Dlatego też coraz więcej zakładów wykorzystuje mieszankę tych gazów jako paliwo do pieców. Problemem jest jednak uzyskiwanie mieszanki o odpowiednich właściwościach.
Niestabilne ciepło spalania
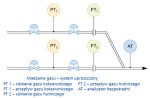
Mieszanie gazu-system uproszczony
Jednym ze wskaźników jakości mieszanki gazowej jest wartość jej ciepła spalania. 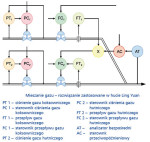
Mieszanie gazu-rozwiązanie zastosowane w hucie Ling Yuan
W trosce o bezpieczeństwo, maksymalizację wykorzystania energii oraz o środowisko, w procesie mieszania, należy przestrzegać pewnych zasad. Po pierwsze powinno się używać tak dużo gazu koksowniczego, jak to tylko możliwe, gdyż wartość jego ciepła spalania jest pięć razy wyższa niż w przypadku gazu hutniczego, z którym jest mieszany. W normalnych warunkach nie ma potrzeby sterowania jego przepływem. Po drugie gazy należy mieszać w ten sposób, aby uzyskać stabilną wartość ciepła spalania.
Ponadto trzeba pamiętać, że piec koksowniczy i hutniczy pracują w dynamicznym środowisku produkcyjnym, w związku z czym ilość gazu, który produkują, może ulegać znacznym zmianom. Gdy ciśnienie gazu koksowniczego jest zbyt wysokie, zawór 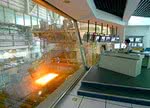
Problem automatycznego pomiaru i kontroli wartości grzewczej uzyskiwanej mieszkanki we wszelkich warunkach operacyjnych doczekał się w końcu rozwiązania. Firma CyboSoft opracowała algorytm, który pozwala na bezpośrednie obliczanie wartości grzewczej przy użyciu czujników programowych. W trybie automatycznym, czujnik umożliwia systemowi na pracę ciągłą – tj. 24 godziny na dobę, 7 dni w tygodni i bez konieczności wykorzystywania bezpośredniego analizatora. Ten ostatni używany jest jedynie do kontroli i kalibracji obliczonej wartości.
MFA zamiast PID
Omawiane rozwiązanie wykorzystuje stworzoną i opatentowaną przez CyberSoft technologię bezmodelowych sterowników adaptacyjnych – MFA (model-free adaptive). Mają one szereg przewag nad nadal dominującymi w procesach przemysłowych, liczącymi sobie już ponad pół wieku, sterownikami PID. Zastosowanie MFA w warunkach oscylacji pozwala na szybką stabilizację systemu. Sterowniki te są w stanie poprawić sytuację, w której znajduje się system w sposób szybszy i lepszy niż PID. Lepsza kontrola oznacza zwiększoną stabilność procesu, wyższą efektywność produkcyjną i zysk, a także mniejsze straty surowca i energii.
MFA pozwala na sterowanie skomplikowanymi systemami bez konieczności stosowania ich modeli. Nie jest potrzebna dokładna znajomość procesu i jego dynamiki a priori, co często jest bardzo trudne, o ile w ogóle możliwe, do osiągnięcia, ze względu na dużą dynamikę i stopień złożoności wielu operacji przemysłowych. MFA dobrze sprawdza się w przypadku procesów nieliniowych, a także takich, na które wpływ ma wiele zmiennych lub w których występują duże opóźnienia. Ponieważ MFA nie wymaga przeprowadzania fazy treningowej, można go uruchomić w dowolnym momencie, natychmiast przejmując kontrolę nad procesem. Inną zaletą tego rozwiązania, jest fakt że po zainstalowaniu nie ma potrzeby dopasowywać ustawień sterownika.
Budowa MFA
MFA składa się z dynamicznego bloku liniowego, który pełni rolę sterownika ze sprzężeniem zwrotnym. Blok dynamiczny stanowi pewien system wejścia/wyjścia. Celem sterowania jest uzyskanie takiej wartości na wyjściu, żeby zminimalizować błąd między wartością zadaną i mierzoną zmiennej procesowej.
Blok dynamiczny zawiera zbiór współczynników wagowych oznaczanych jako wij oraz hi, których wartości można zmieniać w zależności od potrzeb w celu regulacji nieliniowych funkcji bloku. Uczący się algorytm aktualizujący wartości współczynników wagowych ma również na celu minimalizację błędu, między wartością zadaną a mierzoną zmiennej procesową. Wynika z tego, że adaptacja współczynników wagowych może pomóc sterownikowi w minimalizacji błędu.
Sterownik MFA pamięta część danych procesowych, dostarczając w ten sposób cennych informacji o dynamice procesu. Dla porównania, cyfrowa wersja sterownika PID pamięta tylko aktualną i dwie poprzednie próbki.
Nie tylko huta
Na zakończenie warto wspomnieć, że technologia MFA ma dosyć szerokie zastosowanie – znacznie szersze niż do regulowania składem mieszanki hutach. Z CyfoSoft współpracują firmy takie, jak Siemens, National Instruments czy Sixnet. Wiele wskazuje na to, że ich liczba będzie się zwiększać.
Marek Krajewski