Roboty przemysłowe
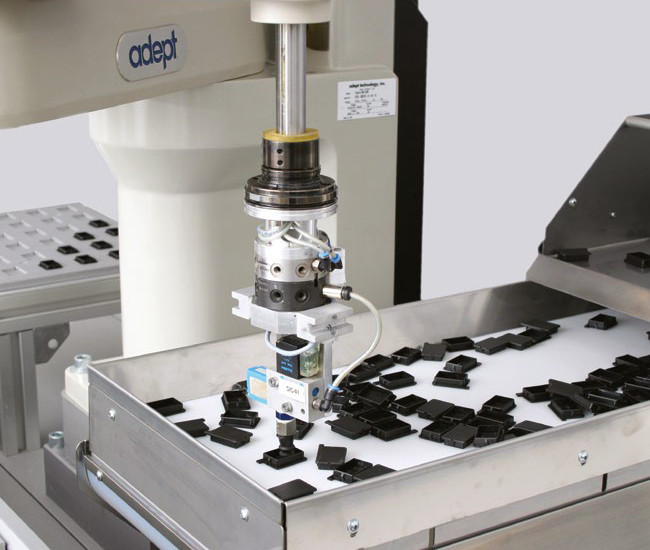
Rynek robotyki przemysłowej należy do szybko rozwijających się i jednocześnie wartościowych sektorów rynku. Owe wzrosty zatrzymała pandemia, natomiast wyniki za 2021 rok są ponownie pozytywne, zaś przyszłość branży obiecująca. O zmianach w tym sektorze pisaliśmy w analizie w zeszłym wydaniu informatora (IRA 2022), w bieżącej analizie uzupełniamy ją, przedstawiając najważniejsze powody, które przekonują klientów do wdrażania robotów przemysłowych.
Koszty pracy
Argumenty natury ekonomicznej i chłodna kalkulacja zazwyczaj najlepiej przemawiają do wyobraźni menedżerów zarządzających fabrykami. Jedną z istotnych przesłanek za robotyzacją, które pojawiły się w ostatnich latach, jest wzrost kosztów pracy. Jest to także jeden z powodów, dla których przemysł w Polsce jest nieco opóźniony w dziedzinie robotyzacji, bo fala wdrożeń robotów w naszym kraju nadeszła dopiero wówczas, kiedy koszty pracy stały się na tyle odczuwalne, by przedsiębiorcy je dostrzegli i zidentyfikowali jako istotną barierę wzrostu. Pomimo że według IFR zaczynamy odrabiać opóźnienie, jednak gęstość robotów, czyli liczba jednostek na 10 tys. pracowników w Polsce, jest wciąż relatywnie mała i wynosi zaledwie 46, podczas kiedy współczynnik ten na świecie wynosi 113. W państwach naszego regionu Czechy z wartością 147 i Słowacja 169 "biją nas pod tym względem na głowę".
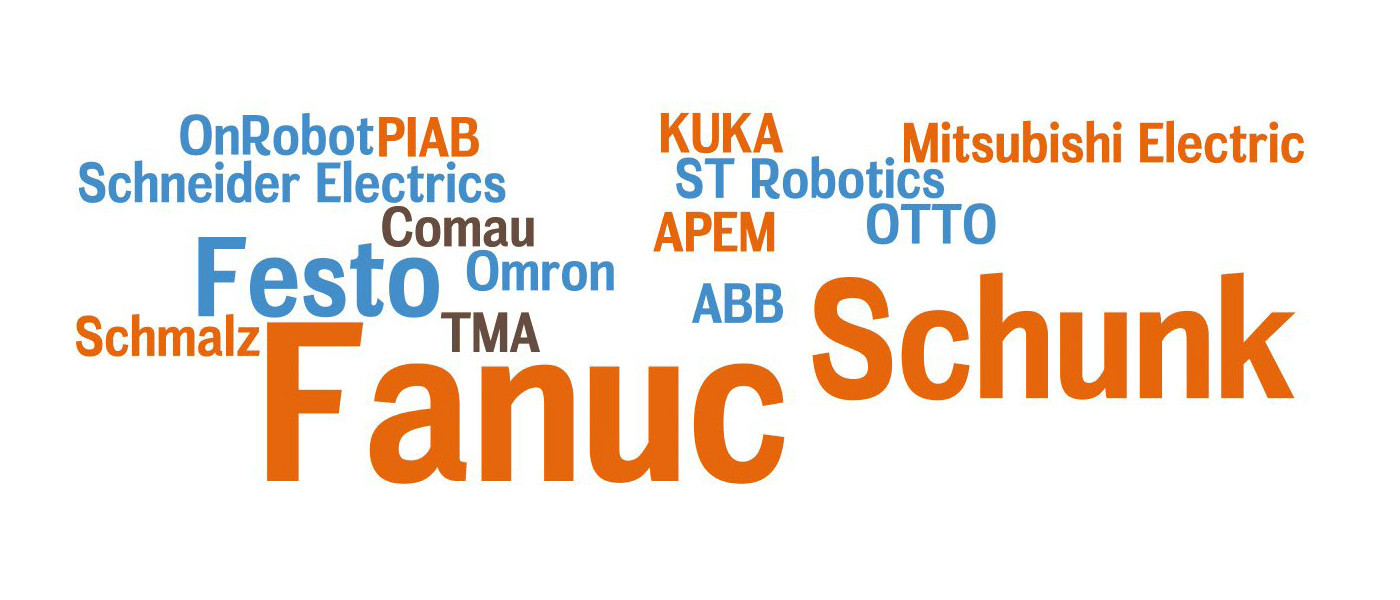
Według danych Eurostatu za 2019 rok koszty pracy w Polsce wynosiły średnio 10,7 euro za godzinę i należały do najniższych w Unii Europejskiej. Na 27 krajów uwzględnianych w tych statystykach niższe od Polski koszty pracy ma jedynie 5, a średnie koszty pracy w całej UE wynoszą 27,7 euro za godzinę. W strefie euro średni koszt pracy to aż 31,4 euro za godzinę. Oznacza to, że przedsiębiorcy w krajach takich jak Dania, Luksemburg, Belgia, Francja czy Holandia, gdzie koszty są najwyższe, mają znacznie większą motywację ekonomiczną do wdrażania robotyki niż przedsiębiorcy w Polsce.
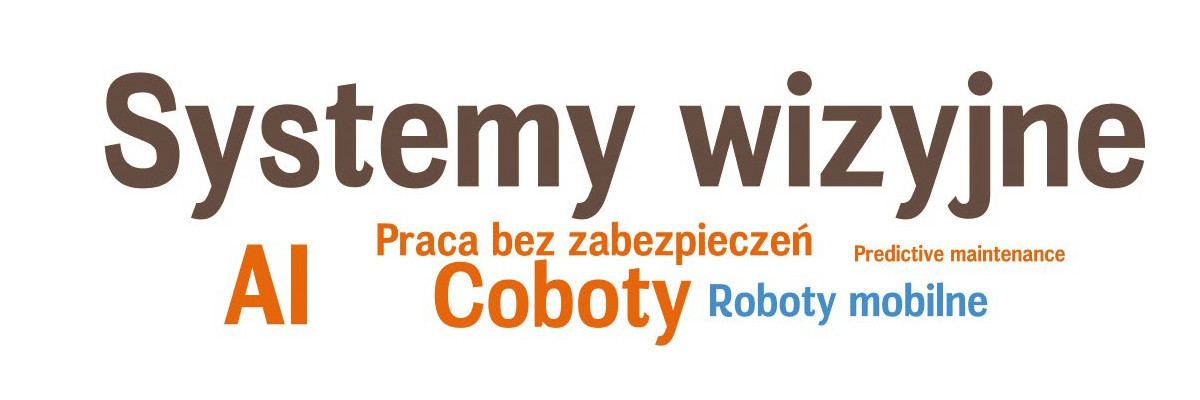
Reasumując, chociaż podkreślane przez wielu ankietowanych koszty pracy i "rynek pracownika" na pewno wywierają istotny nacisk na wzrost poziomu robotyzacji w Polsce, nie należy go jednak przeceniać, bo w innych krajach europejskich presja ekonomiczna na robotyzację wydaje się jeszcze wyższa. Co istotne, kraje naszego regionu, gdzie podobnie jak w Polsce presja kosztowa nie jest aż tak duża jak w Europie Zachodniej (średni koszt godzinowy w Czechach to 13,5 euro na godzinę, a na Słowacji 12,5 euro), wyróżniają się gęstością robotyzacji powyżej średniej światowej. Może to oznaczać, że koszt pracy, aczkolwiek istotny, nie determinuje tempa rozwoju robotyzacji, bo inne czynniki są od nich istotniejsze.
Wojciech Trojniar
ASTOR Robotics Center
Przez ostatnie kilka lat najpopularniejszą aplikacją wdrażaną w zakładach produkcyjnych jest zrobotyzowana paletyzacja. Są dwa główne tego powody. Pierwszy związany jest z problemami zdrowotnymi pracowników. Tradycyjna paletyzacja lub depaletyzacja wykonywana przez ludzi to zadanie mocno obciążające organizmy pracowników. Często to właśnie wydajność końcówki linii produkcyjnej decyduje o możliwościach produkcyjnych całego zakładu. Monotonna praca polegająca na schematycznym układaniu setek kilogramów produktów na pojedynczej palecie przez personel zakładu powoduje, że po wielu latach wykonywania tej czynności mogą się pojawić problemy zdrowotne personelu. Drugim powodem są trudności z pozyskaniem pracowników. Między innymi z tego powodu coraz trudniej znaleźć pracowników, którzy chcieliby podjąć tego typu zajęcie. Rozwiązaniem jest automatyczna paletyzacja, która gwarantuje odpowiednią wydajność przygotowania produktów do wysyłki, niezależną od sytuacji kadrowej. Zrobotyzowana paletyzacja otwiera zatem możliwość, by produkować więcej i szybciej, podnosząc jednocześnie komfort pracy osób zatrudnionych w firmie.
Cykl życia produktów jest coraz krótszy. Nowe linie technologiczne obsługują produkty przez zaledwie kilka lat po czym następuje reorganizacja produkcji. Dzieje się tak z powodu zmian trendów rynkowych, ulepszania produktów, wymogów środowiskowych czy działań marketingowych związanych ze zmianą opakowań. Utrzymanie ciągłości produkcji w takich warunkach wymaga ogromnej elastyczności. Odchodzi się od specjalizowanych maszyn – np. paletyzerów, a znacznie częściej wybierane są roboty, które zapewniają bardzo wysoką wydajność i elastyczność przezbrojenia na inny rodzaj produkcji. W przeciwieństwie do tradycyjnych rozwiązań można znacznie łatwiej i szybciej przestawić na inne gabaryty czy rodzaj produktu. Dziś projektuje się uniwersalne narzędzia do przenoszenia coraz większego asortymentu produktów i opracowuje się coraz lepsze oprogramowanie do paletyzacji. |
Brak wykwalifikowanych pracowników
Brak dostępu do odpowiednio wykwalifikowanych pracowników w kontekście robotyzacji brzmi na pozór mało przekonująco, bo rzeczywiście roboty wykonują na ogół prace powtarzalne i monotonne. Nie znaczy to jednak, że czynności te nie wymagają często wysokiej precyzji wykonania lub specjalistycznej wiedzy pozwalającej właściwie ocenić jakość wykonywanego detalu. Ostatecznie jednak w zadaniach wymagających najwyższej precyzji wykonania to robot góruje nad człowiekiem i z czasem pracowników o rzadkich kwalifikacjach wymagających precyzji, ale powtarzalnych, zastępować będą maszyny.
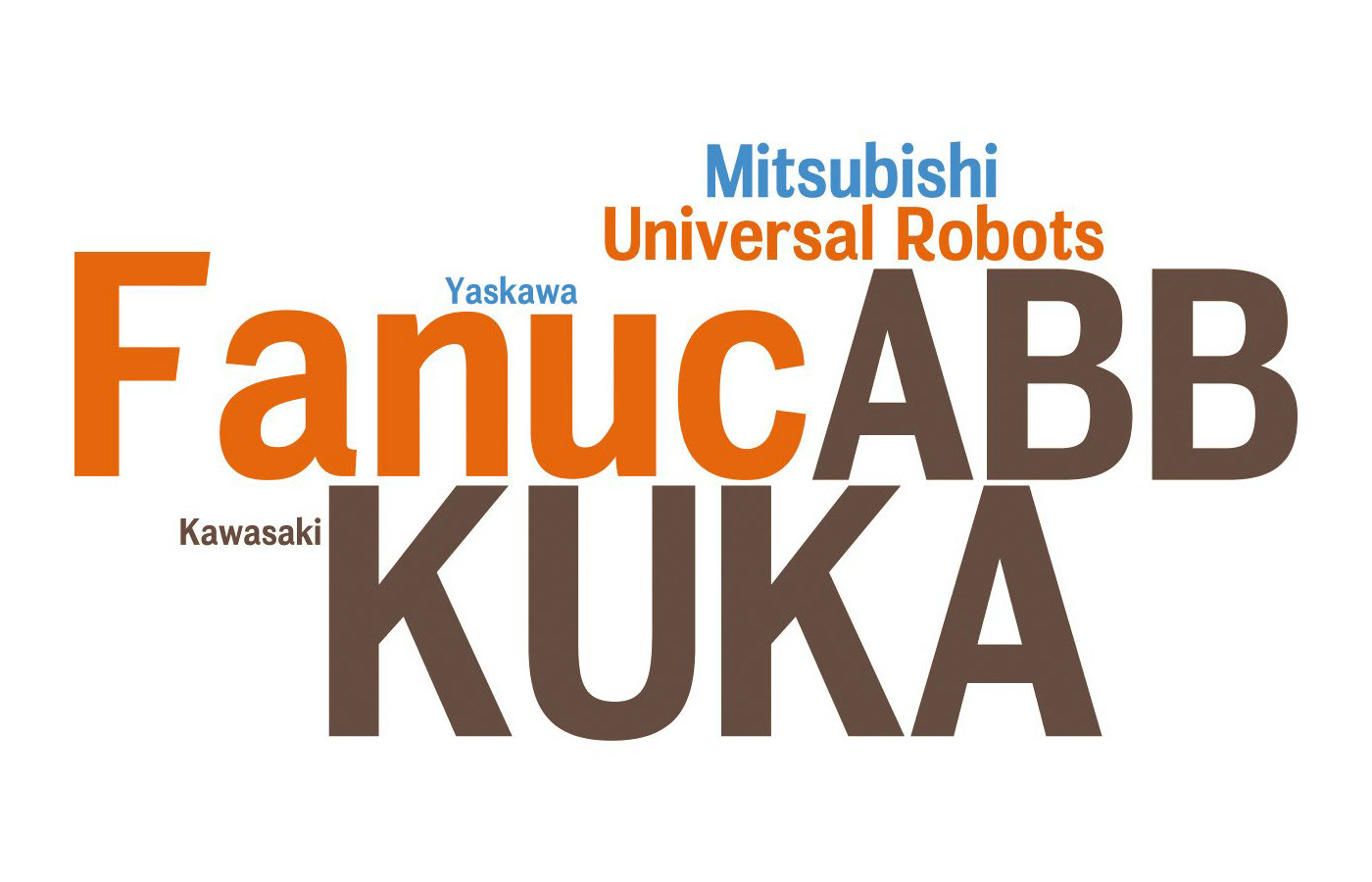
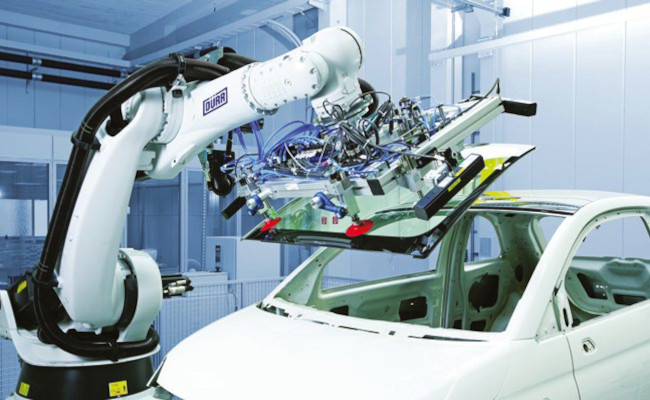
Problem związany z dostępem do wykwalifikowanych pracowników dotyczy nie tylko Polski. Według raportu Komisji Europejskiej "Survey on the access to finance of enterprises (SAFE)", opublikowanego w 2019 r. dostępność wykwalifikowanych kadr była najważniejszym problemem dla 24% polskich przedsiębiorstw, przy średniej dla UE wynoszącej 26%. Dostępność wykwalifikowanej kadry jest szczególnie dużym wyzwaniem w Chorwacji (41%), Estonii (40%), Austrii (37%) i Niemczech (37%). Przyczyną narastającego problemu są zmiany struktury demograficznej, w wyniku których na rynek pracy trafia coraz mniej młodych ludzi, a jednocześnie spada liczba osób w wieku produkcyjnym.
Należy zatem przyjąć, że argument braku odpowiednio wykwalifikowanych "rąk do pracy" z czasem przyczyni się do wzrostu poziomu robotyzacji w całej Europie, w tym także w Polsce.
Innowacje w robotyceWśród wymienianych przez respondentów nowości najczęściej wskazywane były sztuczna inteligencja wraz z uczeniem maszynowym, coboty oraz możliwości predykcyjnego utrzymania ruchu. Zagadnienia te omawialiśmy w zeszłorocznym wydaniu IRA, poniżej natomiast przedstawiamy informacje dotyczące jeszcze jednego obszaru nowości, który związany jest z systemami wizyjnymi. Te montowane w robotach wykorzystywane są w różnych procesach przemysłowych, takich jak kontrola materiałów, rozpoznawanie obiektów, rozpoznawanie wzorców, analiza elementów elektronicznych, a także rozpoznawanie podpisów, znaków optycznych i waluty. Systemy te używane są także do wizualnej kontroli i zarządzania zapasami poprzez odczyt i analizę kodów kreskowych. Możliwości przechowywania informacji o produkcie, które daje system kodów kreskowych, wykorzystują m.in. producenci żywności i napojów do monitorowania ich jakości. Na system wizyjny robota składa się co najmniej jedna kamera, która może być wsparta systemem dodatkowego oświetlenia oraz oczywiście oprogramowanie. Proces obróbki obrazu polega na wykonywaniu zdjęć obszaru roboczego lub obiektu, który chwyta robot, a oprogramowanie pozwala określić cechy obiektu, takie jak na przykład położenie i orientacja. W zależności od zastosowań, kamera zamontowana jest na robocie lub znajduje się w stałej pozycji wewnątrz komórki, w której działa robot. Istotna jest kalibracja działania systemu pozwalająca powiązać przestrzeń współrzędnych systemu wizyjnego z robotem. Dostawcy oferują zwykle sterowane wizyjnie systemy robotyczne wraz z oprogramowaniem ściśle zintegrowanym z kontrolerem robota, co upraszcza programowanie i użytkowanie. Wiele aplikacji wymaga jedynie informacji o osiach X i Y oraz o obrocie obiektu, które można łatwo wyodrębnić z obrazu. Czasami jednak ważna jest także informacja o wysokości, na przykład podczas rozładunku palety, zwłaszcza jeśli wyjmowane obiekty różnią się rozmiarem lub wyładowywana jest tylko część z nich. Z wykorzystaniem systemu wizyjnego 2D lub 3D możliwe jest lokalizowanie elementów niezależnie od ich rozmiaru, kształtu czy położenia. Istnieje kilka sposobów uzyskania informacji o wysokości, na przykład przy użyciu układu dwóch kamer dających widzenie stereoskopowe. W wielu przypadkach najlepszą opcją jest triangulacja laserowa. Wówczas wysokość obiektu określana jest na podstawie położenia linii rzutowanej na powierzchnię docelową i oglądanej pod kątem przez kamerę. Jednym z ograniczeń tej metody jest jednak to, że obiekt lub linia lasera poruszają się. Alternatywnie, gdy znany jest rozmiar elementu pobieranego przez robota, odległość od kamery można określić nawet na podstawie pojedynczych klatek obrazu. Ta technika powszechna jest w przypadku depaletyzacji sterowanej systemem wizyjnym. |
Odciążenie ludzi od prac monotonnych, powtarzalnych i niebezpiecznych
Jednym z istotniejszych powodów robotyzacji jest zastąpienie pracowników wykonujących prace z jednej strony monotonne, z drugiej strony wykonywane w warunkach ciężkich lub zagrażających zdrowiu człowieka. Realizacja wspominanych zadań przez maszyny, które nie odczuwają znużenia ani zmęczenia i są zdolne do pracy praktycznie przez 24 godziny na dobę, wydaje się zatem dobrym rozwiązaniem. Wymieniane przez naszych ankietowanych argumenty przemawiające za robotyzacją: "praca jest monotonna" i "powtarzalna" lub "wyeliminowanie ludzi z jak najprostszych zadań" były dość często wymieniane wśród powodów wdrożenia robotów przemysłowych.
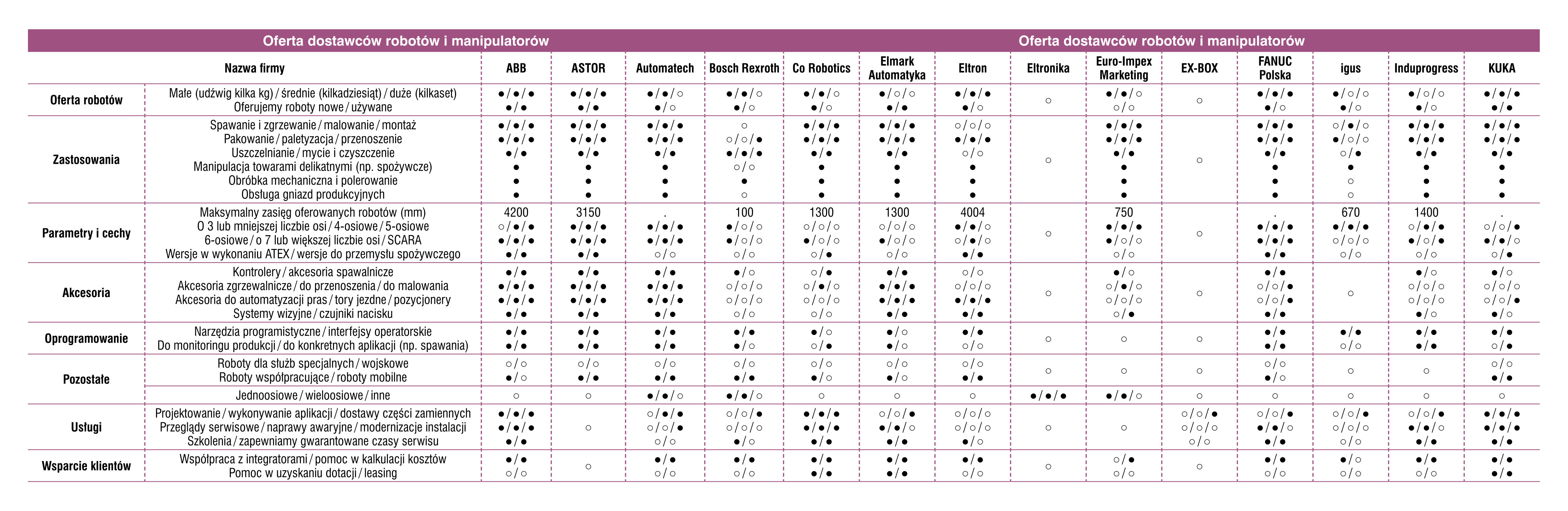
Jakość i dokładność pracy robotów
"Jakość", "precyzja", "dokładność" to atrybuty pracy robotów, które często skłaniają do ich wykorzystania. Wśród aplikacji robotów znaleźć można takie, które pozwalają w pełni wykorzystać precyzję, z jaką wykonują one w pełni powtarzalne zadania. Należą do nich m.in. dozowanie substancji, praca z CNC, kontrola jakości, wkręcanie i wycinanie oraz cała gama innych. Wyposażenie robotów w czujniki siły i momentu siły lub momentu obrotowego pozwala uzyskiwać precyzję niemożliwą do osiągnięcia przez człowieka. Podczas prac wykończeniowych robot może reagować w czasie rzeczywistym na napotkane nieregularne kształty lub wybrzuszenia rzędu ułamków milimetra.
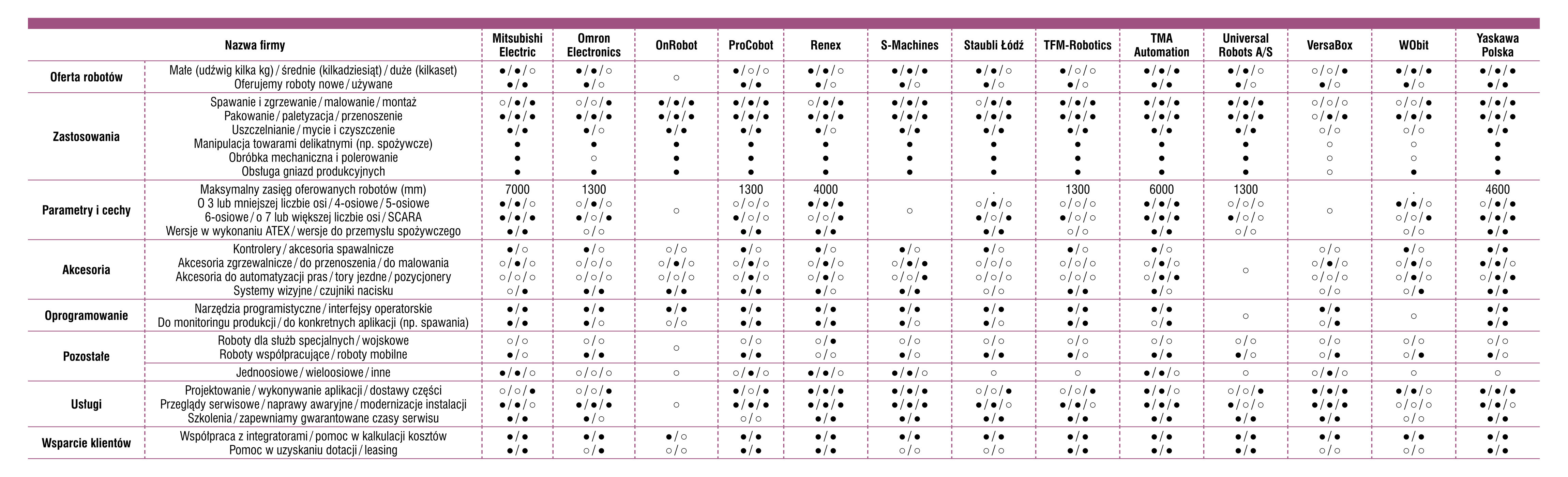
Zwrot z inwestycji w robotyzację (ROI)
Omawianie argumentów wpływających istotnie na wzrost poziomu robotyzacji rozpoczęliśmy od aspektów ekonomicznych i skończymy na nich, albowiem finalnie to twarde dane liczbowe mają największy wpływ na podejmowane decyzje. Wśród argumentów wymienianych przez naszych respondentów "za robotyzacją" pojawiają się m.in. takie jak "cena", "wzrost efektywności" czy "zwiększenie wydajności produkcji". Można je wszystkie sprowadzić do jednego wspólnego mianownika i nazwać "zwrotem z inwestycji w robotyzację". Każda inwestycja wymaga dokładnej analizy kosztów i spodziewanych korzyści. Ostatecznie o wdrożeniu lub niewdrożeniu robotyzacji danej czynności lub linii produkcyjnej najwięcej powie nam wskaźnik ROI oraz spodziewany okres zwrotu z inwestycji. Menedżerowie, szacując je, są zmuszeni do poczynienia pewnych założeń, które nierzadko okazują się zbyt optymistyczne. Dlatego, by zminimalizować ryzyko nietrafionej inwestycji w robotyzację, najlepszym rozwiązaniem jest wdrożenie pilotażowe, którego wynik albo potwierdzi albo obali przyjęte założenia.
Łukasz Szczepkowski
KUKA Polska
Niewątpliwie pandemia miała wpływ na całą branżę przemysłową. Jednak zauważamy, że w zależności od branży oraz wielkości przedsiębiorstwa producenci przyjmują różne strategie działania. Duże firmy, których tegoroczny budżet uwzględniał inwestycje w rozwój rozwiązań z zakresu automatyzacji i robotyzacji, ostrożnie podchodzą do realizacji planów. Sytuacja wygląda zupełnie inaczej w małych i średnich firmach, gdzie widzimy wyraźny wzrost zainteresowania automatyzacją oraz robotyzacją. Producenci dążą do zapewnienia płynności procesów produkcyjnych oraz stworzenia bezpiecznych warunków pracy zatrudnionym, poprzez przekazanie części zadań robotom.
Są nimi: bardzo duża powtarzalność, dokładność prowadzenia ścieżki oraz niezawodność, która zapewnia nawet kilkanaście lat pracy przy zapewnieniu niemalże fabrycznych parametrów danego urządzenia. Z kolei o wyborze konkretnego rozwiązania decydują kluczowe parametry, na podstawie których dobiera się robota, a z których najważniejsze to zasięg i nośność. Najczęstszym zastosowaniem robotów przemysłowych są aplikacje, które przejmują powtarzalne, fizyczne prace takie jak paletyzacja, montaż czy spawanie. Inwestycje związane z wdrożeniem robota do tych aplikacji uznaje się za najprostsze i najszybsze. Oczywiście zależy to od różnych czynników, np. wolumenu czy powtarzalności produkcji.
Sytuacja na rynku w Polsce wygląda bardzo dobrze i takie są też prognozy dla jej rozwoju. W porównaniu do rynków rozwiniętych, jak niemiecki czy czeski, w naszym kraju nadal zagęszczenie robotów przemysłowych w stosunku do liczby zatrudnionych pracowników jest relatywnie niewielkie. Większe firmy z sektora automotive czy general industry nadal będą inwestować na obecnym lub większym poziomie. Z kolei małe i średnie przedsiębiorstwa coraz częściej widzą potencjał drzemiący w automatyzacji i robotyzacji. |