Pierwszym etapem rozwiązywania problemów z serwosilnikiem jest zdiagnozowanie przyczyny. Większość awarii jest sygnalizowana przez serwonapęd. Dlatego najpierw należy sprawdzić, jakiej usterce jest przypisany dany kod błędu. W instrukcji zwykle znajdziemy także wskazówki odnośnie do zalecanego postępowania w konkretnym przypadku. Dalej przedstawiamy najczęstsze powody nieprawidłowości w pracy serwosilników.
Jak zapobiec przegrzewaniu się serwosilników?
Takim jest przegrzewanie się. Problem ten nasila się zwłaszcza, jeżeli silnik pracuje przez dłuższy czas. Serwosilnik może się przegrzewać z wielu powodów. Przyczyną może być przykładowo zbyt duże napięcie zasilania, przekraczające znamionową wartość dla danego silnika. Przegrzewać się będzie również przeciążony serwosilnik i ten uruchamiany zbyt często. Kolejne powody to: za małe napięcie zasilania albo rozmagnesowywanie się wirnika, co zwiększa pobór prądu, który jeżeli przekroczy wartość znamionową, spowoduje nadmierne nagrzewanie się uzwojeń. Przyczyną mogą być także łożyska, zużyte albo niewłaściwego typu, na które wymieniono te oryginalne, jak i zanik fazy – brak jednej z faz sprawia, że w pozostałych uzwojeniach wzrasta prąd. Przegrzewanie powodują oprócz tego problemy z okablowaniem lub strojeniem serwonapędu. Wzrost temperatury serwosilnika może być też skutkiem zablokowanej wentylacji, nagromadzenia się brudu na jego obudowie albo zbyt wysokiej temperatury w otoczeniu.
Środki zaradcze to w związku z tym: obniżenie napięcia zasilania, zmniejszenie obciążenia albo zastąpienie niedowymiarowanego silnika modelem, który nie będzie przeciążony, nieprzekraczanie zalecanej liczby rozruchów, zwiększenie napięcia zasilania, wymiana zużytych albo niewłaściwych łożysk, sprawdzenie stanu złączy (wykrycie poluzowanych) i okablowania (uwaga na postrzępione, przetarte przewody), skorzystanie z opcji automatycznego dostrojenia serwonapędu, monitorowanie jakości zasilania i reagowanie na jej pogorszenie, niedopuszczanie do nagromadzania się zabrudzeń na silniku i w układzie wentylacji i sprawdzanie jej działania, kontrola temperatury w otoczeniu i w razie potrzeby wdrożenie rozwiązań ją obniżających.
Co robić, gdy serwosilnik się nie obraca?
Czasami serwosilnik po podłączeniu do zasilania nie uruchamia się, czemu jednak jednocześnie nie towarzyszą dym, przykre zapachy ani nietypowe dźwięki. Brak takich wskazówek oznacza, że niełatwo będzie znaleźć przyczynę usterki. Najpierw wykluczyć trzeba tę najbardziej oczywistą, czyli brak zasilania. Powodem może być także awaria bezpiecznika – wówczas należy ustalić przyczynę jego przepalenia i wymienić go na nowy. Możliwe jest też, że do kontrolera serwomechanizmu nie docierają polecenia z zadanymi parametrami ruchu – pod tym kątem trzeba sprawdzić jego wejścia. Przyczyną bywają oprócz tego poluzowane sprzęgło i luzy na złączach kablowych połączeń silnika i sterownika. Silnik może się nie obracać, dlatego że zadziałały przekaźniki termiczne z powodu jego przegrzania. Możliwe też, że nie zakończyło się jeszcze albo nie powiodło się debugowanie programu sterowania ruchem.
Czasem serwosilnik nie pracuje zgodnie z oczekiwaniami już po uruchomieniu, jeżeli nie osiąga prędkości znamionowej, nawet kiedy pracuje przy obciążeniu znamionowym. Prawdopodobnymi przyczynami tego problemu są: spadki napięcia zasilania, prąd znamionowy serwowzmaczniacza niewystarczający do wysterowania serwosilnika, przeciążenie i/lub przegrzanie silnika, problemy z okablowaniem, niewłaściwe ustawienia kontrolera serwomechanizmu. Warto też spróbować usunąć tę usterkę, przeprowadzając autostrojenie serwonapędu.
Jak odzyskać kontrolę nad serwosilnikiem?
Serwosilnik nie działa prawidłowo, jeżeli po uruchomieniu nagle się wyłącza po osiągnięciu dużej prędkości. Problem ten również może mieć kilka przyczyn. Taką są przepalone bezpieczniki. Silnik może się też przegrzewać albo bezpodstawnie jest aktywowane zabezpieczenie przed przeciążeniem, w związku z czym należy pod tym kątem sprawdzić ustawienia kontrolera serwomechanizmu oraz przekaźniki termiczne. Pod uwagę trzeba również wziąć: problemy z okablowaniem, uszkodzone kondensatory, niedziałający lub niedokładny enkoder. Warto też spróbować rozwiązać ten problem, przeprowadzając autostrojenie serwonapędu.
Nietypowe jest wskazanie przeciążenia, gdy serwosilnik pracuje bez obciążenia. Trzeba wówczas sprawdzić poprawność podłączenia i stan kabli silnika, upewnić się, że hamulec jest włączony, sprawdzić ustawienia wzmocnień i stałych czasowych pętli sterowania prędkością i pozycją.
Niepożądana jest też utrata kontroli nad serwosilnikiem. Dzieje się tak przede wszystkim wtedy, gdy brak jest sygnału w pętli sprzężenia zwrotnego, dlatego w pierwszej kolejności należy sprawdzić ciągłość połączenia z czujnikami położenia i prędkości. Przyczyną może być także nieprawidłowa konfiguracja kontrolera serwomechanizmu i problem z okablowaniem serwosilnika lub sterownika.
Hałas i wibracje
Niepokoić powinny nietypowe, głośniejsze niż zwykle, dźwięki towarzyszące pracy serwosilnika. Mogą być spowodowane przez poluzowane sprzęgło, które jeżeli podejrzewamy, że jest przyczyną hałasu, należy sprawdzić i zamocować prawidłowo. Źródłem problemu może być asymetria napięcia zasilającego. Hałasować będą również niewystarczająco nasmarowane łożyska. Nasilać to zjawisko będzie poza tym obecność zanieczyszczeń w smarze. Powodem niepokojących dźwięków mogą być też szumy w sygnałach sprzężenia zwrotnego albo sygnałach sterujących. Pod kątem skuteczności ekranowania trzeba wówczas sprawdzić okablowanie łączące silnik, enkoder i sterownik i upewnić się, że serwosilnik jest prawidłowo uziemiony.
Niepożądane są oprócz tego nadmierne wibracje. Powoduje je nierówna albo zbyt duża szczelina powietrzna w łożyskach spowodowana ich zużyciem się – zazwyczaj jest wówczas konieczna ich wymiana, jeżeli standardowe smarowanie nie rozwiąże problemu. Kolejne potencjalne przyczyny to: niewspółosiowość serwosilnika i napędzanego obciążenia, niewyważenie wirnika, wyginanie się wału, niewłaściwe (poluzowane, zużyte) mocowanie serwosilnika.
Uwaga na charakterystyczny zapach
Jeśli poczujemy spaleniznę albo zobaczymy dym, mamy pewność, że silnik się niebezpiecznie przegrzewa. W takim przypadku należy sprawdzić system wentylacji lub chłodzenia silnika, by się upewnić, że nie jest zablokowany. Jeżeli stwierdzimy, że został zatkany kurzem, trzeba go przeczyścić. Jeśli powyższy krok nie pomoże, należy się upewnić, czy łożyska są w dobrym stanie, sprawdzając czy nie są nadmiernie nasmarowane, nie przegrzewają się lub się nie zużyły. Jeżeli dodatkowo czujemy charakterystyczny zapach ozonu, oznacza to, że palą się uzwojenia lub okablowanie serwosilnika.
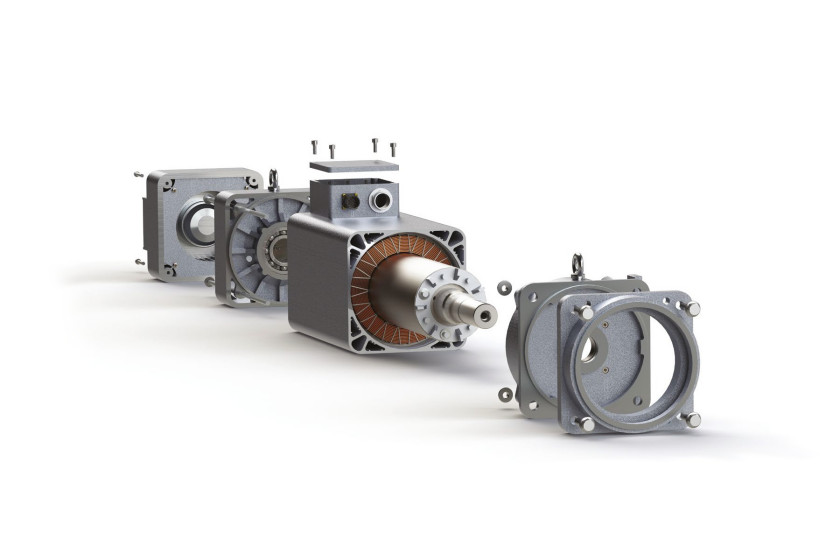
Monika Jaworowska