dyrektywa Parlamentu Europejskiego i Rady z 16 września 2009 roku dotycząca minimalnych wymagań w dziedzinie bezpieczeństwa i higieny użytkowania sprzętu roboczego przez pracowników podczas pracy).
Zawarte w niej wymagania określają, że pracodawca podejmuje konieczne środki zapewniające, aby sprzęt roboczy udostępniany pracownikom w miejscu pracy był właściwy do wykonania pracy i odpowiednio do tej pracy przystosowany.
Pracodawca zobowiązany jest również podjąć konieczne środki umożliwiające poprzez odpowiednią konserwację, utrzymanie sprzętu roboczego w ciągu całego czasu pracy w stanie, w którym może być użytkowany bez narażenia pracowników na uszczerbek na zdrowiu. Dyrektywa 2009/104/ WE dodatkowo wprowadza wymagania dotyczące kontroli sprzętu roboczego.
Pracodawca musi zapewnić, że jeśli bezpieczeństwo sprzętu roboczego uzależnione jest od warunków jego zainstalowania, powinien być on poddany wstępnej kontroli (po zainstalowaniu i przed pierwszym wprowadzeniem do użytku) oraz kontroli po montażu aby zagwarantować, iż został on prawidłowo zainstalowany i działa we właściwy sposób.
Aby utrzymać warunki ochrony zdrowia i bezpieczeństwa oraz dla wykrycia i usunięcia we właściwym czasie usterek mogących prowadzić do niebezpiecznych sytuacji, omawiany sprzęt narażony na takie działania podlega okresowym kontrolom. Te ostatnie należy także przeprowadzać również w przypadku, gdy zaistniały szczególne okoliczności, takie jak modyfikacje w sprzęcie roboczym, wypadki, zjawiska naturalne, na jakie sprzęt jest narażony oraz przedłużone okresy przestoju.
Wyniki kontroli i przeglądów należy rejestrować i przechowywać. Dla niektórych typów maszyn są dostępne normy wyrobu. Są to normy typu C określające większość wymagań w zakresie bezpieczeństwa.
Wśród informacji dotyczących przeglądów konserwacyjnych itp. normy zawierają często informację, że jeżeli dla redukcji ryzyka dla danego zagrożenia zastosowano kurtynę optyczną, wówczas należy okresowo badać czas odpowiedzi całego układu na jej zadziałanie poprzez pomiar czasu zatrzymania.
Jako przykład można by tu przytoczyć normę dotyczącą wtryskarek (PN-EN 201:2011 - Maszyna do przetwórstwa tworzyw sztucznych i mieszanek gumowych - Wtryskarki - Wymagania bezpieczeństwa). Jeśli w maszynie takiej strefa zamykania formy jest zabezpieczona kurtyną optyczną, to pomiar odpowiedzi całego układu na przerwanie wiązki kurtyny powinien być mierzony co roku.
Co w przypadku braku normy typu C? Otóż, jak wiemy, każdej maszynie powinna towarzyszyć dokumentacja techniczna uwzględniająca wyniki przeprowadzonej oceny ryzyka. Dokumentacja ta powinna zawierać zalecenia dotyczące częstości przeprowadzania przeglądów kurtyn.
Na bazie wieloletnich doświadczeń w realizacji ocen ryzyka dla różnych typów maszyn i przeglądów okresowych kurtyn zalecamy, aby dla maszyn użytkowanych ciągle na co najmniej jednej zmianie przeglądy kurtyn przeprowadzać nie rzadziej niż raz w roku.
Normy i przepisyWymienione we wstępie normy to przede wszystkim:
Do oddzielnych przepisów prawa należy również dyrektywa maszynowa 2006/42/WE. |
DLACZEGO INSPEKCJA JEST TAK ISTOTNA?
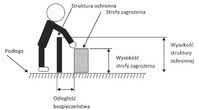
Rys. 2. Dostęp kończynami nad strukturą ochronną
Wymagania dotyczące odległości bezpieczeństwa i wymiarów osłon stałych oraz ruchomych blokujących przedstawione są w normach zharmonizowanych z Dyrektywą Maszynową (2006/42/WE - Dyrektywa Parlamentu Europejskiego i Rady z dnia 17 maja 2006 r. w sprawie maszyn, zmieniająca dyrektywę 95/16/ WE).
Takimi normami są PN-EN ISO 13855:2010 - Bezpieczeństwo maszyn - Umiejscowienie wyposażenia ochronnego ze względu na prędkości zbliżania części ciała człowieka oraz w PN-EN ISO 13857:2010 - Bezpieczeństwo maszyn - Odległości bezpieczeństwa uniemożliwiające sięganie kończynami górnymi i dolnymi do stref niebezpiecznych.
Zgodnie z zawartymi w nich wymaganiami, wysokość środków redukcji ryzyka w postaci osłon stałych i ruchomych powinna być odpowiednia, tak aby niemożliwe było dosięgnięcie do stref zagrożeń górnymi kończynami, jeśli te znajdują się na odpowiedniej wysokości. W odniesieniu do wysokości strefy zagrożenia, a także uwzględniając wymiary ludzkiego ciała, wysokość osłon ruchomych powinna być tak dobrana, aby niemożliwy był dostęp do tych stref zarówno górnymi, jak i dolnymi kończynami.
Przykłady dostępu do tych stref zostały przedstawione na rysunkach. Osłony stałe i ruchome są fizyczną, mechaniczną blokadą dostępu do strefy zagrożeń. Powinny one charakteryzować się solidną konstrukcją, pewnym mocowaniem na swoim miejscu i nie mogą być łatwe do ominięcia. Osłony stałe i ruchome muszą być również umieszczone w odpowiedniej odległości.
O ile łatwo sobie wyobrazić tego typu środki redukcji ryzyka, o tyle rzecz ma się inaczej, jeżeli wymagany dostęp do strefy jest na tyle częsty, że mija się z celem stosowanie osłony ruchomej. W takim przypadku zastosować można kurtynę optyczną, lecz wtedy nie ma już niestety fizycznej bariery.
Osłony ruchome blokujące bez ryglowania oraz kurtyny optyczne powinny być umieszczone w takiej odległości od strefy zagrożenia, aby przy uwzględnieniu prędkości poruszania się części ciała człowieka niemożliwe było dotarcie do ruchomych elementów przed ich zatrzymaniem. Wymagania te zostały określone w normie PN-EN ISO 13855:2010. Wyliczenia odległości bezpieczeństwa dokonuje się na podstawie wzoru: S = K·t + C, gdzie:
- S - odległość bezpieczeństwa (odległość w jakiej od strefy zagrożenia powinna być umiejscowiona kurtyna albo osłona ruchoma blokująca) (mm),
- K - stała wartość określająca prędkość poruszania się ciała człowieka lub części ciała (mm/s),
- t - czas zatrzymania się maszyny (s),
- C - odległość dodatkowa.
Stała K jest wartością prędkości poruszania się części ciała człowieka. Dla kurtyny optycznej umieszczonej w odległości mniejszej lub równej 500 mm od strefy zagrożenia należy przyjąć wartość 2000 mm/s. Dla większych odległości należy przyjąć 1600 mm/s. Czas zatrzymania t oznacza całkowity zmierzony czas, jaki upłynie od momentu przecięcia wiązki kurtyny do momentu całkowitego zatrzymania się maszyny.
Dodatkowa odległość C wyliczana jest na podstawie wzoru: C = 8·(d - 14), gdzie d - rozdzielczość kurtyny optycznej. Kluczowe przy inspekcji urządzenia ESPE (ang. electrosensitive protective equipment - elektroczułe wyposażenie ochronne) jest zmierzenie czasu odpowiedzi układu t. Aby taki pomiar był możliwy, wymagany jest certyfikowany sprzęt pomiarowy.
Sprzęt ten powinien być kalibrowany w odpowiednich odstępach czasu przez uprawnione do tego jednostki. Osoba dokonująca pomiarów powinna mieć wymagane kwalifikacje.
O CZYM NALEŻY WIEDZIEĆ
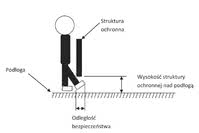
Rys. 3. Dostęp kończynami pod strukturą ochronną
Nie należy jednak zapominać o sposobie montażu kurtyny optycznej. Oprócz tego, że musi się ona znajdować w odpowiedniej odległości bezpieczeństwa od strefy zagrożenia, nie powinno być żadnej możliwości obejścia tej kurtyny.
Jeżeli pod kurtyną odległość między kurtyną i np. stołem roboczym jest na tyle duża, iż możliwe jest sięganie przez tę szczelinę ręką, to należy przewidzieć dodatkowy środek redukcji ryzyka w tym miejscu, jeśli odległość do strefy niebezpiecznej jest mniejsza niż znormalizowana długość ludzkiego ramienia.
Oczywiście należy sprawdzić strefy boczne kurtyny oraz strefę górną. Jeżeli kurtyna jest zainstalowana na statywach mocowanych do podłoża to należy spełnić wymagania opisane powyżej i jednocześnie zagwarantować, że najniższa wiązka kurtyny jest na wysokości uniemożliwiającej przeczołganie się pod kurtyną. Również konfiguracja sprzętowa kurtyny optycznej z resztą układu sterowania wymaga sprawdzenia.
Trudno sobie wyobrazić, żeby kurtyna typu 4 podłączona była do wejścia standardowego sterownika PLC. W tym punkcie należy przeanalizować układ sterowania, począwszy od kurtyny, a skończywszy na elementach wykonawczych typu styczniki czy elektrozawory. Tylko na tej podstawie możliwe jest stwierdzenie, iż układ sterowania związany z bezpieczeństwem jest odpowiednio niezawodny.
Pomiar czasu zatrzymania maszyny jest więc jedynie elementem składowym inspekcji urządzeń ESPE. Potwierdzeniem inspekcji powinien być raport, w którym powinny znaleźć się pełne dane identyfikacyjne kurtyny, maszyny, miejsca instalacji maszyny, użytkownika oraz osoby dokonującej oględzin.
Raport powinien oczywiście zawierać stosowne wyliczenia potwierdzające (bądź nie), w zależności od zmierzonego czasu zatrzymania, odległość bezpieczeństwa oraz informacje na temat bezpośredniego otoczenia kurtyny optycznej. W celu łatwej identyfikacji kurtyna, która przeszła inspekcję z wynikiem pozytywnym, powinna zostać opatrzoną naklejką identyfikującą inspekcję z raportem z tej inspekcji.
Raporty należy przechowywać do wglądu przez okres pięciu lat (Rozporządzenie Ministra Gospodarki z dnia 30 października 2002 r. w sprawie minimalnych wymagań dotyczących bezpieczeństwa i higieny pracy w zakresie użytkowania maszyn przez pracowników podczas pracy).
Pilz Polska przeprowadza wstępne i okresowe inspekcje ESPE zarówno jako oddzielną usługę, jak też przy przeprowadzaniu oceny ryzyka maszyn, o ile wyposażenie ESPE jest środkiem redukcji ryzyka w ocenianej maszynie.
Nasi specjaliści przechodzą indywidualne szkolenia potwierdzane egzaminem przez DAkkS (Deutsche Akkreditierungsstelle) - niemiecką jednostkę akredytującą, co daje naszym klientom gwarancję, iż nasi specjaliści są odpowiednio przeszkoleni i posiadają wymagane kwalifikacje. Otrzymane certyfikaty obligują nas do przechowywania dokumentacji przez wymagany okres i upoważniają do umieszczenia naklejki z odpowiednimi informacjami na badanej kurtynie, która pomyślnie przeszła inspekcję.
Sebastian Remian
Pilz Polska Sp. z o.o.
www.pilz.pl