Roboty przemysłowe i współpracujące
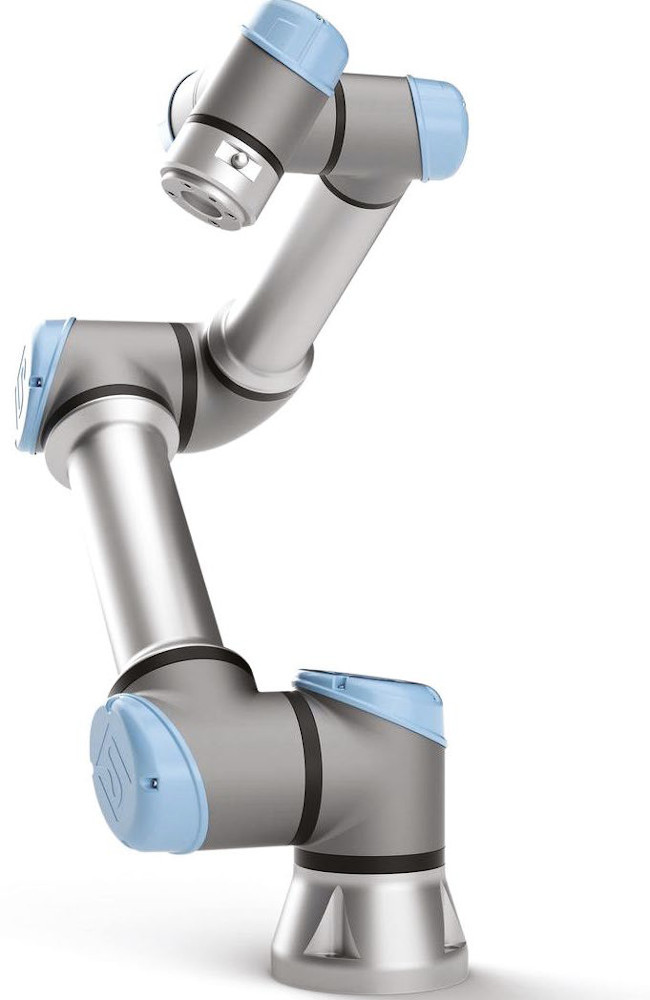
Rynek robotyki przemysłowej od wielu lat odnotowywał rekordowe wzrosty wartości i wolumenu dostarczanych maszyn. W 2019 roku liczba sprzedanych robotów jednak spadła o 12% rok do roku, do około 373 tys. sztuk, na skutek m.in. perturbacji w branży motoryzacyjnej oraz elektronicznej. Rosło natomiast wykorzystanie cobotów. Chociaż maszyny te dekadę temu praktycznie nie istniały, dzisiaj roboty współpracujące stanowią częsty element krajobrazu przemysłowego. Zapewniają one możliwość pracy z ludźmi "ramię w ramię", zmieniając zastosowania robotyki oraz jej postrzeganie przez opinię publiczną. W analizie omawiamy obydwie grupy maszyn i powiązane z nimi branże.
Charakterystyka rynku krajowego
Polski przemysł ma charakter wysoce zróżnicowany, jeżeli chodzi o liczbę i różnorodność branż, przez co również w przypadku robotyzacji mamy do czynienia z praktycznie całym spektrum możliwych zastosowań tych maszyn. Oczywiście skala robotyzacji jest w różnych sektorach oraz aplikacjach różna. W przypadku paletyzacji zastosowany może być jeden robot z osprzętem, zaś w zakładzie motoryzacyjnym linia do spawania i zgrzewania karoserii obejmuje typowo kilkadziesiąt lub więcej robotów. Ostatni z rodzajów aplikacji, tj. związany z produkcją w szeroko rozumianym sektorze automotive, jest dla rynku robotyki kluczowy od momentu jego powstania. Z kolei w ostatnich kilku, kilkunastu latach obserwować można było coraz większy popyt ze strony klientów z tzw. obszaru general industry. Dotyczy to ogółu zastosowań związanych z produkcją, wytwarzaniem towarów i manipulowania nimi – np. w sektorze metalowym, produkcji tworzyw sztucznych oraz spożywczym.
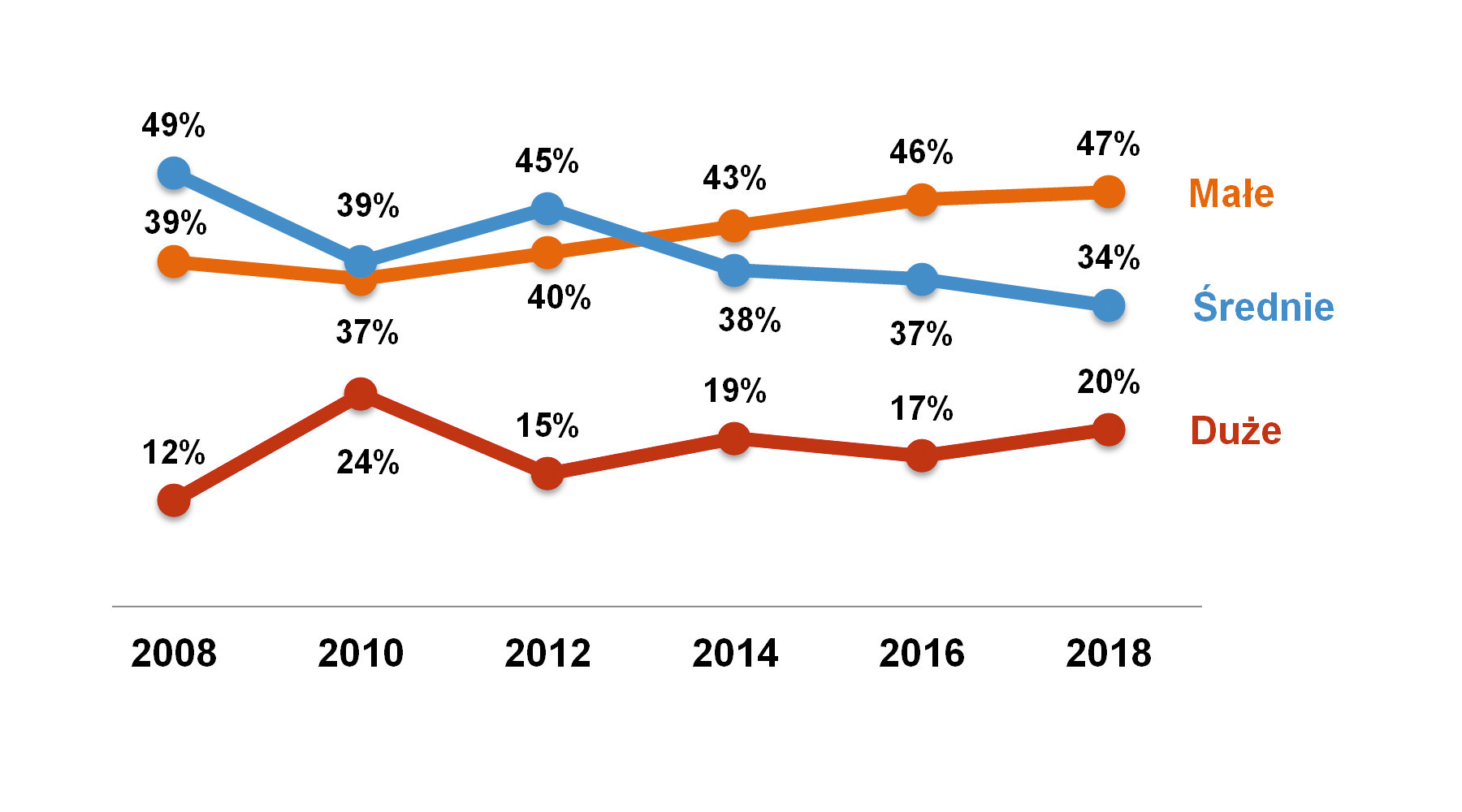
Zdaniem krajowych respondentów najczęstsze zastosowania robotów dotyczą obecnie przenoszenia i paletyzacji, pakowania i montażu, zaś w dalszej kolejności – obsługi gniazd produkcyjnych oraz spawania i zgrzewania. Zmianę wprowadza popularyzacja robotów współpracujących, które rozszerzają możliwości robotyzacji w obszarach związanych z montażem, manipulowaniem elementami, obsługą maszyn, klejeniem, itd. Dodatkowo lista zastosowań robotów jest o wiele dłuższa i wykracza coraz bardziej poza typowy przemysł produkcyjny.
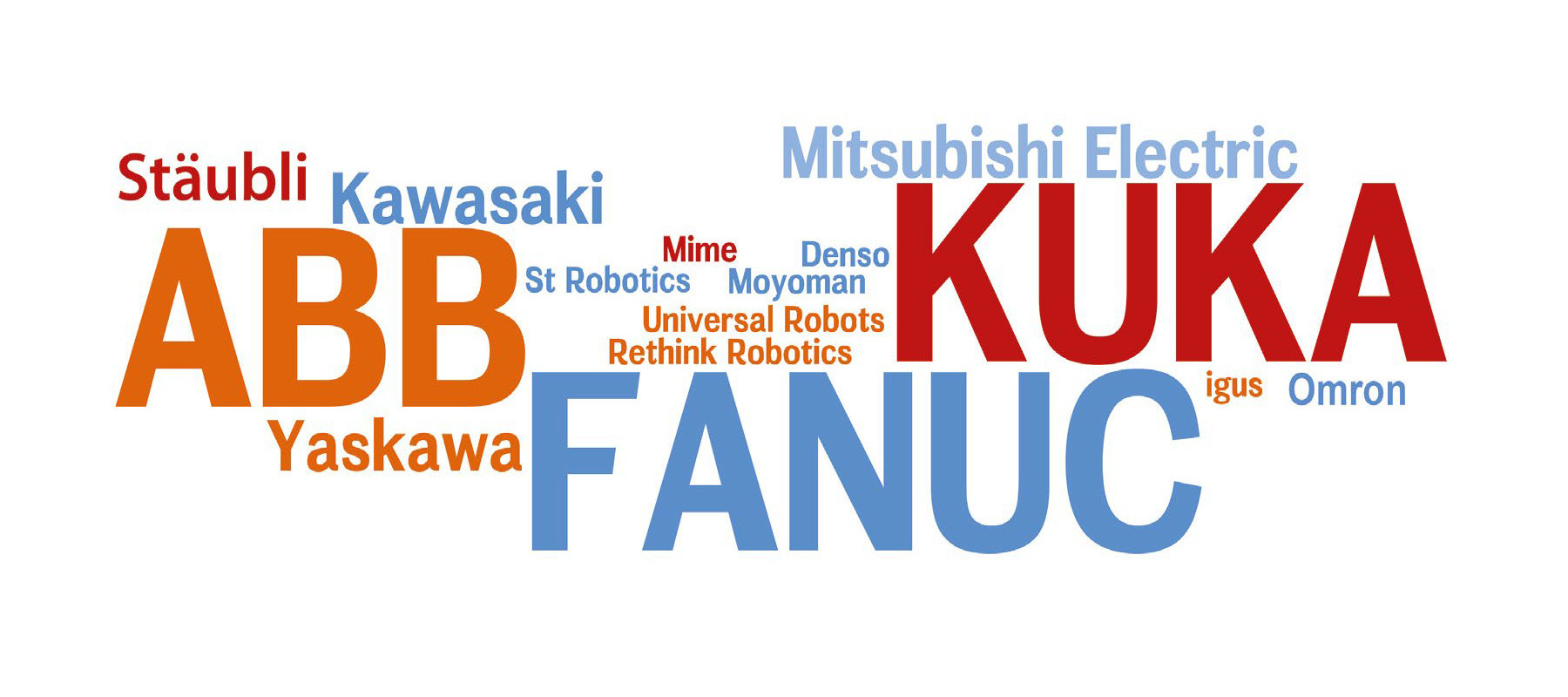
Różnorodność aplikacji sprawia, że wykorzystywane są w nich praktycznie wszystkie typy robotów pod względem rodzaju kinematyki i nośności. O ostatnią z cech zapytaliśmy respondentów i mamy tu obecnie do czynienia głównie ze sprzedażą jednostek mniejszych (47%), a następnie średnich (34%), a więc o udźwigu od kilku do kilkudziesięciu kilogramów. Udział tych dwóch grup w całości krajowego rynku w bieżącej dekadzie zmieniał się, przy czym ogólną tendencją było przesuwanie się w stronę robotów o mniejszych gabarytach i nośności. Jeżeli zaś chodzi o jednostki największe, które wykorzystywane są m.in. w paletyzacji, manipulowaniu dużymi elementami, a także w procesach wytwórczych w motoryzacji, ich udział w sprzedaży jest dosyć stały – zdaniem dostawców typowo co piąty sprzedawany robot jest właśnie tego typu.
"Jakie są najważniejsze powody, które przekonują Państwa klientów do wdrożenia robotów przemysłowych?" – na tak postawione pytanie dostawcy robotów praktycznie jednym głosem zazwyczaj odpowiadali: możliwość zapewniania jakości oraz zwiększania wydajności produkcji. W przypadku pierwszego z czynników mowa nie tylko o "wysokiej jakości" czy o "precyzyjnej produkcji", ale też o jakości niezmiennej w czasie i niezależnej od samych pracowników. Jeżeli zaś chodzi o wydajność, to dotyczy ona zwiększania szybkości produkcji, jej elastyczności oraz zmniejszania kosztów bieżących. Roboty odciążają też personel od prac monotonnych i uciążliwych, co w efekcie przekłada się na ogólny wzrost wydajności produkcji. Motywacją do wdrożeń może być też podpatrzenie danego rozwiązania u innego, często konkurencyjnego producenta, który w podobnej aplikacji już wykorzystuje roboty.
Mateusz Amroziński
FANUC
Na robotyzację najbardziej otwarte są te sektory, w których wysokie koszty produkcji idą w parze z ekstremalnie wysokimi wymogami kontrahentów m.in. w zakresie jakości czy powtarzalności. W Polsce, podobnie jak i w innych krajach świata, producenci poszukują robotów dedykowanych do zadań potocznie zwanych handlingiem, czyli do przenoszenia, przekładania, obsługi produktów. Tego rodzaju aplikacje zrobotyzowane występują we wszystkich branżach, na każdym etapie produkcji. Producenci chętnie zamawiają również roboty montażowe, spawalnicze oraz roboty dedykowane do aplikacji paletyzacji. W obliczu wyzwania dotyczącego konieczności podnoszenia jakości produktów roboty coraz częściej są "zatrudniane" także w obszarze kontroli jakości. Z roku na rok rośnie liczba robotów instalowanych w procesach obsługi maszyn obróbczych. W takich gniazdach produkcyjnych robot jest odpowiedzialny za załadunek i rozładunek maszyny, a operator czuwa nad realizacją planu produkcji, dba o jakość, analizuje parametry obróbki oraz diagnozuje maszynę w przypadku wystąpienia nieprawidłowości. Na inwestycje w technologie trzeba patrzeć szeroko. Z uwagi na ogromną ilość czynników determinujących dobór robota do potrzeb konkretnej aplikacji najlepiej jest, gdy to producent stanowiska zrobotyzowanego zapewnia kompletne stanowisko produkcyjne. Dzięki temu na linię produkcyjną trafia technologia ściśle dostosowana zarówno do obecnych, jak i przyszłych potrzeb zakładu, a służby utrzymania ruchu mogą liczyć na pełne wsparcie producenta i integratora robota, w całym okresie eksploatacji stanowiska zrobotyzowanego.
W niektórych sektorach produkcja znacząco spowolniła, w innych zaś gwałtownie wzrosła. Statystyki firmy FANUC Polska ujawniają, że sprzedaż robotów utrzymuje się na stałym poziomie, ale rozmowy z klientami pokazują, że w wielu przypadkach pojawia się potrzeba rewizji wymagań stawianych robotom. To z pewnością wpłynie na wydłużenie czasowe niektórych projektów inwestycyjnych. Firmy, które już wcześniej inwestowały w roboty, zgłaszają się po kolejne. Naszym zdaniem wynika to z większej świadomości korzyści wynikających z robotyzacji. Ci, którzy mają "mechanicznych pracowników", nie czują obawy przed nieznanym, bo widzą konkretne korzyści z robotyzacji procesów wytwórczych. Dotyczy to możliwości produkowania wyłącznie pod nadzorem człowieka, nierzadko zdalnym, a także łatwego przestawiania produkcji na inny asortyment. Warto dodać, że w tej grupie są także klienci, którzy znacząco przyspieszają inwestycje. Z kolei przedsiębiorstwa, które dotąd nie inwestowały w robotyzację, nadal tego nie robią. Według ekspertów firmy FANUC nastał koniec produkcji just-in-time. Ten model wytwarzania jest zbyt ryzykowny w czasach bardzo niepewnych warunków rynkowych. Pandemia potęguje presję na marże, poszukiwanie optymalizacji kosztowej prawdopodobnie zmieni globalny łańcuch dostaw. Firmom, które dotychczas bazowały na krótkookresowych strategiach i nie poczyniły planów dotyczących inwestycji w nowoczesne technologie będzie najtrudniej wyjść z kryzysu. Te firmy są dziś niestety najmniej elastyczne i nieprzygotowane do nieprzewidzianych warunków rynkowych. Tego typu firmy mogą odczuć również pogłębienie problemów kadrowych, ponieważ wiele wskazuje na to, że pracownicy będą obawiali się pracy w środowiskach, gdzie inni, blisko współpracujący z nimi pracownicy mogą stanowić potencjalne źródło zarażenia wirusem. Ta sytuacja może sprzyjać chęci przekwalifikowania się do innych zadań. |
Chociaż powyższych wskazań pojawiło się w ankietach sporo, statystycznie najczęstszymi były te dotyczące możliwości rozwiązania problemów kadrowych w firmach produkcyjnych. Respondenci stwierdzali wprost: "brakuje pracowników, w tym tych wykwalifikowanych", "mamy dzisiaj do czynienia z rynkiem pracownika", "automatyzacja i robotyzacja stają się nie tylko okazją [do zwiększania jakości], ale koniecznością". O braku pracowników i problemach na rynku mówiła ponad połowa respondentów i jest to największa zmiana w kontekście wyników wszystkich publikowanych dotychczas analiz.
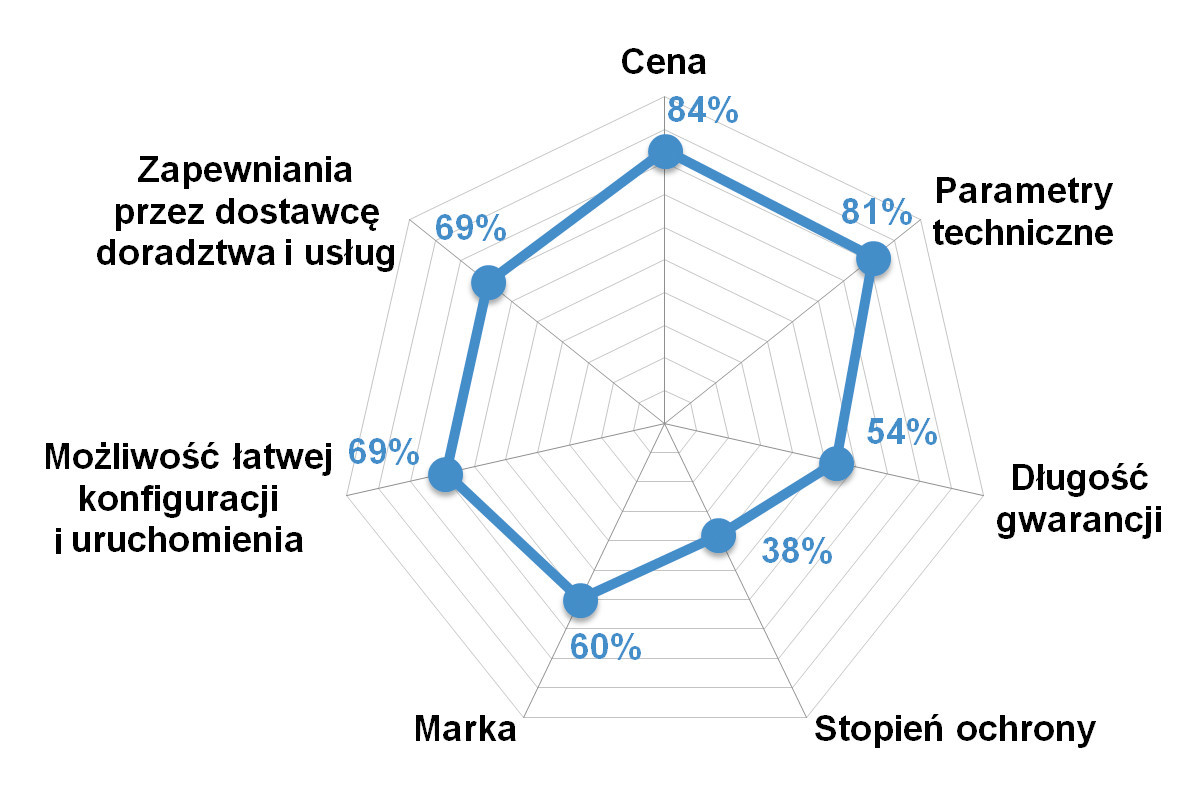
Warto tutaj przedstawić jeszcze jedną statystykę, która dotyczy najważniejszych dla polskich odbiorców cech robotów. Respondenci, zapytani o uszeregowanie elementów niedługiej listy, na początku najczęściej umieszczali cenę (zakupu robota i wykonania aplikacji zrobotyzowanej) oraz parametry techniczne. Kolejne miejsca zajęły czynniki takie jak: doradztwo zapewniane przez dostawcę, łatwość konfiguracji i uruchomienia oraz długość gwarancji. Są to odpowiedzi zbieżne z tymi z poprzednich analiz, przy czym dawniej lista była krótsza, bowiem nie pytaliśmy o wsparcie i uruchomienie.
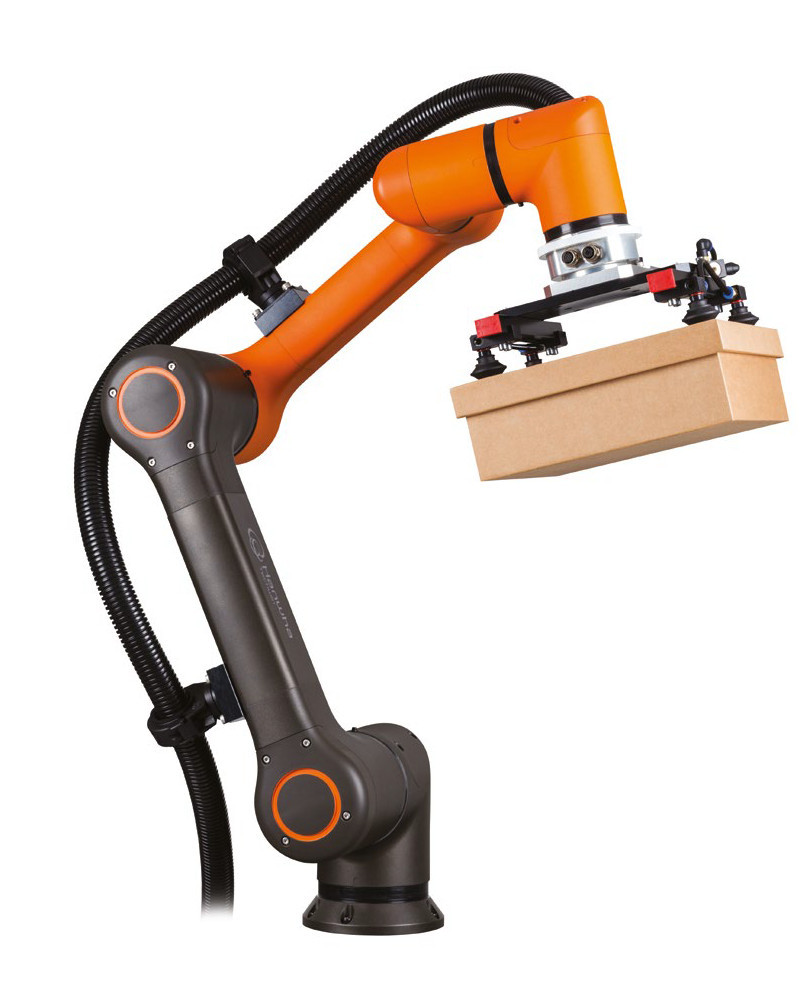
Na koniec jeszcze kilka słów o rynku oraz o możliwym scenariuszu na przyszłość. Pod względem zastosowań największym globalnie odbiorcą robotów przemysłowych pozostaje motoryzacja, gdzie trafia około 150 tys. robotów rocznie. Z kolei jednym z najszybciej rozwijających się sektorów jest przemysł metalowy, kolejne miejsca zajmują sektory elektryczny i elektroniczny oraz przemysł spożywczy. W Polsce mamy do czynienia ze wspomnianym wcześniej dużym zróżnicowaniem odbiorców robotów, a także latami niezłego rozwoju branży General Industry. Ta ostatnia, w tym w szczególności sektory: spożywczy, metalowy i przetwórstwa spożywczego, będzie w przyszłości również wysoce istotna dla dostawców robotyki przemysłowej. Po roboty coraz częściej sięgają nie tylko firmy największe, ale też te z sektora MŚP, co sprzyja ogólnej popularyzacji tych maszyn. Najważniejszą jednak zmianą dotyczącą prognoz dla rynku krajowego jest w przypadku omawianej statystyki powrót motoryzacji na pozycję lidera. Respondenci zwracali też uwagę na przemysł elektroniczny, którego popularność w kontekście robotyzacji w ostatnich latach rosła. Pozostaje również dodać, że liczba wdrożeń systemów automatyki i robotyki jest zawsze pochodną koniunktury w gospodarce – i to od niej, oraz tego, jak zmieniały się będą wymogi odbiorców krajowych i zagranicznych, w praktyce zależał będzie popyt na roboty, manipulatory oraz kompletne systemy zrobotyzowane.
Tomasz Nowak
KUKA Polska
Ostatnie lata w branży robotyki przyniosły istotną zmianę, bowiem Polska stała się dla producentów robotów bardzo interesującym rynkiem. Dane International Federation of Robotics za 2018 rok pokazują, że dostarczono u nas około 2,5 tysiąca robotów. Dotyczyło to wszystkich typów tych maszyn, przy czym tych dla nas najbardziej interesujących, tj. sześcioosiowych robotów przegubowych, sprzedano około 1800 sztuk. Daje nam to 15. miejsce na świecie. Prześcignęliśmy tym samym wiele krajów, zaś do Hiszpanii czy Włoch brakuje nam jeszcze ze dwa tysiące.
Odbiorcami robotów są dzisiaj w Polsce właściwie wszystkie branże i dla dostawcy takiego jak my jest to bardzo pozytywny fakt. Polski sektor General Industry to przykładowo wytwórcy maszyn rolniczych, producenci płotów, firmy dostarczające meble i wiele innych towarów. Coraz częściej brakuje im mocy przerobowych i firmy te są zmuszone do inwestowania, co przekłada się na wiele konkretnych zapytań. Co ciekawe – w omawianym zakresie są coraz aktywniejsi również polscy mali i średni przedsiębiorcy. Sądzę, że jest to wynik edukacji, którą od wielu lat prowadzą w Polsce dostawcy robotów, przez co robotyka "trafia pod strzechy". Kiedyś o rynku GI mówiło się jako o "przyszłościowym", "perspektywicznym", natomiast ta zmiana już zachodzi. Moim zdaniem polski sektor General Industry będzie niebawem drugą siłą napędową, jeżeli chodzi o lokalny rynek robotyki.
Jest tu kilka przesłanek. Po pierwsze, inwestycje w automatyzację i robotyzację wymusza na właścicielach firm sytuacja na rynku pracy. Zmieniły się koszty związane z zatrudnianiem pracowników – i to na tyle, że dzisiaj nie trzeba już przekonywać klientów do robotyzacji tak jak dawniej. Dodatkowo przedsiębiorcy coraz częściej wiedzą, że bez inwestycji technologicznych nie tylko przestają być konkurencyjni, ale też po prostu mogą nie wyprodukować i dostarczyć na czas towarów. Jako że wiele firm obsługuje działające u nas koncerny zagraniczne, są one regularnie sprawdzane właśnie pod kątem zagwarantowania ciągłości dostaw. To ostatnie szczególnie dotyczy firm korzystających z pracowników sezonowych, w przypadku których fluktuacje personelu mogą być duże, zaś sposobem na rozwiązanie tego problemu jest automatyzacja. Do powyższego dochodzą względy wizerunkowe. Przykładowo chcąc dostać kontrakt w dużej sieci marketów budowlanych, trzeba przejść audyt i korzystne jest posiadanie zautomatyzowanej, zrobotyzowanej produkcji. |
Roboty współpracujące

przez dostawców i integratorów robotów
Odrębną grupę produktów, które szybko się popularyzują, stanowią roboty współpracujące. Są one typowo wykorzystywane w dwóch scenariuszach aplikacyjnych: współpracy pracownika i maszyny, gdzie dzielą się obowiązkami w ramach jednego zadania, oraz w wykonywaniu przez nich oddzielnych czynności, przy czym osoba i robot znajdują się w bezpośrednim sąsiedztwie. W obydwu przypadkach coboty wykonują zadania takie jak przykładowo podnoszenie i przenoszenie elementów, pakowanie, montaż, nakładanie kleju oraz wiele innych. Są to czynności powtarzalne i z perspektywy człowieka mało atrakcyjne. Mówi się, że roboty współpracujące uwalniają pracowników do bardziej kreatywnych zadań – i jest w tym dużo prawdy.
Jakie są najczęstsze role cobotów w polskich zakładach? Statystyka obejmuje kilkanaście typowych aplikacji, przy czym kluczowymi są te związane z manipulowaniem elementami (pick & place), montażem, pakowaniem, zaś w dalszej kolejności: tzw. machine tending (obsługą maszyn, podawaniem i odbieraniem detali do obróbki), paletyzacją oraz manipulowaniem delikatnymi / małymi komponentami (np. elektronicznymi). Wielkości i ciężary elementów są tu istotne, bowiem udźwig typowych robotów współpracujących to kilka kilogramów. Dodatkowo niewielkie prędkości ruchu wprost implikują zastosowania tych maszyn. Czasami coboty pracują wspólnie – np. jako dwa ramiona, aczkolwiek popularniejsza jest ich integracja z maszynami obróbczymi czy po prostu współpraca z ludźmi.
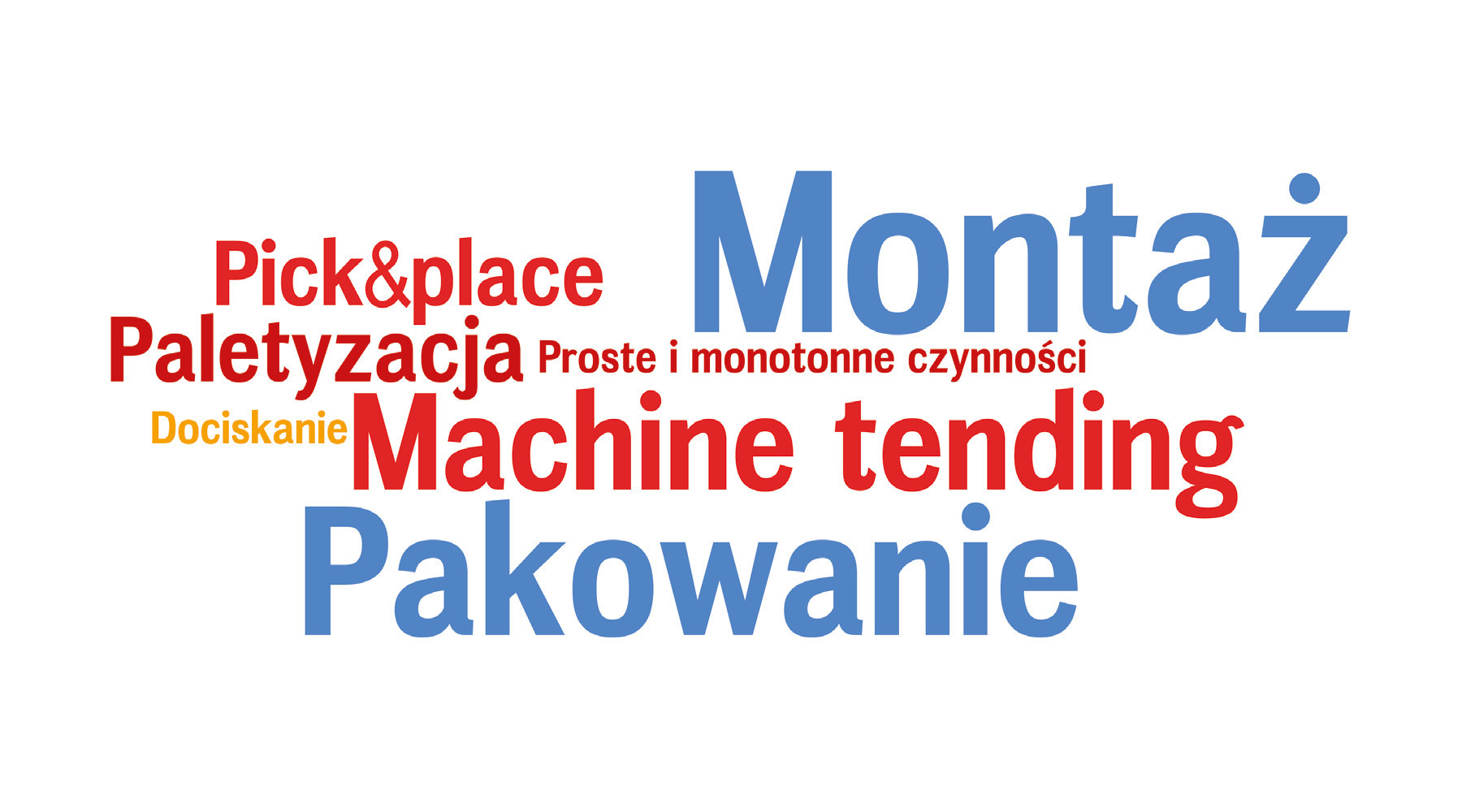
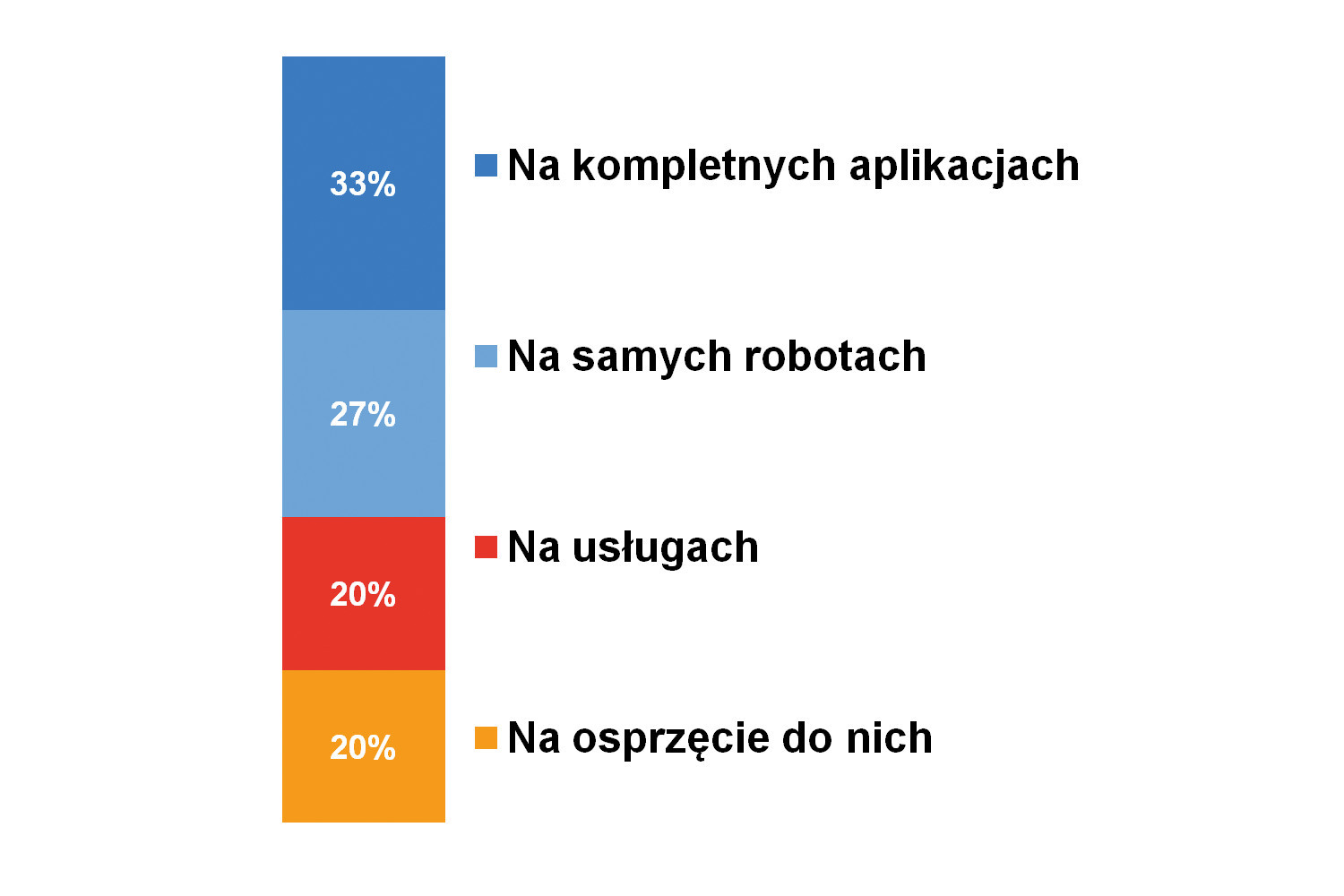
Pytając o zastosowania cobotów, dodaliśmy pytanie uzupełniające, które brzmiało "w jakich aplikacjach współpraca robotów z ludźmi lub wykorzystanie cobotów zamiast pracowników jest najefektywniejsza?". W tym przypadku na czele zestawienia znalazły się: montaż oraz pakowanie, za nimi były machine tending, pozostałe zastosowania pick & place oraz paletyzacja. Są to aplikacje, gdzie pracownicy wykonują monotonne, żmudne lub też nieergonomiczne czynności. Jeden z respondentów wręcz przyznał, że cobot może zastąpić człowieka "w każdych warunkach pozwalających na wyeliminowanie człowieka wykonującego powtarzalną, prostą czynność" – i trudno się z tym nie zgodzić, bowiem do tego właśnie stworzone zostały roboty współpracujące.
Stefan Życzkowski
ASTOR
Rozważając decyzję o inwestycji w roboty współpracujące, nie wpadajmy w emocje, liczmy! Liczmy czas cyklu, liczmy ROI. Okaże się, że niska wydajność cobotów i wysokie koszty ich wdrożenia powodują, że mogą one sprawdzić się co najwyżej w aplikacjach testowych, R&D lub w niszowych czynnościach produkcyjnych. Naprawdę trudno znaleźć biznesowe uzasadnienie dla ich obecności w masowej produkcji.
Taką może być sektor produkcji elektroniki w Azji, gdzie Kawasaki jest liderem rynku robotów współpracujących. Ale tam są inne realia. W Polsce trudno znaleźć mi branżę, która mogłaby z sukcesem (finansowym!) wdrożyć coboty na masową skalę bez posiłkowania się zewnętrznym dofinansowaniem, a opierając się tylko i wyłącznie na wzroście efektywności produkcji. Znam za to wiele branż, które realizują 300% wydajności aplikacji dzięki zastosowaniu typowych robotów przemysłowych. |
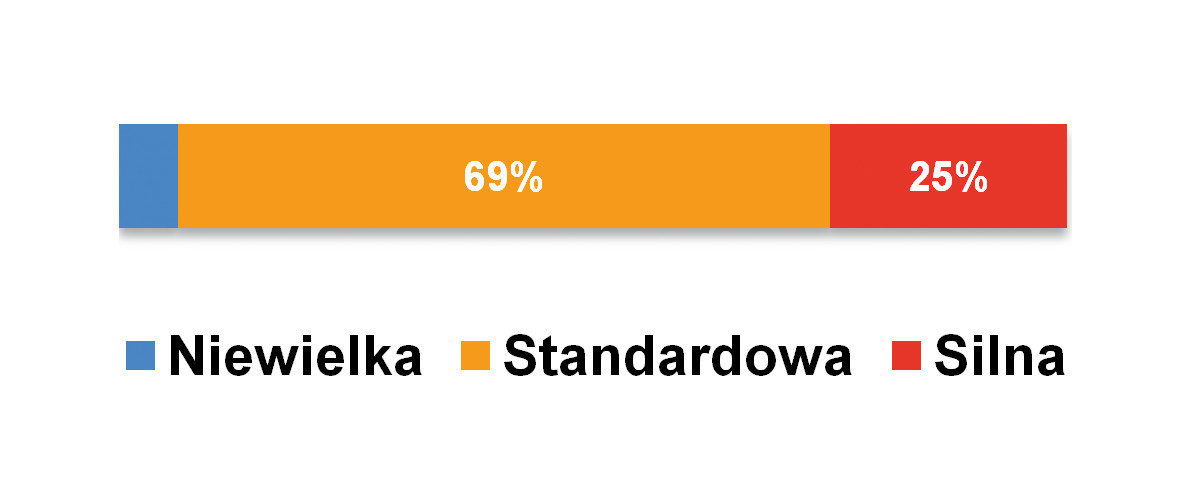
Szacowanie wartości rynku cobotów jest trudne, bowiem branża ta rozwija się, zaś organizacja IFR przez lata badała jedynie obszar związany z tradycyjna robotyką przemysłową. Stąd też szacunki, którymi dotychczas dysponowaliśmy, wynikały z danych podawanych przez producentów cobotów – ale ponownie nie dla naszego rynku, a globalnie. Do tego były to wskazania bardzo ogólne – np. mówiące o "kilkukrotnym wzroście wolumenu produkcyjnego" w ostatnich latach.
W 2019 roku przeprowadziliśmy badanie tej branży, które traktować można jako pierwsze oszacowanie tego rynku w Polsce. Przedstawiamy je z zastrzeżeniem, że są to oceny sumarycznie nieco ponad dwudziestu respondentów i nie jest uprawniona ich generalizacja statystyczna. Wielkość krajowego rynku cobotów szacowana była na 150‒220 sztuk rocznie, przy czym zakres podawanych przez respondentów wartości wynosił od kilkudziesięciu do kilkuset. Jeżeli chodzi o szacowane tempa wzrostu branży, to oceny respondentów wynosiły od 20% do 32%. Jak widać, są to wartości spore, co potwierdza perspektywiczność branży. Stąd również zainteresowanie nimi coraz większej liczby producentów krajowych i zagranicznych, jak też firm dystrybucyjnych oraz zajmujących się integracją systemów.
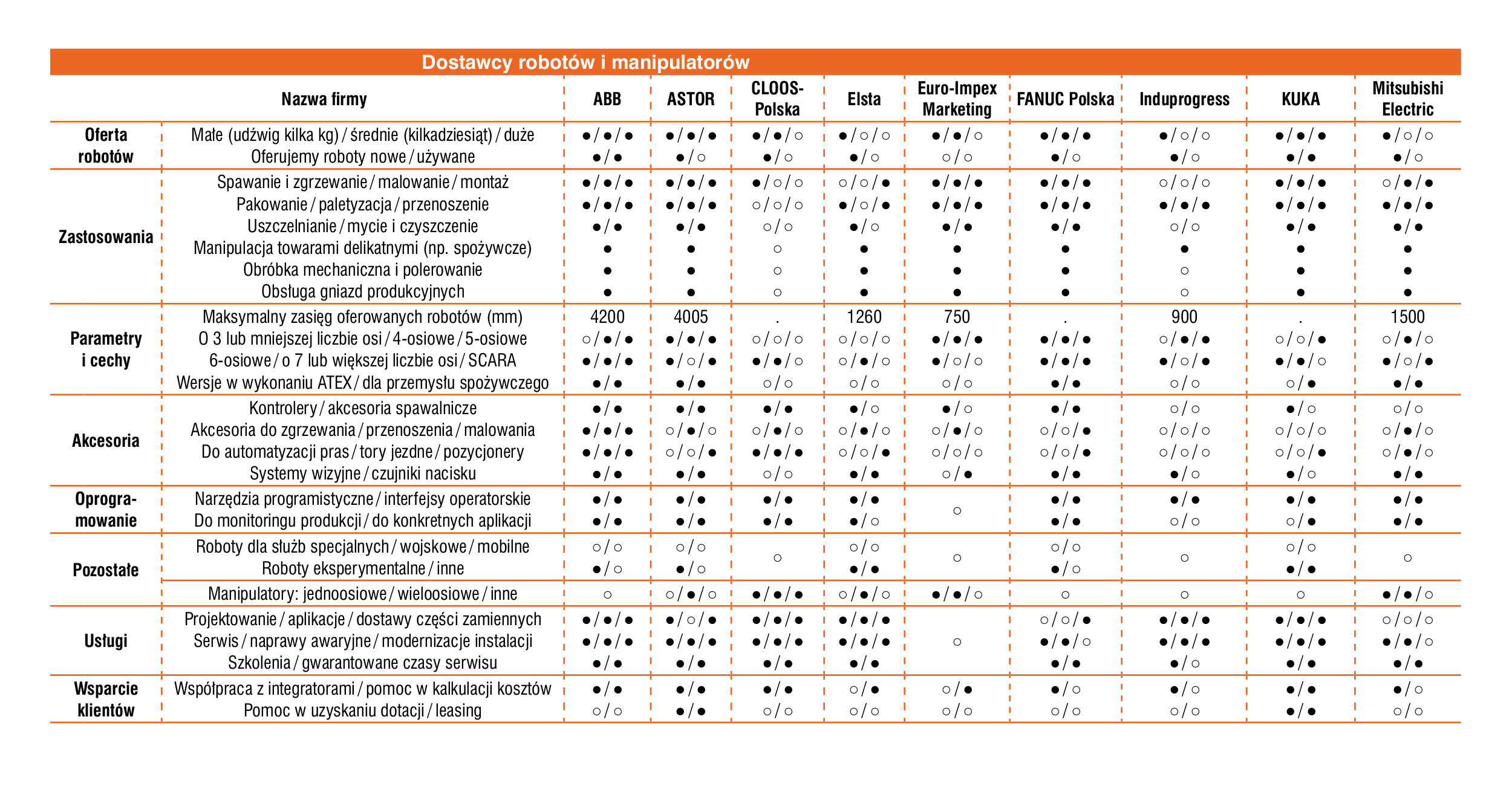
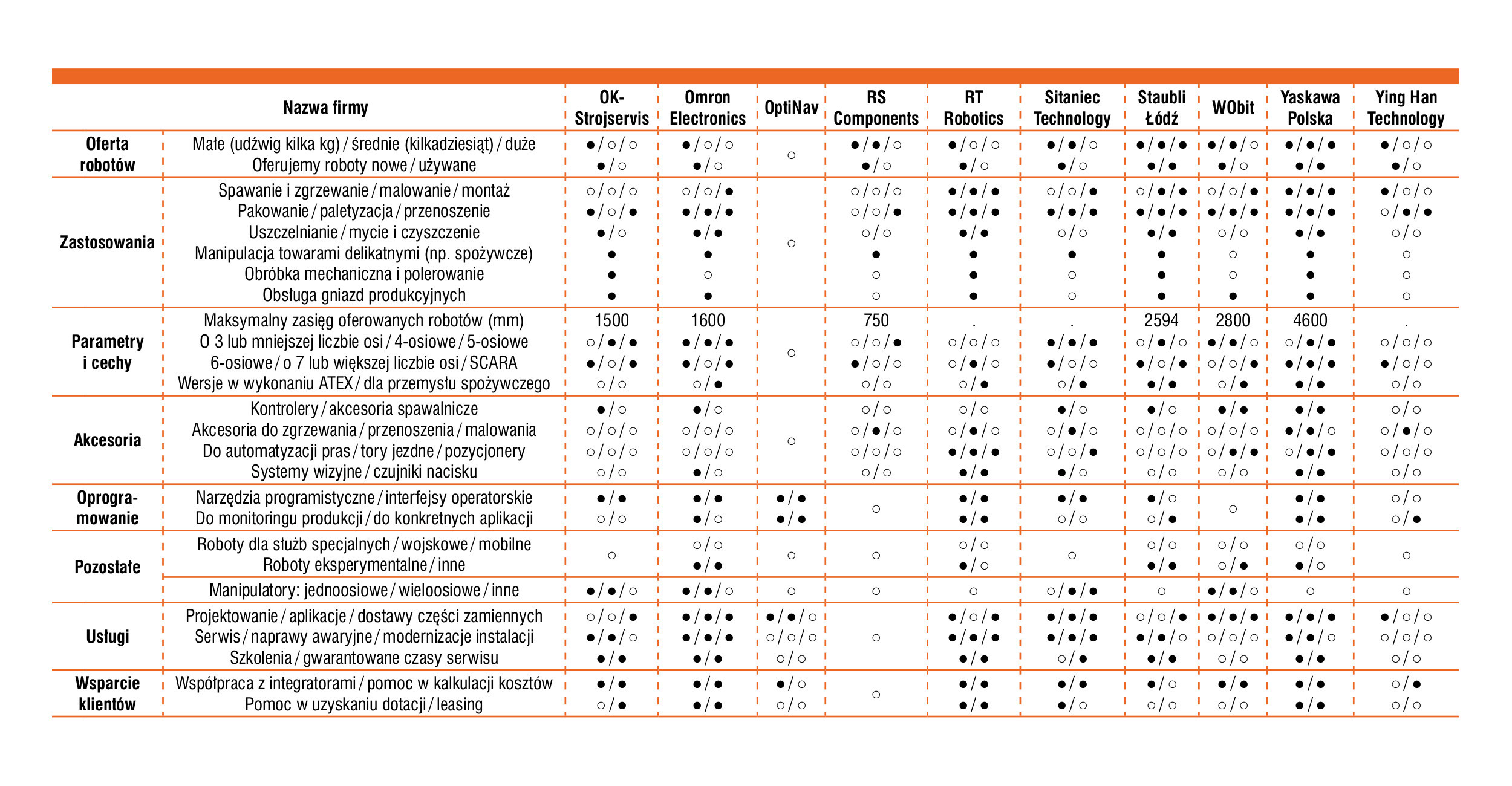
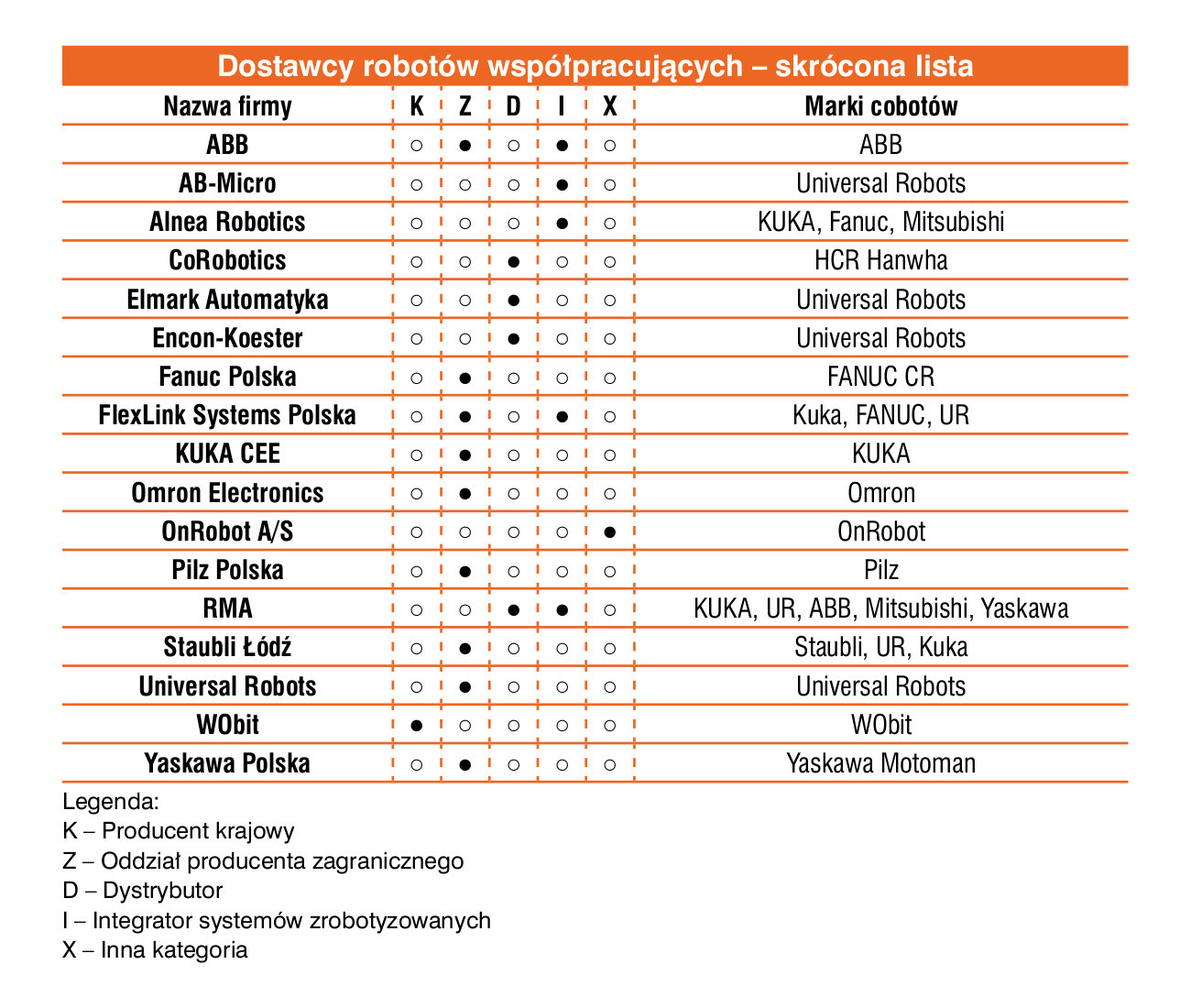
Branża cobotów w przyszłości
Globalna branża cobotów rozwija się o wiele szybciej niż rynek tradycyjnych robotów przemysłowych i w kolejnych latach owa dynamika powinna być utrzymana. Istnieje szereg bieżących i potencjalnych zastosowań robotów współpracujących, szczególnie w krajach rozwiniętych, które borykają się z problemami z siłą roboczą, przez co perspektywy dla cobotyki są obiecujące.
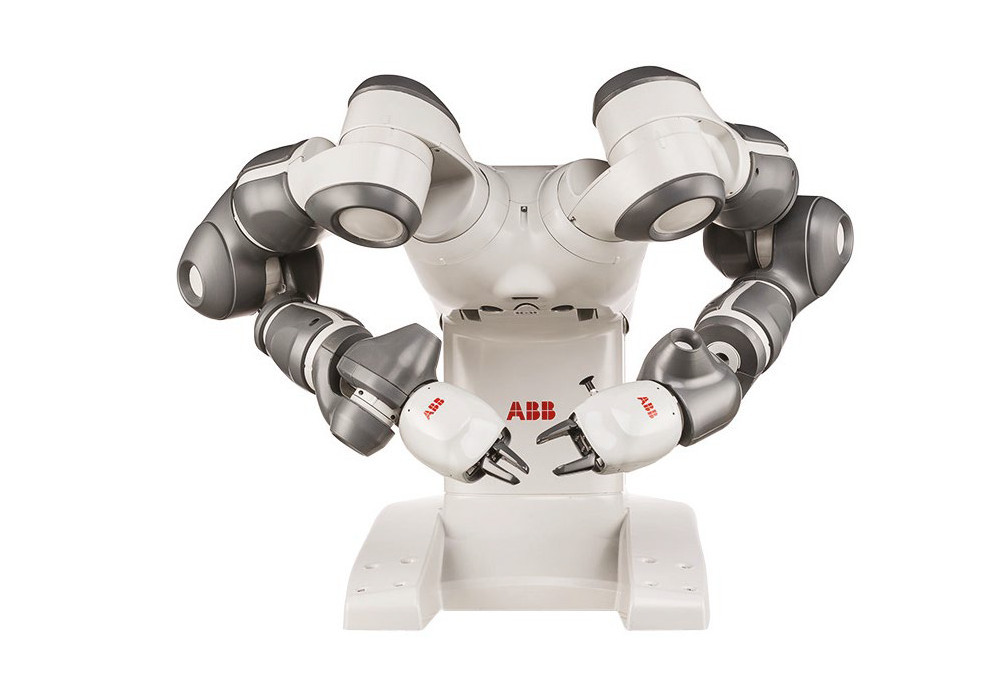
W Polsce branżą najczęściej typowaną jako główny odbiorca robotów współpracujących w przyszłości jest motoryzacja. Sektor ten cechuje duża skłonność do wdrażania innowacji w obszarze procesów technologicznych, w porównaniu z innymi branżami przemysłowymi, również liczba wykonywanych w nim operacji manualnych jest znacząca (dotyczy głównie poddostawców i producentów komponentów). Kolejne dwa ważne rynki to: sektor produkcji elektroniki oraz branża spożywcza (każdy z nich otrzymał o połowę mniej głosów niż motoryzacja). Respondenci wskazywali też istotność sektora tzw. General Industry, metalowego, farmaceutycznego i AGD. Grupa potencjalnych odbiorców robotów współpracujących tworzy tzw. długi ogon, który obejmuje wiele specyficznych branż i zastosowań, w tym nie tylko w przemyśle. I tak też należy o omawianym rynku myśleć, stawiając w centrum uniwersalność aplikacyjną samych cobotów.
Krzysztof Hajzyk
Universal Robots
Według badania "Barometr robotyzacji MŚP" przeprowadzonego na nasze zlecenie w Polsce pod koniec 2019 roku blisko 1/3 małych i średnich przedsiębiorstw produkcyjnych planuje w ciągu 3 lat robotyzację. 38,8% firm z tej grupy potwierdziło, że zamierza wdrożyć roboty współpracujące, przy czym ten wskaźnik był skorelowany z wielkością przedsiębiorstwa – wśród małych firm na coboty wskazało 42,9%, natomiast wśród średnich – 36,8%. Wyniki te pokazują, że rośnie świadomość na temat możliwości robotów współpracujących i zaczęły one być postrzegane jako rozwiązanie także dla mniejszych zakładów, które wcześniej nie inwestowały w automatyzację.
Firmy w pierwszej kolejności planują zrobotyzować pakowanie i paletyzację, obsługę maszyn, montaż i przenoszenie towarów. Coboty mogą wesprzeć zakłady w tych zadaniach, są efektywne kosztowo i oferują szybki zwrot z inwestycji. Użytkownicy zwracają uwagę na prostotę programowania i obsługi, które nie wymagają specjalistycznej wiedzy inżynierskiej. Czas wdrożenia do pracy jest także bardzo ważny – w przypadku cobota UR, rozpakowanie, zamontowanie go i zaprogramowanie pierwszego prostego zadania zajmuje przeważnie mniej niż godzinę. Coboty Universal Robots są lekkie i nieduże, będą zatem dobrym rozwiązaniem dla firm, które chcą wykorzystywać robota do różnych zadań i przemieszczać go w hali produkcyjnej. |
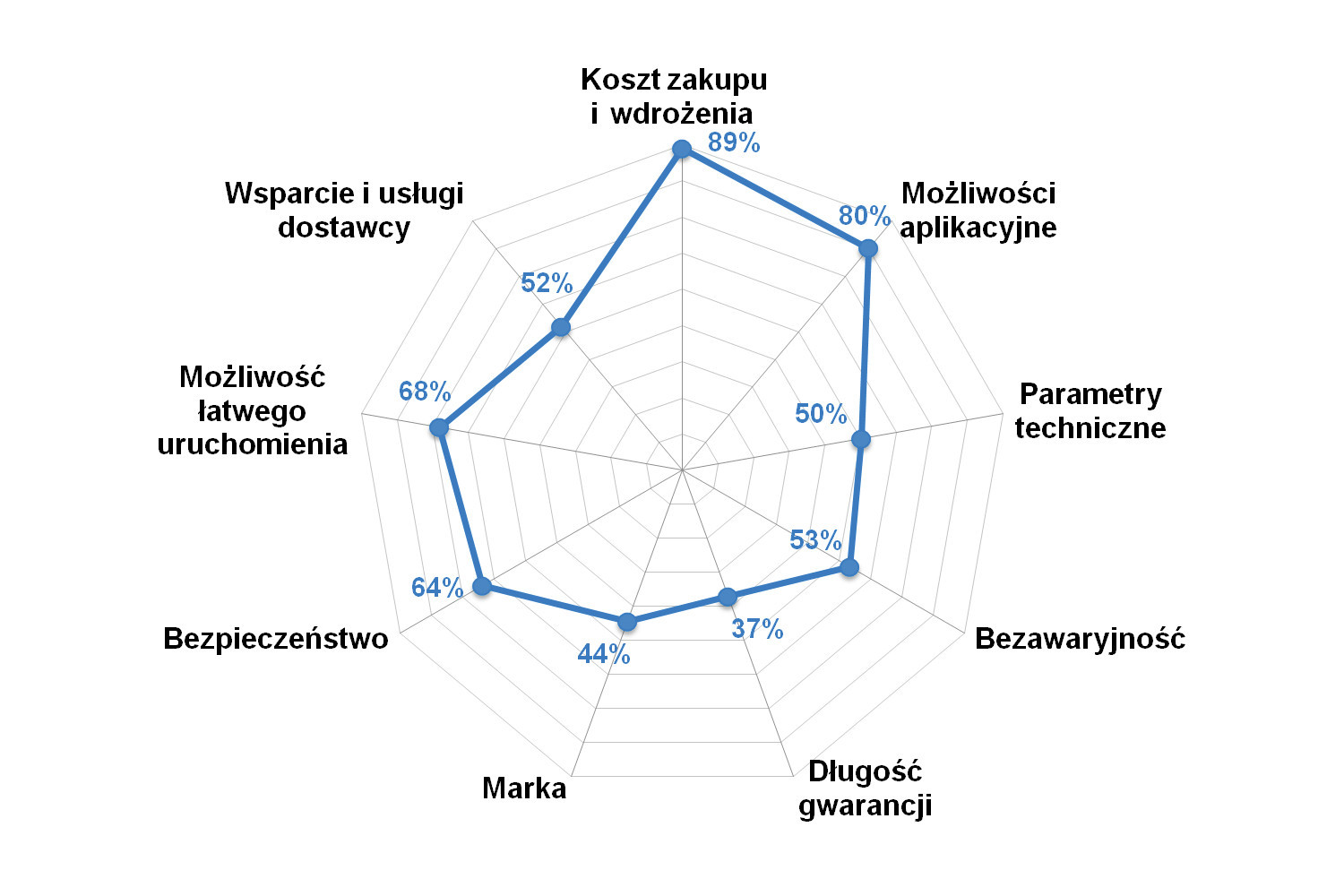
Rozważając perspektywy dla branży, zwracamy szczególną uwagę na komentarz Stefana Życzkowskiego. Prezes firmy ASTOR jest orędownikiem robotyzacji (tradycyjnej), ale nie podziela poglądu, jakoby coboty były ekonomicznie opłacalne w polskim przemyśle. Komentarza w podobnym tonie udziela przedstawiciel firmy Renex. Wskazujemy te dwie wypowiedzi, gdyż pozostają one w kontrze do poglądów "mainstreamowych", które promują dostawcy cobotów.
Na koniec jeszcze spojrzenie na rynek w wymiarze globalnym. BIS Research Analysis w raporcie "Global Collaborative Industrial Robot Market") ocenia, że w 2017 roku wartość sektora cobotów wyniosła 420 mln dolarów, co stanowiło około 2,5% całego rynku robotów (odnosząc to do wartości podawanych przez IFR). Firma prognozowała również, że średnioroczne tempo wzrostu (CAGR) globalnej branży cobotów będzie znacznie większe, niż dla całego sektora robotyki przemysłowej i w latach 2018‒2025 wyniesie 47%. Skutkiem tego na koniec wymienionego okresu branża ma być warta 9 mld dolarów. Prognoza Loup Ventures na ten sam rok wynosi z kolei… 34 mld dolarów. Zdaniem analityków firmy maszyny współpracujące mają wtedy stanowić aż 1/3 wszystkich dostarczanych na rynek robotów. Z kolei Robotics Industries Association (RIA) ocenia, że do 2025 roku sprzedaż cobotów wzrośnie dziesięciokrotnie (w stosunku do stanu z 2018 roku) i będzie stanowiła 34% sprzedaży wszystkich robotów przemysłowych.
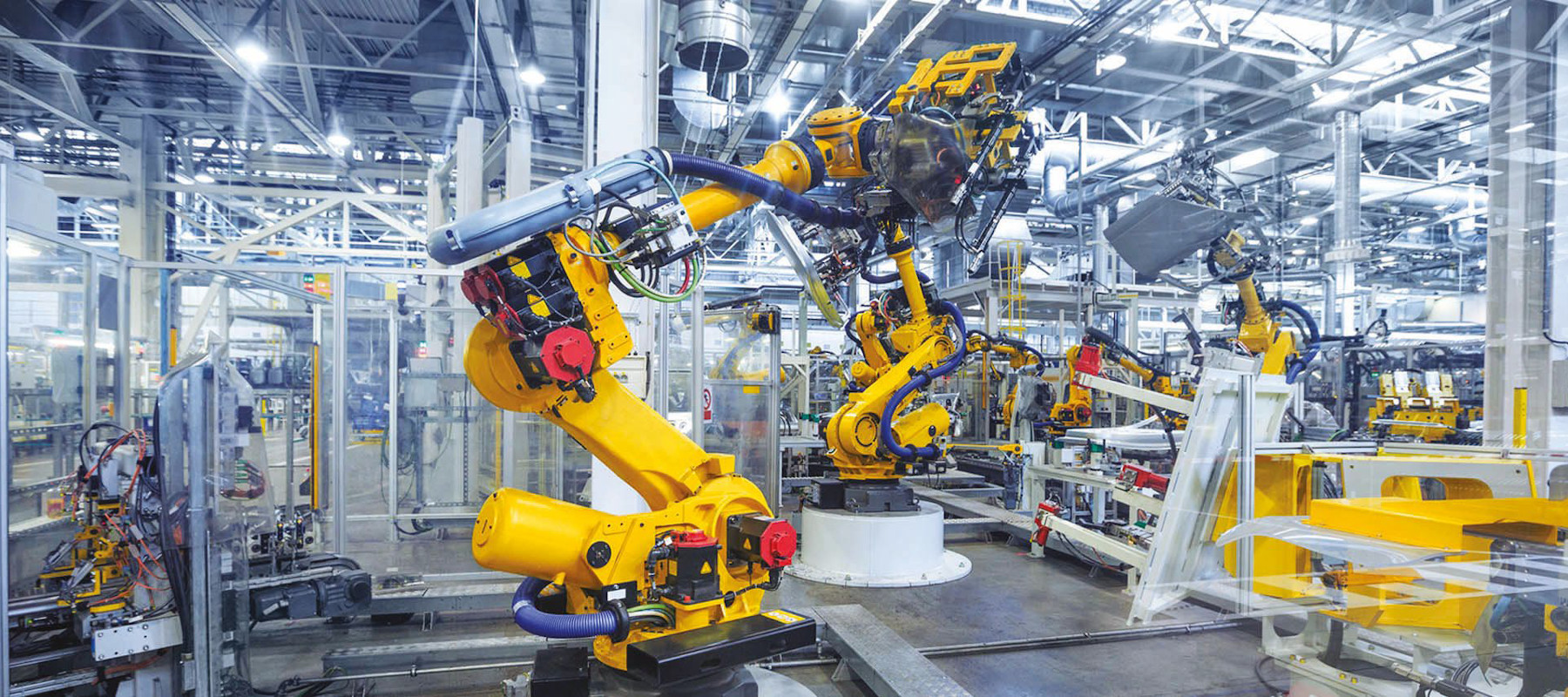
O ile do powyższych prognoz warto podchodzić z dystansem, o tyle na pewno można zgodzić się co do jednego – rynek rozwija się, a wraz z tym obserwować będziemy spadki cen jednostkowych robotów. W efekcie zapewni to dalsze zwiększanie się ich dostępności i popularyzację w różnych sektorach związanych z produkcją, a także tych poza przemysłem.
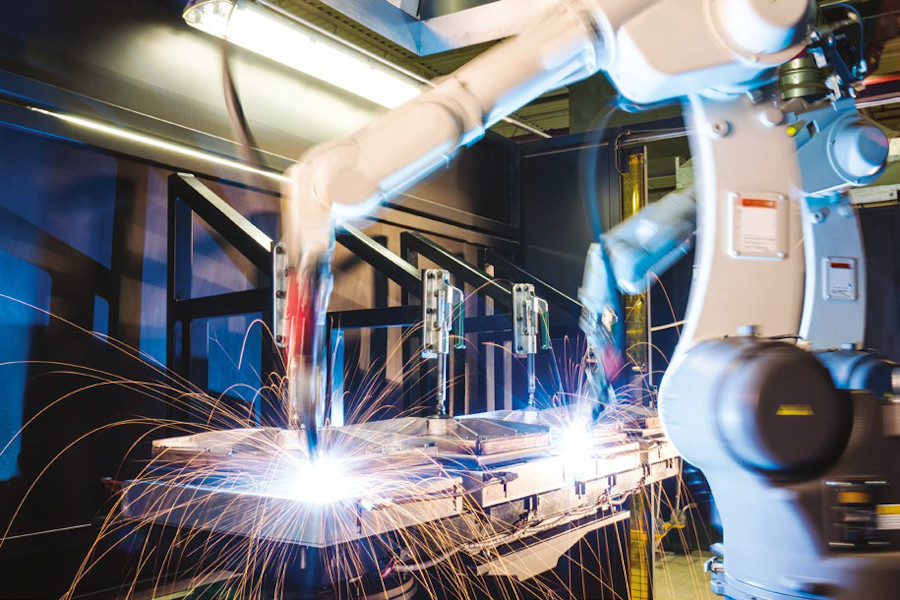