Dlaczego maszyny i systemy powinny być zdigitalizowane i "inteligentne"? Zawsze warto pochwalić się takimi optymalnymi warunkami pracy i jednocześnie osiągnąć sukces marketingowy. Jednak w ostatecznym rozrachunku chodzi o uzasadnienie poniesionych nakładów, trzeba również wykazać wymierne korzyści pieniężne. Tylko wtedy rozwiązania cyfrowe będą rzeczywiście inteligentne.
Dlatego przed podjęciem jakichkolwiek działań należy najpierw sprawdzić procesy, które mają zostać zdigitalizowane. Oczywiste jest, że muszą one mieć znaczenie, ale należy przede wszystkim zwrócić uwagę na ich efektywność i spójność. Możliwe jest również zastosowanie pewnych przemyślanych działań poprzez proste dostosowanie lub modyfikację procesów.
Kluczową motywacją przy wdrażaniu cyfryzacji jest pozyskiwanie informacji: czy to o stanie systemów, maszyn i urządzeń, pozycji produktów, względnie urządzeń, czy np. o statusie zlecenia produkcyjnego. Osiągnięty w ten sposób wzrost przejrzystości nie poprawia jeszcze przepustowości ani wydajności, ale otwiera perspektywę dalszych ukierunkowanych działań.
Rzeczywiste sytuacje panujące dziś w zakładach przemysłowych są zróżnicowane, ale zasadniczo wyróżniają się dwa scenariusze:
- informacje nie są dostępne i muszą być generowane za pomocą odpowiednich czujników, które dodatkowo instaluje się w środowisku produkcyjnym;
- informacje już istnieją, ale nie są dostępne we właściwym czasie lub we właściwej formie tam, gdzie byłyby przydatne.
W obu przypadkach dane należy najpierw zebrać, a potem przechowywać w uporządkowany sposób.
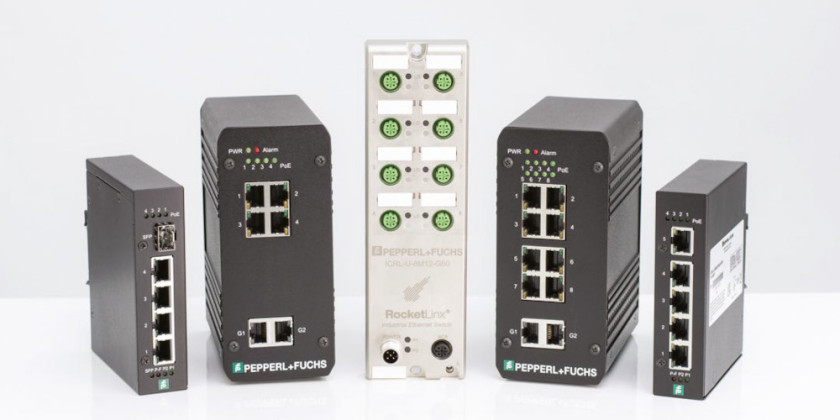
Wiele aplikacji opartych na "inteligentnych" danych wymaga jeszcze większych ilości danych, które muszą być dodatkowo przechowywane przez dłuższy czas. Ponadto często wymagana jest skalowalna wyższa moc obliczeniowa, np. do wykrywania anomalii w systemach konserwacji predykcyjnej. Na poziomie automatyzacji, czyli w sterownikach i komputerach przemysłowych, pamięć i moc obliczeniowa są zwykle ograniczone i drogie. Z drugiej strony, platformy danych oparte na chmurze lub platformy danych obsługiwane "on premise" zapewniają zarówno pojemność pamięci masowej, jak i moc obliczeniową przy stosunkowo niskich kosztach.
Rzeczywiste przetwarzanie danych "IoT" odbywa się zatem w takich systemach informatycznych i należy znaleźć łatwe do wdrożenia sposoby przesyłania danych z poziomu automatyzacji. Mówiąc prościej, informacje są tworzone w hali produkcyjnej i jednocześnie wymaga się ich w biurze, w celu ich przechowywania i dalszego przetwarzania.
W żadnym ze scenariuszy nie trzeba jednak kroczyć zupełnie nowymi ścieżkami, dostępne są już bowiem odpowiednie technologie. Wyzwania polegają na bezpiecznym pokonywaniu granic między automatyką a technologią informacyjną. Te obszary są zwykle zarządzane całkowicie oddzielnie, aby sprostać czasami bardzo różnym wymaganiom. Przykładowo, dwie całkowicie niezależne sieci działają zwykle równolegle.
Konwergencja IT i OT jest napędzana m.in. przez Przemysł 4.0 i IIoT, a obecnie opracowano w tym samym celu także całą gamę koncepcji i rozwiązań.
Inteligentne są tylko rozwiązania otwarte
Oceniając rozwiązania cyfrowe, należy wziąć pod uwagę, że w większości przypadków środowiska produkcyjne są heterogeniczne. Komponenty od różnych wytwórców muszą ze sobą współdziałać bez większych problemów – w przeciwnym razie rozwiązanie może być cyfrowe, ale bynajmniej nie inteligentne.
Dzięki sygnałom wyjściowym, dostarczanym przez czujniki, interoperacyjność jest łatwa do osiągnięcia, poprzez powszechne stosowanie i akceptację znormalizowanych protokołów, takich jak IO-Link, AS-Interface lub magistrale polowe oparte na sieci Ethernet. Za pomocą konwerterów sygnałów lub konwerterów można również zintegrować czujniki z innymi popularnymi sygnałami wyjściowymi w tych standardach. Moduły I/O Ethernet do instalacji w terenie lub w szafie sterowniczej są idealne do konwersji IO-Link na Ethernet.
Podczas gdy standaryzacja znalazła już miejsce w hali produkcyjnej, zastrzeżone łączniki są nadal szeroko stosowane podczas łączenia się z usługami w chmurze. Większość z nich opiera się na znanych, jednolitych i ustandaryzowanych mechanizmach, takich jak interfejsy API MQTT lub REST, ale istnieją zróżnicowane nakłady pracy programistycznej, które są mniej lub bardziej specyficzne dla danej platformy.
Podobnie jest z komunikacją między aplikacjami na poziomie chmury – tutaj też nie ma jednolitych definicji, brakuje również jednolitej semantyki.
Komponenty Przemysłu 4.0 tylko z wirtualną reprezentacją
Interoperacyjna komunikacja w celu dostarczania informacji o zasobach we wszystkich cyklach życia i fazach tworzenia wartości jest długotrwałym i wcześniej nierealizowanym wymogiem automatyzacji. W użyciu pozostaje wiele różnych protokołów lub formatów, a sytuacje zwykle nie są jednolite, nawet w obrębie podobszarów. Wszyscy użytkownicy, tacy jak konstruktorzy maszyn, integratorzy lub operatorzy, wykorzystują w swoich maszynach i systemach różne komponenty różnych producentów. Muszą pracować z wieloma protokołami i formatami danych w celu uzyskania informacji i wdrożenia ścieżek komunikacyjnych. Wdrożenie dostosowań lub konwersji wymaga dużego nakładu pracy, a dane muszą być przepisywane z jednego systemu do drugiego.
Aby przezwyciężyć te problemy, w opublikowanej w 2015 r. "Strategii wdrażania Przemysłu 4.0" wprowadzono warstwę administracyjną jako wirtualną reprezentację zasobów fizycznych. W tym kontekście zaistniał termin Komponent Przemysłu 4.0. Istnienie warstwy administracyjnej jest obowiązkowe dla takich komponentów, aby wymagania te mogły być spełnione zarówno przez biuro, jak i halę produkcyjną. W tym sensie aktywami mogą być "wszystkie wartościowe rzeczy", tj. nie tylko jednostki fizyczne, takie jak maszyny, czujniki czy siłowniki, ale także elementy oprogramowania.
Warstwa administracyjna nie tylko jest postrzegana jako "pojedynczy punkt prawdy" dla komponentów Przemysłu 4.0, ale także umożliwia dwukierunkową komunikację maszyna-maszyna między różnymi jednostkami, takimi jak systemy M-CAD, E-CAD lub ERP. W zwykle heterogenicznym krajobrazie narzędzi inżynieria jest zatem spójna, unika się przerw w mediach. Warstwa administracyjna umożliwia w ten sposób wdrożenie jednego z podstawowych paradygmatów Przemysłu 4.0.
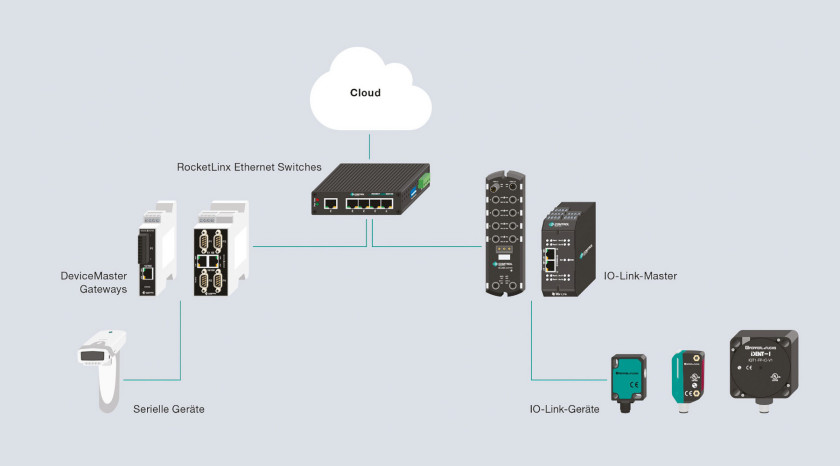
Cyfrowe bliźniaki powinny być otwarte i chętne do współpracy
Wielu producentów oprogramowania i sprzętu reklamuje oraz oferuje wykorzystanie "cyfrowych bliźniaków". Termin ten jest jednak mylący, ponieważ zwykle obejmuje autorskie rozwiązania, które mogą działać tylko w ściśle określonych środowiskach, z określonymi produktami kilku producentów. Takie "cyfrowe bliźniaki" nie umożliwiają otwartej, a więc inteligentnej, współpracy.
Z drugiej strony warstwa zarządzania zasobami (AAS) wdraża w pełni interoperacyjne podejście. AAS zawiera pełny opis semantyczny wszelkiego rodzaju komponentów w stałej strukturze. Stanowi doskonały format wymiany wszystkich istotnych danych o produkcie. AAS jest podzielony na różne podmodele, z których każdy opisuje określony, ograniczony aspekt. Podmodele związane są z aplikacjami, definiowanymi przez ekspertów z odpowiednich dziedzin, przy czym uwzględniane są również odpowiednie standardy i normy.
W celu zapewnienia jednolitych definicji oraz uniknięcia niejasności i powielania zostało utworzone Międzynarodowe Stowarzyszenie Cyfrowych Bliźniaków (IDTA) – jako centralny organ do administrowania i utrzymywania podmodeli, opartych na ZVEI i VDMA.
Koncepcję AAS wspiera również Open Industry 4.0 Alliance (OI4). Wiele firm z branży automatyki i IT (na koniec 2022 r. było to ok. stu członków) połączyło siły w ramach tego sojuszu i opracowało architekturę referencyjną dla spójnej i otwartej komunikacji przemysłowej. Umożliwia ona równoległą integrację informacji z różnych źródeł, zarówno na poziomie chmury, jak i na poziomie czujnika oraz elementu wykonawczego.
Operatorzy systemów przemysłowych są w stanie podłączyć wszystkie swoje urządzenia polowe, muszą jedynie zaimplementować połączenie z chmurą OI4 – mogą za jego pomocą uzyskać dostęp np. do dowolnej liczby różnych portali producentów.
Z wymienionych powodów rozwiązanie cyfrowe w środowisku produkcji przemysłowej można uznać za inteligentne tylko wtedy, gdy jest oparte na uznanych oraz ugruntowanych standardach i zapewnia szeroką otwartość na produkty pochodzące od jak największej liczby różnych producentów.
Tomasz Żyrek - Kierownik Regionalny FA/Regional Manager FA Key Account Manager Automotive
Pepperl+Fuchs Polska
www.pepperl-fuchs.com