ZAŁOŻENIA SYSTEMU
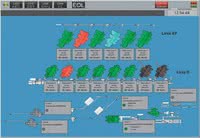
Rys. 1. Wizualizacja obszaru produkcyjnego
Omawiany system, zgodnie z oczekiwaniami ze strony klienta, powinien:
- zapewnić aktualizowaną na bieżąco informację o wydajności parku maszynowego mierzonej wskaźnikami OEE (Overall Equipment Effectiveness),
- oprzeć się na danych pobieranych bezpośrednio z układów sterowania maszyn,
- wyeliminować dokumentację operacyjną tworzoną dotąd ręcznie przez operatorów linii,
- powiązać system z danymi pozyskiwanymi z systemu ERP (SAP) w formie arkuszy Excel,
- zapewnić na liniach produkcyjnych przejrzystą wizualizację aktualnego stanu maszyn i osiąganych wskaźników OEE,
- udostępnić elastyczny i wszechstronny system raportów, w tym tworzenie raportów ad-hoc,
- udostępnić dane uprawnionym użytkownikom w sieci korporacyjnej bezpośrednio w oknie przeglądarki internetowej,
- zapewnić narzędzia do samodzielnej rozbudowy systemu.
KONFIGURACJA SYSTEMU
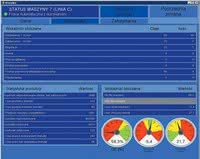
Rys. 2. Wizualizacja stanu maszyny
System obejmuje obecnie 77 maszyn, przy czym można je podzielić na kilka grup ze względu na typ sterowników stanowiących fabryczne wyposażenie maszyn oraz dostępne w tych sterownikach mechanizmy transmisji danych (patrz tabela). Jądrem systemu jest serwer OEE zrealizowany na platformie serwera Fujistu Primergy TX150 z systemem MS Windows Serwer 2008 Standard 64-bit i silnikiem bazy MS SQL Server 2008 Standard.
Serwer OEE pełni następujące funkcje:
- długookresowa archiwizacja w bazie SQL danych służących do wyznaczania wskaźników OEE,
- prowadzenie dla każdej maszyny aktualnej statystyki produkcji (wielkość produkcji, liczba odrzutów, czas pracy, czas postoju, itd.),
- prowadzenie dla każdej maszyny aktualnej statystyki awarii z podziałem na zatrzymania krótsze niż 10 minut i dłuższe niż 10 minut,
- udostępnianie stanowiskom sieciowym informacji o aktualnym statusie pracy poszczególnych maszyn (Praca, Postój, Awaria, Brak komunikacji),
- wyliczanie na bieżąco dla każdej z maszyn trzech wskaźników: OE[%], strata prędkości maszyny, czas stracony (rework) i udostępnianie ich stanowiskom sieciowym do wizualizacji ,
- tworzenie raportów O EE, zarówno automatycznie jak i na żądanie operatorów; raporty są tworzone w różnych przekrojach i stosują szeroki wachlarz sposobów prezentacji danych:
- raporty dla maszyny/operatora/produktu/linii produkcyjnej,
- raporty zmianowe/dzienne/miesięczne/roczne,
- tabele/rozkłady Pareto/wykresy.
Akwizycję danych z obiektu realizują dwa sterowniki Simatic S7-315 (tzw. PLC Gateway), które odczytują dane z praktycznie wszystkich maszyn i wykorzystując sprzęg Ethernet przekazują je dalej do serwera OEE bez jakiegokolwiek pośredniego przetwarzania.
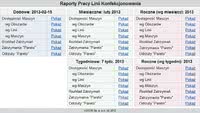
Rys. 3. Menu wyboru raportów
Pozostałe elementy systemu stanowią tzw. stanowiska sieciowe, czyli praktycznie wszystkie komputery funkcjonujące w sieci korporacyjnej klienta, w tym komputery użytkowane bezpośrednio przy liniach produkcyjnych, na których uprawnieni użytkownicy, posiłkując się wyłącznie przeglądarką internetową, uzyskują dostęp do wizualizacji i raportów OEE ewentualnie funkcji specjalnych, jak deklarowanie asortymentu wyrobów produkowanych na poszczególnych maszynach czy przypisanie operatorów do maszyn.
Aktualnie serwer OEE jest skonfigurowany do jednoczesnej obsługi dziesięciu stanowisk sieciowych. System rozpoznaje cztery poziomy uprawnień użytkowników (Operator, Lider linii produkcyjnej, Supervisor obszaru, Administrator systemu) i na tej podstawie decyduje o zakresie korzystania z funkcji systemu. Zgodnie z życzeniem klienta użytkownicy wszystkich kategorii mają nielimitowany dostęp do ekranów synoptycznych oraz do raportów.
WIZUALIZACJA PARKU MASZYNOWEGO
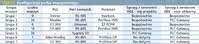
TABELA. Konfiguracja parku maszynowego
Wizualizacja aktualnego stanu parku maszynowego jest zorganizowana hierarchicznie, poczynając od syntetycznego obrazu całego zakładu, poprzez poszczególne obszary produkcyjne do pojedynczej maszyny. Dane zależnie od swojego charakteru są odświeżane w cyklu 5 do 30 sekund. Przykłady wizualizacji na poziomie obszaru produkcyjnego i poziomie maszyny prezentują ekrany synoptyczne (rys. 1 i 2).
RAPORTOWANIE WSKAŹNIKÓW OEE
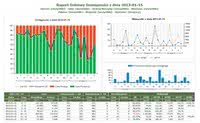
Rys. 4. Raport dobowy dostępności maszyn
Wizualizacja bieżącego stanu parku maszynowego stanowi narzędzie pracy przede wszystkim dla operatorów maszyn i liderów linii. Oczywiście z wizualizacji korzysta także kadra zarządzająca produkcją i utrzymaniem ruchu, ale dla tej grupy użytkowników szczególnie użyteczne są raporty udostępniane przez system MES-OEE.
Zestaw raportów dostępnych w aktualnej fazie wdrożenia jest widoczny na zamieszczonym menu wyboru raportów (rys. 3). Na kolejnych rysunkach (rys. 4, 5, 6) zamieszczono przykłady trzech spośród wielu dostępnych raportów. Z jednej strony pokazują one różnorodność form prezentacji informacji a jednocześnie stanowią ilustrację zastosowania techniki tzw. eksploracji informacji.
Wszystkie raporty są opracowane w sposób pozwalający użytkownikowi na eksplorację informacji - kolejne poziomy uszczegółowienia informacji można uzyskać albo posługując się menu "kryteriów wyboru" konsekwentnie zamieszczanym tuż poniżej tytułu raportu, albo bezpośrednio klikając na aktywne elementy wykresów/tabel (aktywnymi elementami są np. wszystkie słupki na wykresie Pareto pokazanym na rys. 5).
Klikając w raporcie z rys. 5 w słupek reprezentujący najbardziej ważący rodzaj odrzutu natychmiast otrzymamy raport z rysunku 6 zawężający wyniki analizy do tego konkretnego odrzutu i pokazujący, na której z maszyn i w jakich okresach czasu mieliśmy najczęściej z tym problemem do czynienia. Oczywistym faktem jest możliwość wydrukowania raportu na dowolnym etapie analizy, drukowanie raportów wielostronicowych czy opublikowanie raportu w formie elektronicznej, którą można przesłać dalej pocztą elektroniczną.
WNIOSKI Z WDROŻENIA
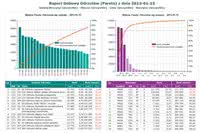
Rys. 5. Raport Pareto dobowy (tylko 1. z 3 stron)
Wdrożenie systemu przyniosło szereg wniosków i doświadczeń, w tym niekoniecznie oczywistych. Na pierwszym miejscu należy wymienić wiele problemów z akwizycją danych. Według pierwotnych założeń wszystkie maszyny mające własne sterowniki PLC miały być podłączone do serwera OEE bezpośrednio, zależnie od posiadanego portu komunikacyjnego przez sieć Profibus FMS/DP lub Ethernet.
Tylko maszyny niemające na wyposażeniu własnego sterownika (w tabeli maszyny te, stanowiące blisko 30% parku maszynowego, połączono w grupę nr 5) miały być obsługiwane przez zewnętrzny sterownik Simatic S7-300 (PLC Gateway), do którego z każdej maszyny doprowadzono 3 podstawowe sygnały dwustanowe: Postój, Praca, Awaria.
W trakcie realizacji systemu okazało się, że niekompatybilności/błędy w oprogramowaniu firm trzecich (Moeller/Siemens) uniemożliwiają bezpośrednią komunikację serwera OEE ze sterownikami marki Moeller. Jedynym wyjściem okazało się przeniesienie komunikacji do sterownika PLC Gateway. W tej sytuacji również komunikację z maszynami grupy nr 4 przeniesiono do PLC Gateway i odinstalowano w serwerze OEE procesor komunikacyjny Profibus, co z kolei pozwoliło zastosować 64-bitową wersję systemu operacyjnego Windows i tym samym poprawić warunki pracy silnika bazy SQL.
Problemy stwarzały także wtyczki Profibus systemu Fast Connect w połączeniu ze sztywnym kablem Profibus dedykowanym do zastosowań w przemyśle spożywczym - parokrotnie nie zapewniały kontaktu i ostatecznie wymieniono je na klasyczne wtyczki. Jednakże najbardziej uciążliwe okazały się skutki błędów w oprogramowaniu firmowym sterowników maszyn, które objawiały się chwilowymi przekłamaniami niektórych wartości liczników.
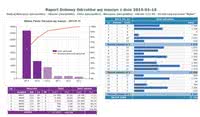
Rys. 6. Raport Pareto dobowy odrzutów dla konkretnego odrzutu
Usunięcie tych błędów wymagało nawiązania współpracy z zagranicznym dostawcą maszyn. Konieczne okazały się także zmiany w pierwszej wersji systemu, gdy wyszło na jaw, że od czasu do czasu klient dokonuje przemieszczenia maszyn pomiędzy liniami produkcyjnymi. Pod kątem tej cechy nieujętej w pierwotnej specyfikacji należało zmienić strukturę bazy danych, wprowadzić elastyczną konwencję nazewnictwa maszyn stosowaną na ekranach synoptycznych i dostosować system raportowania.
Problemy rodziło także ręczne wprowadzanie na liniach produkcyjnych danych o produktach. Brak dyscypliny pracowników praktycznie uniemożliwia wyliczenie pełnych raportów OEE. Nie wdając się z braku miejsca w bliższe omówienie tego tematu, można stwierdzić, że jedynym w pełni skutecznym rozwiązaniem będzie zrealizowanie sprzęgu z systemem SAP i automatyczne wprowadzanie danych o produktach do systemu MES-OEE.
SYSTEM ASIX.EVO
Oprogramowanie aplikacyjne MES-OEE wykonane zostało na bazie systemu Asix.Evo, produkcie opracowanym i rozwijanym przez firmę ASKOM. Pakiet Asix ma wiele atutów ułatwiających tworzenie zaawansowanych systemów monitorowania wskaźników OEE, takich jak: wydajny historian, środowisko do tworzenia raportów oparte na standardzie Microsoft Reporting Services czy technologii pozwalającą na natychmiastowe udostępnienie opracowanej wizualizacji w przeglądarce internetowej.
Zainteresowanych Czytelników odsyłamy do witryn: www.askom.com.pl i www.asix.com.pl a także zapraszamy do spotkania na targach Automaticon.
Janusz Mierzwa
Askom Sp. z o.o.
www.askom.com.pl