Systemy tego typu bazuje na środowisku komputerowym i wykorzystuje interfejs procesowy z klasycznego sterownika PLC. Jako platformę sprzętową dla systemu można wykorzystać zarówno komputer klasy PC w wersji biurowej lub przemysłowej oraz inne urządzenia pracujące pod kontrolą np. systemu Windows, w tym panele wielofunkcyjne. W artykule porównano realizacje specjalnych algorytmów regulacji ciągłej – predyktora Smitha, regulatora redukcyjnego i kompensatora dynamicznego, które zostały wykonane na dwóch wymienionych platformach sprzętowych softPLC.
Obiekt regulacji
W ramach symulacji wykorzystywany jest laboratoryjny obiekt cieplny, którego główną częścią jest pręt miedziany długości 260mm i średnicy 2mm ogrzewany na jednym końcu elektrycznym elementem grzejnym w postaci spirali grzejnej nawiniętej na pręt poprzez izolator ceramiczny. Pręt nie jest izolowany cieplnie na bokach i wymiana ciepła zachodzi wzdłuż całej jego długości. Element grzejny sterowany jest sygnałem prądowym 0÷1,5A, 24VDC ze wzmacniacza mocy, na wejście którego podawany jest znormalizowany sygnał z zakresu 0÷5mA. Temperatura pręta jest odczytywana czujnikiem rezystancyjnym nawiniętym w połowie długości pręta. Zmiana rezystancji czujnika odczytywana jest w układzie mostkowym, przy czym napięcie z przekątnej mostka (0÷4mV) przetwarzane jest na sygnał prądowy z zakresu 0÷5mA z wykorzystaniem przetwornika APU-11.
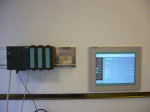
Fot. 1. Element stanowiska projektowego systemu
W rozważanym przypadku obiektu regulacji sygnały wejściowy i wyjściowy mają charakter elektryczny. Niemniej procesy fizyczne zachodzące w nim stanowią dobry przykład kilku klas rzeczywistych procesów przemysłowych, które podlegają sterowaniu. Pierwszą z nich są procesy cieplne, a inną – procesy z opóźnieniem.
Opis układu w przestrzeni stanu
Podstawowym modelem matematycznym procesów zachodzących w rozważanym obiekcie jest równanie przewodnictwa cieplnego. Przyjmując założenie, że punkt zamocowania czujnika temperatury jest stały, równanie to może być zapisane w postaci równania równoważnego, którego skończenie wymiarowa aproksymacja może być zastosowana do modelowania rozważanego obiektu - np. w środowisku Matlab. Dokonując dyskretyzacji modelu ciągłego, otrzymuje się równoważny model dyskretny o następującej postaci:

gdzie: Q(i) oznacza temperaturę w chwili czasu i oraz w punkcie zamocowania czujnika, A+ jest macierzą stanu systemu, B+ jest macierzą sterowań i C+ jest macierzą wyjść systemu. W rozważanym wypadku dobrą aproksymację rzeczywistego obiektu zapewnia przyjęcie wymiaru równania stanu równego: N=25. Wartości liczbowe parametrów z jego macierzy mogą być wyznaczone numerycznie z użyciem metody najmniejszych kwadratów. W rozważanym przypadku liczbowe wartości parametrów macierzy A+ , B+ i C+ podane są w 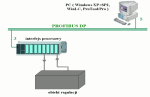
Rys. 1. Schemat sprzętowy układu sterowania softPLC - do jego realizacji użyty został komputer osobisty z procesorem Intel Celeron 2,8GHz, pamięcią operacyjną 512MB oraz kartą komunikacyjną Siemens CP 5611
Schemat logiczny komunikacji w obrębie rozważanego systemu softPLC podany jest na rys. 2. Najważniejszą cechą rozważanego układu jest mechanizm wymiany danych Softbus. Zasadnicza jego idea polega na tym, że poszczególne komponenty układu sterowania są połączone ze sobą z wykorzystaniem sieci Profibus, która jest częściowo fizyczna a częściowo wirtualna. Fragment wirtualny łączy komponenty systemu sterowania zlokalizowane w obrębie platformy sprzętowej PC, jednak z punktu widzenia komunikacji nie ma rozróżnienia pomiędzy nim a rzeczywistą częścią sieci.
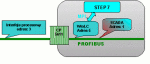
Rys. 2. Schemat logiczny oprogramowania i komunikacji w obrębie systemu softPLC do jego uruchomienia wykorzystano system Windows XP Professional SP2
Do realizacji systemu wykorzystano oprogramowanie konfiguracyjne i narzędziowe Step7 5.4 Professional. System SCADA zrealizowano z wykorzystaniem oprogramowania ProTool/Pro, a wirtualną jednostkę obliczeniową zrealizowano z użyciem oprogramowania WinLC 4.0 w wersji demonstracyjnej. Komunikacja pomiędzy Simatic Manager i WinLC odbywa się za pomocą programowego interfejsu MPI, natomiast pomiędzy pozostałymi komponentami systemu z wykorzystaniem sieci Profibus i omawianego mechanizmu Softbus. Podczas budowy systemu program dla sterownika jest zintegrowany w obrębie jednego projektu z systemem SCADA.
System bazujący na multipanelu
Drugą platformą sprzętową na której zrealizowano sterowanie softPLC, był system wykorzystujący multipanel (rys. 3). Do realizacji układu wykorzystano urządzenie Siemens MP 370 Touch oraz interfejs procesowy, którego konfiguracja podana jest w 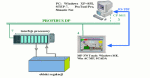
Rys. 3. Schemat sprzętowy systemu sterowania softPLC zrealizowanego na multipanelu; sieć pracuje w trybie multimaster z wykorzystaniem protokołu znacznikowego stacje master to komputer o adresie 3 oraz multipanel o adresie 4, stacja slave to interfejs procesowy o adresie 7
Istotną cechą omówionych powyżej rozwiązań jest fakt, że w obydwu przypadkach wykorzystuje się takie samo środowisko programowe, jak w przypadku systemu hardPLC. Przeniesienie aplikacji napisanej wcześniej dla systemu hardPLC do dowolnego systemu softPLC jest proste i wymaga tylko przedefiniowania konfiguracji sprzętu i ewentualnej zmiany adresów wejść i wyjść sterownika. Stwarza to duże możliwości stosunkowo łatwej rekonfiguracji platformy sprzętowej bez konieczności dużej ingerencji w oprogramowanie.
W ramach opracowywania oprogramowania dla omawianych konfiguracji przewidziano następujące funkcje systemu SCADA:
Na obu testowanych platformach sprzętowych najdłuższy maksymalny czas cyklu zaobserwowano dla kompensatora dynamicznego. Najczęściej powtarzająca się wartość czasu cyklu nie zależy od typu algorytmu, ale tylko i wyłącznie od platformy sprzętowej na jakiej algorytmy są realizowane.
W każdym z badanych przypadków, niezależnie od typu systemu i wszystkich pozostałych czynników, najdłuższy zmierzony czas cyklu był około 10 razy krótszy niż przyjęty okres próbkowania algorytmu. W związku z tym każdy z testowanych systemów sprzętowo-programowych softPLC stanowi stabilną platformę spełniającą wymogi czasu rzeczywistego do realizacji sterowania procesem ciągłym z użyciem algorytmu specjalnego.