Kiedy prędkość wirnika silnika jest większa niż jego prędkość synchroniczna, może on działać jako generator, przetwarzając energię mechaniczną w energię elektryczną. Ta ostatnia musi zostać w jakiś sposób zagospodarowana i generalnie są na to dwa sposoby – rozproszenie w postaci ciepła lub jej ponowne wykorzystanie. Drugie realizuje się w ramach hamowania regeneracyjnego, zaś pierwsze dzięki hamowaniu dynamicznemu.
Na czym polega hamowanie dynamiczne?
Podczas hamowania dynamicznego energia elektryczna generowana przez silnik jest rozpraszana w formie energii cieplnej w rezystorze. Ze względu na ten ostatni wyróżnia się dwie konfiguracje. W pewnych zastosowaniach jeden lub wiele rezystorów jest oddzielonych od modułu z przełącznikami tranzystorowymi i sterownikiem. Dzięki temu oporniki można lepiej dobrać, a dodatkowo separuje się wrażliwe komponenty od źródła ciepła, którym są rezystory. W drugim rozwiązaniu zintegrowany moduł hamowania dynamicznego obejmuje przełączniki IGBT, sterownik, jak i rezystor.
Wyróżnić można dwie metody sterowania hamowaniem dynamicznym – z histerezą i z modulacją szerokości impulsu. W pierwszym przypadku sterownik monitoruje napięcie na zaciskach silnika i przełącza tranzystory IGBT, gdy jego wartość przekracza zdefiniowane progi. Umożliwia to odpowiednio przepływ prądu do gałęzi obwodu z rezystorem i jego w nim konwersję na ciepło lub odłączenie opornika od prądu. W sterowaniu PWM tranzystory są przełączane w sposób ciągły zgodnie z przyjętym algorytmem sterowania i w oparciu o pomiar napięcia. To ogranicza tętnienia momentu obrotowego.
Dobór rezystora hamowania wymaga analizy parametrów pracy napędu oraz silnika (moc, napięcie, prędkość obrotowa, bezwładność) i obciążenia (bezwładność, moment tarcia, czas zwalniania i cykl pracy). Generalnie urządzenia o dużym momencie tarcia, jak wentylatory i pompy, nie wymagają hamowania dynamicznego, inaczej niż obciążenia, które charakteryzują się dużą bezwładnością i małym momentem tarcia.
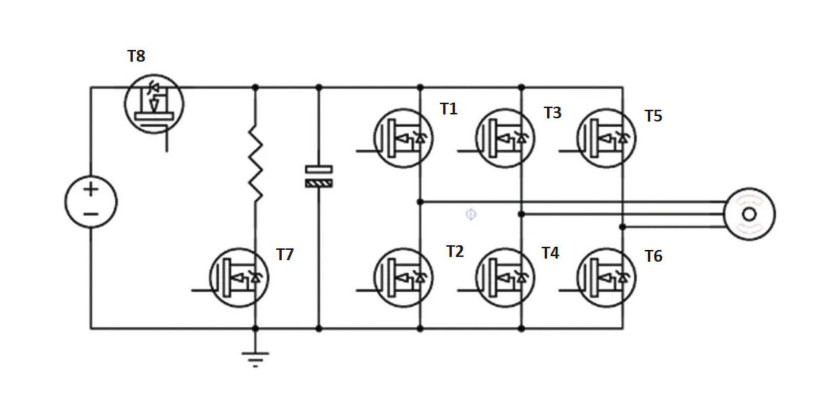
Jak zrealizować hamowanie regeneracyjne?
Hamowanie regeneracyjne różni się od dynamicznego tym, że zamiast rozpraszać energię powstałą w wyniku hamowania, przechowuje ją w sieci zasilającej silnik i podłączonych do niej elementach magazynujących (akumulator, superkondensator itp.), o ile te są dostępne. Można je zrealizować, wykorzystując mostki H sterownika silnika i jego wewnętrzną indukcyjność do utworzenia przekształtnika podwyższającego napięcie. Ma to na celu zwiększenie napięcia w sieci zasilającej silnik powyżej napięcia zasilania, tak aby prąd płynął od silnika do źródła zasilania.
Jest to realizowane następująco: kiedy hamowanie regeneracyjne jest aktywowane, zamiast włączyć tranzystory high-side jednego mostka H, sterownik włącza te low-side, (rys. 2). Ponieważ w kolejnym mostku też załączone są tranzystory low-side dochodzi do zwarcia zacisków silnika. To powoduje narastanie prądu w jego indukcyjności, a gdy tranzystory low-side zostają wyłączone, odkłada się na niej napięcie, które sumuje się z siłą przeciwelektromotoryczną silnika. W efekcie napięcie na jego zaciskach przewyższa napięcie zasilania, co powoduje przepływ prądu z silnika do źródła zasilania.
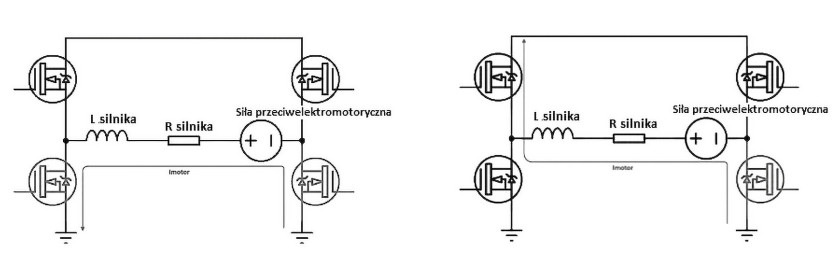
Źródło zasilania silnika powinno być jednak w stanie energię jego hamowania przyjąć. Jeżeli jest nim akumulator, będzie on podczas hamowania doładowywany. Podobnie jeśli źródłem jest zasilacz dwukierunkowy, możliwy będzie odwrotny przepływ energii. W obu przypadkach kluczową kwestią jest, by moc/prąd hamowania nie były większe niż dopuszcza to dane źródło zasilania.
Przykładowo akumulatory kwasowo-ołowiowe mogą rozładowywać chwilowe prądy, które są do pięciu razy większe niż pojemność akumulatora, jednak do ich ładowania prąd musi być zwykle ograniczony maksymalnie do połowy pojemności. W efekcie dopuszczalna moc hamowania jest w ich przypadku ograniczona do 1/10 maksymalnej mocy chwilowej. Podobnie jest, jeśli chodzi o akumulatory litowe – typowo dopuszczalny jest prąd rozładowania, który jest nawet 40-krotnie większy niż pojemność, jednak prąd ładowania jest ograniczony tylko do 2-krotności pojemności. Analogiczne zależności dotyczą również zasilaczy. Poza tym wszystkie typy akumulatorów mają szczytowe napięcie na zaciskach, powyżej którego ulegają uszkodzeniu.
Jeśli źródło zasilania silnika nie jest w stanie przyjąć energii jego hamowania, napięcie w sieci zasilającej wzrośnie i o ile nie jest monitorowane, może przekroczyć wartości znamionowe innych urządzeń do niej podłączonych i je uszkodzić. Metoda ta zapewnia duże oszczędności energii – w przypadku obciążeń o dużej bezwładności co najmniej połowę tej wymaganej do uruchomienia silnika z daną prędkością można dzięki hamowaniu regeneracyjnemu odzyskać, jednak wymaga dodatkowych rozwiązań na poziomie systemu, które nie zawsze są możliwe do zrealizowania.
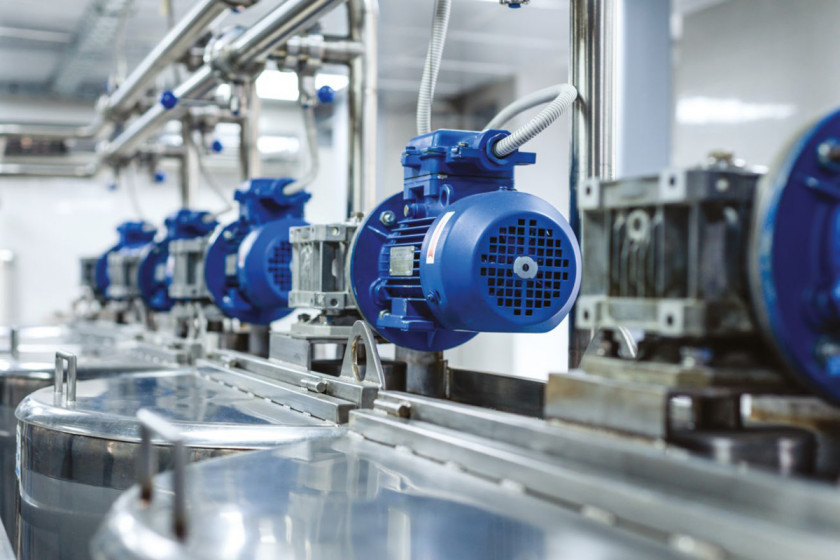
Jaki jest trzeci sposób?
Istnieje także trzecia metoda hamowania silników: plugging. W porównaniu do dwóch poprzednich gwarantuje ona najszybsze zatrzymanie, ale może być uciążliwa zarówno dla elektrycznych, jak i mechanicznych komponentów napędu. Dlatego jest to najrzadziej stosowana metoda hamowania, chociaż w niektórych zastosowaniach się sprawdza.
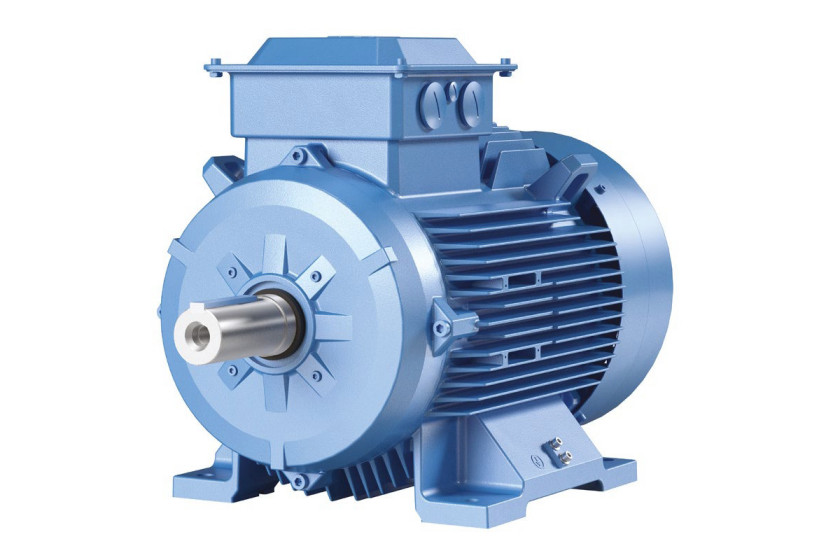
Plugging, inaczej hamowanie prądem wstecznym, ma zastosowanie w przypadku silników prądu stałego, jak i indukcyjnych prądu przemiennego. W przypadku silników prądu stałego odbywa się to przez odwrócenie biegunowości napięcia twornika. Wówczas siła przeciwelektromotoryczna nie jest już przeciwstawna do napięcia zasilania. Zamiast tego oddziałują one w tym samym kierunku, przeciwstawiając się obrotowi silnika i powodując jego niemal natychmiastowe zatrzymanie. Prąd wsteczny temu towarzyszący ma bardzo duże natężenie, dlatego wymagany jest rezystor w celu jego ograniczenia.
W przypadku silników indukcyjnych prądu przemiennego napięcie stojana jest odwracane przez zamianę dowolnych dwóch przewodów zasilających. Jego pole obraca się wówczas w przeciwnym kierunku, zaś poślizg silnika, czyli różnica pomiędzy prędkością obrotową wirnika a prędkością pola wirującego generowanego przez stojan, staje się większy od jednego. Oznacza to, że wirnik obraca się szybciej niż wirujące pole magnetyczne stojana. Wówczas moment obrotowy jest wytarzany w kierunku przeciwnym do obrotów silnika. To zapewnia silny efekt hamowania. Kiedy prędkość silnika spadnie do zera, o ile nie zostanie odłączony od zasilania, zacznie się obracać w przeciwnym kierunku. W pewnych zastosowaniach odwrócenie kierunku obrotów silnika może być efektem pożądanym, jednak w czasie hamowania nie, dlatego wykorzystuje się stycznik, który odłącza silnik od zasilania, gdy jego prędkość spada do zera.
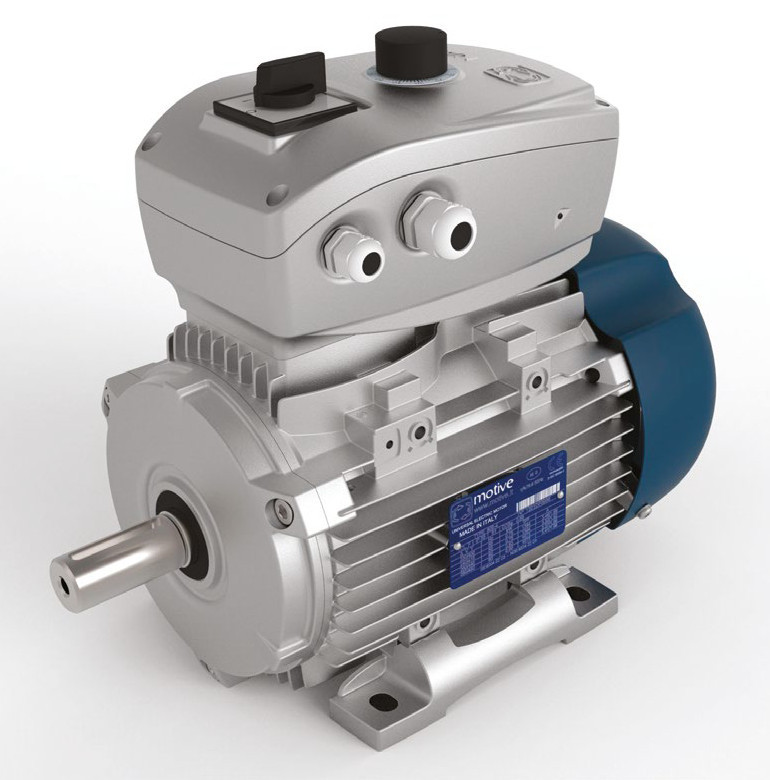
Generalnie zatrzymywanie silnika opisaną metodą, szczególnie jeżeli czas hamowania jest krótki, dokładnie przy zerowej prędkości może być trudne. Kolejnym problemem jest to, że może powodować duże mechaniczne obciążenie udarowe silnika i podłączonego obciążenia, ponieważ powoduje nagłe zatrzymanie. Dodatkowo towarzyszą temu duże straty na ciepło. Mimo tych wad jest wykorzystywane m.in. w windach, dźwigach oraz prasach, czyli w urządzeniach, w których wymagane jest szybkie zatrzymanie silnika.
Monika Jaworowska