Pierwszym etapem w unikaniu wypadku w miejscu pracy jest ograniczenie dostępu do stref niebezpiecznych zagrażających życiu i zdrowiu pracownika - np. strefy pracy robota przemysłowego czy prasy hydraulicznej. Najlepiej do tego zadania nadają się modułowe systemy wygrodzeń, projektowane specjalnie i indywidualnie na zamówienie każdego klienta.
![]() Fot. 1. System wygrodzeń Basic |
![]() Fot. 2. Zamek Schmersal AZM415 |
Zapewniają one maksymalne wykorzystanie dostępnej przestrzeni oraz pozwalają na bezpieczny dostęp do miejsc obsługiwanych przez człowieka. Dodatkowo, w celu zwiększenia bezpieczeństwa przy wchodzeniu do stref niebezpiecznych, stosuje się różnego rodzaju microswitche montowane przy drzwiach, które powodują wyłączanie maszyn podczas pobytu pracownika. Ponadto szereg zamków klasy III oraz IV czuwa dodatkowo nad wyłączeniem maszyn. Spełniają one wszystkie wymogi unijne.
Kolejnym rozwiązaniem jest zastosowanie kurtyn świetlnych, zgodnych z wprowadzonymi dyrektywami i normami unijnymi dotyczącymi bezpieczeństwa pracy. Fotoelektryczne kurtyny i bariery świetlne zostały zaprojektowane z myślą o ochronie operatorów maszyn oraz osób postronnych przed uszkodzeniami ciała przez ruchome elementy maszyn i urządzeń. Obejmują one urządzenia o różnych rozmiarach stref bezpiecznych oraz rozdzielczości wiązek i mogą być stosowane praktycznie w każdej firmie przemysłowej.
System zabezpieczeń optycznych Grein (kategorii 4) może być z powodzeniem stosowany do zabezpieczania m.in. pras, robotów, urządzeń paletyzujących czy linii produkcyjnych. Bazując na analizie ryzyka, producent maszyny powinien podjąć decyzję odnośnie do charakterystyki technicznej oraz ulokowania bariery lub kurtyny świetlnej. W normach rozróżnione są dwie kategorie ryzyka dla urządzeń ESPE (elektroczułe wyposażenie ochronne):
![]() Fot. 3. Kurtyna świetlna firmy Grein |
![]() Fot. 4. Sygnalizator świetlno-dźwiękowy Pfannenberg PAB 110 |
Kategoria 2 - urządzenia te zapewniają wystarczający poziom bezpieczeństwa w sytuacji, gdy ryzyko wypadku jest stosunkowo niewielkie. Przeznaczone są one do stref, w których ryzyko urazów jest niewielkie lub takich, które nie są przez cały czas dostępne.
Kategoria 4 - zapewnienie wystarczającego poziomu bezpieczeństwa w sytuacji, gdy ryzyko wypadku jest bardzo duże i zachodzi często. Urządzenia kategorii 4 są produkowane w oparciu o najnowocześniejsze rozwiązania techniczne, muszą umożliwiać bezpieczne, całkowite zatrzymanie maszyny lub urządzeń.
W informacji o stanie maszyny i tym samym w trosce o bezpieczeństwo pracowników powinny być stosowane różnego rodzaju sygnalizatory. Mogą to być sygnalizatory świetlne w postaci pojedynczych lamp lub kolumn sygnalizacyjnych, gdzie każdy kolor modułu oznacza konkretny stan maszyny. Plusem zastosowania kolumn sygnalizacyjnych jest możliwość połączenia ich w sieć, dzięki czemu operator na każdym stanowisku może obserwować stan maszyny, nie będąc przy niej.
![]() Fot. 5. Kolumna sygnalizacyjna Werma |
![]() Fot. 6. Grzybek wyłączenia awaryjnego Giovenzana |
Dodatkowo w miejscach o ograniczonej widoczności mogą być stosowane sygnalizatory akustyczne o odpowiedniej głośności i systemie informowania o przeszkodach. Najlepszym rozwiązaniem w większości fabryk są sygnalizatory kombinowane tzn. świetlno-dźwiękowe. Zapewniają one szeroką gamę modulacji dźwięku i rodzaju światła (błyskowe, ciągłe).
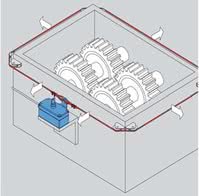
Rys. 1. Zastosowanie wyłącznika linkowego
Ostatnim etapem dbania o bezpieczeństwo pracowników jest zamontowanie awaryjnych przycisków bezpieczeństwa w łatwo dostępnych miejscach. W celu ochrony przed nieumyślnym wciśnięciem mogą one być blokowane przez specjalne obudowy, które zmniejszają prawdopodobieństwo ich załączenia. Tego typu przyciski mogą wyłączać całą linię produkcyjną lub wyselekcjonowane maszyny, zapewniając pracownikom ostateczną ochronę ich zdrowia.
Alternatywą dla "grzybków" bezpieczeństwa są wyłączniki linkowe zatrzymania awaryjnego. Są one często stosowane w systemach transportu bliskiego tj. przy przenośnikach taśmowych. Aktywacja wyłączników polega na pociągnięciu rozciągniętej linki wokół maszyny, dzięki czemu operator nie musi szukać "grzybka" bezpieczeństwa i od razu może wyłączyć maszynę.
Dzięki sprzężeniu bezpośrednio z zestykiem rozwiernym wyłącznika możliwe jest również wykrycie pęknięcia linki. Przy montażu tego typu wyłączników trzeba jednak wziąć pod uwagę rodzaj środowiska pracy, temperaturę otoczenia oraz wymaganą długość linki - czy wymagane jest zastosowanie wyłącznika dwustronnego.
Astat
www.astat.com.pl