Co brać pod uwagę, projektując system odpylania przemysłowego?
Projektując układ, należy uwzględnić kilka czynników. Pierwsze z nich to wilgotność oraz lepkość pyłu. Są one uzależnione od tego, w jaki sposób wygląda proces obróbki drewna w danym zakładzie.
By nie przerywać ciągłości pracy, układ odpylania musi realizować także automatyczne zbijanie pyłu z mat filtracyjnych. Efekt? Oczyszczone powietrze pozbawione pyłu drzewnego, które ponownie powraca do hali produkcyjnej.
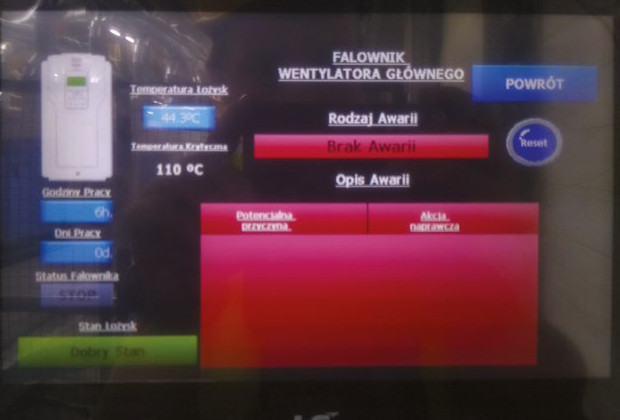
Ponadto system powinien być wyposażony w odpowiedni układ sterowania, aby spełniał wymagania technologiczne przy jednoczesnej efektywności energetycznej, a dodatkowo nie wymagał częstych wymian wkładów filtracyjnych.
Konieczne jest także utrzymanie stałego podciśnienia w układzie, a wentylatory wyciągowe muszą załączać się w zależności od tego, ile maszyn pracuje w danej chwili w zakładzie. Można to osiągnąć m.in. dzięki zastosowaniu przemienników częstotliwości.
Jakie elementy automatyki powinien zawierać układ?
Przemienniki częstotliwości sterują pompami oraz wentylatorami m.in. w instalacjach wentylacyjnych, układach oddymiania czy omawianych tu systemach odpylania.
Przyjrzyjmy się bliżej przykładowi aplikacji sterowania układem filtra produkowanego przez firmę Nawara Serwis (www.nawaraserwis.pl).
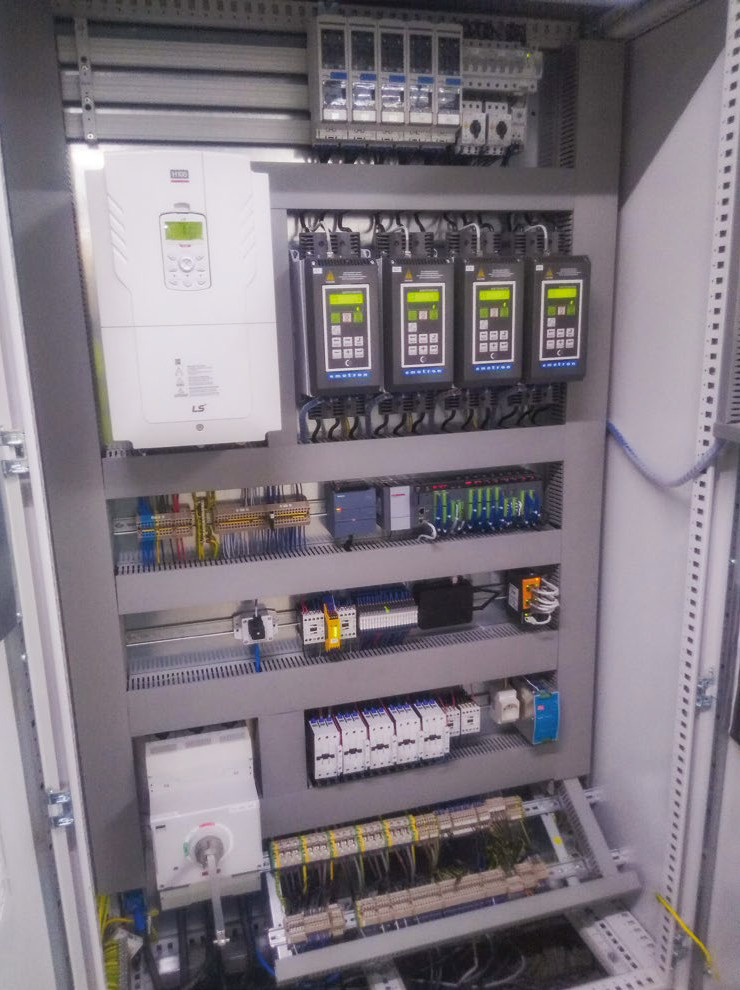
Podciśnienie w układzie zapewnia tu wentylator główny, sterowany za pomocą przemiennika częstotliwości LS Electric serii H100 (produkowanego w zakresie mocy 0,75‒500 kW).
Przemiennik, bazując na sygnale z czujnika ciśnienia oraz w oparciu o wbudowany regulator PID, odpowiednio reguluje prędkość obrotową silnika.
Ma on duże możliwości konfiguracji, dzięki czemu bardzo dobrze sprawdza się zarówno w prostych, jak i bardziej rozbudowanych układach HVAC. Użytkownik ma do wyboru m.in. poniższe funkcje:
- specjalne makra aplikacyjne (takie jak wentylator, wentylator wyciągowy, pompa cyrkulacyjna, pompa, wieża chłodnicza, kompresor, stały moment);
- rozbudowany regulator PID: procesowy PID z obsługą dwóch sygnałów PID zewnętrznych, a także funkcji sleep, sleep boost, wake up, 39 jednostek fizycznych regulacji;
- tryb pożarowy: po otrzymaniu sygnału z czujnika PPOŻ przemiennik rozpoczyna pracę i ignoruje większość błędów aż do momentu uszkodzenia lub zdjęcia sygnału PPOŻ;
- wbudowany zegar czasu rzeczywistego: możliwość tworzenia harmonogramów pracy (8 harmonogramów, 4 przedziały czasowe, 8 wątków z wyjątkiem daty, 30 funkcji działania);
- sterowanie wielosilnikowe (kaskadowe);
- wykrywanie uszkodzenia rury, czyszczenie pompy, miękkie wypełnianie itp.
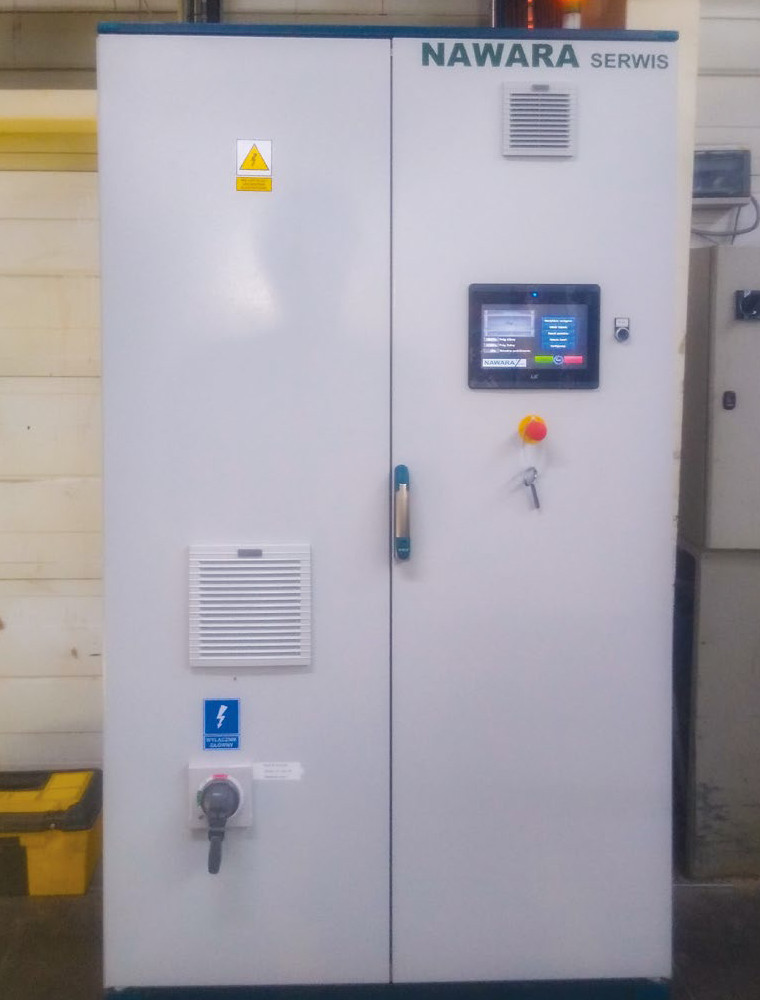
Wróćmy jednak do omawiania gotowego układu. W przypadku uruchamiania kolejnych maszyn w hali produkcyjnej pojawia się potrzeba odprowadzania większej ilości pyłu. Problem ten został rozwiązany dzięki kaskadowemu załączaniu kolejnych wentylatorów, sterowanych za pomocą softstartów marki CG (do 16 wentylatorów dodatkowych). Za każdym razem po dołączeniu kolejnych wentylatorów przemiennik reguluje prędkość silnika głównego dla zapewnienia odpowiedniego podciśnienia.
Nad poprawną pracą całego układu czuwa sterownik PLC LS Electric, który steruje sekwencją załączania się wentylatorów dodatkowych i zlicza ich czas pracy dla równomiernego zużywania się napędów.
Wszelkie dane z softstartów dotyczące parametrów elektrycznych lub ewentualnych błędów pobierane są za pomocą komunikacji Modbus TCP do sterownika PLC, gdzie są zapisywane i w razie potrzeby wyświetlane na panelu operatorskim EXP marki LS Electric.
Układ mierzy również aktualny stan łożysk poprzez pomiar drgań i temperatury łożysk. Dane te wyświetlają się także na panelu operatorskim.
Aniro
www.aniro.pl