Wyzwanie
Zwiększenie wydajności procesu tłoczenia komponentów do nadwozia samochodu
W obecnych czasach firmy produkcyjne z branży motoryzacyjnej znajdują się pod znaczną presją globalnej konkurencji, dlatego nieustannie poszukują skutecznych sposobów optymalizacji produkcji oraz minimalizacji kosztownych przestojów. Jednym z kluczowych etapów procesu wytwórczego jest tłoczenie metalowych elementów nadwozia. Metalowe płyty są wtłaczane do specjalnych form, w których kształtuje się poszczególne części pojazdu. Tłoczenie jest jednym z kluczowych, ale też energochłonnych etapów w łańcuchu wytwórczym. Z jednej strony, stanowi podstawę jakości produktu końcowego. Z drugiej, awarie i opóźnienia mają daleko idące konsekwencje dla całego przepływu produkcji, a tym samym kosztów wytworzenia pojazdu.
Biorąc pod uwagę znaczenie procesu tłoczenia, duży producent z branży automotive poszukiwał skutecznego rozwiązania kwestii wykrywania anomalii w silnikach elektrycznych wykorzystywanych w maszynach pracujących w tłoczni.
Rozwiązanie
Centralne zbieranie wszystkich danych o pracy silnika elektrycznego i ich analiza z wykorzystaniem algorytmów uczenia maszynowego
W ramach rozwiązań dla cyfrowej fabryki (Digital Factory), firma Phoenix Contact oferuje kompleksową gamę produktów, rozwiązań, koncepcji i usług do digitalizacji zakładów produkcyjnych. Jednym z elementów tego portfolio jest rozwiązanie do uczenia maszynowego MLnext, które składa się z dwóch kluczowych komponentów programowych: MLnext Creation oraz MLnext Execution.
MLnext umożliwia proste i efektywne zastosowanie algorytmów uczenia maszynowego (ML) w cyfrowej fabryce. Korzystając z opcji wykrywania anomalii, producent elementów karoserii samochodów może teraz zidentyfikować potencjalne problemy z silnikami elektrycznymi służącymi do tłoczenia na wczesnym ich etapie i podjąć proaktywne działania, aby zminimalizować przestoje i zapewnić wysoką jakość produktu (fot. 1).
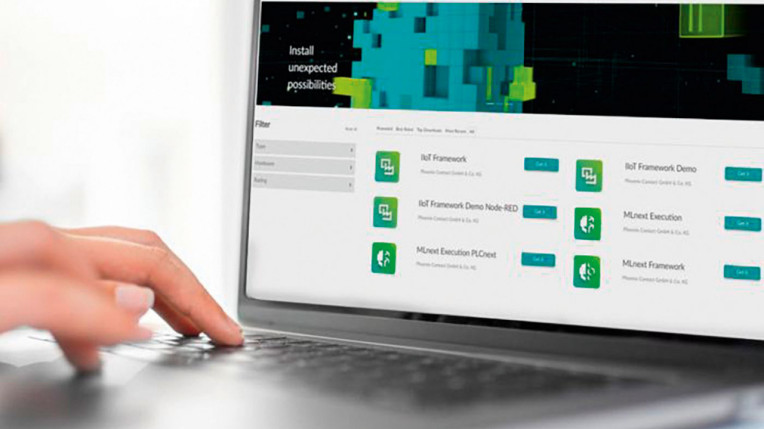
Pierwszym i najważniejszym krokiem w każdym projekcie uczenia maszynowego jest stworzenie bazy danych i punktu odniesienia. We wspomnianym zakładzie produkcyjnym dane z dwóch linii produkcyjnych – każda z czterema prasami z silnikami elektrycznymi – zostały zebrane w bazie danych dla każdej tłoczni. Do tego celu wykorzystano kolejne rozwiązanie: IIoT Framework, zaimplementowane w sterownikach PLCnext Technology. Platforma IIoT Framework jest skalowalnym, otwartym i elastycznym interfejsem łączącym poziom produkcyjny OT z rozwiązaniami z sieci IT. Wyposażono ją w konektory dla takich protokołów, jak Profinet, Modbus czy MQTT, które mogą zbierać dane z różnych czujników zainstalowanych w zróżnicowanym świecie OT. Informacje te mogą być następnie przesyłane do bazy danych – takich jak MySQL lub InfluxDB – albo do usług chmurowych, takich jak Proficloud. io, AWS lub Azure, przy użyciu wspomnianych konektorów. W ten sposób dane są dostępne w zunifikowanej formie na wszystkich poziomach przez cały czas (rys. 1).
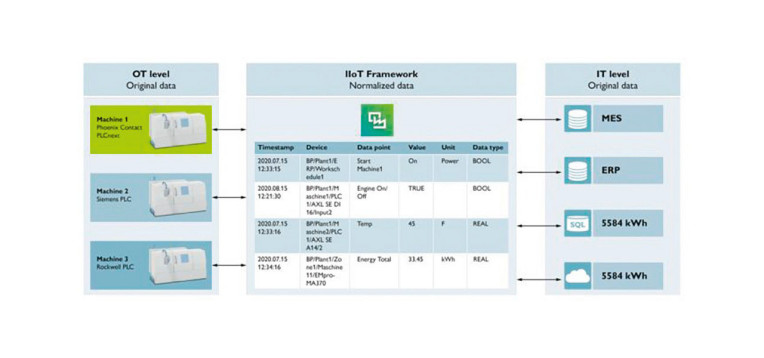
Kluczowy jest fakt, że cały proces przesyłania i unifikacji danych odbywa się w prosty sposób, w graficznym edytorze, bez konieczności dysponowania zaawansowaną wiedzą programistyczną, co znacznie przyspiesza i upraszcza cały proces. Do rejestrowania parametrów elektrycznych silnika wykorzystano mierniki z rodziny produktów EMPro od firmy Phoenix Contact. Zarejestrowane przez miernik EMpro dane o pobieranym prądzie, jak również o zużyciu energii przez silnik, przesyłane są do sterownika PLCnext Technology za pośrednictwem interfejsu Modbus/ TCP. Ponadto dodatkowy czujnik mierzy temperaturę i wibracje na silniku, a następnie przekazuje te wartości do sterownika za pośrednictwem protokołu Profinet oraz IO- Link. Serce układu, w którym zainstalowana jest aplikacja IIoT Framework, stanowi sterownik PLCnext Technology, w formie komputera brzegowego z serii EPC 1522. Urządzenie to zbiera centralnie dane ze wszystkich silników i archiwizuje je lokalnie w bazie danych. Pierwsza baza danych, która została wykorzystana do opracowania i trenowania modelu ML, była dostępna po miesiącu.
Proste trenowanie modelu ML bez wiedzy programistycznej
Początkowy model ML (bazowy) został wygenerowany przy użyciu wcześniej stworzonej bazy danych. Narzędzie programowe MLnext Creation, instalowane na dowolnym komputerze PC, zapewnia intuicyjny interfejs użytkownika, który umożliwia trenowanie modelu ML bez zaawansowanej wiedzy programistycznej czy też z obszaru analityki danych. Interfejs aplikacji prowadzi użytkownika przez cały proces krok po kroku. Po zaimportowaniu danych do MLnext Creation wybrano strategię uczenia "wykrywanie anomalii". Na koniec ustalono złożoność oraz dokładność wyszukiwania hiperparametrów. Parametr ten określa, ile różnych modeli jest trenowanych i porównywanych ze sobą, aż do czasu znalezienia optymalnego modelu. Decydujące znaczenie mają tutaj dostępny czas obliczeniowy i moc obliczeniowa. Wszystkie dalsze kroki, takie jak wstępne przetwarzanie danych, odbywają się w tle (rys. 2).
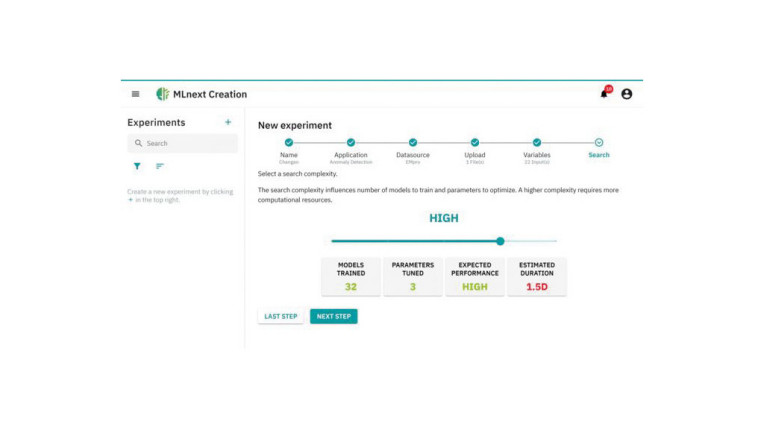
Model stworzony przez MLnext Creation to sieć neuronowa w formie autoenkodera. Ma to na celu kompresję danych wejściowych i zredukowanie ich do najważniejszych cech, aby następnie zrekonstruować je z tej skompresowanej reprezentacji. W przypadku wykrywania anomalii, autoenkoder jest trenowany na podstawie normalnych danych roboczych silników. Jeśli anomalia zostanie wykryta w danych wejściowych po treningu, autoenkoder nie może jej w pełni zrekonstruować. W rezultacie występują znaczne odchylenia między danymi wejściowymi a zrekonstruowanymi, dzięki czemu można zidentyfikować anomalie.
Przygotowanie graficznego interfejsu użytkownika
Kolejny krok wykorzystuje wytrenowany w poprzednim kroku model już w środowisku produkcyjnym. Do tego celu służy narzędzie MLnext Execution, oferujące konfigurowalny system, który obejmuje cały proces – od pozyskiwania danych, wstępnego przetwarzania i wnioskowania, łącznie z modelem do przechowywania zdarzeń. Zaletą MLnext Execution jest to, że nie wymaga od użytkownika żadnej wiedzy programistycznej; wszystkie parametry można ustawić w pliku konfiguracyjnym. W opisywanym projekcie MLnext Execution uruchomiony jest na tym samym urządzeniu brzegowym EPC 1522 z rodziny PLCnext Technology, na którym działa IIoT Framework. Pozwala to na płynną integrację z istniejącą infrastrukturą. Zarejestrowane z silników elektrycznych dane są pobierane z bazy danych niemal w czasie rzeczywistym i poddawane temu samemu przetwarzaniu wstępnemu, co podczas trenowania modelu. Następnie model analizuje dane pod kątem anomalii i zapisuje wyniki – takie jak okres i powód wyzwolenia – z powrotem w bazie danych.
Do wizualizacji danych oraz oceny wyników statystycznych modelu wykorzystano środowisko open source Grafana, które bardzo dobrze sprawdza się w wizualizacji danych i ich analizie. Środowisko to może być używane do tworzenia pulpitów nawigacyjnych oraz interfejsu graficznego dostosowanego do użytkownika, zapewniając tym samym przegląd danych operacyjnych silników oraz wykrytych anomalii. Narzędzie to pozwala również na skonfigurowanie alertów w celu identyfikacji anomalii i ostrzegania personelu z działu utrzymania ruchu o potencjalnych problemach (rys. 3).
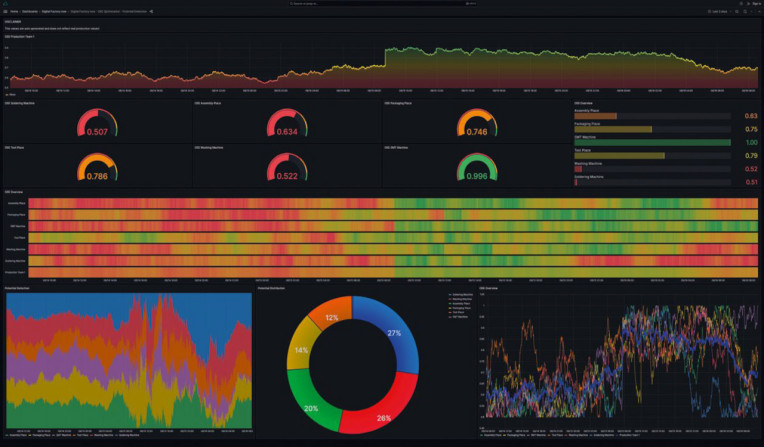
Wyniki
Ciągłe rozwijanie i usprawnianie modelu
Wykorzystanie MLnext do wykrywania anomalii w opisanej aplikacji pokazuje, w jaki sposób można wcześnie wykrywać potencjalne problemy, minimalizując kosztowne przestoje parku maszynowego, a tym samym zwiększając konkurencyjność zakładu produkcyjnego. Proces uczenia maszynowego oferuje również opcję ciągłego ulepszania modelu poprzez ocenę wykrytych anomalii, a tym samym zwiększenie precyzji wykrywania anomalii.
Opisany przykład wdrożenia pokazuje, jak rozwiązanie zaimplementowane na sterownikach PLCnext Technology, z wykorzystaniem takich nowoczesnych narzędzi, jak IIoT Framework czy MLnext, pozwala na:
- zastosowanie kompleksowego podejście do zbierania, przechowywania i analizy danych na poziomie sterownika PLC;
- zwiększenie poprzez analizę danych wydajności urządzeń oraz skrócenie czasu przestojów;
- wykorzystanie potencjału uczenia maszynowego bez posiadania specjalistycznej wiedzy domenowej;
- elastyczne dostosowanie opracowanego rozwiązania do wykorzystania w różnych środowiskach produkcyjnych.
Dowiedz się więcej:
Anomaly Detection – Digital Factory | Phoenix Contact:
https://www.phoenixcontact.com/pl-pl/galezie-przemyslu/aplikacje/anomaly-detection
Robert Gałązka, Menadżer Produktu – systemy automatyki i produkty safety w firmie Phoenix Contact
Phoenix Contact
www.phoenixcontact.pl