Amoniak - klasyczny czynnik chłodniczy
Mleczarnie, rozlewnie, rzeźnie i zakłady produkcyjne z tunelami zamrażalniczymi nie mogą się bez tego obejść - produkcja i przetwórstwo żywności wymagają niskich temperatur podczas przechowywania, do konserwacji lub przy realizacji technologii i procesów specjalnych. Amoniak (wzór chemiczny NH3) jest wykorzystywany do tego celu od ponad stu lat – a ów zasadowy związek azotu i wodoru dominuje dziś na rynku instalacji chłodniczych bardziej niż kiedykolwiek. Nie stanowi to zaskoczenia, ponieważ ten naturalny czynnik chłodniczy, użyty po raz pierwszy przez Carla von Linde w 1870 r. do chłodzenia 0-9, wykazuje szereg zalet.
Amoniak ma dobrą objętościową wydajność chłodniczą i jest bardzo wydajnym chłodziwem, dzięki ciepłu parowania wynoszącemu 1368 kJ/kg.
Uzyskanie wysokiej wydajności chłodniczej wymaga obiegu jedynie niewielkiej ilości amoniaku – ok. 13 do 15% w porównaniu z węglofluorami. NH3 jest dzięki temu bardzo ekonomiczny. Instalacja amoniakalnego systemu chłodniczego pozostaje tańsza o ok. 10 do 20% od podobnych systemów i – co więcej – koszty operacyjne są także znacznie niższe.
Kolejna zaleta: w odróżnieniu od węglofluorów, amoniak jest bardziej przyjazny dla środowiska. Jego potencjał tworzenia efektu cieplarnianego (GWP) i potencjał niszczenia ozonu (ODP) wynoszą zero.
Amoniak - toksyna z ostrzeżeniem zapachowym
Na świecie produkuje się rocznie ponad 130 milionów ton amoniaku i liczba ta wciąż rośnie. NH3 pozostaje jednym z najczęściej produkowanych związków chemicznych i jednocześnie jedną z najczęściej używanych substancji niebezpiecznych w przemyśle. Istnieje kilka powodów tego stanu rzeczy:
1. Zagrożenie wybuchem i pożarem instalacji amoniakalnej
Amoniak jest palny w stanie gazowym - może tworzyć palne lub potencjalnie wybuchowe mieszaniny z suchym powietrzem w zakresie od 15 do 30% objętości. Wymagana temperatura samozapłonu jest jednak wysoka i wynosi 630°C.
Amoniak jest ogólnie lżejszy od powietrza i osiąga atmosferę z wysoką szybkością dyfuzji. W przestrzeniach ograniczonych i zbiornikach może wypierać wszelki dostępny tlen. Wykazuje wysokie powinowactwo do wody i szybko tworzy związki z wilgocią w atmosferze. Jeśli wystąpi wyciek, pary amoniaku są nawilżane kurtynami wodnymi. On sam opada wtedy na podłoże w postaci aerozolu widocznego jako biała mgła.
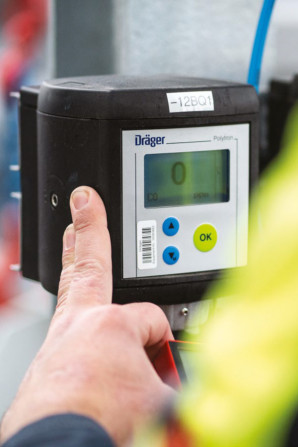
Amoniak ma dość niską palność i płonie nieprzerwanie tylko z płomieniem podtrzymującym. Gdy objętość pary wodnej w powietrzu przekracza 11%, nie powstają palne i potencjalnie wybuchowe mieszaniny. Pomimo masowego użycia amoniaku, wybuchy i pożary spowodowane wyłącznie przez NH3 są bardzo rzadkie. Wszystkie znane incydenty dotyczą prawie wyłącznie przestrzeni zamkniętych. Ryzyko wybuchu istnieje tylko wtedy, gdy stężenie w niewentylowanym pomieszczeniu przekroczy DGW (105 g/m³) lub gdy istnieją źródła zapłonu o dużej energii.
Prace konserwacyjne przy instalacjach amoniakalnych wymagające spawania, lutowania lub cięcia należy wykonywać z wielką ostrożnością: obecne mgły olejowe mogą obniżyć granicę wybuchowości mieszanin NH3/powietrze. Aby usunąć resztki amoniaku, instalacje należy przed rozpoczęciem prac przedmuchać powietrzem lub gazem niepalnym.
Kolejne zagrożenie dla bezpieczeństwa stanowi korozyjne działanie amoniaku na żelazo, miedź, cynk, cynę i ich stopy. Przecieki mogą uszkodzić części instalacji chłodniczej i spowodować niekontrolowane wycieki gazu. Poza perforacjami w postaci dziur, korozja wywołana amoniakiem potrafi powodować powstanie pęknięć korozyjnych – często drobnych i trudnych do wykrycia.
2. Amoniak a zagrożenie toksyczne - zatrucie amoniakiem
Amoniak jest gazem o silnym działaniu drażniącym i żrącym, zarówno w stanie gazowym, jak i ciekłym. Najsilniejsza reakcja zachodzi przy wilgotnych powierzchniach ciała, takich jak błony śluzowe – powstają wtedy bolesne oparzenia chemiczne, np. rogówki, które mogą nawet spowodować ślepotę. Temperatura ciekłego amoniaku wynosi poniżej -33°C i wywołuje poważne odmrożenia skóry. Wdychanie może uszkodzić drogi oddechowe i płuca. Symptomy (lekkiego) zatrucia amoniakiem obejmują uczucie duszenia i problemy z oddychaniem, zawroty głowy, pieczenie gardła, ślinotok, ból brzucha i wymioty. Przedłużone narażanie na działanie NH3 skutkuje uszkodzeniem narządów oddechowych i pokarmowych. W niektórych przypadkach poważne objawy mogą wystąpić kilka godzin po wchłonięciu drogą oddechową. Skażenie powyżej 1700 ppm stanowi już zagrożenie dla życia.
Wypadki śmiertelne z udziałem amoniaku są jednak rzadkie. Z powodu charakterystycznego ostrego zapachu, który można wyczuć w bardzo niskich stężeniach, począwszy od 5 ppm, ludzie zazwyczaj zauważają obecność tego gazu jeszcze poniżej progu stężenia szkodliwego. Ma to swoje zalety, ale i wady, bo niski próg wyczuwalności zapachu może spowodować panikę wśród pracowników, nawet jeśli stężenie nie jest niebezpieczne. To także powód, dla którego niezbędna staje się niezawodna i precyzyjna detekcja – pomaga ona zapobiegać pomyłkom i gwałtownym reakcjom.
Unikanie wypadków dzięki precyzyjnej i szybkiej detekcji wycieku amoniaku
Wycieki amoniaku mogą nastąpić z wielu powodów – korozji, nieszczelności zaworów lub błędów, nawet jeśli układy chłodnicze są należycie serwisowane. Eksperci oceniają, że straty spowodowane wyciekami w złożonych instalacjach chłodniczych wynoszą 2-17% rocznie, w zależności od wieku i stanu instalacji (Ulotka informacyjna stowarzyszenia Euroammon, nr 2 z kwietnia 2016 r. - https://www.eurammon.com/images/eurammon/attachments/02_Ammonia__A_Natural_Refrigerant.pdf). Pęknięcia mogą powstawać po ogrzaniu i rozszerzeniu ciekłego amoniaku uwięzionego w pompach lub liniach podczas przestoju. Inne krytyczne scenariusze obejmują straty zachodzące w wyniku napełniania zbiorników, ich konserwacji i czyszczenia.
Szybka detekcja wycieków amoniaku jest niezwykle istotna. Po pierwsze, co oczywiste, aby uniknąć uszkodzenia instalacji i produktów składowanych w chłodni, należy ograniczyć do minimum wysiłek wymaganego ponownego napełnienia instalacji. Po drugie, wszelkie przerwy w produkcji kosztują – niezależnie od tego, czy wystąpił prawdziwy alarm wskutek niebezpiecznych stężeń, czy też tylko fałszywy. Dlatego właśnie szczególnie wycieki amoniaku należy wykrywać z wysoką precyzją.
Detekcja amoniaku: wyzwanie w ekstremalnych warunkach
Zapewnianie bezpieczeństwa pracy i produkcji w zakładach stosujących instalacje amoniakalne nie jest łatwym zadaniem – wymaga niezawodnego monitorowania substancji toksycznej w trudnych warunkach zmiennych temperatur lub wysokiej wilgotności.
Jednym z fundamentów bezpieczeństwa pozostaje stałe monitorowanie. Najwydajniejszą i najbardziej niezawodną metodą szybkiej detekcji przekroczonych progów i ostrzegania personelu jest stacjonarny system detekcji gazu. Wycieki można lokalizować detektorami noszonymi przez pracowników lub tymczasowo umieszczanymi w punktach krytycznych. W przypadku alarmu wymagane są także właściwe środki ochrony indywidualnej, obejmujące – w zależności od potencjału zagrożenia – maski z pochłaniaczami lub sprzęt izolujący, kombinezony ochrony przeciwchemicznej i aparaty ucieczkowe.
Na co uważać przy instalacji stacjonarnego systemu detekcji amoniaku?
1. Prawidłowa lokalizacja punktów pomiaru NH3
W przypadku amoniakalnych instalacji chłodniczych, głowice systemu detekcji zwykle instaluje się w sprężarkowni i przy stacjach zaworowych, np. aby kontrolować końcówki rur. Czujniki w sprężarkowni są zazwyczaj umieszczane przy suficie, ponieważ amoniak jest o ok. połowę lżejszy od powietrza i szybko unosi się po wycieku. Nawet jeśli pozostaje niewyczuwalny w dolnej części pomieszczenia, stężenia pod sufitem mogą być znacznie wyższe. Przy instalacji głowic należy upewnić się, że czujniki nie znajdują się bezpośrednio w strumieniu powietrza skierowanym do lub od parownika.
2. Źródła potencjalnych zaburzeń
W sprężarkowniach często występują ekstremalne wahania temperatur. Wskutek kondensacji, podczas podgrzewania i chłodzenia powietrza może powstawać wilgoć, która wpływa na wyniki wrażliwych urządzeń. Wilgoć może być także generowana podczas procesów rozmrażania przy parownikach. Jeśli to możliwe, czujniki należy umieszczać w punktach zapewniających najlepszą ochronę przed tego rodzaju czynnikami zaburzającymi.
3. Pamięć o charakterystyce czujnika
Temperatury ujemne, wahania temperatur, wilgoć i korozja – w wymagającym środowisku instalacji chłodniczej nie sprawdzi się każdy czujnik. Jednocześnie, szczególnie w obszarze detekcji amoniaku, bardzo ważny jest wysoki poziom precyzji. Niezawodne wyniki pomiarowe wymagają więc wyboru detektorów gazu charakteryzujących się wystarczającą odpornością, aby sprostać szerokim zakresom temperatur i innym istniejącym wyzwaniom.
4. Wybór właściwych progów alarmowych
W amoniakalnych instalacjach chłodniczych występują często poziomy bazowe z niskimi stężeniami tła. Aby uniknąć fałszywych alarmów, skonfigurowane progi alarmowe należy ustawić odrobinę powyżej poziomu NDS. Wysoka jakość czujnika zapewnia wsparcie dla niezawodnych i precyzyjnych pomiarów i przyczynia się do minimalizacji występowania fałszywych alarmów oraz przestojów w produkcji.
5. Regularna konserwacja
Aby zapewnić niezawodne i precyzyjne pomiary, system detekcji gazu trzeba regularnie kalibrować i konserwować w określonych interwałach. To ważne tym bardziej, jeśli instalacja działa w wymagających warunkach. Opłaca się zainwestować w wyższą jakość serwisu: technicy mający specjalistyczną wiedzę szybciej zauważą i naprawią typowe skutki starzenia oraz oznaki zużycia. Zwiększają tym samym niezawodność urządzeń i przedłużają ich żywotność.
Solidne rozwiązania bezpieczeństwa
W większości wypadków z udziałem amoniaku, substancja niebezpieczna występuje w postaci gazowej. Jeśli spodziewamy się, że w strefie skażonej znajdują się osoby poszkodowane, ich uratowanie uzyskuje najwyższy priorytet. Dla straży pożarnej i innego personelu ratowniczego niezbędny jest sprzęt do ochrony układu oddechowego, niezależny od powietrza otaczającego. Ważny element stanowi tu część twarzowa, która równocześnie bezpiecznie chroni oczy przed kontaktem z atmosferą skażoną. W wielu przypadkach w oczekiwanej sytuacji zagrożenia wymagane są tak czy inaczej gazoszczelne kombinezony ochrony przeciwchemicznej.
Sytuacja staje się bardziej problematyczna, jeśli z instalacji chłodniczych wydostaje się ciekły amoniak. Temperatura cieczy, która wynosi -33°C lub mniej, powoduje po kontakcie ze skórą odmrożenia. Ich stopień pozostaje zależny od powierzchni kontaktu i ilości. Podstawowa odzież ochronna w takich sytuacjach nie wystarczy, ponieważ lodowata ciecz przedostaje się przez materiał. Zalecane są więc kombinezony z materiału odpornego na niskie temperatury. Aby chronić skórę przed odmrożeniem, pod kombinezonem należy nosić ciepłą odzież roboczą, jak również wełniane skarpety i rękawice.
Wybór właściwego pochłaniacza
Personel mający za zadanie wykryć wycieki z uszkodzonych instalacji należy ze względów bezpieczeństwa wyposażyć w indywidualne detektory gazu. Do prac, które wiążą się z ryzykiem wycieku lub nagle ulatniającego się amoniaku – takich, jak otwieranie obiegu chłodzenia – trzeba udostępnić i zastosować środki ochrony indywidualnej, jeśli jest to wymagane.
Obejmują one:
- maskę pełnotwarzową, z wkręcanym pochłaniaczem amoniaku (zielony kolor identyfikacyjny, litera K) i ze zintegrowaną ochroną oczu;
- rękawice ochronne;
- gumowe buty;
- gogle ochronne.
W przypadku alarmu, aparaty ucieczkowe niezależne od powietrza otaczającego zapewniają wsparcie przy zorganizowanej ewakuacji zakładu. Oczyszczające aparaty ucieczkowe chroniące przed gazami toksycznymi również zapewniają bezpieczeństwo osobom ewakuowanym.
Wymagania specjalne potrzebują rozwiązań indywidualnych
Amoniakalne instalacje chłodnicze stanowią szczególne wyzwanie dla zarządzania bezpieczeństwem. Detektory gazu, środki ochrony i aparaty ucieczkowe wymagają indywidualnych rozwiązań uwzględniających specyfikę każdego zakładu. Zarówno nowe instalacje, jak i integracja nowych komponentów z istniejącą infrastrukturą wymagają fundamentalnej wiedzy dotyczącej zasad chemicznych i fizycznych, parametrów technicznych i wymogów prawnych – co oznacza niezwykle złożony proces planowania. Fachowe porady będą jednak warte swojej ceny na każdym etapie: podczas zakupu, montażu, uruchamiania, jak również konserwacji instalacji.
Dräger
www.draeger.com
Źródło: Dräger
Więcej na www.draeger.com