CZUJNIKI W POMIARACH TEMPERATURY
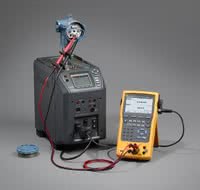
Fot. 1. Kalibrator Fluke współpracuje z innymi kalibratorami tej firmy w celu automatyzacji i dokumentowania procesu
Do pomiarów i monitorowania temperatury w przemyśle procesowym bardzo często wykorzystywane są elementy termorezystancyjne (RTD), w tym platynowe (PRT) oraz termopary. RTD i PRT są używane zwłaszcza wtedy, gdy liczy się duża dokładność pomiarów. Termopary mogą być wykorzystywane w szerszych zakresach temperatur niż PRT i RTD, ale są one mniej dokładne. Najczęstszym problemem z nimi związanym jest dryft czujnika, co koryguje się poprzez kalibrację.
Czujniki temperatury wyposażone są w osłonę ochronną, która pozwala na umieszczanie ich bezpośrednio w środowisku/medium, którego pomiar ma być wykonany. Mogą one być również umieszczane w dodatkowej osłonie, co stosowane jest po to, aby zapewnić ochronę czujnika przed drganiami oraz by móc umieszczać go w środowiskach, w których panuje zwiększone ciśnienie lub też tam, gdzie bezpośrednie zamontowanie nie zapewniłoby wystarczającego bezpieczeństwa jego pracy.
Mierniki konwertują zmiany w rezystancji termometrów na temperaturę wyświetlaną w postaci cyfrowych wskazań, zaś przenośne kalibratory temperatury oprócz tego, że wyświetlają wartość temperatury, wyposażone są też w odpowiednie wyjście umożliwiające kalibrację mierników, regulatorów, przetworników, itp.
CZUJNIKI I PRZETWORNIKI
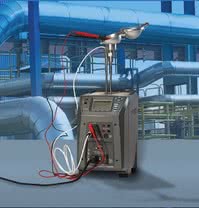
Fot. 2. Kalibrator 914X Dry-Well z automatycznym grzaniem i chłodzeniem czujnika; zapewnia pomiar pętli prądowej 4-20 mA, rezystancji, napięcia oraz zautomatyzowany zapis wyników.
W wielu instalacjach przetworniki temperatury są podłączone do zacisków termorezystorów i termopar. Odpowiadają one za zmianę zmierzonej wartości rezystancji lub napięcia na standardowy sygnał, taki jak np. prądowy 4-20 mA. Może on być przesyłany do mierników, regulatorów czy układów sterowania.
W tym przypadku skalibrowane muszą zostać dwa elementy: czujnik temperatury i przetwornik. Kalibracja czujnika wymaga źródła temperatury, takiego jak kalibrator z suchym blokiem lub mikro-wanna. Z kolei kalibrację przetwornika można wykonać za pomocą np. kalibratora przenośnego, służącego do kalibracji temperatury lub urządzenia wielofunkcyjnego.
Niektóre przetworniki temperatury mogą być regulowane cyfrowo za pomocą dedykowanych narzędzi lub standardowych protokołów komunikacyjnych, takie jak np. HART. Inne zaś wymagają regulacji śrubokrętem, ustawienia odpowiednio potencjometra umieszczonego w przetworniku. Jeśli czujnik z zamontowanym przetwornikiem w głowicy znajduje się poza zakresem tolerancji, należy umieścić czujnik w kalibratorze temperatury np. Fluke 9142 z suchym blokiem, nastawić pożądaną wzorcową temperaturę, a zakres i przesunięcie należy regulować na przetworniku.
TERMOMETRY MECHANICZNE
Są one stosowane do pomiarów temperatury w takich aplikacjach jak zbiorniki ciśnieniowe, kotły i rurociagi. Powodem ich kalibracji są wymogi zapewniania jakości czy zarządzania energią, które związane są z takimi normami jak ISO 9001 oraz ISO 50001, przepisy FDA, wymogi bezpieczeństwa, ale też dobre zasady praktyki produkcyjnej oraz konieczność kontroli kosztów energii.
W niektórych przypadkach króćce pomiarowe są wbudowane w instalację tak, że termometr odniesienia może być umieszczony w jednej linii z termometrem do kalibracji, a pomiar wykonuje się in situ. Termometry mechaniczne (bimetalowe, wypełnione płynem, szklane) nie wymagają użycia kalibratorów wielofunkcyjnych.
Do wzorcowania powyższych termometrów stosuje się kalibratory z suchym blokiem np. Fluke 9140. Natomiast jeżeli kryzy, gniazda lub zbiorniczki uniemożliwiają minimalne zanurzenie w suchym bloku kalibratora lub jeśli czujnik jest zbyt krótki dla wystarczającego zanurzenia w suchym bloku, należy użyć mikrowannę.
ŹRÓDŁA TEMPERATUR
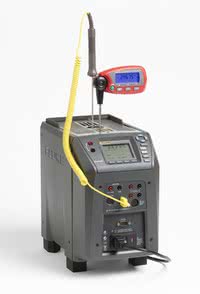
Fot. 3. Czujniki są umieszczane w kalibratorze w otworach wymiennych bloków
Takimi źródłami są m.in. piece Fluke, które zapewniają odpowiednią temperaturę do kalibracji elementów pomiarowych. Wyróżniamy ich dwa podstawowe rodzaje: kalibratory z suchym blokiem , które są zazwyczaj przenośne, oraz wanny kalibracyjne, w których wykorzystuje się ciekłe substancje (olej, glikol, itp.) w celu osiągnięcia większej stabilności mierzonej temperatury. Wanny są większe niż piece z suchymi blokami, ponadto są przeważnie stacjonarne.
Kalibratory z suchymi blokami wyposażone są we wkłady, które zawierają otwory wywiercone tak, aby dopasować do nich standardowe średnice czujników RTD, PRT i termopar. W zależności od modelu, kalibratory mogą być wyposażone w wymienne wkłady/bloki.
Aby skalibrować czujnik RTD lub PRT, należy zdemontować sondę z ochronnej osłony lub innej lokalizacji, w której czujnik został zamontowany. Następnie umieszczamy czujnik w bloku kalibratora i podłączamy go do odpowiednich zacisków w kalibratorze. Ustawiamy pożądaną temperaturę i po jej ustabilizowaniu odczytujemy rezystancję na wyświetlaczu kalibratora.
DLACZEGO KALIBROWAĆ?
Konieczność uzyskania spójnych w czasie wyników jest jednym z najważniejszych powodów, dla których wykonujemy kalibrację. Ważna jest przy tym odpowiednia dokładność samego kalibratora. Może istnieć potrzeba potwierdzenia poziomu dokładności zgodnego z normami, które określają współczynnik dokładności pomiaru lub współczynnik niepewności pomiaru. Na przykład wiele standardów wymaga stosunku 4:1 pomiędzy określoną tolerancją badanego urządzenia a dokładnością lub niepewnością urządzeń użytych do kalibracji.
Omawiana dokładność jest ważna z jeszcze jednego powodu. Stosując dokładne wzorce i określone procedury, można dokładnie zaplanować czas przestoju potrzebny do wykonania kalibracji. Przy zastosowaniu wzorców o małej dokładności możemy uzyskać wyniki poza zakresem tolerancji. W rezultacie procedura weryfikacji zamienia się w dodatkowe dostrajanie i weryfikację w każdym z punktów testowych, tak aby wykazać, że ostateczna nastawa spełnia normy. Procedury te zwiększają czas przeprowadzenia kalibracji, w rezultacie wydłużając czas przestoju.
Fluke
www.fluke.com.pl