Zakłady KRIO Odolanów, które wybudowane zostały w latach 70. zeszłego wieku, od samego początku istnienia mogły pochwalić się stosowaną tam wysoką technologią. Jako nieliczne funkcjonują one również do dzisiaj, ciągle znajdując się w czołówce pod względem zaawansowania kontroli procesów technologicznych.
Pozycja taka to wynik polityki zarządu firmy, który w inwestycjach w automatyzację widzi sposób na redukcję kosztów działania przedsiębiorstwa. W artykule opisano proces wdrożenia oraz wyniki pracy nowoczesnego układu sterowania pieca wygrzewającego absorbent, co przyczyniło się do wzrostu ekonomiczności procesów przetwarzania gazu ziemnego w omawianym zakładzie.
Opis obiektu
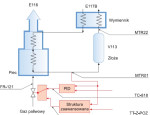
Rys. 1. Schemat instalacji
Zakład KRIO Odolanów, dzisiejszy PGNiG Oddział w Odolanowie, zbudowany został na ponad 30 lat temu. Usytuowanie i cel jego istnienia zdeterminowały odkrycia na Niżu Polskim złóż gazu ziemnego o niskiej zawartości metanu. Zakład zajmuje się przetwarzaniem tego typu zaazotowanego gazu ziemnego wydobywanego w kopalniach zlokalizowanych w Wielkopolsce, Ziemi Lubuskiej oraz na Dolnym Śląsku. Stosowana technologia opiera się o procesy niskotemperaturowe (kriogeniczne). W wyniku kriogenicznego przetwarzania gazu zaazotowanego uzyskiwane są takie produkty jak gaz wysokometanowy zasilający sieć przesyłu gazu, skroplony gaz ziemny LNG, gazowy i ciekły hel oraz ciekły azot.
Kriogeniczne przetwarzanie polega na schładzaniu gazu do niskich temperatur oraz jego skropleniu dzięki czemu następnie możliwe jest odseparowanie w kolumnie destylacyjnej z mieszaniny gazów czystego azotu i helu. Warunkiem wpuszczenia mieszaniny gazów do kolumny jest ich oczyszczenie z ciężkich węglowodorów. Zabieg ten wymagany jest ze względów technologicznych, aby nie doprowadzić do zanieczyszczenia wymienników ciepła.
Usunięcie ciężkich węglowodorów następuje w wyniku przepuszczenia mieszaniny gazów przez złoże absorpcyjne. Następnie gaz wpuszczony zostaje do kolumny destylacyjnej, gdzie następuje odazotowanie (uzyskanie gazu wysokometanowego) i wydzielenie się helu. Złoże absorpcyjne wymaga regeneracji co kilka godzin, w tym celu przez złoże przepuszczany jest wysokometanowy gaz (uzyskiwany w kolumnie destylacyjnej) podgrzany w piecu do temperatury ponad 300°C. Gaz podgrzewa złoże i zabiera ciężkie węglowodory, które uwalniane są w wysokiej temperaturze. Proces regeneracji kończy się w momencie, kiedy złoże osiągnie temperaturę 280°C, co gwarantuje pełną regenerację. Wygrzewanie złoża ma charakter cykliczny, częstotliwość uzależniona jest od składu gazu i obciążenia z jakim pracuje zakład. Zdarza się, że wymagana częstotliwość wynosi nawet raz na trzy godziny, co przy średnim czasie wygrzewu sięgającym 1h i czasie chłodzenia około 2h powoduje, że omawiany fragment procesu staje się „wąskim gardłem” całej linii produkcyjnej.
Cele wdrożenia
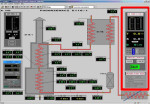
Rys. 2. Grafika operatorska systemu sterowania Ovtion dla podgrzewacza E116/1
Celem przeprowadzonych prac optymalizujących proces wygrzewu było:
- skrócenie jego czasu,
- zredukowanie ilości zużywanego gazu paliwowego,
- występujących w procesie, co pozwoliłyby na przeprowadzenie procesu w sposób łagodniejszy (przy mniejszym zużyciu elementów wykonawczych i redukcji szoków termicznych powstających podczas gwałtownych zmian strumienia gazu paliwowego).
W zakładzie zainstalowane są dwa ciągi technologiczne, które działają w ten sam sposób, dlatego dla obydwu zastosowano identyczną zaawansowaną strukturę regulacji. W artykule przedstawiono wspólny opis obydwu ciągów, akcentując różnice w uzyskanych wynikach.
Instalacja z podstawową strukturą regulacji
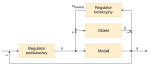
Rys. 3. Schemat struktury Model Following Control
Na rys. 1 przedstawiono schemat obiektu z naniesioną podstawową strukturą regulacji i sposobem włączenia struktury zaawansowanej opartej na regulatorze predykcyjnym DMC (Dynamic Matrix Control) w konwencji MFC (Model Following Control). Układ regulowany był przez bazowy 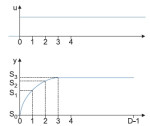
Rys. 4. Przykładowa odpowiedź obiektu na skok jednostkowy na wejściu
Optymalizacja procesu wygrzewu została zrealizowana poprzez wprowadzenie nowej struktury regulacji lepiej dostosowanej do właściwości procesu. Została ona zaprojektowana i wykonana przez zespół badawczy firmy Transition Technologies przy współpracy kadry inżynierskiej zakładów PGNiG Oddział w Odolanowie. Nowe rozwiązanie oparte zostało na wspomnianym regulatorze predykcyjnym zastosowanym w strukturze MFC, która cechuje się większą odpornością na błędy modelowania. Jako regulatora korekcyjnego użyto PID z członem różniczkującym realizowanym zewnętrznie. Ponadto ze względu na całkujący charakter zakłócenia jakim jest temperatura gazu wlotowego użyto człon odprzęgający (feed-forward) realizowany poza regulatorem predykcyjnym. Cała struktura regulacji została zaprogramowana w kontrolerze jako integralna część systemu Ovation. Dodatkowo struktura została przygotowana na zmiany mogące pojawić się w wyniku sezonowych zmian temperatury zewnętrznej – zastosowano podejście obszarowe zaczerpnięte z logiki rozmytej (fuzzy logic) oparte na wnioskowaniu Takagi-Sugeno.
Struktura MFC
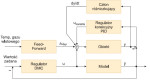
Rys. 5. Zaawansowana struktura sterowania piecem E116/1 I E116/2
Struktura Model Following Control pojawiła się w automatyce w latach 90. ubiegłego wieku i należy do jednych z najnowszych technik stosowanych w przemyśle. Jej idea polega na zastosowanie regulatora podstawowego sterującego modelem procesu, czyli realizującego sterowanie w pętli otwartej. Dodatkowo stosuje się regulator korekcyjny, którego sygnał sterowania wypracowany jest na podstawie predykowanej wartości procesu pochodzącej z modelu i rzeczywistej wartości procesu. Schemat ogólny struktury przedstawiono na rys. 3.
Zastosowanie struktury MFC pozwala na silniejsze zestrojenie regulatora korekcyjnego, gdyż na wejściu tego regulatora sygnał uchybu jest znacznie mniejszy niż w przypadku struktury klasycznej. Dodatkowym atutem struktury MFC jest dwutorowość pozwalająca na niezależne nadążanie procesu za wartością zadaną oraz tłumienie zakłóceń.
Regulator predykcyjny typu DMC

Rys. 6. Struktura w ujęciu logiki rozmytej
Regulator DMC należy do grupy algorytmów MPC (Model Predictive Control). Historia tego algorytmu sięga końca lat 70. ubiegłego wieku, kiedy powstała jego pierwotna forma, a zaraz potem miało miejsce pierwsze wdrożenie w przemyśle chemicznym. Od tego czasu algorytm przeszedł szereg unowocześnień, polegających głównie na opracowaniu sposobu uwzględniania ograniczeń na sygnały regulujące (MV), a następnie na sygnały regulowane (CV). Funkcjonalność tę uzyskano poprzez formułowanie zadania w postaci zadania kwadratowego z ograniczeniami liniowymi, które jest rozwiązywane przy użyciu procedury programowania kwadratowego. Pierwsze teoretyczne prace powstały w końcu lat 80. ubiegłego stulecia i rozwijane są do dzisiaj – szczególnie mechanizmy unikania pustych zbiorów rozwiązań.
W algorytmie DMC dynamika obiektu regulacji modelowana jest dyskretnymi odpowiedziami skokowymi zależności pomiędzy wyjściami z obiektu (CV), a jego wejściami (MV). Warto wspomnieć, że taki opis jest bardzo prostym i wygodnym sposobem modelowania dynamiki obiektu. Jego model może zostać otrzymany na drodze prostego eksperymentu polegającego na dokonaniu wymuszenia na wejściu obiektu.
Na podstawie modelu obiektu w każdym kroku liczona jest predykcja sygnałów regulowanych, która potem jest używana w zadaniu minimalizacji wskaźnika jakości opisanego zależnością:
gdzie:
N – horyzont predykcji,
Nu – horyzont sterowania,
yzad(k + p k) – predykcja wartości zadanej, gdzie długość predykcji równa jest długości horyzontu predykcji pomniejszonemu o minimalne opóźnienie występujące w modelu,
y(k + p | k)– predykcja wartości regulowanej (wyjściowej) – trajektoria ta uzyskiwana jest jako złożenie trajektorii swobodnej i zmian wynikających z wyliczonego sterowania, przy czym obydwie wielkości wyznaczane są na podstawie modelu wewnętrznego,
D u(k + p | k)– predykcja zmian wartości sygnału sterującego – trajektoria ta uzyskiwana jest w wyniku rozwiązania zadania optymalizacji, długość trajektorii równa jest horyzontowi sterowania,
Q– kwadratowa diagonalna macierz wag sygnału wyjściowego, która pozwala na różnicowanie wpływu poszczególnych wyjść na wartość wskaźnika jakości,
R– kwadratowa diagonalna macierz wag sygnału sterującego, która pozwala na różnicowanie wpływu poszczególnych sygnałów sterujących oraz modyfikowanie wpływu składników drugiej sumy we wskaźniku jakości. Rozwiązanie powyższego zadania jest równoważne z rozwiązaniem zadania kwadratowego programowania z ograniczeniami.
Zaawansowana struktura sterowania pieca E116/1 i E116/2
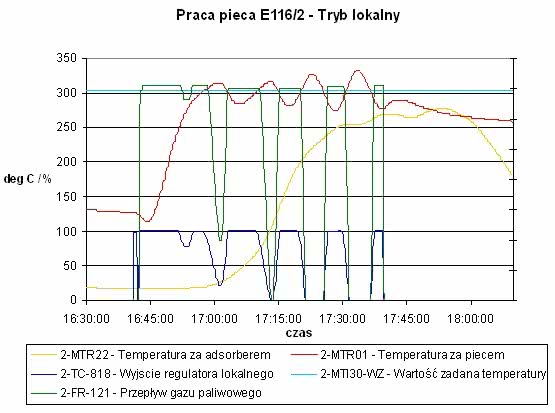
Na rys. 5. przedstawiono schematycznie strukturę regulacji zastosowaną do sterowania i optymalizacji procesu wygrzewu pieca E116/1 i E116/2. Dla obu pieców zastosowano identyczną strukturę, różnice występują tylko na poziomie parametrów strojeniowych. Zadaniem regulatora DMC jest wyliczenie sterowania w pętli otwartej oraz wyliczenie trajektorii referencyjnej dla regulatora korekcyjnego PID. Ze względu na charakter procesu człon różniczkujący zrealizowano zewnętrznie, jak również z powodu całkującego wpływu temperatury gazu wlotowego użyto członu odprzęgającego realizowanego zewnętrznie.
W celu utrzymania wysokiej jakości sterowania w całym zakresie pracy zastosowano podejście zaczerpnięte z logiki rozmytej, w szczególności modeli Takagi-Sugeno. Pomysł polega na implementacji równolegle kilku struktur regulacji różniących się tylko wartościami parametrów strojeniowych, które dostrojone są do różnych punktów pracy. Następnie na bieżąco, wraz ze zmianą punktu pracy, wyliczana jest wartość finalna sterowania jako średnia ważona wartości wyliczonych z poszczególnych regionów. Wartość wagi zależy od tego jak blisko proces jest danego punktu pracy. Ideę tę przedstawiono schematycznie na rys. 6.
Omówione podejście pozwala na niezależne zestrojenie struktury do różnych parametrów pracy – np. uwzględnienie sezonowości, czyli dużych różnic w temperaturze zewnętrznej.
Uzyskane wyniki
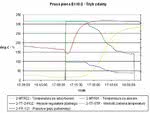
Na rys. 7 przedstawiono przykładową szarżę układu przed wdrożeniem zaawansowanej struktury regulacji (dla ciągu nr 2). Przebieg wartości zmiennych procesowych charakteryzuje się dużą oscylacyjnością zarówno sygnału wyjściowego z regulatora (TC-818), jak i wartości regulowanej (MTR01). Oscylacje występujące w układzie przekładają się na duże wartości przeregulowania wartości regulowanej, wydłużony czas wygrzewania złoża oraz zwiększony pobór gazu paliwowego. Podczas pracy struktury bazowej w początkowej fazie nagrzewania obserwowalne było zbyt wczesne przymykanie zaworu gazu paliwowego, co prowadziło do opóźnienia czasu w którym wielkość sterowana MTR01 osiągała wartość zadaną MTI30-WZ, a co za tym idzie wydłużał się czas całego cyklu. Wielkości charakteryzujące jakość regulacji (przebieg cyklu) zostały zawarte w tab. 1.
Zastosowanie zaawansowanej techniki regulacji wyraźnie poprawiło przebieg procesu wygrzewania, co można zaobserwować na rys. 8. Wyeliminowanie oscylacji przełożyło się na mniejsze wartości przeregulowania, przez co proces spalania odbywa się w sposób najkorzystniejszy z możliwych dla elementów ciśnieniowych pieca, poprawiając tym samym ich żywotność. Mniejsze oscylacje to również łagodniejsze eksploatowanie elementów wykonawczych – zaworów palnikowych, oraz zmniejszenie zjawiska szoków termicznych występujących przy gwałtownych zmianach strumienia gazu paliwowego. W celu porównania regulacji zaawansowanej (zdalnej) z układem bazowym (lokalnym) przedstawiono poniżej tabelę analogiczną do poprzedniej.
Różny czas wygrzewania spowodowany jest zmienną wartością opałową gazu paliwowego, jednak przy porównywalnych warunkach zastosowanie układu regulacji predykcyjnej pozwala na zmniejszenie czasu wygrzewania średnio o 10 minut (redukcja z 1 godziny do 50 minut). Zmniejszeniu ulega również zużycie gazu paliwowego, średnio o 8%. Dodatkową zaletą układu regulacji zaawansowanej jest możliwość zmniejszenia czasu trwania cyklu w sytuacjach awaryjnych poprzez zwiększanie wartości zadanej nawet do 320°C. Uzyskane rezultaty potwierdzają słuszność przeprowadzania inwestycji, a zwrot nakładów uzyskany w opisanym przykładzie i wynikający tylko z oszczędności gazu paliwowego nastąpił po kilkunastu miesiącach pracy układu.
Andrzej Kociemba
Sebastian Plamowski
Sławomir Wieczorek