Polski oddział firmy zlokalizowany w Piekarach Śląskich wytwarza 40 tys. km siatek wędliniarskich rocznie. Wyroby produkowane przez firmę trafiają do większości zakładów mięsnych w Polsce i do dystrybutorów w 30 krajach na całym świecie.
Firma wdrożyła system 5S zgodny z filozofią Lean Manufacturing. Jednym z elementów poprzedzających to wdrożenie były badania migawkowe pozwalające na wskazanie obszarów wymagających usprawnienia. Ich wyniki wykazały możliwości poprawy wydajności realizacji zleceń.
CZĘŚĆ 1 - INTEGRACJA SYSTEMU MES Z ERP - WDROŻENIE

Rys. 1. Główne etapy zarządcze projektu
Odpowiedzią na zapotrzebowanie w obszarze automatyzacji i poprawy wydajności produkcji było przeprowadzenie przez zespół specjalistów z firmy Queris analizy potrzeb użytkowników biznesowych i produkcyjnych, na bazie których zbudowano szczegółową specyfikację wymagań oraz architekturę rozwiązania mającego integrować system ERP (system Impuls firmy BPSC) z Platformą Systemową Wonderware rozbudowaną o moduły klasy MES. Podczas warsztatów planistycznych prace podzielono na trzy główne etapy zarządcze.
PRZYGOTOWANIA
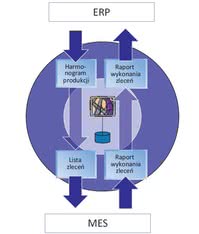
Rys. 2. Przepływ informacji z wykorzystaniem mechanizmu middleware
Pierwszym krokiem było ujednolicenie listy produktów (indeksów, wyrobów). Kluczowe dla procesu integracji jest prawidłowe zamodelowanie procesów produkcyjnych, które w dalszych fazach pozwala różnym osobom dobrze orientować się w specyfice produkcji firmy. Trzeba było również uporządkować kwestie logistyczne związane z obiegiem surowców w produkcji.
Zdecydowano o zakupie wysokiej klasy sprzętu: serwerów, macierzy dyskowej, switchy zarządzalnych. Skonfigurowano oprogramowanie Wonderware: platformę komunikującą się z warstwą sprzętową, system do wizualizacji procesów przemysłowych, platformę informacyjną opartą na serwerze WWW. Dzięki elastycznej architekturze systemu moduły łatwo integrują się z systemami ERP z jednej strony, a z drugiej z automatyką przemysłową.
Tak przygotowane zasoby pozwoliły na uzyskanie podstawowych funkcjonalności w ramach połączenia systemu ERP z danymi przychodzącymi z produkcji, takich jak: automatyczne generowanie dokumentów magazynowych, automatyczna wymiana zleceń w produkcji, informowanie o stanach magazynowych. Efektem pierwszego etapu była możliwość zdalnej wizualizacji stanu prac maszyn na terminalach użytkowników przy użyciu aplikacji Information Server.
WDROŻENIE MES
Drugi etap dotyczył wdrożenia systemu zarządzania produkcją MES. Określono przepływy materiałów w przedsiębiorstwie i skonfigurowano je w systemie. Zdefiniowane zostały magazyny podręczne oraz magazyny główne: surowców, półproduktów oraz wyrobów gotowych.
Zdefiniowano w systemie procedury produkcyjne oraz receptury dla ponad 600 produktów firmy NomaNet. Dodano w systemie również poszczególne maszyny i urządzenia (jednostki produkcyjne), gniazda produkcyjne oraz zmiany i zespoły pracownicze odpowiedzialne za obsługę poszczególnych obszarów produkcyjnych i etapów produkcji.
WYMIANA INFORMACJI
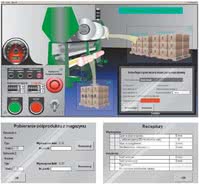
Rys. 3. Przykładowe ekrany wizualizacyjne
Już na tym etapie zaczęła funkcjonować obustronna wymiana informacji pomiędzy wdrażanym systemem MES i systemem Impuls. Po otrzymaniu informacji o wpłynięciu zamówienia, system ERP generuje zlecenie na wykonanie określonej ilości produktu o zadanych parametrach (w tym przypadku jest to liczba metrów bieżących siatki wędliniarskiej o ściśle określonych właściwościach, takich jak rozciągliwość siatki, zagęszczenie włókien gumy, rodzaj oplotu, rodzaj osnowy i wielu innych).
Zlecenie przekazywane jest bezpośrednio na panele operatorskie, w które wyposażone zostały maszyny produkcyjne. Gdy produkcja gotowego wyrobu zostaje ukończona (np. wykonano przesłane przez system zlecenie na 10 tys. metrów bieżących siatki) i produkt zostaje spakowany, w sposób automatyczny wygenerowany zostaje dokument przyjęcia do magazynu.
W automatyczny sposób generowane są również pozostałe dokumenty związane z przepływem materiałów w przedsiębiorstwie (przesunięcia międzymagazynowe, rozchód wewnętrzny, przyjęcie do magazynu surowca lub wytworzonego półproduktu) oraz wydaniem gotowego produktu na zewnątrz, do klienta.
Każde odejście od zdefiniowanych w systemie procedur jest natychmiast sygnalizowane kierownikowi produkcji, ze wskazaniem miejsca i przyczyny. Jeśli np. pracownik nie wykona zadania (np. nie ustawi właściwych parametrów maszyny produkującej), system może automatycznie zablokować wykonanie kolejnej czynności oraz wygenerować ostrzeżenie do przełożonego o braku wprowadzenia koniecznych danych lub wykonania określonych czynności (ustawień i regulacji maszyny zgodnych z recepturą i niezbędnych do wykonania partii produktu o określonych parametrach).
Tak skrupulatna kontrola prowadzona w czasie rzeczywistym obejmuje maszyny i urządzenia wykorzystywane w procesie produkcji, począwszy od przyjęcia surowców do magazynu, aż po etap pakowania i etykietowania gotowych produktów.
W ten sposób wyeliminowane zostają potencjalne błędy w procesie produkcji, ponieważ system natychmiast sygnalizuje, gdy do wyprodukowania zadanej partii produktu omyłkowo próbuje zostać użyty niewłaściwy surowiec lub półprodukt. Ilość odpadów zostaje zredukowana do minimum, co równocześnie obniża koszty strat na surowcach i półproduktach oraz koszty segregacji i utylizacji odpadów poprodukcyjnych.
ZWIĘKSZENIE WYDAJNOŚCI
Proces kończy się wdrożeniem ostatniej części systemu, odpowiedzialnej za zwiększenie wydajności produkcji. Po zdefiniowaniu wskaźników wydajnościowych i ich skonfigurowaniu w systemie MES można śledzić wyniki i wprowadzać odpowiednie działania korygujące.
Wstępna ocena wdrożenia pozwoliła na stwierdzenie, że założone cele biznesowe i operacyjne są realizowane. Jest to jeden z nielicznych przypadków wdrożeń na terenie Polski, w którym użytkownik zdecydował się na połączenie zalet stosowania technologii informatycznych w obszarze produkcji z metodycznym podejściem do jej doskonalenia.
CZĘŚĆ 2 - KORZYŚCI Z WYKONANEGO WDROŻENIA
Wdrożenie pełnego systemu umożliwia podgląd aktualnego stanu pracy maszyny, otrzymanie natychmiastowych powiadomień o stanach awaryjnych, zdalne przesyłanie poleceń, uwag i instrukcji, gromadzenie danych historycznych o stanie maszyn, dokonywanie szczegółowych analiz, poprawę wydajności i efektywności produkcji, a co najważniejsze - śledzenie przepływów materiałowych, genealogii produkcji, monitorowanie stanów materiałowych i zleceń. Wszystkie informacje są bezpośrednio lokowane w systemie ERP klienta.
USPRAWNIENIE PRZEPŁYWU INFORMACJI
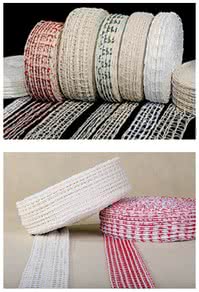
Rys. 4. Przykładowe siatki wytwarzane przez NomaNet
Wdrożenie rozwiązania MES, dedykowanego do analiz procesów produkcyjnych, przynosi ogromne korzyści, ponieważ do minimum redukuje w przedsiębiorstwie tradycyjny obieg informacji związanej z realizacją zleceń produkcyjnych, a tym samym minimalizuje liczbę potencjalnych pomyłek i błędów często popełnianych podczas produkcji.
Informacja generowana i przekazywana w sposób automatyczny oszczędza czas personelu hal produkcyjnych, przeznaczany w sporej części na wypełnianie kart maszynowych i prowadzenie dokumentacji przebiegu produkcji. Teraz wszystkie te informacje, automatycznie zebrane, gromadzone są przez system, który na żądanie uprawnionego użytkownika generuje raport.
Dyrektorzy produkcji i zarząd przez przeglądarkę internetową mają możliwość podglądu stanów pracy poszczególnych maszyn, gniazd i linii produkcyjnych oraz wgląd w stopień wykonania poszczególnych zamówień. Istotną funkcjonalnością systemu MES zintegrowanego z systemem ERP jest automatyczny monitoring stanów magazynowych.
Wpływające do przedsiębiorstwa zamówienie na określoną ilość danego rodzaju produktu system identyfikuje z recepturą - sprawdza stan magazynowy w zakresie surowców oraz półproduktów niezbędnych do realizacji zamówienia, automatycznie generując informację o możliwościach produkcyjnych pod względem aktualnych stanów magazynowych oraz pod względem obłożenia maszyn na linii produkcyjnej.
Funkcja ta pozwala na określenie terminu realizacji zamówienia. Istnieje więc możliwość harmonogramowania produkcji oraz określenia priorytetów dla danego rodzaju zleceń produkcyjnych. Zamówienie dla kluczowego dla nas klienta powinno zostać wykonane w jak najkrótszym terminie. System jest w stanie w optymalny sposób rozplanować obłożenie maszyn w przypadku, gdy wpływa zlecenie na dużą ilość danego rodzaju produktu.
W takiej sytuacji algorytm - biorąc pod uwagę obłożenie maszyn zleceniami w danym gnieździe produkcyjnym oraz priorytet każdego z tych zleceń - jest w stanie zaproponować optymalny ich podział na poszczególne maszyny, tak aby zlecenia o najwyższym priorytecie zostały wykonane w pierwszej kolejności i w najkrótszym czasie.
System MES ułatwia komunikację z personelem odpowiedzialnym za utrzymanie ruchu na liniach produkcyjnych poprzez podgląd stanu pracy poszczególnych maszyn i urządzeń. Automatyczna informacja o wystąpieniu awarii danego urządzenia oraz jej rodzaju pozwala na natychmiastową i odpowiednią reakcję personelu, oszczędzając w ten sposób czas, a tym samym skracając czas przestoju maszyny.
Sprzężenie następuje również pomiędzy sferą finansowo-księgową a produkcją, co pozwala na efektywne i wydajne prowadzenie procesów biznesowych. Systemy MES pozwalają również odnaleźć zależności ukryte między informacjami z produkcji, zamieniając je na realne oszczędności firmy.
PODSUMOWANIE
Integracja systemów informatycznych sprawia, że wszystkie szczegółowe dane gromadzone są w jednym miejscu, a na ich podstawie można dokonać zbiorczej analizy zarówno od strony biznesowej (np. efektywności, planowania, kosztów), jak i produkcyjnej (wydajności, czasu produkcji, przestojów, renowacji maszyn itp.). Osoba zarządzająca, mając dostęp do przekrojowych danych i wyników analizy, może usunąć słabe ogniwa i wdrożyć rozwiązania usprawniające działanie przedsiębiorstwa.
Paweł Drobny
Integrator: Queris
www.queris.eu
Dostawca: ASTOR
www.astor.com.pl