SoftPLC to sterownik PLC, który ma postać oprogramowania (aplikacji), uruchomionego na komputerze przemysłowym. Po co stosować takie rozwiązanie, zamiast po prostu wdrożyć „zwykły” sterownik? Można wymienić kilka powodów, dla których warto je rozważyć.
Możliwość zastosowania komputera przemysłowego w roli sterownika PLC przeanalizowaliśmy na przykładzie komputera Astraada PC, wykorzystującego oprogramowanie Codesys Runtime. W kolejnym artykule, na naszej stronie, pokazujemy, jak skonfigurować driver komunikacyjny protokołu EtherCAT dla jednej z dwóch kart sieciowych w Astraada PC.
Uruchomienie tego protokołu pozwala na zbudowanie aplikacji, w których jądrem systemu jest komputer przemysłowy, pełniący rolę jednostki centralnej, do której podłączamy urządzenia za pośrednictwem sieci EtherCAT. Poniższy przykład aplikacji Codesys demonstruje ruch osią SoftMotion z wykorzystaniem standardu PLCopen.
PC w roli PLC to większa wydajność i moc obliczeniowa
Po pierwsze, komputer przemysłowy zapewnia znacznie większą moc obliczeniową. Wydajność sterowników PLC nie jest porównywalna do wydajności komputerów, które wyposażone są w nowoczesne procesory i dużą ilość pamięci RAM. Nie ma to znaczenia w przypadku prostych programów sterujących, natomiast wszędzie tam, gdzie potrzebna jest duża moc obliczeniowa, komputer przemysłowy może okazać się znacznie lepszym rozwiązaniem. Ważne jest również to, że kod aplikacji w przypadku PC może być (częściowo lub nawet w całości) pisany w językach wysokiego poziomu (np. C lub C++), co dodatkowo zwiększa możliwości tworzenia programów realizujących nawet najbardziej skomplikowane zadania.
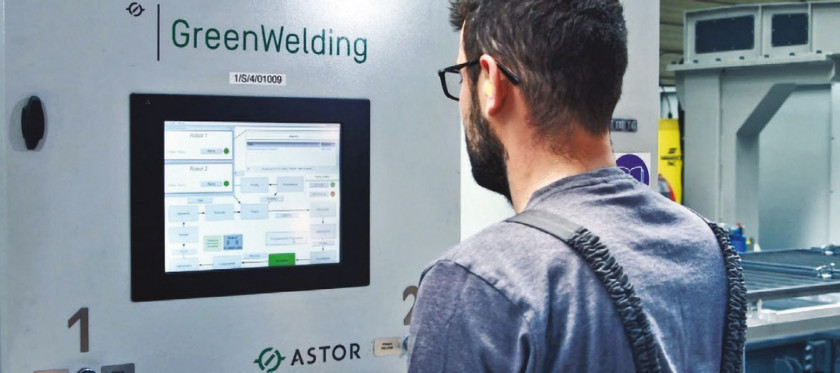
Rozbudowane możliwości komunikacyjne
Drugim uzasadnieniem dla zastosowania PC w roli PLC może być ułatwienie integracji w ramach bardziej rozbudowanego systemu. Komputer ma po prostu większe możliwości komunikacyjne. Jest to szczególnie widoczne, jeżeli komunikacja odbywa się z zastosowaniem protokołów wykorzystujących sieć Ethernet. Do komputera łatwo podpiąć różne oddalone urządzenia, w tym układy wejść/wyjść. Komputer przemysłowy ma zwykle dwie karty sieciowe i jest w stanie obsługiwać wszystkie popularne protokoły oparte na TCP/IP. Zapewnia to łatwy dostęp do wszystkich podpiętych urządzeń, a nawet opcję szybkiej konfiguracji każdego z nich. Równie łatwo da się połączyć taki komputer z innymi stacjami roboczymi, działającymi np. w ramach systemów informatycznych, takich jak MES czy ERP.
Komputer przemysłowy PC jako PLC zapewnia większą funkcjonalność
Komputer PC zastosowany w roli PLC umożliwia zintegrowanie w jednej aplikacji funkcjonalności, które dotąd były realizowane przez kilka osobnych urządzeń. Rozwiązanie takie pozwala aplikacji sterującej np. na bezpośredni dostęp do baz danych, zarządzanie recepturami, łatwe zapisywanie i odczytywanie plików, wizualizacje czy wysyłanie e-maili (np. alarmowych). Prostsza staje się też integracja z nadrzędnymi systemami informatycznymi (np. biznesowymi). Jeżeli nawet tego typu zadania da się zrealizować na PLC, to zazwyczaj jest to dużo trudniejsze, znacznie bardziej pracochłonne lub możliwe tylko w ograniczonym zakresie.
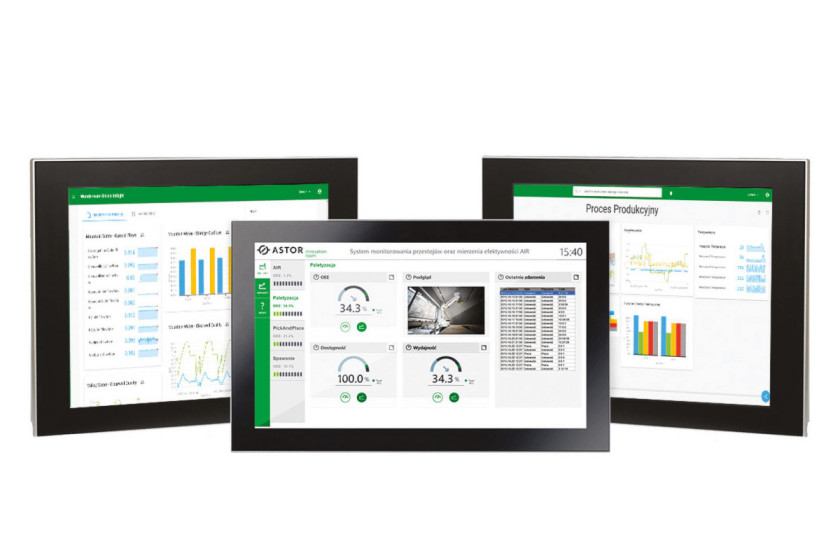
PC jako PLC - spojrzenie z drugiej strony
Skoro zastosowanie komputera PC w roli sterownika PLC ma tak istotne zalety, to można zapytać: w takim razie po co nam w ogóle PLC? Dlaczego nie sięgać po PC w każdej sytuacji?
Należy wyraźnie zaznaczyć, że komputer przemysłowy może realizować funkcję sterowania PLC, ale nie jest sterownikiem i nigdy nie będzie działał dokładnie tak samo, jak sterownik.
Po pierwsze, ze względu na wykorzystanie standardowego systemu operacyjnego rozwiązania SoftPLC wciąż nie są deterministyczne, w odróżnieniu od sterowników PLC, zapewniających deterministyczne działanie w czasie rzeczywistym. Właśnie z tego względu stosowanie PC w roli PLC ma wciąż wielu przeciwników. Oczywiście nie należy zapominać, że wydajność obecnych komputerów oraz niezawodność systemów operacyjnych jest dziś znacznie większa niż np. 20 lat temu. Wciąż jednak nie można powiedzieć, że nie ma pod tym względem różnicy między PC a PLC.
Po drugie, zastosowanie komputera w roli sterownika stawia zupełnie nowe wyzwania w zakresie zapewnienia bezpieczeństwa aplikacji. Ze względu na fakt, że nasz „sterownik” jest de facto komputerem, staje się on podatny na wszystkie wynikające z tego zagrożenia. Mówiąc w ogromnym uproszczeniu – do komputera znacznie łatwiej się włamać, niż ma to miejsce w przypadku PLC. Kwestii tej trzeba poświęcić wiele uwagi i zagwarantować odpowiedni poziom zabezpieczeń.
Po trzecie, komputer przemysłowy nie ma wbudowanych układów wejść/wyjść, co wymusza stosowanie zewnętrznych układów łączonych za pośrednictwem sieci przemysłowej. Sprawia to, że – szczególnie w mniejszych i mniej rozproszonych aplikacjach – sterownik, który może integrować moduły I/O w jednej obudowie, pozostaje najbardziej racjonalnym wyborem.
Co wybrać: PC czy PLC?
Odpowiedź na tak postawione pytanie jest bardzo prosta: to zależy. W wielu aplikacjach zastosowanie konwencjonalnego sterownika PLC pozostaje całkowicie wystarczające i ekonomicznie uzasadnione. Są też oczywiście takie aplikacje, w których PLC jest niezastąpiony z innych względów, np. wymagań związanych z deterministycznym działaniem lub łatwości zastosowania modułów wejść/wyjść. Gdy jednak zaczynamy odczuwać ograniczenia możliwości sterownika, np. w zakresie mocy obliczeniowej lub integracji z systemami informatycznymi, zastąpienie go komputerem przemysłowym jest rozwiązaniem, które warto brać pod uwagę i przemyśleć.
Zachęcamy do sprawdzenia oferty komputerów Astraada PC w naszym sklepie internetowym.
ASTOR
www.astor.com.pl