Według ISO/TS 15066 proces identyfikacji zagrożeń związanych z pracą robotów powinien uwzględniać co najmniej następujące elementy:
– zagrożenia związane z robotami, w tym:
- charakterystykę robota (np. obciążenie, prędkość, siła, pęd, moment obrotowy, moc, geometria, powierzchnia, kształt i materiał);
- quasi-statyczne warunki kontaktu z robotem, gdzie część ciała operatora może być ściśnięta pomiędzy ruchomą częścią systemu robota a inną nieruchomą lub ruchomą częścią;
- położenie operatora w stosunku do bliskości robota (np. praca pod robotem);
- zagrożenia związane z systemem robota, w tym:
- zagrożenia związane z efektorem końcowym i elementem obrabianym, ergonomią konstrukcji, występowaniem ostrych krawędzi, upadkiem przedmiotu obrabianego, występowaniem części odstających, wymianą narzędzi;
- ruch i lokalizację operatora w odniesieniu do położenia części, orientację konstrukcji (np. wyposażenie, podpory budowlane, ściany) oraz lokalizację zagrożeń na osprzęcie;
- projekt wyposażenia, miejsce występowania ściśnięcia ciała operatora, inne powiązane z tym zagrożenia;
- określenie czy kontakt byłby przejściowy (w którym część ciała operatora nie jest ściśnięta i może cofnąć się z ruchomej części systemu robota), czy quasi-statyczny, oraz określenie narażonych części ciała operatora;
- projekt i lokalizację każdego ręcznie sterowanego urządzenia prowadzącego robota (np. dostępność, ergonomia, potencjalne niewłaściwe użycie, możliwość pomylenia elementów sterowniczych, wskaźników stanu itp.);
- wpływ i skutki otoczenia (np. usunięcie osłony sąsiedniej maszyny, bliskość promieniowania laserowego);
– zagrożenia związane z aplikacją, w tym:
- zagrożenia specyficzne dla procesu (np. temperatura, części wyrzucane, odpryski spawalnicze);
- ograniczenia spowodowane obowiązkowym stosowaniem środków ochrony indywidualnej;
- wady projektu pod względem ergonomii (np. skutkujące utratą uwagi, nieprawidłową obsługą).
W porozumieniu z użytkownikiem integrator powinien zidentyfikować i udokumentować zadania związane z komórką robota. Należy ustalić wszystkie racjonalnie przewidywalne kombinacje zadań i zagrożeń. Zadania oparte na współpracy można scharakteryzować przez:
- częstotliwość i czas przebywania operatora we wspólnym obszarze roboczym z ruchomym systemem robota (np. zespołowy montaż z zewnętrznymi mocowaniami);
- częstotliwość i czas trwania kontaktu operatora i systemu robota z mocą napędową lub źródłami energii czynnej związanymi z aplikacją (np. prowadzenie ręczne, fizyczna interakcja z narzędziem lub przedmiotem obrabianym);
- przejście z operacji niewspółpracujących do operacji opartych na współpracy;
- automatyczny lub ręczny restart ruchu systemu robota po zakończeniu współpracy;
- zadania obejmujące więcej niż jednego operatora;
–wszelkie dodatkowe zadania w ramach wspólnego obszaru roboczego.
Eliminacja zagrożeń i redukcja ryzyka robota współpracującego z człowiekiem
Po zidentyfikowaniu zagrożeń należy ocenić ryzyko związane z pracą systemu robotów współpracujących przed zastosowaniem środków zmniejszających ryzyko. Środki te są oparte na następujących podstawowych zasadach wg ISO 10218-2, wymienionych w kolejności ich obowiązywania:
- eliminacja zagrożeń na etapie projektowania za pomocą rozwiązań konstrukcyjnych bezpiecznych samych w sobie (eliminowanie, zastępowanie);
- stosowanie technicznych środków ochronnych (np. osłony) w celu zapobiegania przed kontaktem operatora z zagrożeniami lub kontrolowanie zagrożeń poprzez osiągnięcie bezpiecznego stanu (np. zatrzymanie, ograniczenie siły, ograniczenie prędkości), zanim operator będzie mógł uzyskać dostęp do zagrożeń lub być na nie narażony;
- zapewnienie uzupełniających środków ochronnych, takich jak informacje dotyczące użytkowania, szkolenia, znaki, sprzęt ochrony osobistej itp.
W przypadku tradycyjnych systemów robotów redukcja ryzyka jest zwykle osiągana dzięki zabezpieczeniom oddzielającym operatora od systemu robota. W ramach współpracy zespołowej redukcja ryzyka dotyczy natomiast przede wszystkim projektu i zastosowania systemu robota oraz wspólnego obszaru roboczego.
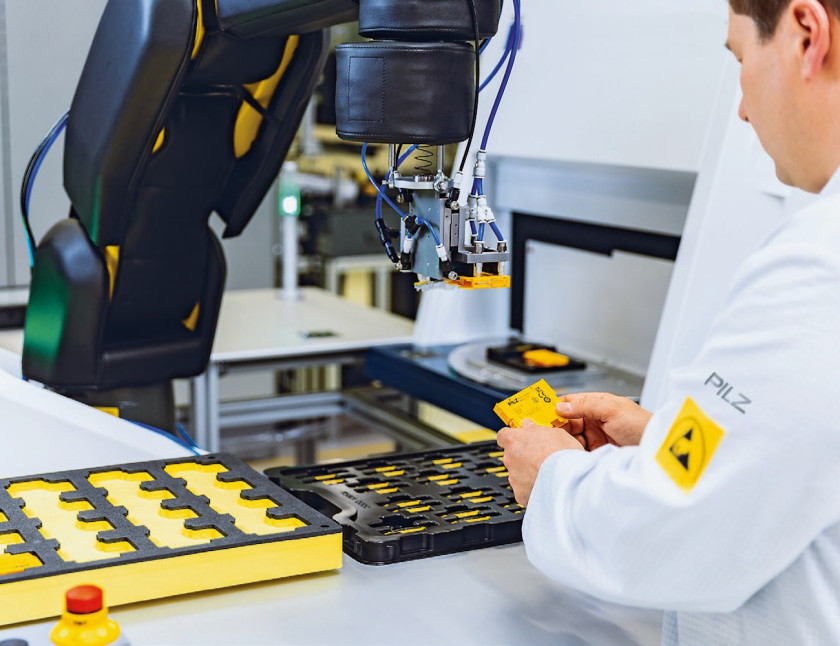
Ocena ryzyka dla stanowiska zrobotyzowanego, w którym współdzielimy obszar pracy z robotem, wymaga zatem indywidualnego podejścia do szacowania i zmniejszania tego ryzyka, biorąc pod uwagę zadania, jakie są wykonywane przez człowieka. Robot jest tylko narzędziem, które pomaga w podejmowaniu precyzyjnych lub monotonnych czynności, ale człowiek musi czerpać z tej współpracy korzyści. W dzisiejszych czasach w wyniku niedoskonałości technologicznych wciąż jesteśmy zmuszeni do stosowania zasad ograniczonego zaufania, więc współpraca maszyn z ludźmi stanowi wciąż rozwijaną technologię, mającą swoje ograniczenia. Nie we wszystkich obszarach owa współpraca jest możliwa lub nakłada takie ograniczenia, które powodują, że nie przynosi ona oczekiwanych korzyści – ze względu na spowolnienie produkcji, niedokładność lub ludzką frustrację z powodu występowania wad kolaboracyjnych. Po kilku latach funkcjonowania tej technologii często można dowiedzieć się z przekazów medialnych o nietrafionych inwestycjach, które wynikają z marketingowych ambicji kreowania "fabryk przyszłości". Czas pokazał, że projektowanie systemu kolaboracyjnego to proces wymagający kompleksowego podejścia do zadań i redukcji zagrożeń.
Andrzej Kowalski Certified Machinery Safety Expert
Pilz Polska
tel. 22 884 71 00
info@pilz.pl, www.pilz.pl