Model operacyjny Pharma 4.0 rozpoczyna się od waloryzacji zasobów ludzkich, obejmując następnie systemy informatyczne, organizację i procesy oraz kulturę organizacji (jak pokazano na rys. 1).
Podczas konferencji w Manchesterze prelegenci z całego świata przedstawili spostrzeżenia technologiczne, omówili też trwające badania i przypadki wykorzystania nowego modelu. W wielu wystąpieniach często odwoływano się do koncepcji cyfrowej fabryki. Stało się oczywiste, że do tej pory nie ma jej jasnej definicji. Niektórzy kojarzą tę ideę z wprowadzeniem elektronicznej rejestracji partii, inni z Internetem Rzeczy, a jeszcze inni z uzupełnieniem przedsiębiorstwa o system MES. Wspominano również o pracach podjętych przez BioPhorum na rzecz modelu dojrzałości cyfrowej zakładów (DPMM), który stanowi obraz aktualnej sytuacji związanej z systemami cyfrowymi w produkcji farmaceutycznej.
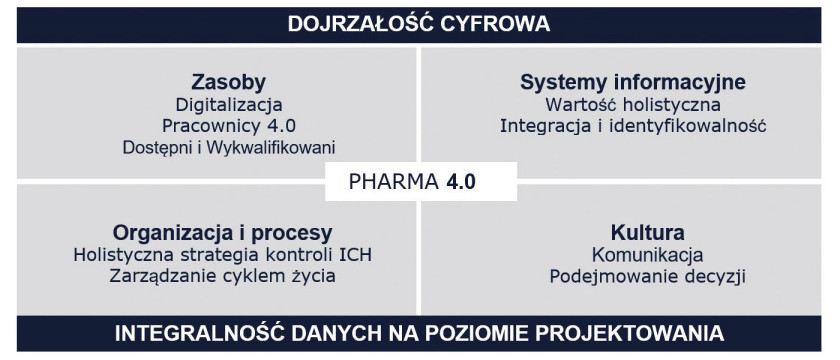
Model dojrzałości cyfrowej zakładów (dpmm)
Koncentrując się jednoznacznie na branży farmaceutycznej, DPMM opisuje kolejne etapy dojrzałości cyfrowej zakładów produkcyjnych, począwszy od tradycyjnej jednostki "opartej na papierze", aż do w pełni zautomatyzowanej i zintegrowanej "adaptacyjnej" fabryki przyszłości.
Stworzony w ramach DPMM model jest przydatnym narzędziem wykorzystującym pięciostopniową klasyfikację do oceny poziomu dojrzałości cyfrowej zakładu. Stosując go, można również zidentyfikować kroki, które należy podjąć, aby zwiększyć fabryczną integrację.
Model DPMM zaprezentowany na rysunku 2 został celowo rozwinięty, aby oprócz stanu obecnego pokazać również założenia dotyczące osiągnięcia etapu zaawansowanego zakładu adaptacyjnego (poziom 5).
Zakład na poziomie 1 charakteryzuje się powszechnym wykorzystaniem czynności manualnych na różnych poziomach organizacji. Na przykład wszystkie działania produkcyjne są prowadzone zgodnie z procedurami spisanymi na papierze, a parametry w instalacjach i maszynach ustawia się ręcznie. Z tego powodu, mimo iż procesy i prace są kontrolowane przez sterowniki PLC i systemy DCS, brakuje systemów HMI, które pozwalałyby na elektroniczne zarządzanie recepturami lub zintegrowanymi funkcjami ścieżki audytu. W takich okolicznościach spełnienie wymagań formalnych dotyczących integralności danych okazuje się niemożliwe.
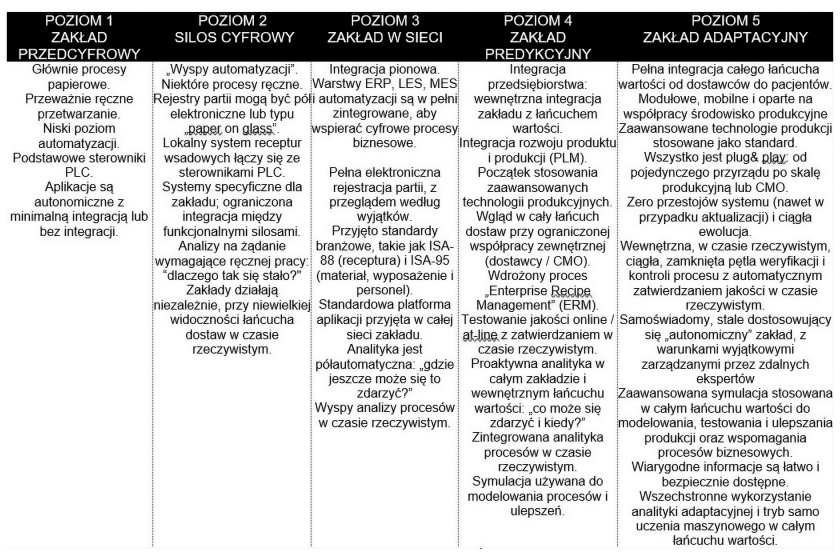
W zakładzie z poziomu 2 zautomatyzowane systemy produkcyjne integrują zarządzanie użytkownikami, recepturami i ścieżką audytu oraz są w stanie wygenerować raport po zakończeniu partii produkcyjnej. Każda maszyna jest tu jednak wciąż izolowaną wyspą. Brakuje integracji danych między systemami operacyjnymi (OT) a systemami IT (np. MES, ERP) oraz integracji poziomej, na przykład między maszynami na linii. Operator musi przemieszczać się wśród urządzeń i na każdym logować, aby wybrać receptury i parametry przetwarzania. Nadzór pracy całej linii wymaga od niego dokładnej znajomości parametrów procesu. Procedury operacyjne i rejestry partii są zwykle sporządzane na papierze. Dane operacyjne niezbędne dla integralności procesu, takie jak ścieżki audytu lub odchylenia od krytycznych parametrów według GMP, pozostają na poziomie maszyny. Taka konfiguracja komplikuje zarządzanie archiwizacją danych i tworzeniem kopii zapasowych według wytycznych GMP.
Na poziomie 3 przepływ danych zaczyna być płynny, ponieważ maszyny na linii produkcyjnej są zarządzane przez jeden centralny system. Operator jest w stanie tworzyć i przesyłać receptury do różnych urządzeń, przeprowadzać operacje i wstępne kontrole, uruchamiać partię produkcyjną i nadzorować pracę linii z jednego stanowiska operatorskiego. System zarządzania linią pobiera dane produkcyjne bezpośrednio z maszyn i przesyła informacje o wszelkich odchyleniach od krytycznych parametrów wytyczonych przez GMP do systemu MES w czasie rzeczywistym. Ścieżka audytu jest scentralizowana w jednym miejscu i może zostać przesłana do elektronicznego systemu rejestracji partii (EBR) zakładu. Faza zatwierdzania partii jest ułatwiona dzięki funkcji "przegląd według wyjątków" (RBE).
Nawet izolowane maszyny i instalacje techniczne, takie jak te związane z produkcją wody, da się zintegrować za pośrednictwem platform do automatyzacji, które mogą bezpośrednio skomunikować ze sobą systemy sterowania i pobierać dane dotyczące krytycznych parametrów GMP, wstępnie je przetwarzać i zarządzać odchyleniami, a także eksportować do systemów IT wyższego rzędu.
Od poziomu 3 zgodność integralności danych staje się łatwa do osiągnięcia i skuteczna.
Poziom 4 pozwala już na optymalizację procesów pod względem jakości, wydajności i zrównoważonego rozwoju. Dzięki szeroko zakrojonej akwizycji i archiwizacji danych produkcyjnych możemy korzystać z nowoczesnych technik uczenia maszynowego i analiz predykcyjnych, które pozwalają przewidywać problemy z jakością i potencjalne odchylenia od parametrów GMP.
Analizując poziom 5, wkraczamy już w technologie przyszłości. Jak widać na rysunku 2, w zakładzie przyszłości digitalizacja rozciąga się poziomo, począwszy od dostawcy do klienta końcowego, którym w branży farmaceutycznej jest pacjent. Nowe maszyny są zintegrowane ze sobą i z systemami nadrzędnymi oraz z chmurą, a procesy produkcyjne stają się zdolne do samoczynnej optymalizacji.
Prawdą jest jednak, że droga do poziomu 5 pozostaje wciąż długa i obecne technologie nie są jeszcze wystarczająco dojrzałe, aby ten poziom osiągnąć.
W kierunku pełnej digitalizacji zakładów farmaceutycznych
Czy istnieją rozwiązania, które można zastosować natychmiast, aby zwiększyć cyfrową dojrzałość fabryki farmaceutycznej bez zbyt obszernej ingerencji w istniejącą infrastrukturę i ponoszenia dużych kosztów? Dla uproszczenia odnieśmy się do procesu produkcji i spójrzmy na kilka przykładów.
Wyobraźmy sobie, że jesteśmy w zakładzie na poziomie 1. Nasze aktywa produkcyjne są niezawodne i wydajne. Mają również znaczną wartość ekonomiczną. Niestety, brak im niezbędnych funkcji zapewniających zgodność z przepisami i regulacjami dotyczącymi integralności danych. Jeśli więc chcemy poprawić działania w zakresie tej integralności i uczynić pierwszy krok w kierunku pełnej digitalizacji, zalecane jest wyposażenie urządzeń w interfejs użytkownika, który ma zaimplementowane takie funkcje, jak: autoryzowany dostęp, synchronizacja czasu, ścieżka audytu, zarządzanie recepturami, gromadzenie danych o krytycznych parametrach GMP i pionową integrację danych z wyższymi poziomami IT.
Rozważmy teraz firmę poziomu 2. Mimo że jej maszyny nie są w sieci (silosy cyfrowe), zakład osiągnął już odpowiedni poziom zgodności pod względem integralności danych. Przyjęcie systemu zarządzania dla linii produkcyjnych – takiego jak system zarządzania liniami produkcyjnymi (Line Management System) – może wówczas uprościć konfigurację nowych partii produkcyjnych (procedury czyszczenia i wymiany za pomocą urządzenia cyfrowego oraz zarządzanie recepturami w całej linii). Ponadto uzyskuje się opcję generowania elektronicznych raportów dotyczących monitoringu pracy linii oraz statusu procesu produkcji, które można dodatkowo udostępnić pionowo do systemów nadrzędnych w zakładzie i zintegrować je z przepływami pracy w całej firmie.
Dla wszystkich systemów, które nie są zintegrowane z linią produkcyjną w firmie poziomu 2, można zaimplementować pionową warstwę integracji danych. Jest to zwykle określane jako platforma integracji automatyzacji Internetu Rzeczy. Dzięki wysokiemu stopniowi komunikacji platforma zachowuje dwukierunkową wymianę danych między różnymi urządzeniami. Będzie ona również pozyskiwać i przechowywać krytyczne parametry wymagane przez GMP, umożliwiać scentralizowane zarządzanie odchyleniami tych parametrów oraz zarządzać i wysyłać grupy ustawień (receptury) do urządzeń. Platforma jest w stanie pozyskiwać dane wprowadzane przez operatorów za pośrednictwem urządzeń mobilnych ("paper on glass"), a dzięki opcji archiwizacji będzie przechowywać informacje potrzebne do stworzenia rejestru partii.
W ten sposób osiągamy poziom 3 zdigitalizowanej produkcji – dzięki pionowej integracji danych, przy użyciu zestandaryzowanych, modułowych i skalowalnych rozwiązań programowych konfigurowalnych jako CAT.4, zgodnie z GAMP5. Kładziemy też podwaliny pod kontynuację naszej podróży do poziomu 4 i 5.
Giuseppe Menin menedżer ds. przemysłu farmaceutycznego w COPA-DATA
COPA-DATA Polska
www.copadata.com