Dla użytkowników końcowych odpowiedzialnych za konserwację i utrzymanie ruchu maszyn sprawa jest prosta. System IIoT dostarcza dane z maszyny, zapewniając, że jej systemy lub komponenty pracują w normalnym zakresie. W tym kontekście to użytkownicy końcowi naciskają na wdrożenie IIoT.
Sytuacja wygląda często inaczej w przypadku konstruktorów maszyn. Mogą oni mieć wielu klientów, którzy nalegają na wdrożenie rozwiązań IIoT, więc producenci OEM pytają: "Jak tego dokonać? Kto ma odpowiedni produkt, aby to zrealizować? Co powinniśmy monitorować?".
Instalacje pneumatyczne już od pewnego czasu korzystają z funkcji diagnostycznych. Możemy np. sprawdzić, czy pobór mocy nie jest zbyt niski lub zbyt wysoki, albo czy w układzie We/Wy doszło do zwarcia, które stało się przyczyną awarii.
Teraz idziemy o krok dalej, wprowadzając czujniki i opcję wykorzystania układów We/Wy do przechwytywania danych o wydajności komponentów. Najczęściej wywołuje to jednak pytania typu: "Mam te wszystkie dane, ale co one znaczą? Jak je zmienić w przydatne informacje?".
Ze zmagań rodzą się wyzwania – i możliwości
Uwagę skupia się więc teraz na sposobie, w jaki użytkownicy końcowi przekształcają otrzymywane dane w przydatne informacje i reagują na awarie lub nawet je przewidują. Przykładowo, programowalny czujnik firmy Emerson marki AVENTICS serii ST4-2P od lat jest dostępny w naszej ofercie produktów. Mierzy drogę i prędkość przesuwu siłowników pneumatycznych. Możemy mierzyć prędkość tłoka w siłowniku, ale jesteśmy w stanie również wykorzystać dane z czujników do monitorowania działania amortyzatorów końcowych i amortyzatorów wewnątrz siłownika. Zapewnia to ich działanie w określonym zakresie specyfikacji. Interpretacja tych danych pozwala się upewnić, czy siłownik działa zgodnie z oczekiwaniami, i szybko stwierdzić, czy wymaga konserwacji.
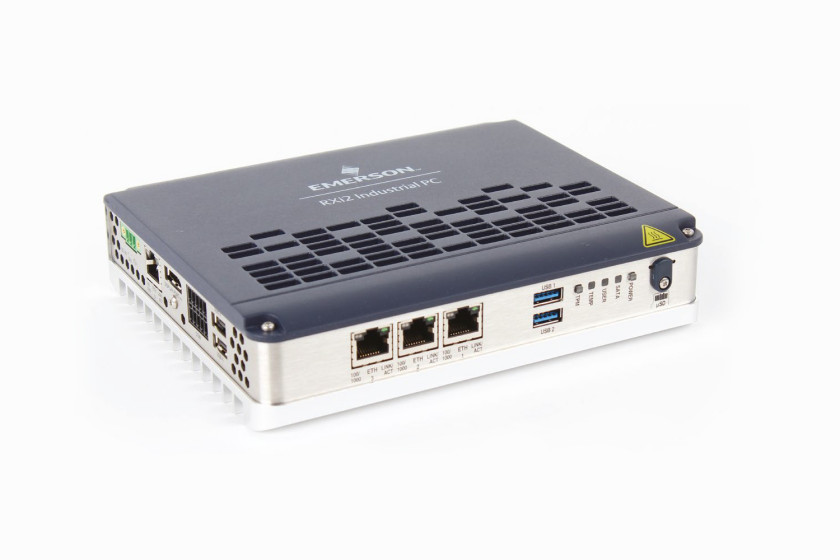
Dane można analizować przy użyciu komputera przemysłowego (IPC) Emerson RXi2-LP Edge Gateway, który pozwala na uruchamianie aplikacji HMI, aplikacji historycznych i analitycznych bezpośrednio na maszynie. Zapewnia to lepszą kontrolę operacji w czasie rzeczywistym oraz lepszą integrację z systemami w obrębie maszyny.
Przyjrzyjmy się np. zużyciu energii. Można zmierzyć ciśnienie powietrza przepływającego do układu, zmierzyć przepływ i zestawić uzyskany wynik ze zdarzeniem, a także stwierdzić, że po włączeniu danego zaworu uzyska się określony przepływ. Jeżeli przy następnym włączeniu zaworu przepływ się zmieni, oznacza to, że system nie działa prawidłowo. Możliwe, że przewód pneumatyczny wypadł lub uszczelnienia w siłowniku się zużyły.
Co innego jednak wiedzieć, że coś jest nie tak, a co innego umieć zrobić użytek z tego rodzaju informacji. Konstruktorzy maszyn szukają sposobów na wykorzystanie możliwości IIoT.
Odpowiedzialność za rozwiązanie problemów wykrytych na podstawie tych danych spoczywa zarówno na producentach OEM, jak i na producencie komponentów. Nasze podejście do IIoT nie opiera się na zasadzie „IIoT w pigułce”. Rozumiemy, że sukces wymaga również współpracy i wsparcia. Najczęściej producenci OEM i użytkownicy końcowi chcieliby dodatkowego monitorowania, aby mieć pewność, że kontrola ich procesów maszynowych przebiega prawidłowo. Jesteśmy w stanie współpracować z producentem OEM w celu opracowania takiej architektury IIoT, która zapewni, że na miejscu zostaną zamontowane odpowiednie czujniki, prawidłowo odczytujące sygnały, co pomoże utrzymać pracę maszyny w pełnym wymiarze czasu. Takie rozwiązanie maksymalizuje zwrot z inwestycji dla użytkownika końcowego, przez obniżenie całkowitego kosztu posiadania maszyny (TCO, Total Cost of Ownership).
Eksperci IT już na wczesnym etapie
Znajomość koncepcji wyższego poziomu analizy i udostępniania danych wśród klientów jest coraz wyższa. Co ważniejsze, zależy to od tego, z kim toczą się rozmowy na etapie projektowania maszyny. W przeszłości, podczas wspólnych prac z projektantami maszyn, omawialiśmy takie kwestie, jak zasilanie i przyłącze powietrza. Teraz rozmowy muszą również uwzględniać zagadnienia tego rodzaju, jak połączenia sieciowe, bezpieczeństwo, a także połączenia VPN.
Obecnie bardziej niż kiedykolwiek wcześniej ważne jest, aby włączyć dział IT w struktury projektu i omówić z nim, jak wyglądają te połączenia i jak przemieszczają się dane. Kwestie bezpieczeństwa są również ważne, zwłaszcza dla użytkowników końcowych, dlatego specjalistów IT należy zaangażować już na wczesnym etapie projektowania, aby uwzględnić takie czynniki, jak ilość przetwarzanych danych, miejsce ich przesyłania i sposób połączenia.
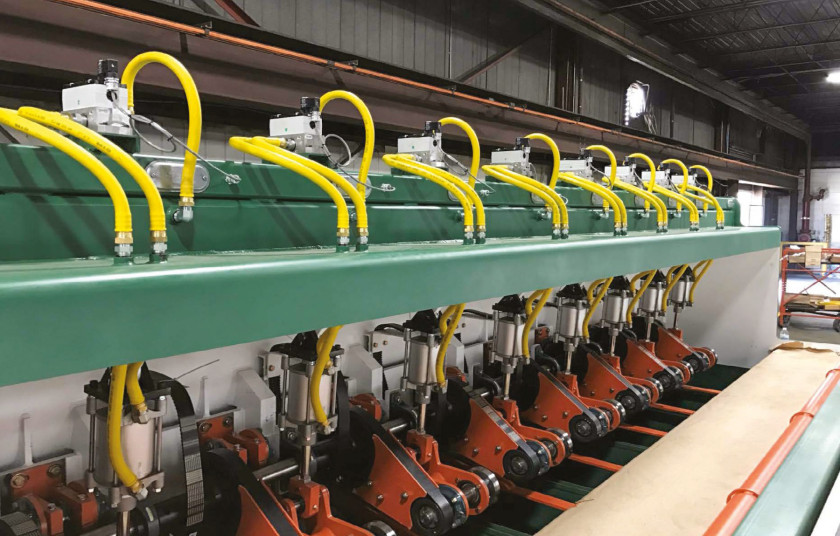
Wykorzystanie partnerstwa do sukcesu IIoT
Producenci komponentów do wyposażenia maszyn muszą ze sobą współpracować, aby zrozumieć, jaką rolę zaczynają odgrywać inteligentne instalacje pneumatyczne – chodzi o stworzenie prawdziwego partnerstwa, które pozwoli opracować dla klientów najlepsze rozwiązania IIoT. Na poziomie maszyn instalacje pneumatyczne, napędy, sterowniki i układy We/Wy muszą ze sobą współgrać. Kluczem jest wiedza na temat tego, w jaki sposób między tymi elementami przemieszczają się dane, i pewność, że docierają one tam, gdzie powinny – czy to lokalnie na serwer internetowy, czy do systemu w chmurze.
Spójrzmy ponownie na przykład zużycia energii: najlepszym sposobem uzyskania oszczędności energii jest wyłączenie sprężarki. Mimo że nie produkujemy sprężarek ani systemów sterowania do sprężarek, dzięki inteligentnej instalacji pneumatycznej możemy poinformować system sterowania sprężarki, jakie wystąpi zapotrzebowanie na powietrze w ciągu najbliższych 12 godzin. Na tej podstawie będzie on w stanie w odpowiednim momencie wyłączyć sprężarkę, ponieważ może ona nie potrzebować całego powietrza. Jest to tylko jeden z przykładów komponentów i systemów „rozmawiających” ze sobą w celu uzyskania oszczędności energii.
Połącz elementy, czyli o lepszą wydajność instalacji
Jak wszystkie te elementy wpływają na poprawę sytuacji producenta?
Jedną z wizji, do której dążymy, jest umożliwienie wysoce autonomicznego procesu konserwacji. Dla nas oznacza to, że obwód pneumatyczny, a tym samym maszyna, ma czas sprawności na poziomie 100% i nigdy nie ulega awarii. Oczywiście komponenty zużywają się; zawory i siłowniki przechodzą określone cykle eksploatacyjne i w końcu wymagają wymiany, ale dane umożliwiają przewidywanie awarii, zanim do niej dojdzie, a także zapobiegają kosztownym awariom całkowitym.
Jedna z aplikacji np. przewiduje spadek wydajności zaworów pneumatycznych. Opierając się o wzorzec cyklu okresu eksploatacji i jego kredyty B10, możemy wykorzystać te dane, aby określić, kiedy dany zawór osiągnie 75 milionów cykli i będzie wymagał wymiany. Operator otrzyma wówczas komunikat o przewidywanej awarii i jest w stanie wymienić zawór, zanim dojdzie do przerwania produkcji.
Dane z czujników pozwalają nam również przewidzieć, kiedy amortyzator na końcu siłownika ulega uszkodzeniu – przez wykrycie przyspieszenia cyklu, nawet o kilka milisekund. Mogłoby to wyzwolić alarm lub nawet wysłać dostawcy komponentów automatyczną wiadomość e-mail informującą o tym, że należy zakończyć konserwację lub że komponent jest gotowy do wymiany. System może też wygenerować zamówienie, a nowy komponent zostanie automatycznie dostarczony do klienta, dzięki czemu montaż da się zaplanować w taki sposób, aby zminimalizować wszelkie okresy przestoju w produkcji.
Dzięki właściwemu podejściu do technologii IIoT, na podstawie danych jesteśmy w stanie uzyskać użyteczne informacje, które pomogą zapewnić samoczynną diagnostykę maszyn, przejrzystość dla użytkowników końcowych oraz bezawaryjność.
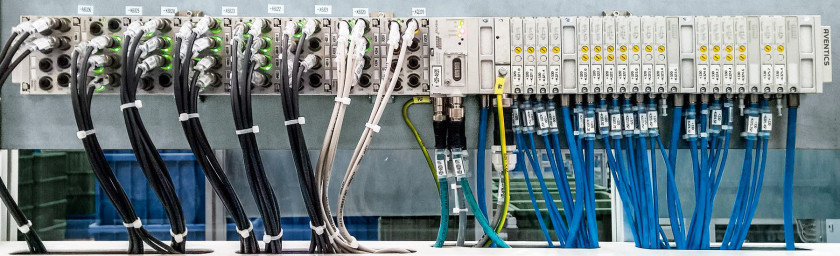
Marek Szymański, Specjalista Sprzedaży ds. Automatyki, Machine Automation Solutions w Emerson
Emerson
www.emerson.com/pl-pl