Co to jest CNC i jak działa? Materiały wykorzystywane w obróbce CNC
CNC to skrót od angielskiego terminu "Computerized Numerical Control" - sterowanie numeryczne przy użyciu komputera. Jest to system, który może być dowolnie programowany. W zasadzie oznacza to, że maszyna jest kontrolowana przez zestaw poleceń z kontrolera, zwykle w formie listy współrzędnych tworzonych według zasad znormalizowanego języka zapisu poleceń dla urządzeń CNC - G-code. Każda maszyna sterowana tym kodem może być określona jako maszyna CNC.
Zautomatyzowany charakter obróbki CNC umożliwia produkcję z dużą precyzją i zapewnia opłacalność przy realizacji zarówno jednorazowych, jak i średnioseryjnych serii produkcyjnych. W celu kształtowania materiału wyjściowego proces ten wykorzystuje skomputeryzowane elementy sterujące do obsługi maszyn i narzędzi tnących. Do sterowania maszynami CNC używa się kilku języków programowania, w tym kodu G i kodu M. Kod G kontroluje ruchy narzędzi - kiedy włączyć/wyłączyć, jak szybko poruszać się do konkretnej lokalizacji, jakie ścieżki obrać - natomiast kod M steruje funkcjami pomocniczymi maszyny, takimi jak automatyzacja zdejmowania i wymiany osłony maszyny.
Obróbka CNC to subtraktywny proces produkcyjny, co oznacza, że materiał jest sukcesywnie usuwany z pełnego bloku (półfabrykatu) w celu uzyskania pożądanego kształtu. W przeciwieństwie do procesów addytywnych, np. drukowania 3D, które łączą warstwy materiału, procesy subtraktywne usuwają je. Proces ten jest odpowiedni dla wielu różnych materiałów, w tym metali (takich jak stal nierdzewna, stal węglowa, aluminium, mosiądz, tytan, miedź czy nadstopy), tworzyw sztucznych (w tym POM), drewna, szkła, pianki i kompozytów (np. styrodur).
Wybór materiału jest kluczowy i zależy od konkretnego zastosowania. Materiał musi wytrzymać proces obróbki, co oznacza odpowiednią twardość, wytrzymałość na rozciąganie, wytrzymałość na ścinanie oraz odporność chemiczną i temperaturową. Właściwości fizyczne materiału wpływają na optymalną prędkość i posuw skrawania oraz głębokość cięcia.
Historia i rozwój technologii CNC
Obróbka CNC wyewoluowała z procesu obróbki sterowanej numerycznie (NC), który wykorzystywał karty perforowane. Pierwsze maszyny NC powstały na początku lat 50. XX wieku, a ich sterowanie było możliwe dzięki dziurkowanym taśmom oraz kartom.
Przełom nastąpił w 1952 roku, kiedy to w Massachusetts Institute of Technology (MIT) uruchomiono pierwszą obrabiarkę NC – NC Hydrotel firmy Cincinnati, która posiadała pionowe wrzeciono, liniową interpolację 3D oraz kodowaną binarnie taśmę dziurkowaną. W tym samym roku na rynek trafiła również pierwsza komercyjna maszyna tego typu.
Wraz z pojawieniem się mikrokomputerów w latach 80. nastąpił dalszy dynamiczny rozwój technologii CNC, która spowodowała ogromną rewolucję w przemyśle wytwórczym. Współcześnie, w przypadku maszyn posiadających zbyt mało wbudowanej pamięci, stosuje się również technologię DNC (Direct Numerical Control), która pozwala na sterowanie aparaturą za pomocą zewnętrznych komputerów.
Rodzaje układów sterowania CNC
Rozróżnia się trzy główne rodzaje układów sterowania obrabiarek CNC:
- Punktowe (point-to-point, pozycjonujące)
Podstawową funkcją jest tu pozycjonowanie narzędzia w ściśle określonym punkcie względem przedmiotu i nie ma znaczenia, po jakim torze oraz z jaką szybkością porusza się narzędzie, choć dla zwiększenia wydajności zazwyczaj jest to ruch po linii prostej z maksymalną prędkością. To najprostszy układ sterowania, stosowany w maszynach, gdzie kluczowe jest dokładne pozycjonowanie narzędzia nad osią otworu, np. wiertarkach, wytaczarkach, przebijarkach. Ruch narzędzia może odbywać się sekwencyjnie prostopadle do osi (kolejno wzdłuż osi X, a następnie Y - to najwolniejszy sposób), pod kątem 45°, lub w skoordynowanym ruchu liniowym wzdłuż obu osi, przy czym ostatni jest najszybszy, ale najbardziej złożony. - Odcinkowe (segmental, prostoliniowe/paralelne)
Tutaj istotą jest przemieszczanie narzędzia po określonym torze i z zadaną prędkością, a odcinki toru narzędzia muszą być równoległe do ustalonej osi współrzędnych w określonej płaszczyźnie. Takie sterowanie stosowane jest w przypadku planowania i tłoczenia wzdłużnego w obróbce wałków wielostopniowych oraz przy frezowaniu zarysów prostokątnych czy odsadzeń przelotowych. - Kształtowe (contouring/continuous path, konturowe)
Umożliwia realizację dowolnego ruchu - proste, skosy, łuki, krzywe. Dowolny zarys uzyskiwany jest dzięki współdziałaniu dwóch lub więcej silników napędów ruchów posuwowych. Wyróżnia się:
- sterowanie kształtowe 2D, gdzie narzędzie może wykonywać ruchy po łuku okręgu lub elipsy;
- sterowanie 2½D - narzędzie może wykonywać ruchy na różnych płaszczyznach (X/Y, X/Z, Y/Z), przy czym wszystkie trzy osie są sterowane, ale w danej płaszczyźnie najwyżej dwie naraz;
- sterowanie 3D - narzędzie może wykonywać ruchy przestrzenne.
W praktyce często stosuje się układy sterowania mieszanego, np. punktowo-odcinkowego czy odcinkowo-kształtowego.
Ważnym aspektem jest również sterowanie w pętli otwartej lub zamkniętej. W otwartej pętli brakuje informacji zwrotnej, co uniemożliwia korekcję błędów, dlatego jest rzadko stosowana w sterowaniu odcinkowym/konturowym. W systemach z zamkniętą pętlą obwód sprzężenia zwrotnego monitoruje wartości i pozwala na kompensację odchyleń, zapewniając większą dokładność sterowania.
Proces obróbki CNC krok po kroku
Proces skomputeryzowanego wytwarzania przedmiotu składa się z następujących etapów:
- Tworzenie projektu pod obróbkę CNC (CAD)
Proces rozpoczyna się od stworzenia projektu CAD - Computer-Aided Design - w postaci wektorowej 2D lub 3D. Oprogramowanie CAD umożliwia projektowanie modelu z niezbędnymi specyfikacjami technicznymi, jak wymiary i geometrie. Projekty są ograniczone możliwościami maszyny CNC i oprzyrządowania fizycznego, np. cylindryczny kształt narzędzi tworzy narożniki wewnętrzne zakrzywione, a nie ostre. Właściwości materiału i oprzyrządowania ograniczają także minimalną grubość części, maksymalny rozmiar oraz złożoność wewnętrznych wnęk. Po zakończeniu projektowania, plik CAD jest eksportowany do formatu zgodnego z CNC, np. STEP lub IGES.
Dobre praktyki w projektowaniu pod obróbkę CNC
Aby w pełni wykorzystać możliwości obróbki CNC i unikać problemów, warto przestrzegać kilku dobrych praktyk projektowych.
- Zawsze należy zapewnić odpowiednie odstępy pomiędzy detalami przedmiotu, aby narzędzie tnące miało swobodny dostęp do wszystkich powierzchni.
- Głębokość wnęk powinna być ograniczona do czterokrotności ich szerokości.
- Dobrze jest, jeśli promień narożnika wewnętrznego wynosi co najmniej jedną trzecią głębokości danej wnęki. Zwiększenie promienia pozwala narzędziu na cięcie po torze kołowym, co daje lepszą jakość wykończenia powierzchni.
- Zalecane są odpowiednio cienkie ścianki - grubości ścianek to powyżej 0,5 mm dla metali i powyżej 1 mm dla tworzyw sztucznych. Im większy wymiar, tym większa możliwa do osiągnięcia dokładność.
- W przypadku elementów wystających, maksymalny stosunek ich wysokości do ich szerokości nie powinien przekraczać 4.
- W przypadku otworów warto odnosić się do standardowych rozmiarów wierteł - zalecana głębokość to czterokrotność średnicy nominalnej.
- Zawsze warto wybierać możliwie największy rozmiar gwintu dopuszczalny w danym projekcie - i nie powinien być on głębszy niż to konieczne. Najlepiej wybierać standaryzowane rozmiary gwintów.
- Grawerowanie tekstu wymaga usunięcia mniejszej ilości materiału niż tłoczenie. Warto używać fontów standardowych, pod kątem których wiele obrabiarek jest wstępnie zaprogramowanych.
- Jeśli to możliwe, warto tak rozmieszczać elementy konstrukcyjne, by można je było wykonać bez konieczności częstego obracania przedmiotu obróbki. Zmiany ustawienia spowalniają i podnoszą koszty, a ręczne obracanie może negatywnie wpływać na dokładność. W niektórych przypadkach bardziej opłacalne może okazać się złożenie przedmiotu z dwóch niezależnie wykonanych części.
- Konwersja pliku CAD do programu CNC (CAM)
Sformatowany plik CAD przechodzi przez oprogramowanie CAM - Computer-Aided Manufacturing. CAM wyodrębnia geometrię części i generuje cyfrowy kod programowania (G-code i M-code), który będzie sterował maszyną CNC. G-code kontroluje ruchy narzędzi, a M-code funkcje pomocnicze maszyny. Wygenerowany program CNC jest następnie ładowany do maszyny. Istnieją narzędzia programowe do symulacji ścieżek narzędzi, aby ograniczyć ryzyko awarii. - Ustawianie maszyny CNC i uruchomienie procesu obróbki maszynowej
Operator przygotowuje maszynę CNC, mocując obrabiany przedmiot, np. bezpośrednio do maszyny, na wrzecionach lub w imadłach, oraz wymagane oprzyrządowanie, np. wiertła, frezy palcowe. Po pełnym skonfigurowaniu, operator uruchamia program CNC, który stanowi instrukcje dla maszyny - polecenia dyktujące działania i ruchy oprzyrządowania. Interfejs komputera maszyny pozwala operatorowi na wczytywanie, edycję i wykonywanie programów obróbki, wprowadzanie informacji korekcyjnych dla narzędzi, przesuwanie układu współrzędnych oraz śledzenie postępów programu. Procesy obróbki CNC mogą być wykonywane we własnym zakresie lub zlecone wyspecjalizowanym przedsiębiorstwom. Odpowiednio wykwalifikowany operator jest w stanie obsłużyć kilka maszyn jednocześnie, nadzorując proces i korygując błędy.
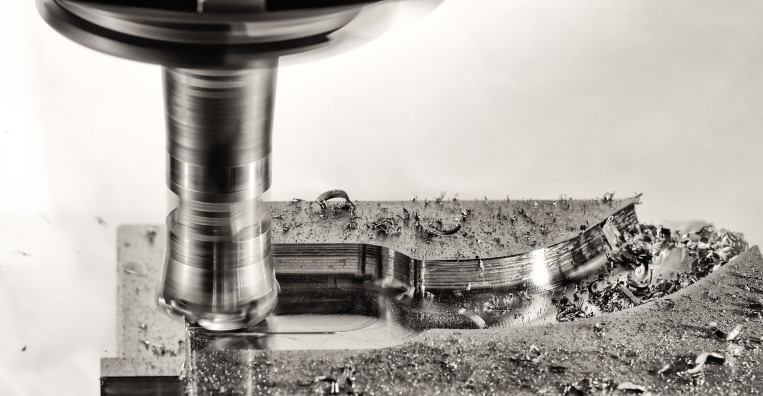
Najczęściej stosowane metody obróbki CNC
Obróbka CNC to proces produkcyjny odpowiedni dla wielu gałęzi przemysłu, w tym motoryzacyjnego, lotniczego, budowlanego, rolniczego, telekomunikacyjnego, medycznego, wojskowego i energetycznego. Proces ten obejmuje kilka różnych sterowanych komputerowo operacji, które usuwają materiał z przedmiotu obrabianego. Do najważniejszych należą:
- Wiercenie - wykorzystuje wielopunktowe wiertła do wykonywania cylindrycznych otworów. Maszyna CNC podaje obracające się wiertło prostopadle do płaszczyzny powierzchni przedmiotu obrabianego. Możliwe są również operacje wiercenia kątowego. Obejmuje pogłębianie, rozwiercanie i gwintowanie.
- Frezowanie - wykorzystuje obrotowe wielopunktowe narzędzia skrawające do usuwania materiału. Podczas frezowania maszyna zazwyczaj podaje obrabiany przedmiot do narzędzia w tym samym kierunku, co obrót narzędzia. Możliwości obejmują frezowanie czołowe (cięcie płytkich, płaskich powierzchni) i frezowanie obwodowe (cięcie wgłębień, rowków). Frezarki CNC mogą produkować płaskie części, ale maszyny bardziej skomplikowane - z większą liczbą stopni swobody - mogą tworzyć kształty złożone.
- Toczenie - wykorzystuje jednopunktowe narzędzia tnące do usuwania materiału z obracającego się przedmiotu obrabianego. Tokarka CNC podaje narzędzie tnące ruchem liniowym wzdłuż powierzchni obracającego się przedmiotu, usuwając materiał na całym obwodzie, aż do uzyskania pożądanej średnicy, w celu wytworzenia kształtów cylindrycznych, jak szczeliny, stożki i gwinty. Możliwości obejmują wytaczanie, planowanie, rowkowanie i nacinanie gwintów.
Inne procesy obróbki CNC obejmują wyoblanie CNC, czyli formowanie metalu poprzez obrót z dużą prędkością i użycie walca (rolki), oraz obróbkę szwajcarską, która wykorzystuje wyspecjalizowany rodzaj tokarki (np. wielowrzecionowy aparat tokarski), pozwalający wykonywać w dużych ilościach precyzyjne i skomplikowane małe części do zastosowań wymagających krytycznych tolerancji prostoliniowości lub współosiowości. Obróbka typu szwajcarskiego pozwala na jednoczesne prowadzenie wielu operacji obróbczych na tym samym przedmiocie.
Poza procesami skrawania, sterowanie CNC można zintegrować z różnymi maszynami do procesów mechanicznych (obróbka ultradźwiękowa, cięcie strumieniem wody i obróbka strumieniem ściernym), chemicznych (frezowanie chemiczne, wykrawanie i grawerowanie), elektrochemicznych (gratowanie elektrochemiczne i szlifowanie) czy termicznych (obróbka wiązką elektronów, cięcie laserowe, cięcie łukiem plazmowym i obróbka elektroerozyjna).
Wieloosiowe centra CNC i maszyny kompaktowe
Maszyny CNC zwykle działają w maksymalnie 5 osiach - kombinacje osi X, Y, Z dla głównych wektorów kartezjańskich oraz A, B, C dla obrotu wokół tych osi. Trzyosiowe frezarki i tokarki są popularne ze względu na dokładność i łatwość programowania, ale mają ograniczenia w dostępie pod pewnymi kątami, co wymaga obracania przedmiotu.
Wieloosiowe centra obróbcze CNC oferują dodatkowe stopnie swobody dzięki możliwości obrotu stołu lub głowicy. Przykładowo, w pięcioosiowej frezarce CNC narzędzie robocze ma zwykle dwie osie obrotowe oraz trzy liniowe względem przedmiotu obróbki, które mogą poruszać się jednocześnie. Zapewniają one wysoką jakość wykończenia i dużą dokładność wymiarów detali, również w przypadku skomplikowanej geometrii, choć koszt jednostkowy jest wysoki.
Dostępne są również kompaktowe obrabiarki CNC, które są mniejsze, lżejsze i lepiej radzą sobie z miękkimi materiałami, jak plastik i pianka, mniejszymi częściami i umiarkowaną produkcją. Maszyny stołowe są przydatne do małych serii produkcyjnych i prototypowania, np. stołowa tokarka CNC do biżuterii.
Akcesoria i komponenty CNC
Wśród akcesoriów i komponentów do maszyn CNC znajdują się elementy, które wpływają na bezpieczeństwo, estetykę i efektywność systemów. Są to rozdzielacze zasilania, wieże sygnalizacyjne - niezbędny dodatek do kontroli procesów produkcyjnych, listwy przyłączeniowe, zasilacze impulsowe, konwertery - jako układy dostosowania napięcia, manipulatory pozwalające na szybkie konfigurowanie baz materiałowych. Inne komponenty to sterowniki, moduły rozszerzeń, serwonapędy, serwosilniki i systemy odczytu położenia.
Współczesne obrabiarki CNC często są uzupełniane o sondy pomiarowe - np. sondy dotykowe TC50 i TC60, sonda OMP40-2 elektrostykowa. Są one montowane w uchwytach i głowicach obrabiarek i wykorzystywane na różnych etapach procesu obróbki. Przed rozpoczęciem cyklu roboczego ułatwiają zestrojenie osi obrabiarki i identyfikację przedmiotu obróbki, co pozwala na sprawdzenie programu i odniesienie położenia przedmiotu do układu współrzędnych maszyny. Ustalają również zapas na rozmiary narzędzia. W trakcie pracy umożliwiają aktualizowanie parametrów ruchu, ścieżek i offsetu narzędzia w reakcji na odkształcenie przedmiotu lub odchylenia narzędzia. Przy końcowej kontroli jakości sondy mierzą wymiary gotowego przedmiotu.
Wyposażenie obrabiarki w sondy pomiarowe zwiększa stopień zautomatyzowania wstępnej konfiguracji, co oszczędza czas, skraca przestoje i zwiększa wydajność produkcji. Dzięki sondom eliminowane są również błędy ręcznego ustawiania, a także wykrywane uszkodzenia i błędy narzędzi, co przyczynia się do ograniczenia liczby wybrakowanych przedmiotów.
Serwonapędy i ich rola w CNC
Serwonapędy to układy wykonawcze kluczowe dla automatyki przemysłowej, w tym maszyn CNC. Sprawdzają się wszędzie tam, gdzie specyfika branży wymaga wysokiej precyzji pracy i gdzie konieczne jest odpowiednie ustawienie optymalnych parametrów działania dla danego urządzenia. Serwonapędy tworzą trzy główne elementy:
- silnik - element wykonawczy serwonapędu;
- enkoder - działa jak licznik lub czujnik, zapisując wartości na poziomie silnika, oraz umożliwia pełną kontrolę nad obrotami silnika i regulację prędkości, przekazując te informacje do sterownika;
- sterownik - łączy silnik z enkoderem, przetwarzając sygnały płynące z kontrolera ruchu.
Aktualne trendy w branży CNC
Branża CNC dynamicznie się rozwija. Obecne trendy wskazują na integrację technologii oraz automatyzację i wdrażanie idei Przemysłu 4.0. Coraz więcej centrów wytwórczych łączy wiele technologii w jedną maszynę, wykorzystując mocne strony zarówno maszyn subtraktywnych, jak i addytywnych.
Nieustanny postęp prowadzi do powstawania bardziej zautomatyzowanych systemów. Będą one w stanie samodzielnie diagnozować, optymalizować i działać przy minimalnej interwencji ludzi. Systemy informatyczne umożliwią coraz głębszą analizę procesów poprzez zbieranie danych i przesyłanie ich do systemów nadrzędnych.
Dzięki oferowanej przez maszyny CNC elastyczności, produkty będą mogły być wykonywane w oparciu o indywidualne wymagania konsumentów.
Zalety i wady obróbki CNC
Zalety obróbki CNC:
- szybkość i precyzja - żaden człowiek nie może dorównać szybkości, precyzji i dokładności obrabiarce CNC;
- wysoka powtarzalność wykonania detali, co jest kluczowe w produkcji przemysłowej;
- elastyczność materiałowa - możliwa jest obróbka praktycznie każdego materiału o odpowiedniej twardości, co pozwala wybrać materiał optymalny dla danego zastosowania;
- jakość wykończenia - gwarantowana jest wysoka jakość wykończenia powierzchni i duża dokładność wymiarowa detali;
- opłacalność - obróbka jest konkurencyjna cenowo, zarówno w produkcji małej, jak i średniej liczby wyrobów, dzięki efektowi skali;
- automatyzacja i bezpieczeństwo - maszyny mogą działać bez przerwy, a jeden operator może obsługiwać wiele maszyn. Zwiększa to bezpieczeństwo, ponieważ operatorzy są mniej narażeni na bezpośredni kontakt z narzędziami.
Wady obróbki CNC:
- wysoki koszt początkowy - maszyny CNC są zaawansowanymi urządzeniami o wysokich wymaganiach w zakresie tolerancji, co przekłada się na ich wysoki koszt zakupu;
- koszty utrzymania i kwalifikacje operatorów - obrabiarki CNC wymagają wysoko wykwalifikowanych operatorów i mają wyższe koszty utrzymania w porównaniu do maszyn ręcznych;
- ograniczenia projektowe ze względu na zasadę usuwania materiału i kształt narzędzi - niektóre kształty geometryczne są niemożliwe do wykonania, np. ostre narożniki wewnętrzne zawsze będą zaokrąglone, maksymalna głębokość podcięcia jest ograniczona, a przedmiot nie powinien mieć wewnętrznych elementów, które uniemożliwiają narzędziu dostęp;
- deformacje i wibracje - nacisk wywierany na materiał i jego nagrzewanie mogą powodować wibracje i deformacje, co ogranicza minimalną grubość ścianek oraz maksymalny stosunek szerokości do wysokości wystających elementów;
- koszty złożonej obróbki - im większy stopień złożoności projektu, tym zwykle większy jest koszt jego realizacji.
Porównanie obróbki CNC i wytwarzania addytywnego (druku 3D)
Obróbka CNC i druk 3D są często przedstawiane jako konkurencyjne technologie.
Jednak obróbka CNC to proces subtraktywny, a druk 3D - proces addytywny. Druk 3D jest zalecany np., gdy przedmiot ma na tyle złożoną geometrię, że jej wykonanie przekracza możliwości obrabiarek CNC, gdy zależy nam na krótkim czasie realizacji zlecenia. Druk 3D jest zazwyczaj tańszy dla małych serii wyrobów - typowa liczba sztuk mniejsza niż 10. Ponadto druk jest stosowany przy obróbce specyficznych materiałów, np. nadstopów metali czy tworzywa TPU, gdzie obróbka subtraktywna wiąże się z komplikacjami.
Obróbka CNC jest - dzięki efektowi skali - konkurencyjna cenowo w produkcji małej i średniej liczby wyrobów. Zapewnia bardzo dobre właściwości fizyczne detali, ponieważ materiał bazowy nie jest modyfikowany, oraz wysoką jakość wykończenia i dokładność wymiarową. W przeciwieństwie do druku 3D, linie kolejnych warstw materiału nie są widoczne.
Firmy i rozwiązania na rynku CNC
Firmy działające w branży CNC oferują szerokie spektrum produktów i rozwiązań automatyki przemysłowej. Dostępne są między innymi sterowniki, moduły rozszerzeń, serwonapędy, serwosilniki, systemy odczytu położenia oraz wiele innych akcesoriów.
Istotną wartością dla klientów jest kompleksowa obsługa – od pomysłu i projektu, przez oprogramowanie i opracowanie technologii produkcji, aż po dostarczenie gotowych urządzeń. Polska firma CS-Lab Electronic Laboratory jest przykładem producenta oferującego takie rozwiązania, cieszącego się popularnością zarówno w Unii Europejskiej, jak i na całym świecie, dzięki nowoczesnym i profesjonalnym rozwiązaniom oraz konkurencyjnym cenom. Firma podejmuje wszelkie wyzwania z zakresu automatyki przemysłowej i CNC, oferując konkurencyjne ceny.
Ważnymi graczami na rynku są również inne firmy, takie jak WAS SHENG z 40-letnim doświadczeniem w obróbce CNC, która oferuje kompleksowe rozwiązania w produkcji precyzyjnych elementów mocujących i komponentów przemysłowych, jak śruby, podkładki, tuleje i wałki, czy Xometry Europe - realizująca usługi obróbki CNC.
Polskie maszyny CNC są cenione za duże możliwości indywidualizacji i dopasowania do konkretnych wymagań klienta. Rośnie zapotrzebowanie na kompleksowe usługi, obejmujące nie tylko same automaty CNC, ale także maszyny towarzyszące, transportery i podajniki. W kontekście Przemysłu 4.0, rozwiązania takie, jak IoT Gateway, umożliwiają dogłębną analizę procesów produkcyjnych poprzez zbieranie danych i ich przesyłanie do systemów nadrzędnych, co pozwala na minimalizację interwencji człowieka.