Jakość energii elektrycznej a zużycie mediów i żywotność urządzeń
Jednym z ważniejszych czynników wpływających na wysokość kosztów zużycia energii elektrycznej jest jej jakość, rozumiana jako zbiór parametrów charakteryzujących napięcie zasilające oraz opisujących ciągłość zasilania odbiorcy.
Jakość energii elektrycznej dostarczanej do systemów automatyki i sterowania ma ponadto znaczący wpływ na żywotność urządzeń oraz niezawodność ich pracy. Usunięcie problemów związanych ze spadkami napięcia, chwilowymi skokami czy przepięciami, jak również kwestiami dotyczącymi wyższych harmonicznych prądów oraz napięć może znacząco poprawić OEE (Overall Equipment Effectiveness), czyli całkowitą efektywność wyposażenia przez zapewnienie większej dostępności urządzeń do produkcji.
Wpływ urządzeń na jakość energii elektrycznej
Za jakość energii elektrycznej odpowiadają nie tylko jej dostawcy, ale także odbiorcy. Mają na to bowiem wpływ eksploatowane w firmach produkcyjnych odbiorniki elektryczne, mogące przyczyniać się do pogarszania jakości energii w obrębie danego zakładu.
Na jakość tę po stronie odbiorcy wpływają przede wszystkim:
a) zapady napięcia zasilającego
- zjawisko występujące w sytuacji, kiedy wartość skuteczna napięcia zasilającego spada poniżej 90% wartości napięcia znamionowego w czasie 10‒60 ms. Głównymi źródłami tego typu zaburzeń są zwarcia w sieci zasilającej oraz załączanie odbiorników dużej mocy. Zjawiska te negatywnie wpływają na pracę odbiorników energii elektrycznej, powodując:
- zmniejszenie prędkości obrotowej silników, a co za tym idzie – spowolnienie procesów produkcyjnych,
- przyspieszenie procesu nagrzewania się torów zasilających, przyczyniając się do szybszego starzenia się ich izolacji,
- niedoładowywanie szyn DC przemienników wykorzystywanych w układach napędowych
- zmiany momentów silników, mogące powodować ich utyk,
- zmiany sił w elektromagnesach, wpływające na stany styczników/przekaźników,
- zmiany natężenia oświetlenia;
b) wyższe harmoniczne prądu oraz napięcia – to jedne z najczęściej występujących zaburzeń wprowadzanych do sieci energetycznej poprzez m.in. układy napędowe o regulowanej prędkości obrotowej, wykorzystujące przemienniki częstotliwości/serwonapędy, układy podtrzymania zasilania typu UPS, zasilacze DC urządzeń elektronicznych, oświetlenie energooszczędne, silniki czy transformatory. Zjawiska te powodują:
- przegrzewanie się przewodów neutralnych,
- problemy (przeciążenia/rezonanse) związane z układami kompensacji mocy biernej,
- wzrost rezystancji przewodów,
- nadmierne grzanie oraz wibracje silników elektrycznych,
- konieczność przewymiarowania transformatorów.
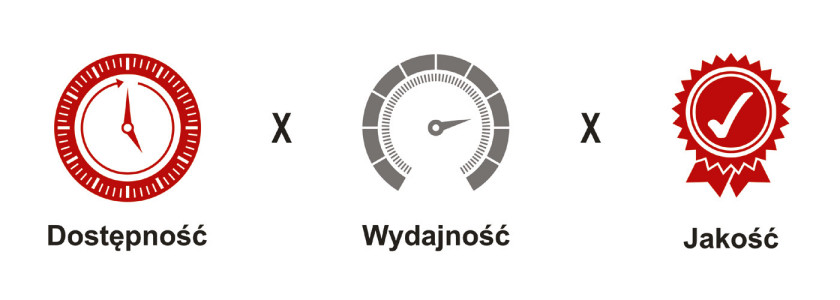
Trzy kroki do poprawy jakości zasilania
Chcąc optymalizować zużycie energii elektrycznej w zakładzie produkcyjnym, warto skupić się na takich zagadnieniach, jak:
- monitorowanie zaburzeń sieci,
- analiza danych i optymalizacja zużycia,
- ograniczenie zaburzeń sieci.
Monitorowanie zaburzeń sieci
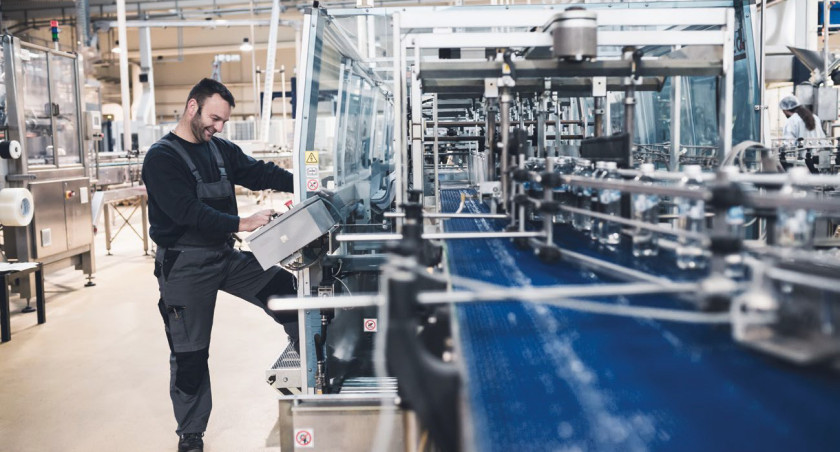
Bieżące monitorowanie sieci zasilającej pozwala na szybką identyfikację zaburzeń i w efekcie – sprawniejszą ich eliminację. Na rynku znajdziemy urządzenia umożliwiające przeprowadzenie szybkiej analizy sieci zasilającej, jak również bardziej zaawansowane produkty służące do monitorowania, pomiaru oraz automatycznej detekcji zaburzeń zaawansowanych parametrów energii elektrycznej.
Analiza danych i optymalizacja zużycia
Analiza parametrów sieci zasilającej pomaga optymalizować zużycie energii i lepiej zarządzać kosztami mediów w zakładzie produkcyjnym.
Decydując się na zakup oprogramowania do interpretacji oraz zarządzania danymi pomiarowymi, warto szukać rozwiązań, które:
- umożliwią wymianę danych w czasie rzeczywistym,
- pozwolą na szybką wizualizację i analizę konkretnych parametrów,
- będą intuicyjne w obsłudze,
- pozwolą na wskazanie konkretnego odbioru/odbiorów stanowiących problem,
- pozwolą tworzyć prognozy energetyczne bazujące na danych historycznych.
Ograniczenie zaburzeń sieci
Silniki są podstawowym źródłem energii mechanicznej dla maszyn, zużywającym nawet do 70% energii w zakładach przemysłowych. Optymalizacja pracy układów napędowych może zatem znacząco obniżyć koszty zużycia mediów w przedsiębiorstwie. Jednym ze sposobów na zwiększenie efektywności energetycznej układów jest przeciwdziałanie problemom związanym z występowaniem zaburzeń sieci zasilającej – takich jak wspomniane wcześniej wyższe harmoniczne – poprzez zastosowanie napędów niewpływających negatywnie na sieć zasilającą (konstrukcja typu AFE).
Ograniczając zaburzenia sieci, przeciwdziałamy także przegrzewaniu się przewodów neutralnych, nadmiernemu grzaniu oraz wibracjom silników elektrycznych czy problemom związanym z układami kompensacji mocy biernej, takim jak przeciążenia czy rezonanse.
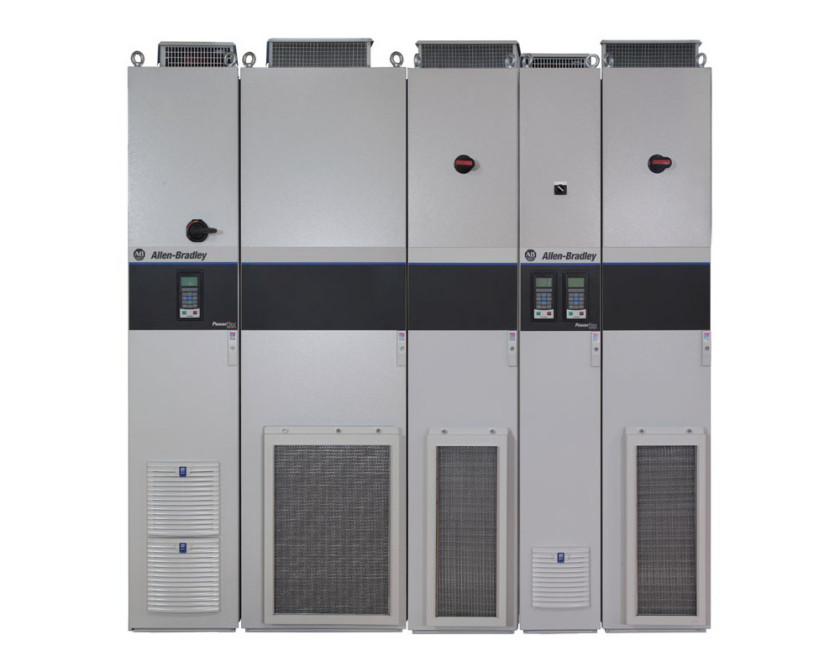
Dlaczego warto optymalizować zużycie energii elektrycznej?
Poprawa efektywności energetycznej może pozytywnie wpłynąć zarówno na wielkość zużycia energii i obniżenie kosztów eksploatacyjnych, jak również na zwiększenie niezawodności urządzeń i wydajności produkcji. Poprawę tę warto rozważyć nie tylko w sektorach szczególnie energochłonnych, ale w każdym przedsiębiorstwie poszukującym oszczędności w procesie produkcyjnym. Zwiększając efektywność energetyczną, redukujemy wpływ naszej działalności na środowisko naturalne, stajemy się bardziej odporni na wahania cen energii elektrycznej i w efekcie zwiększamy naszą konkurencyjność na rynku.
Serdecznie zapraszamy do kontaktu. Z przyjemnością doradzimy Państwu, w jaki sposób poprawić efektywność energetyczną w Państwa przedsiębiorstwie.
Tomasz Depta
Kierownik Rozwoju Grupy Produktów – Systemy Napędowe i Komponenty Elektryczne
tdepta@racontrols.pl