Tam, gdzie na terenie zakładu przemysłowego trzeba często wchodzić w strefę zagrożenia, stosowane są zabezpieczenia eliminujące lub minimalizujące wiążące się z tym ryzyko. Dokonując ich wyboru, warto jednak zadbać o to, by nie utrudniały dostępu do samej strefy. Poniżej przedstawiamy szereg aspektów, na które warto zwrócić uwagę, chcąc zadbać o prawidłowe dystansowanie technicznych środków ochronnych na liniach produkcyjnych.
Obowiązek sprawdzenia poprawności dystansowania
Dla producentów maszyn obowiązek ten wynika z domniemania zgodności przez stosowanie norm zharmonizowanych z Dyrektywą Maszynową. Norma PN-EN 62046 określa m.in. czasokres wykonania pomiarów, natomiast PN-EN 13855 zawiera wytyczne dotyczące prawidłowego dystansowania. Dla użytkowników maszyn (czyli w tym przypadku dla zakładów produkcyjnych) oznacza to obowiązek zapewnienia bezpieczeństwa swoim pracownikom, wynikający wprost z obowiązującego prawa. Jako że poprawne zabezpieczenie urządzeń leży w interesie obydwu stron, często zakłady pracy wymagają okazania raportu z pomiarów, wraz z wykazaniem prawidłowej odległości bezpieczeństwa.
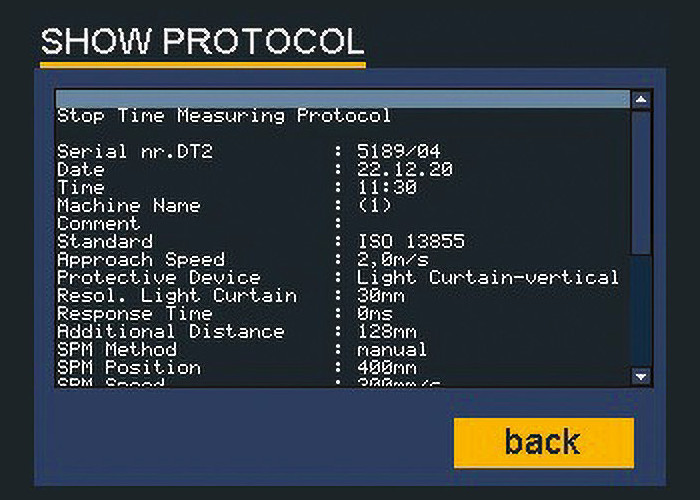
Odległość bezpieczeństwa
Określenie to oznacza np. dystans pomiędzy płaszczyzną wykrywania kurtyny świetlnej a punktem, w którym występuje zagrożenie dla operatora (np. miejscem zgniotu lub pochwycenia). Chodzi o minimalną odległość gwarantującą, że operator nie zdąży dosięgnąć zagrożenia, zanim ono nie zaniknie (np. zatrzymanie suwaka prasy). Odległość bezpieczeństwa wyznaczana jest ze wzoru biorącego pod uwagę prędkość zbliżania (ręki, ciała) oraz czas zatrzymania układu (sterowania, wykonawczego).
Techniczne środki ochronne podlegające dystansowaniu
Do tego rodzaju środków zaliczamy wszelkie urządzenia optoelektroniczne związane z bezpieczeństwem, takie jak kurtyny i bariery świetlne, skanery laserowe, kamery, a także osłony blokujące bez funkcji ryglowania, maty bezpieczeństwa i urządzenia sterowania oburęcznego. Z pewnością powyższa lista będzie się powiększać. Wciąż powstają nowe rozwiązania, które zostaną w przyszłości uwzględnione w normach. Należy przy tym pamiętać, że osłony blokujące z funkcją ryglowania nie wymagają dystansowania ze względu na czas dobiegu. To układ sterowania po zatrzymaniu maszyny zezwala na wejście operatora. Oczywiście nadal monitorowany jest stan osłony – na czas otwarcia staje się niemożliwe ponowne uruchomienie maszyny.
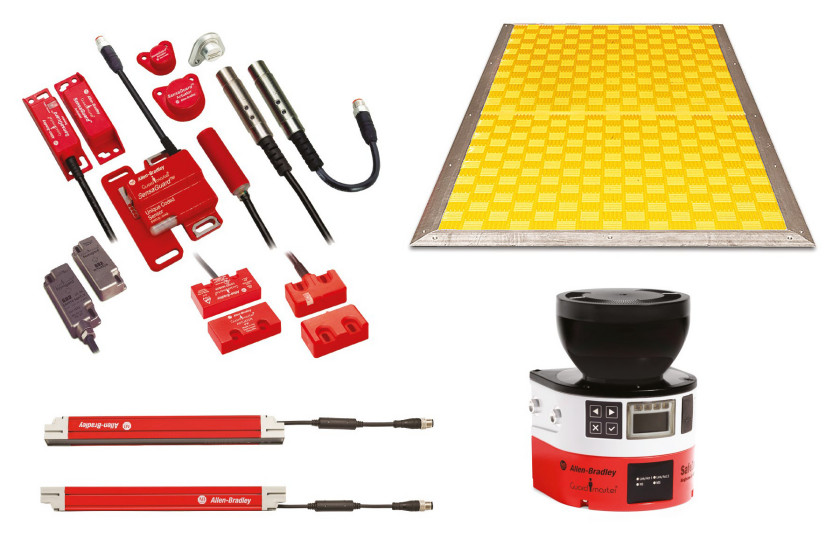
Urządzenie do walidacji odległości bezpieczeństwa
Ogólnie przyjętym sposobem wyznaczenia odległości bezpieczeństwa jest użycie dobiegometru – takiego jak np. safetyman DT2 firmy hhb. Urządzenie to mierzy najpierw czas dobiegu poprzez symulację zadziałania technicznego środka ochronnego (np. kurtyny bezpieczeństwa), a następnie, na podstawie pomiaru, wylicza odległość bezpieczeństwa, zgodnie ze wzorami z normy PN- EN 13855. Wynik oznacza minimalny dystans, jaki musi dzielić kurtynę od zagrożenia. Ruch stanowiący zagrożenie odwzorowujemy za pomocą czujników przeznaczonych do określonego typu ruchu (czujnik linkowy, kołowy, fotokomórka odbiciowa). Symulację zadziałania środka ochronnego wykonuje się za pomocą elektromechanicznego aktywatora.
A jeśli pomiar wykaże niezgodność?
W takiej sytuacji mamy dwa wyjścia. Po pierwsze, możemy oddalić kurtynę od zagrożenia. Rozwiązanie to bywa jednak kłopotliwe, gdyż zazwyczaj wymaga zmian w konstrukcji samej maszyny i może wprowadzić dodatkowe zagrożenia ergonomiczne (pozycja pracy operatora).
Drugą opcją jest próba skrócenia czasu zatrzymania. Być może satysfakcjonujące wyniki da tu wprowadzenie hamulca. Pomocny może się również okazać odpowiedni dobór siłownika i instalacji pneumatyki. Jednocześnie nie należy zapominać o roli jednofunkcyjnych przekaźników bezpieczeństwa. Ich zaletą w tego typu sytuacjach jest stosunkowo krótki czas reakcji. Warto zwrócić też uwagę na parametry techniczne kurtyn, barier i skanerów (takich jak np. response time).
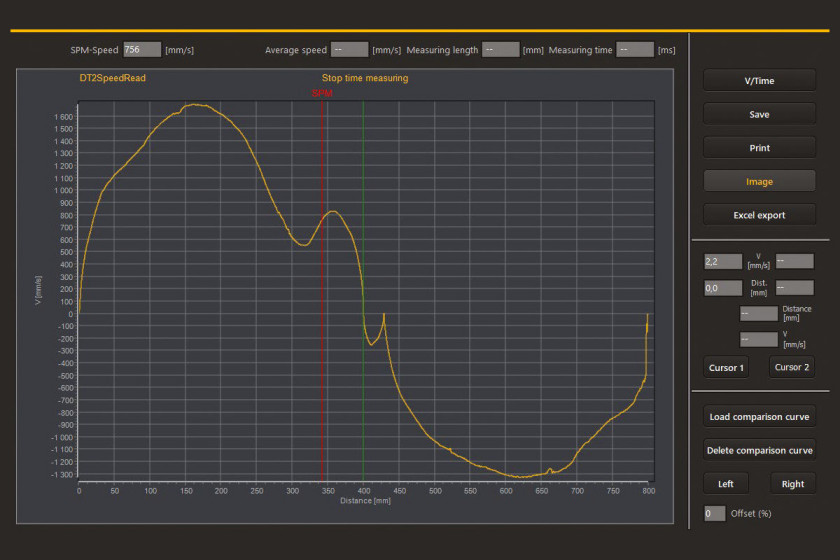
O czym warto pamiętać?
Dobrze jest uwzględnić konieczność walidacji odległości bezpieczeństwa już na etapie projektowania maszyny. Pozwoli to uniknąć kosztownych przeróbek, gdy ta jest już zainstalowana albo nawet uruchomiona. Użytkownik z kolei powinien odpowiednio zaplanować proces kontroli maszyn – tak, by nie wystąpiła kumulacja pomiarów w jednym okresie. Ważnym elementem jest również stworzenie odpowiedniej bazy wiedzy, aby maksymalnie skrócić czas pomiaru na maszynie. Oprogramowanie towarzyszące dobiegometrowi pozwala na zapis protokołów pomiarowych oraz innych przydatnych dokumentów (np. zdjęć lub filmów pokazujących ustawienie czujników).
Zachęcam do skorzystania z naszego wieloletniego doświadczenia w przeprowadzaniu pomiarów z wykorzystaniem dobiegometru. Serdecznie zapraszam też do umówienia się na bezpłatną prezentację urządzenia pomiarowego – w Państwa obiekcie lub poprzez spotkanie online.
Tomasz Drewniok konsultant ds. bezpieczeństwa maszynowego
tdrewniok@racontrols.pl
www.racontrols.pl