Przez wiele lat czeskie miasto Karlowe Wary było najbardziej znanym i modnym uzdrowiskiem na świecie. Od XIV wieku woda lecznicza z dwunastu źródeł jest używana do kąpieli uzdrowiskowych, a od XVI wieku również do kuracji pitnych. Trzynaste źródło, jak mówi się o Becherovce, powstało w 1807 roku, kiedy to Josef Vitus Becher opracował likier ziołowy, który pierwotnie służył jako lek.
Ze względu na brak gorzkiego smaku, likier szybko stał się popularny wśród dużej liczby wiernych konsumentów. Likier pod nazwą Becherovka jest obecnie integralną częścią tradycji kulinarnej Czech i z pewnością można go znaleźć w każdym dobrze zaopatrzonym barze. Od XIX wieku Jan Becher produkuje likier na skalę przemysłową i eksportuje go na cały świat.
W 2001 roku fabryka stała się własnością największego na świecie producenta alkoholi, koncernu Pernod Ricard. Stara fabryka funkcjonuje teraz jako muzeum dla zwiedzających, a produkcja odbywa się w nowoczesnym zakładzie, który otwarto w 2010 roku na obrzeżach Karlowych Warów.
DŁUGI CZAS DOJRZEWANIA LIKIERU, KRÓTKI CZAS NAPEŁNIANIA

Produkcja partii Becherovki trwa od 90 do 100 dni. Najpierw według ściśle tajnej receptury w tzw. komorze lekowej tworzona jest mieszanka około 20 ziół pozyskiwanych z różnych części świata. Mieszanka jest następnie pakowana do ponadgabarytowej torebki przypominającej tę do herbaty i przechowywana przez tydzień w zamkniętym pojemniku z czystym alkoholem, który początkowo jest gorący, a następnie powoli ulega schłodzeniu.
Do alkoholu dodaje się inne składniki, głównie wodę i cukier, a likier pozostawia do leżakowania przez dwa miesiące w dębowych beczkach. Kolejnym etapem jest filtrowanie, po którym likier ziołowy jest schładzany do temperatury -5°C, a następnie przekazywany do centralnej linii napełniającej.
"Sprzedajemy Becherovkę w butelkach o różnych rozmiarach - od miniatur o pojemności 50 ml po znane na całym świecie spłaszczone butelki o pojemności do trzech litrów" - mówi Tomáš Bryzgal, dyrektor zakładu Jan Becher - Karlovarská Becherovka. "Cały proces napełniania jest wysoce zautomatyzowany, począwszy od depaletyzacji pustych butelek po paletyzowanie i etykietowanie napełnionych butelek, aż do przyklejania banderoli akcyzowej".
DOKUMENTACJA I SZACUNKI SPISYWANE RĘCZNIE JAKO ŹRÓDŁO PROBLEMÓW
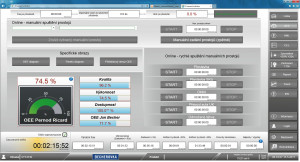
Od momentu zainstalowania linii napełniającej system napełniania został podzielony na dziesięć sekcji. Każda z nich została wyposażona w indywidualny sterownik i zostały one połączone ze sobą za pomocą prostych interfejsów sprzętowych. "Ta konfiguracja działała bardzo dobrze podczas normalnych okresów eksploatacji", mówi Tomáš Bryzgal. I dalej kontynuuje: "Ale zaczęły pojawiać się trudności, które spowodowane były brakiem centralnego dostępu do informacji w przypadku wystąpienia przestojów, np. spowodowanych awarią".
W takich sytuacjach często zdarzało się, że nie można było szybko ustalić przyczyn przestoju. To nie tylko opóźniało proces rozwiązywania problemów, ale również uniemożliwiało późniejsze oszacowanie wydajności systemu. Pracownicy produkcji ręcznie zapisywali informacje dotyczące każdego przestoju systemu. Powodowało to, że w trakcie poszukiwania i naprawy usterki dane nie zawsze okazywały się precyzyjne", przyznaje Bryzgal. "Zwłaszcza okresy przestojów były często dość niedokładnie określone, ponieważ były to głównie szacunki retrospektywne".
Niedogodnością było również to, że pracownicy musieli manualnie przenieść te ręcznie zapisane dane do arkuszy kalkulacyjnych w celu dokonania oceny. Z praktyki wiemy, że formularze te oferują ograniczone możliwości analiz. Ponadto dane i oceny były odizolowane zarówno od systemów informatycznych firmy, jak i systemów automatyki, tak więc nie mogły być bezpośrednio wykorzystane do celów menedżerskich.
WYMAGANY ELASTYCZNY SYSTEM MONITOROWANIA
W celu lepszego monitorowania wydajności systemu i utrzymania go na wysokim poziomie, zarząd zdecydował się zastąpić ten odizolowany system danych nowoczesnym, zintegrowanym kompleksowym rozwiązaniem. W tym celu należało wyposażyć system napełniania i pakowania w nadrzędny system kontroli procesu.
Klient oczekiwał zapewnienia, że nie będzie konieczna zmiana dobrze funkcjonujących podsystemów, w związku z tym rozwiązanie zenon zostało wdrożone bez ingerencji w program sterowników PLC. Założenia projektowe były obszerne, jednak celem nadrzędnym, jaki klient chciał osiągnąć, był centralny monitoring całego systemu napełniania i pakowania wraz z oceną całkowitej efektywności wyposażenia (OEE).
Oczekiwano łatwo dostępnych raportów zawierających między innymi informacje dotyczące oceny czasów przestojów i mikroprzestojów (do 10 sekund) w tym wyświetlanych na wykresie Pareto. Określono również, że system powinien umożliwiać dostęp za pośrednictwem serwera WWW, niezależnie od lokalizacji, ale dla bezpieczeństwa powinien być chroniony przed nieuprawnionym dostępem za pomocą logowania RFID.
OTWARTE OPROGRAMOWANIE ZENON - IDEALNE DOPASOWANIE
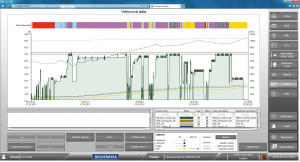
Zamówienie na wykonanie projektu otrzymała firma Kropf Solutions, która w Czechach ma lokalny oddział. Specjalizuje się ona w automatyce przemysłowej i od ponad 20 lat ściśle współpracuje z COPA-DATA. "Oprogramowanie zenon jest dostosowane do elastycznych, otwartych i niezawodnych aplikacji", mówi Ronny Duchek, szef działu technicznego Kropf Solutions, który kierował projektem. "Dzięki temu solidnemu fundamentowi możemy tworzyć rozwiązania szyte na miarę, które są bardzo dynamiczne i ergonomiczne dla naszych klientów".
Pierwszą częścią całościowego rozwiązania dla zakładu Jan Becher było zintegrowanie wszystkich podsystemów w jednym centralnym systemie napełniania i pakowania służącym jako process-gateway i udostępnienie w nadrzędnej sieci zakładowej Ethernet. Pozwoliło to na komunikację systemów produkcyjnych z serwerem oprogramowania zenon, który zapewnia również połączenie z siecią firmy. Przemysłowy panel HMI typu Multi-Touch umożliwia bezpośrednie sterowanie maszynami. Panel ma również czytnik RFID, który służy do logowania się przez użytkownika w oprogramowaniu zenon.
Przedstawiciele klienta końcowego i wykonawca dokładnie testowali projekt zenon jeszcze przed wdrożeniem go do użytku codziennego. W fazie testów pojawiały się kolejne, nowe cele, o których nikt nie myślał na samym początku definiowania zakresu projektu. Jednak ze względu na otwartą strukturę oprogramowania zenon wymagania te można było łatwo zintegrować z wdrażaniem, gdy system był prawie skończony. Kropf Solutions było w stanie przekazać rozwiązanie, które było gotowe do praktycznego zastosowania po bardzo krótkiej fazie testowej.
PEŁNY PODGLĄD DO DANYCH BEZ MANUALNEGO WPISYWANIA DANYCH
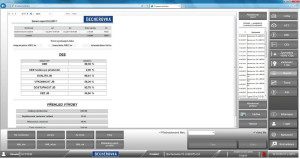
Wdrożony projekt kontroli procesów oparty na oprogramowaniu zenon sprawił, że wszystkie ręczne zapisy, które wcześniej były wymagane, stały się zbędne, ponieważ w pełni automatyczny system w sposób ciągły rejestruje stany pracy wszystkich komponentów w sekundę i bez możliwości wystąpienia błędów ludzkich. Zniknął również etap przekazywania danych do arkuszy kalkulacyjnych, ponieważ gotowe, dostosowane do potrzeb odbiorców analizy są od ręki dostępne w bazie danych tuż po ich zapisaniu w systemie.
Wskaźnik OEE umożliwiający ocenę wykorzystania maszyn jest teraz obliczany według jednego standardu w całej grupie. Inżynierowie z Kropf Solutions zaprogramowali odpowiednie algorytmy w zintegrowanym systemie soft PLC zenon Logic na podstawie predefiniowanych wzorów.
Dane są prezentowane w różnych formach w postaci podglądu na żywo tzw. live lub wykresu trendów: z jednej strony na panelu HMI, a z drugiej w biurach za pomocą dostępu przez przeglądarkę internetową. Przestoje i wymuszone redukcje prędkości linii napełniającej mogą być wyświetlane w postaci szczegółowych widoków, ale również jako wykres Pareto. Niezbędne do działania i kontroli całego procesu produkcji, ale również do podejmowania dalszych decyzji w ramach grupy stanowią automatycznie tworzone i wysyłane dziennie i miesięcznie raporty.
Benefity dla klienta końcowego
|
BAZA DANYCH DO CIĄGŁYCH OPTYMALIZACJI
"Dzięki swojej wszechstronności, możliwości dostosowania się do naszych szczegółowych wymagań oraz przyjaznego dla użytkownika interfejsu, oprogramowanie zenon sprawiło, że nasze procesy produkcyjne są bardziej przejrzyste, a konieczność wykonywania przez pracowników manualnej dokumentacji została usunięta", mówi Tomáš Bryzgal. "Kolejnym krokiem jest wykorzystanie systemu do dalszej optymalizacji procesów produkcyjnych".
COPA-DATA Polska
Więcej na www.copadata.com