Wzrost wydajności i sposoby reagowania
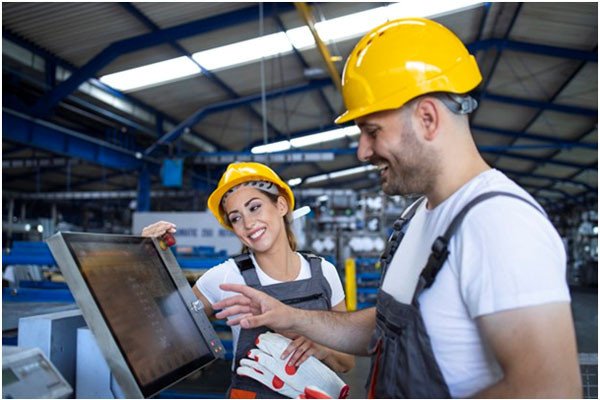
Przed kierownikami i inżynierami produkcji nieustannie stawiane są zadania zwiększania wydajności i maksymalizacji zwrotu z inwestycji (ROI) w zakresie wykorzystywanych urządzeń i zasobów ludzkich. Wzrastają wymagania w zakresie zgodności z przepisami oraz standardów jakości, przy jednoczesnym wzroście liczby urządzeń do zarządzania, raportów do wykonania, oraz wzroście poziomu nadzoru nad przezbrojeniem linii.
Istnieją różne strategie reagowania na te wyzwania związane ze wzrostem wydajności:
- doskonalenie istniejącej infrastruktury lub procesów,
- inwestycje w nowe linie lub wynajem od podwykonawców,
- zatrudnienie większej liczby osób,
- zwiększenie liczby linii produkcyjnych z różnym poziomem ryzyka czy kompromisu.
Pierwsza z opcji jest często najlepsza pod warunkiem, że dysponujemy danymi, które pozwolą wdrożyć odpowiednie zmiany. Krótko mówiąc, trudno jest usprawnić proces, którego nie jesteśmy w stanie zmierzyć.
W takich przypadkach narzędzie OEE może okazać się pomocne, poprzez precyzyjne monitorowanie produkcji w czasie rzeczywistym, jak również uzyskanie historycznych danych na temat głównych przyczyn strat produkcji. Dzięki rozpoznaniu głównych przyczyn przestoju lub obniżenia jakości, można podjąć działania naprawcze, uzgodnić priorytety i monitorować efektywność.
Czym jest OEE, czyli definicja Całkowitej Efektywności Maszyn
Definicja OEE – Całkowita Efektywność MaszynStandardowa metoda pomiaru produktywności linii obejmuje 3 kluczowe wskaźniki poziomu wykonania (KPIs) odnoszące się do trzech pytań: ![]() |
Poznaj 3 kroki wdrożenia narzędzi OEE
Najbardziej skuteczni przedsiębiorcy osiągają wydajność OEE na poziomie 85%, dzięki wprowadzaniu stopniowych modyfikacji. Przeciętny poziom OEE przed wdrożeniem zmiany to około 50-60%.
Przedstawiamy trzy kluczowe kroki wdrożenia narzędzi OEE, od koncepcji do testów na pierwszej wybranej linii produkcyjnej.
1. Diagnoza
Sprecyzowanie potrzeb oraz celu są kluczowe przy wyborze metody monitorowania odpowiedniej dla danego profilu biznesu. Należy wziąć pod uwagę jakość danych, wskaźnik ROI, horyzont czasowy, budżet oraz gotowość do podjęcia ryzyka. Ręczne rozwiązanie OEE, takie jak na przykład wypełnianie formularzy przez operatorów jest niedrogie i łatwe we wdrożeniu, jednakże uzyskane dane nie zawsze są wiarygodne i nie można ich konsolidować. Operatorzy są zbyt zajęci czynnościami związanymi z produkcją i ryzyko nieprawidłowego wypełniania formularzy jest wysokie.
Wdrożenie, zaprojektowanie, dostosowanie do indywidualnych potrzeb wyrafinowanych rozwiązań OEE, dostarczane przez specjalistów w zakresie automatyzacji, może zająć lata lub miesiące i kosztować setki tysięcy euro oraz wymagać wstrzymania produkcji na dłuższy czas. Takie podejście jest uzasadnione w przypadku bardzo wydajnych linii i drogich produktów.
Dla fabryki z branży FMCG, jak na przykład zakładu produkującego żywność z 5 liniami, przy wydajności od 10 do 300 produktów na minutę, przy niskiej i średniej marży lepiej będzie zdecydować się na standardowe rozwiązanie OEE, które może zostać wdrożone w ciągu kilku dni, a wskaźnik ROI będzie poniżej 1 roku. Zapewni ono wystarczający dostęp do danych, by wprowadzać stopniowe modyfikacje z niewielkim ryzykiem, bez większych zakłóceń w codziennej produkcji. Implementacja podstawowego, niedrogiego rozwiązania, łatwego w dalszej rozbudowie odpowiada na potrzeby takich firm.
Po podjęciu decyzji o wyborze gotowego rozwiązania zarządzający muszą zdecydować, jaki zakres zmiany i w jakim obszarze przyniesie największe korzyści. Istnieją dwie opcje do rozważenia:
- Linia poniżej wydajności, wytwarzająca produkty krytyczne, ale nie osiągająca oczekiwanych poziomów (tzw. gwiazda). ROI jest tutaj zazwyczaj najszybszy.
- Linia problematyczna, generująca tak wiele problemów, że nie wiadomo od jakich modyfikacji zacząć. Tutaj najbardziej przydatne będzie narzędzie OEE do zdiagnozowania sytuacji. Należy również określić poziom oczekiwań. Standardowe narzędzia OEE mogą zapewnić 10-15% podniesienia efektywności w ciągu 12 miesięcy od wdrożenia działań naprawczych. Lepsze efekty można uzyskać przy wyższych poziomach nakładów inwestycyjnych. Firma Markem-Imaje, oferuje kalkulator ROI pomocny przy ocenie obszarów usprawnień przy pomocy oprogramowania OEE.
2. Plan
Po wyborze narzędzia OEE oraz linii produkcyjnej wspólnie z kluczowymi osobami zaangażowanymi w proces należy opracować plan działania zgodny z wyżej opisanymi celami. Zwykle są to osoby zarządzające produkcją z działów utrzymania ruchu, inżynieryjnego i jakości. Pierwsze dwie są szczególnie ważne, ponieważ często występuje naturalne tarcie między nimi. Poprzez zademonstrowanie, w jaki sposób narzędzie OEE może umożliwić dostęp do obiektywnych danych na temat problemów z linią produkcyjną, można doprowadzić do współpracy w celu znalezienia efektywnego rozwiązania.
Warto również wyznaczyć lidera procesu OEE, który będzie czuwał nad wdrożeniem. Taka osoba powinna być w 100% zaangażowana w proces i może wywodzić się z powyższych działów, jednakże bez zaangażowania wszystkich stron w proces, istnieje ryzyko wielu frustracji i straty czasu.
3. Budowa
Na szkolenie operatorów należy przeznaczyć co najmniej jeden tydzień, ponieważ ważne jest, by pracownicy wszystkich zmian zrozumieli, w jaki sposób wdrożenie narzędzi OEE ułatwi im pracę. Bez ich przekonania, by sumiennie wpisywać dane w wyskakujące okienka z pytaniem o powód przestoju, otrzymane statystyki będą nierzetelne i niewystarczające do wdrożenia optymalnych rozwiązań. Problem ten jednak może zostać rozwiązany za pomocą automatycznych procedur zbierania danych, pod warunkiem dostępności danej funkcjonalności w wybranym narzędziu.
Po przeprowadzeniu szkolenia dane powinny zostać zebrane w ciągu tygodnia, a następnie przeanalizowane wspólnie z dostawcą OEE w celu zidentyfikowania ewentualnych niezgodności i dostrojenia konfiguracji.
Po ostatecznym skonfigurowaniu narzędzia powinno ono zostać uruchomione na co najmniej jeden miesiąc, by uzyskać wiarygodny obraz sytuacji, ponieważ poziom OEE może zmieniać się każdego dnia w zależności od pracowników i zmiany. Wykresy wodospadowe wskazujące na obszary strat KPI w priorytetowych produkcjach, mogą wspomóc ustalenie priorytetów w oparciu o zakres oddziaływania, koszty oraz łatwość wdrożenia.
Po wprowadzeniu modyfikacji narzędzie OEE może monitorować jej skuteczność w zakresie poprawy kluczowych wskaźników produktywności KPIs. Wartość dodana powinna być zauważalna w czasie od 3 do 6 miesięcy. Zakres i tempo zmian zależy jednak od punktu startowego oraz zakresu podjętych inwestycji dla rozwiązania zidentyfikowanych problemów.
CoLOS® OEE – przykład wdrożeniaRozwiązanie CoLOS OEE zostało wdrożone na linii typu „gwiazda” w europejskiej fabryce. Narzędzie zidentyfikowało wiele krótkich zatrzymań linii, w związku z przepełnieniem na końcu transportera, któremu operatorzy nie byli w stanie poświęcić uwagi w związku z wykonywaniem innych istotnych zadań. Ręczne raportowanie OEE nie odzwierciedlało rzeczywistej skali problemu. Ze względu na to, że zatrzymania były krótkie (2-3 minuty) i było sporo innych obowiązków do wykonania, ignorowali oni problem lub czekali do końca swojej zmiany z wypełnieniem formularzy, w których pomijali kluczowe detale. ![]() Narzędzie OEE na bieżąco rejestrowało zatrzymania i wykazało, że w ciągu jednej zmiany łączny czas zatrzymań produkcji to minimum 20 minut. Posiłkując się tymi danymi, zespół inżynierów produkcji zdołał przekonać Zarząd do inwestycji 80,000 € w celu poprawy efektywności. Wskaźnik ROI wyniósł 4 miesiące, a w tym okresie wskaźnik OEE wzrósł o 5%. Rozwiązanie zostało wdrożone również w pozostałych zakładach firmy zlokalizowanych w innych krajach. Operatorzy linii docenili wdrożone rozwiązanie, ponieważ pozwoliło im na wykonywanie innych obowiązków, na które do tej pory nie mieli czasu (np. wykonywanie raportów w zakresie monitorowania. Operatorzy linii docenili wdrożone rozwiązanie, ponieważ pozwoliło im na wykonywanie innych obowiązków, na które do tej pory nie mieli czasu (np. wykonywanie raportów w zakresie monitorowania. Osoby zarządzające daną linią również posługują się statystykami OEE podczas cotygodniowych spotkań ze swoim zespołem. ![]() |
Wdrożenie narzędzi OEE — korzyści
Podejście 3 kroków ogranicza ryzyko i demonstruje zalety monitorowania OEE na pierwszej, testowej linii, zanim wdrożymy rozwiązanie na szeroką skalę w całym zakładzie.
Menadżerowie otrzymują niezbędne informacje, aby ustalić priorytety i monitorować postępy. Takie podejście może również przekonać lokalne zespoły do podejmowania wysiłków w kierunku ciągłego doskonalenia. Ponadto operatorzy linii doceniają omówione wyżej rozwiązanie OEE, które zwalnia ich z ręcznego raportowania. Wydajność produkcji stopniowo wzrasta, zgodnie z zasadami doskonalenia procesów produkcyjnych, przy większym poziomie zaufania i mniejszym wysiłku.
Zobacz wideo i przekonaj się, jak wdrożenie narzędzi pomiaru wpływa na wzrost OEE!
Źródło: Markem-Imaje
CoLOS® firmy Markem-Imaje to modułowa platforma softwarowa, która umożliwia pełną integrację urządzeń z innymi systemami informatycznymi w zakładzie; zawiera elastyczne narzędzia konfiguracyjne uwzględniające specyficzne potrzeby biznesowe użytkownika.
Markem-Imaje oferuje szeroką gamę urządzeń do znakowania i etykietowania produktów, od drukarek ink jet niskiej i wysokiej rozdzielczości, datowników termotransferowych, laserów, do urządzeń do nakładania i druku etykiet. Coleman International Sp. z o.o. jest dystrybutorem firmy Markem-Imaje w Polsce. Więcej na https://coleman.pl Zobacz film o CoLOS® tutaj. |
Źródło: Coleman International Sp. z o.o.