Dżungla komponentów
Chociaż każdy zakład przemysłowy stara się wprowadzić jakąś standaryzację urządzeń, większość z nich napotyka na swojej drodze wiele barier. Mniejsze firmy często korzystają z maszyn czy nawet całych linii produkcyjnych z rynku wtórnego. Z kolei zakłady z zagraniczną centralą nierzadko dostają urządzenia „w spadku” z likwidowanych lub modernizowanych lokalizacji. Ci zaś, których teoretycznie byłoby stać na wszystko i są niezależni, borykają się z brakiem dostępnych podzespołów na rynku i czasami dostaw na poziomie 12 miesięcy i dłużej.
Skutkuje to sięganiem po systemy sterowania tych producentów, którzy są w stanie dostarczyć urządzenia szybciej niż inni – i odchodzeniem od standaryzacji. W typowej hali przemysłowej spotkać można sterowniki PLC przynajmniej dwóch lub więcej producentów, dodatkowe sterowniki wagowe, a często jeszcze zupełnie inne systemy automatyki budynkowej, przeróżne czujniki, skanery kodów i wiele innych elementów, które są od siebie odseparowane albo połączone w mniejsze grupy lub systemy niepołączone w całość. Tymczasem idea Industry 4.0 dąży do wszechobecnej integracji, która pozwala na lepszą widoczność i transparentność procesów (nie tylko produkcyjnych), a w kolejnych etapach – zdolność do przewidywania zdarzeń i maksymalnie automatycznej adaptacji do zmieniających się potrzeb i warunków.
W komunikacji siła
Mając wiele rodzajów urządzeń i systemów w fabryce lub kilku fabrykach i chcąc efektywnie nimi zarządzać, potrzebujemy rozwiązania, które zapewni pewną, stabilną i bezpieczną komunikację oraz centralne miejsce, gdzie będą trafiać dane pochodzące z różnych źródeł, a następnie będą przetwarzane, archiwizowane i analizowane (już niekoniecznie w tym samym miejscu).
Takim rozwiązaniem jest KEPServerEX firmy Kepware (grupa PTC), występujący także pod nazwą ThingWorx Kepware Server. To nie tylko znakomity serwer i klient OPC UA/DA, ale też platforma komunikacyjna, pozwalająca na obustronną wymianę danych (odczyt i zapis) ze sterownikami PLC różnych producentów (m.in. firm Siemens, Allen-Bradley, Mitsubishi, Fanuc, Omron, Wago, Yokogawa), modułami wagowymi, systemami HVAC i BMS (np. po protokole BACnet), systemami DCS, terminalami RTU, a także maszynami CNC (np. Fanuc FOCAS, Euromap 63/77). Oprócz wszystkich tych urządzeń, oprogramowanie firmy Kepware komunikuje się z różnego typu bazami danych (np. przez ODBC) i systemami HMI (wizualizacja), SCADA czy MES (najczęściej przez OPC UA). Możliwa jest również wymiana danych procesowych z chmurą, np. Microsoft Azure, Amazon (AWS), MindSphere itp. z wykorzystaniem protokołów REST i MQTT.
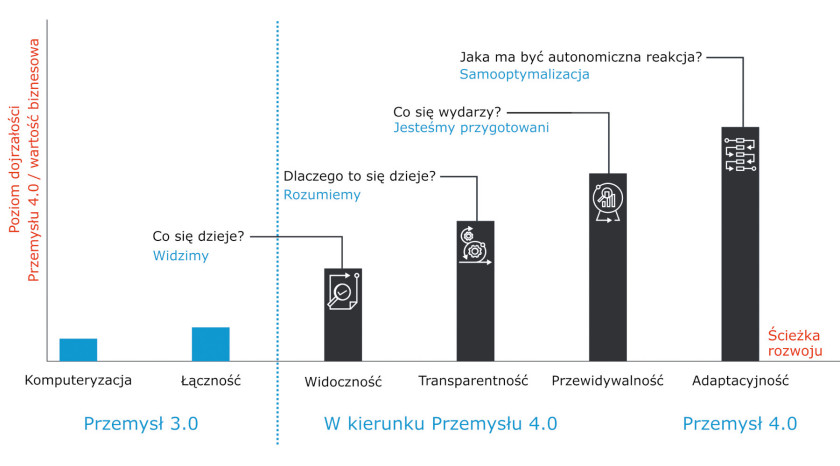
Liczby nie kłamią
Używany w ponad 75 tys. lokalizacji na całym świecie, KEPServerEX – z wbudowanymi zabezpieczeniami, skalowalnością i biblioteką ponad 150 sterowników i zaawansowanych wtyczek, obsługujących ponad 300 protokołów przemysłowych – zapewnia jedno źródło danych przemysłowych dla wszystkich urządzeń automatyki, maszyn i aplikacji. Dzięki temu jest w stanie sprostać prawie wszystkim wyzwaniom związanym z komunikacją i wymianą danych w przemyśle.
Od danych do pieniędzy
Nie każda firma czuje potrzebę akwizycji danych, monitorowania i analizy produkcji czy tym bardziej wdrażania „jakiegoś tam Przemysłu 4.0”. Jednak właściciele każdego przedsiębiorstwa z pewnością czują potrzebę powiększania zysków i redukcji kosztów.
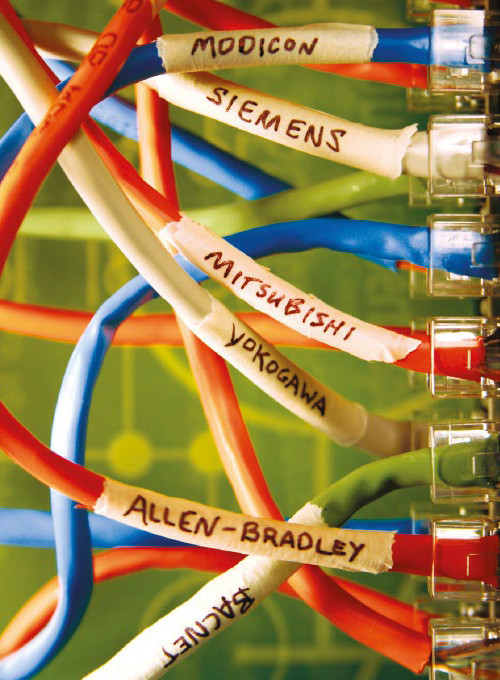
Zastosowanie oprogramowania KEPServerEX jest prostym, szybkim i niedrogim rozwiązaniem, z krótkim czasem wdrożenia i najczęściej z szybkim zwrotem z inwestycji – tym szybszym, im słabiej zdigitalizowana i zoptymalizowana jest produkcja przed jego wdrożeniem.
Jak twierdzi Abby Eon (General Manager w firmie Kepware): „Niezależnie od tego, czy wykorzystujesz nowe technologie, takie jak IoT i AR, czy po prostu automatyzujesz ręczne procesy, cyfryzacja ogranicza liczbę ludzkich błędów, zapewniając wzrost produktywności i jakości”.
Kepware+ i szkolenia
Aby ułatwić i zoptymalizować zarządzanie, firma Kepware wprowadziła niedawno usługę o nazwie Kepware+. Jest to oprogramowanie w chmurze (SaaS), które umożliwia podgląd oraz hurtową aktualizację i modyfikację wszystkich posiadanych konfiguracji serwera OPC KEPServerEX. Szacuje się, że dziesięć serwerów podłączonych do Kepware+ pozwala zaoszczędzić rocznie minimum 96 godzin (12 dni) pracy administratorów.
Zapraszamy do kontaktu, przetestowania wersji demo oraz na szkolenia z komunikacji przemysłowej, bazującej na KEPServerEX.
Krzysztof Kuźniarz
INEE Sp. z o.o.
www.inee.pl