Główne komponenty złącz to: obudowa wtyczki, dławnica kablowa, wkład męski i wkład żeński ze stykami i obudowa gniazda. Ze względu na rodzaj przenoszonych sygnałów klasyfikuje się je na: silnoprądowe do przesyłania energii, złącza transmitujące sygnały analogowe i cyfrowe (wersje sygnałowe, do sieci komunikacyjnych, światłowodowe) i do przesyłu sprężonego powietrza. Są też dostępne wersje hybrydowe, w których do jednej obudowy podłącza się przewody zasilające oraz sygnałowe, elektryczne i optyczne, i pneumatyczne, w różnych kombinacjach. Złącza oferowane są również w różnych rozmiarach i kształtach (prostokątne i okrągłe, które wyróżnia kompaktowość).
Wybór złączy jest uwarunkowany szeregiem czynników. Oprócz cech funkcjonalnych i specyfiki wykonania, pod uwagę trzeba wziąć ich wytrzymałość na warunki pracy. Do tych najuciążliwszych zalicza się: silne drgania i uderzenia, skrajne temperatury oraz wilgotność, chemikalia, pyły i kurz, atmosfery wybuchowe, promieniowanie UV.
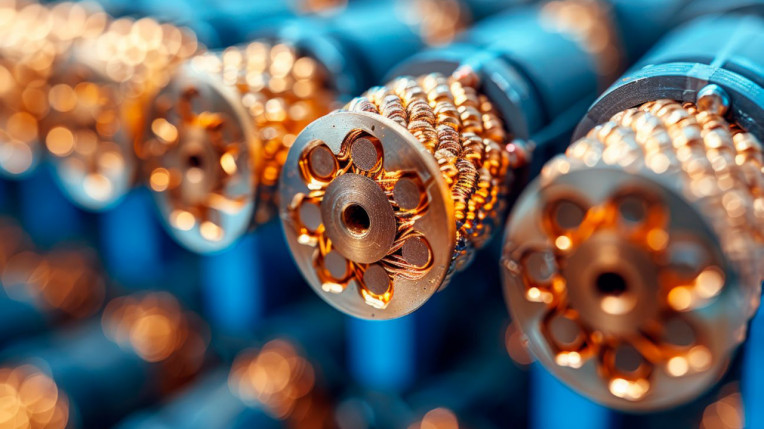
Warunki przemysłowe
Przykładem stanowiska, na którym złącza narażone będą na silne drgania, jest to, na którym pracują podajniki wibracyjne, sortujące i/lub transportujące produkty dzięki drganiom generowanym przez elektromagnes. Kolejny problem to wilgotność. Za wysoka może powodować korozję (rdzewienie) metalowych części złączy, natomiast przy zbyt niskiej zawartości wilgoci w powietrzu mogą się na nich gromadzić ładunki elektrostatyczne. Przykładami stanowisk, na których występują pierwsze warunki, są te, gdzie pracują kotły, parowniki, stacje czyszczące. Zbyt sucho może być z kolei m.in. na stanowiskach montażu w branży elektronicznej.
Normą w przemyśle są również ekstremalne temperatury – od tych skrajnie niskich w chłodniach, po ekstremalnie wysokie w pobliżu pieców. Z kolei tam, gdzie używane są chemikalia, np. kwasy, albo występuje mgła solna, mogą łatwo wytwarzać się atmosfery korozyjne.
Każde stanowisko, na którym wykonuje się jakiś typ obróbki (wiercenie, frezowanie, szlifowanie, natryskiwanie), nieuchronnie generuje pył i zanieczyszczenia, które – jeżeli wnikną do obudowy złącz – mogą spowodować problemy z ciągłością połączeń. Złącza używane na zewnątrz budynków będą z kolei wystawione na bezpośrednie działanie promieni słonecznych.
Czynniki uciążliwe
Silne nasłonecznienie na skutek działania promieniowania ultrafioletowego na materiał obudowy może go osłabiać, przez co łatwo pęka. W wielu branżach tworzą się także atmosfery wybuchowe, np. w spożywczej, gdzie eksplodować może pył mączny albo cukrowy. Złącza używane w takich warunkach nie powinny się zatem stać źródłem zapłonu. Zazwyczaj kilka z wymienionych czynników uciążliwych występuje niestety jednocześnie.
Wymagania stawiane złączom są z tego powodu bardzo wysokie, m.in. w pojazdach w transporcie drogowym i szynowym. Przykładowo, od złączy montowanych na zewnątrz pociągów (pomiędzy wagonami, pod nimi, na dachu, przy torach) oczekuje się odporności na: silne wibracje, osłabiające połączenia, uderzenia drobin piasku, kamieni i opady atmosferyczne (deszcz, śnieg), powodujące erozję i korozję, oblodzenie i nasłonecznienie, a więc skrajnie niskie i wysokie temperatury, które skutkują kurczeniem się i rozszerzaniem materiałów.
Na wstrząsy, drgania i skrajne temperatury narażone są też złącza w autach dostawczych. Te poza tym trzeba zabezpieczyć przed: wnikaniem wilgoci, kontaktem z substancjami korozyjnymi (sól drogowa, chemikalia), wnikaniem pyłów, kurzu i innych zanieczyszczeń.
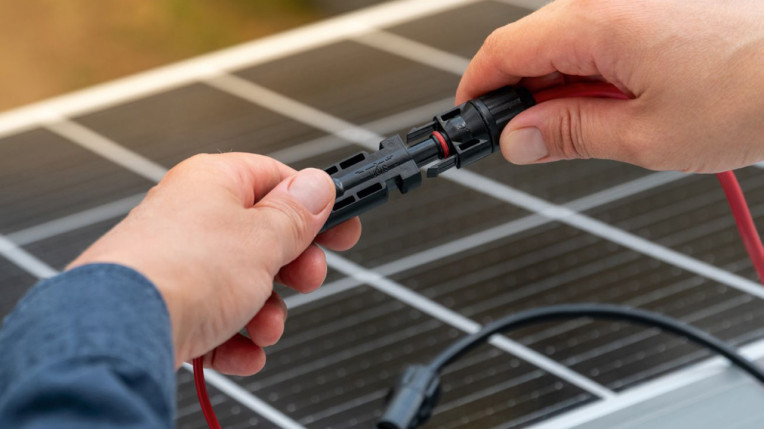
Materiały obudowy
W przypadku obudów złącz kluczowy jest materiał, z jakiego zostały wykonane, od właściwości którego zależy ich wytrzymałość mechaniczna i odporność na czynniki środowiskowe. Jest to zwykle metal albo tworzywo sztuczne. Złącza w obudowach z metali są cięższe niż z tworzyw sztucznych. Pierwsze sprawdzają się jednak w razie narażenia na duże siły ciągnące oraz ekstremalne temperatury, a przy okazji pełnią funkcję ekranu.
Popularny materiał to aluminium, co wynika z jego właściwości. Jest to materiał o gęstości oraz sztywności równej jednej trzeciej tych parametrów stali, plastyczny, a dodatkowo łatwy w obróbce. Czyste aluminium charakteryzuje duża odporność na korozję. Wynika to stąd, że jego powierzchnia samoczynnie pokrywa się bardzo cienką – o grubości zaledwie kilku nanometrów, lecz jednocześnie szczelną i ściśle przylegającą do podłoża – warstwą ochronną tlenku. Powłoka ta przeciwdziała postępowi rdzewienia. W przypadku uszkodzenia następuje jej szybka odbudowa.
W agresywnych środowiskach nie stanowi to jednak wystarczającego zabezpieczenia przed korozją. Dlatego obudowy z aluminium są poddawane dodatkowej obróbce poprawiającej jego właściwości, np. anodowaniu, malowaniu proszkowo lub pokrywaniu różnymi powłokami, m.in. niklową, niklowo-teflonową oraz z natryskiwanego plazmowo tlenku tytanu. Te ostatnie np. cechuje duża wytrzymałość na oddziaływania mechaniczne. Obudowy złączy wykonuje się również ze stali nierdzewnej, a jeżeli koszt złącza ma mniejsze znaczenie niż jego waga, jak m.in. w wyposażeniu samolotów – z tytanu.
Osłony z tworzyw sztucznych, wzmacniane np. włóknem szklanym, są natomiast tańsze i lżejsze niż metalowe. Ich zastosowanie ogranicza jednak z reguły temperatura pracy, brak ekranowania, zmiana koloru oraz osłabienie struktury pod wpływem promieni UV.
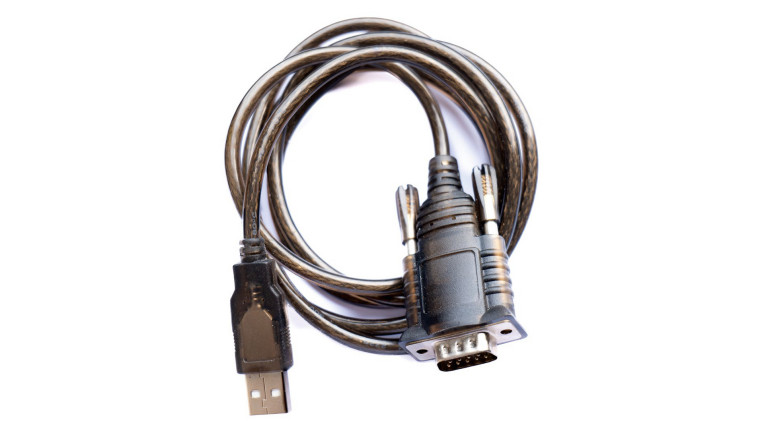
Wibracje, szczelność
W zakresie zabezpieczenia przed wibracjami stosuje się z kolei mechanizmy blokujące. Standardowy pojedynczy ma dźwignię (rygiel) z przodu albo z boku obudowy. Ruch dźwigni powoduje zamknięcie obudowy i osłony. Podwójne systemy blokowania mają dwie dźwignie.
Złącza wodoodporne oraz pyłoszczelne są chronione uszczelnieniami z tworzyw sztucznych. Ich skuteczność charakteryzuje dwucyfrowy stopień ochrony IP. Pierwsza cyfra w jego zapisie, 5 albo 6, opisuje odpowiednio pyłoodporność oraz pyłoszczelność, natomiast druga, z przedziału 0-9, wodoszczelność przy różnym nasileniu oddziaływania wody – od pojedynczych kropel, przez polewanie strugą wody, po pełne w niej zanurzenie.
Przykładowo, złącza z gwarantowanymi stopniami ochrony IP67 i IP68 są pyłoszczelne, ale pierwsze jest odporne jedynie na krótkotrwałe zanurzenie w wodzie, natomiast drugie pozostanie wodoszczelne nawet przy ciągłym. Największą szczelność gwarantują złącza hermetyczne uszczelniane szkłem, ceramiką lub żywicą. Projektuje się je również tak, by wytrzymały wysokie ciśnienie.
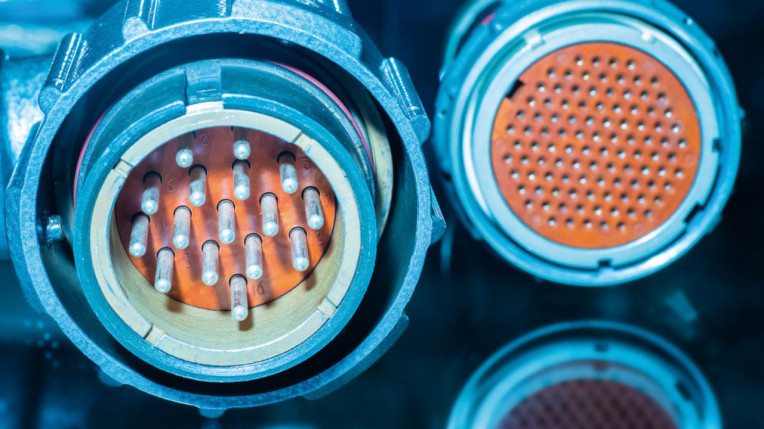
Popularne są szczególnie złącza z uszczelnieniem szklanym. Zalety tego materiału to: trwałość, wytrzymałość mechaniczna, wysoka temperatura pracy. Proces uzyskiwania hermetyczności polega na topieniu szkła w piecu do czasu, aż wypełni ono przestrzeń pomiędzy kontaktami i obudową wkładki, a między szkłem i metalem powstaną trwałe wiązania. Wtedy temperatura jest obniżana, aż do schłodzenia wkładów. Aby uzyskać szeroki zakres temperatur pracy, szkło i metal powinny charakteryzować się zbliżonymi wartościami współczynników rozszerzalności cieplnej. Zapobiega to niekontrolowanym naprężeniom oraz przesunięciom komponentów wkładek złącz przy zmianach temperatury.
Celem konstruktorów złącz dopuszczonych do użytku w atmosferze wybuchowej jest natomiast wykluczenie możliwości powstania iskry i otwartego płomienia. Przykładowe rozwiązanie stanowi ich umieszczenie w ognioszczelnej osłonie. Projektuje się ją tak, żeby styki wkładek zostały rozłączone, zanim będzie ona zdjęta. Oprócz tego, na wypadek eksplozji wewnątrz osłony gniazdo wykonuje się w taki sposób, by wytrzymało ciśnienie wybuchu.
Monika Jaworowska