W produkcji addytywnej produkty i komponenty są wytwarzane na podstawie cyfrowego projektu w drukarce 3D i wykorzystują warstwową strukturę materiału. Jest to możliwe dzięki optymalnej interakcji nowoczesnych maszyn, inteligentnego połączenia w sieć poprzez platformę opartą na chmurze oraz dojrzałych technologicznie procesów druku 3D. Materiały stosowane obecnie w drukarkach 3D to głównie metale, specjalne tworzywa sztuczne, żywice syntetyczne oraz ceramika.
OPTYMALIZACJA KOMPONENTÓW I REDUKCJA MASY
Produkcja addytywna ma już ugruntowaną pozycję w branżach, w których ogromne znaczenie ma redukcja wagi komponentów. Należą do nich przemysł samochodowy i lotniczy, ale także sektor metalowy i medyczny. Na przykład w przemyśle lotniczym stosuje się wytwarzanie przyrostowe w celu obniżenia masy elementów konstrukcyjnych samolotów, co prowadzi do znacznych oszczędności materiałowych w produkcji części. Dodatkowo, mniejsza masa całkowita samolotu ma bezpośredni wpływ na wartości zużycia paliwa przez statek powietrzny, a to z kolei przyczynia się bezpośrednio do poprawy jego oddziaływania na środowisko.
Od kilku lat z platformy 3DEXPERIENCE oraz oprogramowania do inżynierii i projektowania 3D CATIA firmy Dassault Systèmes korzysta Airbus. Producent samolotów opracował również we współpracy z Dassault Systèmes specjalne narzędzie do projektowania 3D. Używany do produkcji komponentów do Airbusa A350 "MyShape" pozwala Airbusowi tworzyć nowe elementy konstrukcyjne za pomocą generatywnego procesu projektowania. Termin ten oznacza, że nowe części nie są już opracowywane na podstawie kształtu jako wyznacznika, ale na podstawie funkcji. Projektantów interesuje ustalenie, jaki kształt elementu najlepiej spełni w samolocie dane wymagania. Na tej podstawie oprogramowanie Dassault Systèmes generuje optymalną dla danego samolotu konstrukcję komponentu. Następnie symulowane jest użycie nowych komponentów w samolocie w celu wypróbowania różnych składów materiałów lub w razie potrzeby dokonania dalszych optymalizacji. Procedura ta znacznie przyspiesza opracowywanie nowych części.
Kolejną zaletą symulacji jest możliwość uwzględnienia odkształceń termicznych komponentów już na etapie konstruowania. Dzieje się tak w trakcie lub po wytworzeniu elementu w drukarce 3D w zależności od charakteru materiału i może wpłynąć na zmianę funkcjonalności produktu końcowego. Aby tego uniknąć, CATIA oferuje możliwość symulacji odkształceń termicznych i włączenia ich wyniku bezpośrednio do geometrycznej kompensacji odkształceń. Gwarantuje to, że element będzie ostatecznie wykonany dokładnie w wymaganym kształcie.
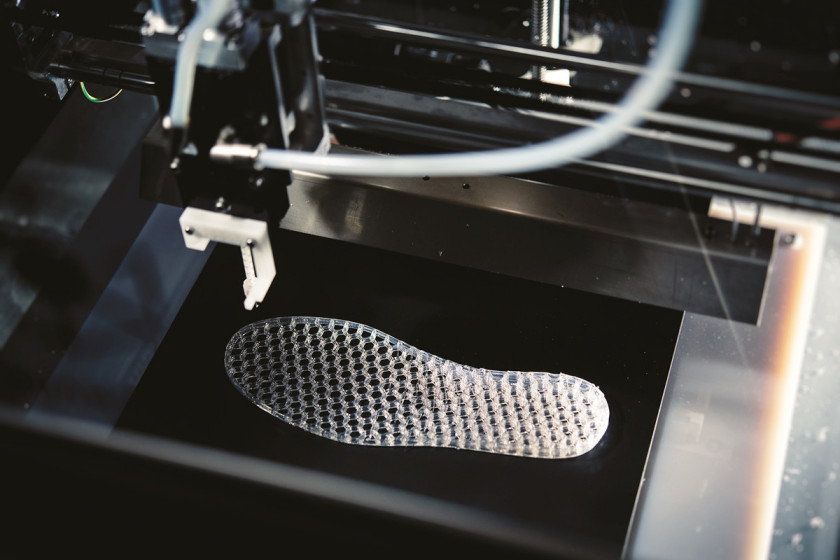
ZMNIEJSZENIE KOSZTÓW MATERIAŁÓW
Nie tylko skład materiału odgrywa ważną rolę w produkcji addytywnej. W miarę możliwości należy bowiem za jej pomocą promować również oszczędzanie cennych materiałów. W ramach optymalizacji topologii firmy mogą dostosować i poprawić wykorzystanie materiałów konstrukcyjnych w sposób celowy, znacznie zmniejszając ilość resztek powstających w produkcji konwencjonalnej – na przykład przy zastosowaniu metali. Dany element jest zazwyczaj frezowany z dużego bloku, zatem po zakończeniu produkcji pozostaje spora ilość materiału, który nie może być ponownie wykorzystany bezpośrednio. Natomiast w produkcji addytywnej komponenty są budowane warstwowo, co prowadzi do oszczędności materiału.
Wytwarzanie przyrostowe pozwala również na wytwarzanie jednorazowo całych podzespołów bez konieczności czasochłonnego przezbrajania maszyn produkcyjnych. Co więcej, kompletny zespół jest wytwarzany warstwa po warstwie przy użyciu druku 3D, co minimalizuje nie tylko czas potrzebny na wyprodukowanie go, ale także poświęcony na złożenie poszczególnych części zespołu. W ten sposób przedsiębiorstwo może zaoszczędzić czas na produkcję i trwale obniżyć koszty materiałowe.
Dzięki zastosowaniu produkcji addytywnej Airbus był w stanie zredukować wskaźnik Buy to Fly do jednej dziesiątej – w porównaniu do konwencjonalnie produkowanych komponentów. Wskaźnik ten odnosi się do stosunku ilości materiału zakupionego do faktycznie wykorzystanego, czyli w przypadku Airbusa ostatecznie zainstalowanego w samolocie. Airbus w swoich samolotach Airbus A350 wykorzystuje obecnie ponad 1000 komponentów, które zostały wyprodukowane z wykorzystaniem produkcji addytywnej.
ELASTYCZNA REALIZACJA WYMAGAŃ KLIENTA
Kolejną zaletą wytwarzania addytywnego jest elastyczna i, w porównaniu z produkcją konwencjonalną, ekonomiczna produkcja prototypów lub pojedynczych części. Dzięki temu firmy mogą w najlepszy możliwy sposób uwzględniać życzenia swoich klientów. W szczególności z tej technologii może skorzystać branża dóbr konsumpcyjnych. Marka Ecco wprowadziła na rynek projekt personalizacji obuwia QUANT-U, który stanowi połączenie skanowania 3D z drukiem 3D. W ramach projektu QUANT-U wykorzystywane są możliwości analizy w czasie rzeczywistym, co pozwala na stworzenie projektu i druku personalizowanych silikonowych wkładek, na podstawie unikalnego cyfrowego odcisku stopy. Cały proces odbywa się w sklepie i trwa zaledwie kilka godzin.
Elastyczność jest również korzystna dla przedsiębiorstw przy produkcji złożonych prototypów lub części zamiennych. Dzięki produkcji addytywnej mogą one szybko odpowiadać na potrzeby i produkować w bliskiej odległości od klienta. Jeśli dana firma zazwyczaj produkuje w Europie, ale potrzebuje części zamiennej w Indiach, można ją łatwo wyprodukować na miejscu, używając druku 3D. Oznacza to nie tylko skrócenie dystansu do klienta, ale także znaczne obniżenie kosztów transportu.
CO PRZYNIESIE PRZYSZŁOŚĆ?
Obecnie produkcja addytywna jest stosowana szczególnie w branżach, którym przede wszystkim zależy na produkcji prototypów, spersonalizowanych pojedynczych części lub małych serii. Trwają już jednak prace nad wprowadzeniem procesów drukowania 3D do produkcji seryjnej na większą skalę.
Szczególnie w sektorze medycznym prowadzone są szeroko zakrojone badania i rozwój w zakresie materiałów użytkowych. Dzięki produkcji addytywnej firma Otto Bock Healthcare zdołała w bardzo krótkim czasie udoskonalić swoją innowacyjną protezę dłoni Michelangelo. Bazując na platformie 3DEXPERIENCE i aplikacji CATIA Imagine & Shape firmy Dassault Systèmes, firma ta, reprezentująca branżę technologii medycznych, była w stanie zoptymalizować konstrukcję powierzchni swoich protez dłoni i tym samym wymodelować je szczególnie wiernie. Kolejne projekty badawcze wykazują również dalszy potencjał w dziedzinie odbudowy narządów, co może pomóc w przyszłości wielu ludziom.
Interesujące możliwości pojawiają się również dla branży high-tech i elektroniki, dla których liczą się możliwie najmniejsze rozmiary. W tym przypadku możliwe byłoby wbudowanie czujników lub komponentów elektronicznych bezpośrednio w strukturę uzyskaną za pomocą produkcji addytywnej. Na przykład czujniki przyrządów pomiarowych mogłyby być bezpośrednio wdrukowywane w układy elektroniczne. Pojawili się nawet pierwsi dostawcy, którzy są już w stanie produkować złożone wielowarstwowe płytki drukowane w technologii druku 3D w ciągu 15 godzin zamiast 50 dni.
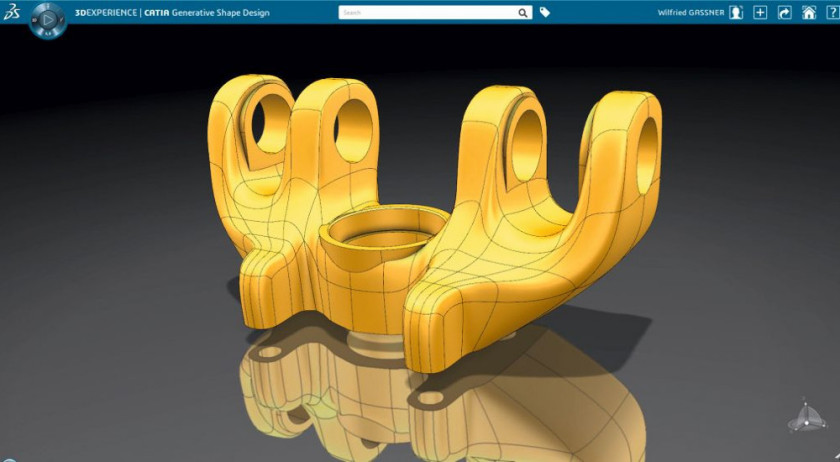
POSUMOWANIE
Produkcja addytywna jest ewidentnie nie tylko trendem, ale i technologią rewolucyjną, która będzie w przyszłości nabierać coraz większego znaczenia, pozwalając firmom na uzyskanie przewagi konkurencyjnej poprzez większą zwinność, innowacyjny rozwój produktów, elastyczne wytwarzanie i trwałą redukcję kosztów.
Ireneusz Borowski, Country Manager Poland
Dassault Systèmes
www.3ds.com