Opis problemu
W omawianym zakładzie zdarzały się sytuacje, gdy operator omyłkowo umieszczał w maszynie kosz z niewłaściwym materiałem, przeznaczonym do dalszej obróbki. Materiał ten planowo miał zostać poddany obróbce dopiero po zakończeniu bieżącego zlecenia (kolejkowanie FIFO). Ze względu na pełne traceability w procesie produkcji elementów dla rynku automotive konieczne jest dokładne dokumentowanie drogi partii/serii części materiału/surowca – od jego dostawy do zakładu aż po partie wyrobów gotowych.
Cel projektu
Efektem planowanego projektu miało być stworzenie rozwiązania, umożliwiającego uzyskanie większej kontroli nad załadunkiem materiału do maszyny, a przede wszystkim pozwalającego na uniknięcie lub maksymalne zminimalizowanie ryzyka umieszczenia w maszynie niewłaściwej partii detali – czyli takiej, która nie była uwzględniona w bieżącym zleceniu produkcyjnym. Każda partia detali umieszczona w osobnej skrzyni ma swój kod kreskowy. Jak każde dopracowane rozwiązanie, przygotowywany system miał z założenia przewidywać sytuacje specjalne, kiedy dochodzi np. do utraty połączenia z systemem zleceń lub braku zlecenia w samym systemie. W oparciu o powyższe, klient oczekiwał również pełnej archiwizacji nadzorowanych zdarzeń.
Dobór rozwiązania – OPC router
Do projektu wybrano oprogramowanie OPC Router, niemieckiej firmy INRAY. W sposób bezpieczny, poprzez interfejs OPC UA (program jest OPC UA klientem, ale może też być serwerem), sięga ono do serwera OPC UA po dane ze sterownika PLC. Modułowa budowa tego narzędzia oraz liczne pluginy (wtyczki) prawie zawsze pozwalają wyeliminować konieczność jakiegokolwiek ręcznego programowania – cała logika tworzona jest w sposób graficzny na schemacie blokowym. Drugim z wykorzystanych pluginów (poza OPC) był zaimplementowany gotowy plugin do obsługi skanerów kodów kreskowych firmy Zebra. Kolejnym – interfejs do komunikacji z bazami danych MS SQL, a ostatnim – plugin do programu MS Excel.
Wdrożenie rozwiązania
Uzyskane ostatecznie rozwiązanie, w oparciu o OPC Router i komunikację z PLC (Siemens SIMATIC S7) za pośrednictwem serwera OPC, odpowiednio zezwala lub blokuje wjazd kosza z materiałem do maszyny. Po zeskanowaniu kodu kreskowego znajdującego się na etykiecie produkcyjnej kosza z detalami i porównaniu go ze zleceniami aktualnie zalogowanymi w systemie zarządzania zleceniami produkcyjnymi MPDV (Hydra) uniemożliwiamy operatorowi załadunek niewłaściwego materiału. Wszystkie próby załadunku są dodatkowo archiwizowane, pozwalając na śledzenie historii procesu załadunku.
Projekt obejmował również dostarczenie i montaż prostych szafek elektrycznych, na których zamontowano skanery kodów kreskowych (Zebra), obsługiwane przez OPC Router, lampki informujące operatora o stanie systemu (łączność z bazą danych), o możliwości załadunku lub o nieprawidłowości zlecenia oraz stacyjkę z kluczykiem, pozwalającą na ominięcie działania systemu w przypadku jego awarii lub przezbrojenia maszyny na inne zlecenie. Integracja systemu w zależności od maszyny była wykonana poprzez modyfikację programu sterującego maszyny (S7-300) lub fizyczny szlaban, który uniemożliwia wykonanie załadunku wózkiem widłowym (sterowanie szlabanem realizowane jest poprzez sterownik PLC Siemens S7-1200 – serwer OPC z protokołem S7 – OPC Router).
OPC Router jest "mózgiem" całego systemu kontroli – odbiera kod kreskowy, szuka zleceń w bazie MSSQL, podejmuje decyzję o zezwoleniu na załadunek i wysyła ją do serwera OPC (sterownika PLC), zbierając przy tym niezbędne dane. Z zebranych danych przygotowuje raporty w arkuszach Excel i przesyła je protokołem SMB bezpośrednio na komputery osób nadzorujących proces.
Podsumowanie
Poza poprawnie zrealizowanym celem projektu klient uzyskał wartość dodaną w postaci oprogramowania OPC Router, pozwalającego w prosty sposób, bez konieczności programowania, dodawać, modyfikować, jak również monitorować przepływ danych pomiędzy źródłem (w tym przypadku skaner kodów i sterownik PLC) a systemem zarządzania zleceniami. Za pomocą przedstawionych na schemacie (rys. 1) pluginów (wtyczek) można realizować dowolną dwukierunkową wymianę informacji. Każda z tych informacji może być wielokrotnie użyta w różnych wtyczkach. Jedynym ograniczeniem pozostaje kreatywność inżyniera, który z udziałem OPC Routera jest w stanie wykonać bardzo dużo różnych zadań.
Firma INEE jako preferowany dystrybutor i wieloletni partner firmy INRAY zamierza od trzeciego kwartału 2022 r. rozszerzyć swoją ofertę szkoleniową. Poza szkoleniami z komunikacji przemysłowej, opartej o standard OPC i bazującej na rozwiązaniach firmy Kepware, planuje więc wprowadzić szkolenia oparte właśnie o to potężne, aczkolwiek bardzo przyjazne narzędzie, jakim jest OPC Router.
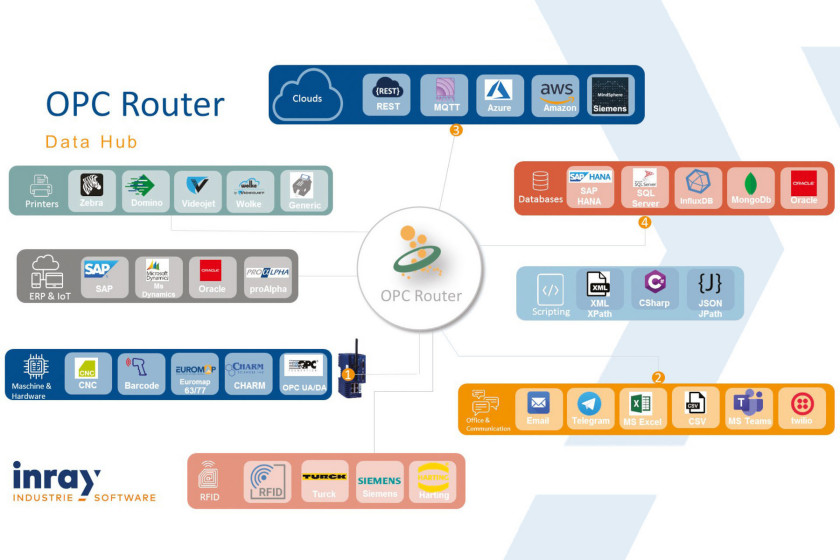
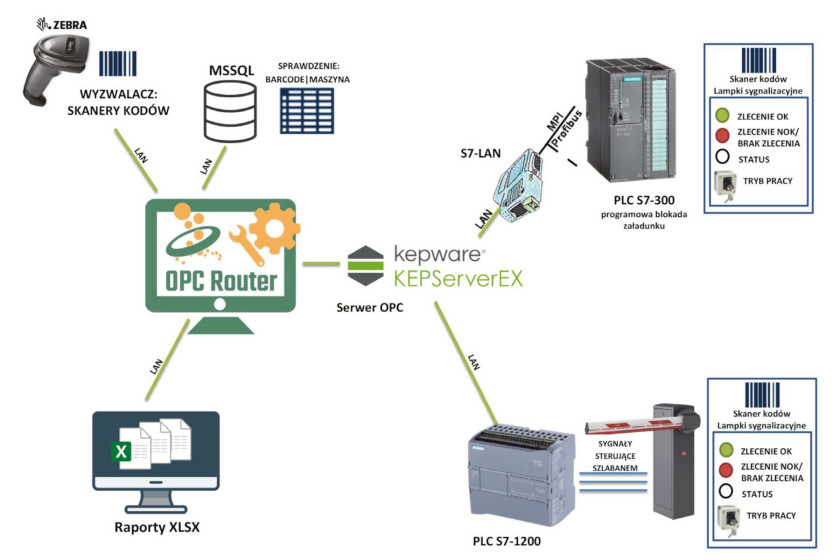
Marcin Szendzielorz
Krzysztof Kuźniarz
INEE Sp.z o.o.
www.inee.pl
info@inee.pl
tel. 32 235 45 60