W konsekwencji liczba wypadków przy pracy w Europie w ciągu ostatnich lat nieustannie spada – przykładowo w Niemczech o ponad 50% w ciągu ostatnich 10 lat. W artykule przedstawiamy niektóre z najważniejszych aspektów europejskiego podejścia na przykładzie bezpieczeństwa maszyn.
ODPOWIEDZIALNOŚĆ PRODUCENTÓW
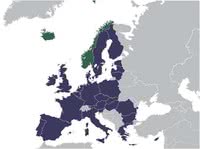
Rys.1.Podejście europejskie oznacza legislację związaną z wymaganiami dotyczącymi bezpieczeństwa i higieny pracy we Wspólnocie Europejskiej (27 krajów) i 4 krajach europejskich nienależących do UE, w których jednakże przyjęto w prawie krajowym legislację UE
Jedną z najważniejszych różnic jest złożenie odpowiedzialności za przestrzeganie odpowiednich zobowiązań bezpośrednio na barki producentów wyposażenia roboczego, tj. producentów maszyn. Jeżeli producent ma siedzibę poza Unią Europejską, musi ustanowić przedstawiciela na terenie UE, który będzie odpowiedzialny za spełnienie wspomnianych zobowiązań.
Oznacza to, że wyrób może zostać wprowadzony do obrotu w sposób legalny jedynie wówczas, gdy spełnia określone wymagania dotyczące zdrowia i bezpieczeństwa. Dzięki temu wymagań tych nie muszą brać pod uwagę użytkownicy maszyn, ponieważ zostały one już uwzględnione przez producenta (danej maszyny).
Oczywiście użytkownikom również stawia się wymagania, ale są one dodatkowe – np. związane ze środowiskiem pracy. Uczynienie producentów odpowiedzialnymi za wyroby wpływa w identyczny sposób na wszystkich konkurentów, wymuszając umieszczanie na rynku wyłącznie bezpiecznych wyrobów, a więc z punktu widzenia konkurencji procedura taka jest sprawiedliwa. Ponadto z punktu widzenia skuteczności i efektywności producentowi najłatwiej jest spełnić wymagania związane z bezpieczeństwem.
Późniejsze wprowadzenie odpowiednich elementów przez użytkowników jest dużo trudniejsze. W tym kontekście producent ponosi odpowiedzialność przed organami nadzoru rynkowego, które mają prawo do nałożenia rozmaitych sankcji, aż do wycofania wyrobów ze sprzedaży lub wycofania z rynku; jak również przed klientami, firmami ubezpieczeniowymi i stronami trzecimi z kompensatą strat, które mogły spowodować niebezpieczne wyroby.
ZNACZENIE DYREKTYW RADY EUROPEJSKIEJ
Wdrażanie omawianej legislacji realizowane jest poprzez dyrektywy Rady Europejskiej, których treść musi być przenoszona do prawa poszczególnych państw członkowskich Unii Europejskiej, przy czym przepisy krajowe nie mogą być ani mniej, ani bardziej surowe niż dyrektywa.
Przedmiotem dyrektyw Rady UE jest wskazanie kluczowych wymagań dotyczących zdrowia i bezpieczeństwa związanych z określonymi wyrobami (wymienianymi normalnie w załącznikach) oraz obowiązujących procedur prawnych pozwalających na sprawdzenie zgodności wyrobu z tymi wymaganiami (tak zwana procedura zgodności CE, z końcowym wskazaniem za pomocą oznaczenia CE wyrobu. W przypadku maszyn należy przestrzegać obecnie dyrektywy Rady WE 98/37/WE, zaś w niedalekiej przyszłości dyrektywy 2006/42/ WE (wchodzącej w życie w grudniu 2009 r.).
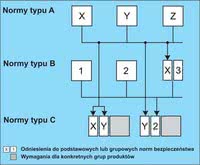
Rys.2.Powiązania pomiędzy europejskimi normami dotyczącymi bezpieczeństwa maszyn
ZNACZENIE NORMALIZACJI EUROPEJSKIEJ
Cechą wspomnianych dyrektyw Rady Europejskiej oraz zawartych w nich kluczowych wymagań dotyczących zdrowia i bezpieczeństwa – np. wskazanych w Załączniku 1 do europejskiej Dyrektywy Maszynowej – jest to, że formułują one jedynie cele ochrony w stosunkowo abstrakcyjnej formie.
Jest to jednakże zgodne z polityką świadomego samoograniczania UE, ponieważ Komisja Europejska pozostawiła szczegółowe opracowanie, wskazanie rozwiązań, opcji i pomoc w interpretacji sposobów spełniania podstawowych wymagań europejskim organom normalizacyjnym – CEN i CENELEC. Jednocześnie, dzięki współpracy z międzynarodowymi organizacjami normalizacyjnymi, takimi jak ISO i IEC, uniknięto sytuacji, w której określone wymagania europejskie różniłyby się od wymagań stosowanych w pozostałych rejonach świata. Na tym tle z inicjatywy Komisji Europejskiej stworzono nowy, całościowy zbiór tzw. norm zharmonizowanych, opublikowanych w Dzienniku Urzędowym UE.
Zachowanie zgodności z normami zharmonizowanymi pozwala na założenie, że spełnione zostały kluczowe wymagania dotyczące zdrowia i bezpieczeństwa zawarte w odpowiedniej dyrektywie. W obszarze bezpieczeństwa maszyn rozróżnia się, w postaci struktury hierarchicznej, normy typu A, B i C:
a) Normy typu A dotyczą fundamentalnych koncepcji dotyczących wszystkich maszyn; przykładem tej kategorii jest norma PN-EN ISO 12100-1 – Bezpieczeństwo maszyn – Pojęcia podstawowe, ogólne zasady projektowania – Część 1: Podstawowa terminologia, metodyka;
b) Normy typu B – Normy typu B1 dotyczą aspektów związanych z bezpieczeństwem, odnoszących się do zasięgu działania maszyn, takich jak np. bezpieczne odległości (PN-EN 999 – Maszyny – Bezpieczeństwo – Umiejscowienie wyposażenia ochronnego ze względu na prędkości zbliżania części ciała człowieka); – Normy typu B2 dotyczą elementów lub urządzeń, takich jak urządzenia bezpieczeństwa, które są stosowane w wielu zróżnicowanych maszynach; przykładem może być tu norma PN-EN 1088 – Maszyny – Bezpieczeństwo – Urządzenia blokujące sprzężone z osłonami – Zasady projektowania i doboru;
c) Normy typu C to tak zwane normy „pionowe”, obejmujące jeden typ maszyny np.: PN-EN 12750 – Bezpieczeństwo obrabiarek do drewna – Frezarki czterostronne. Niemniej jednak zasady i regulacje zawarte w normach nie są ostateczne. Możliwe jest niezależne stosowanie odmiennych rozwiązań, jeżeli gwarantują one co najmniej ten sam stopień bezpieczeństwa co normy EN. Z tego punktu widzenia normy EN interpretujące europejską dyrektywę w sprawie maszyn działają jako miara (możliwego) stopnia bezpieczeństwa, jaki należy osiągnąć.
ZASADY INTEGRACJI BEZPIECZEŃSTWA
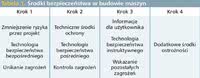
Tabela 1. Środki bezpieczeństwa w budowie maszyn
Zapewnienie, że bezpieczny wyrób (np. maszyna) jest zgodny z regulacjami dotyczącymi zgodności CE, wymaga kilku bardzo podstawowych kroków. Kroki te znane są jako analiza zagrożeń (ryzyka), ocena zagrożeń (ryzyka) i wreszcie – oszacowanie zagrożeń (ryzyka).
Z punktu widzenia inżynierów odpowiedzialnych za bezpieczeństwo maszyn bardzo przydatny opis znaleźć można w normie PN-ISO 12100-1/-2. W szczególności analiza zagrożeń może zostać wykonana za pomocą różnych list kontrolnych, ponadto istotną pomoc przy przeprowadzaniu analizy zagrożeń stanowić może norma PN-EN ISO 14121-1:2008 – Maszyny – Bezpieczeństwo – Zasady oceny ryzyka. Wreszcie, co nie mniej ważne, normy C (normy dotyczące konkretnych wyrobów) obejmują poszczególne aspekty zarządzania zagrożeniami dla różnych typów maszyn i dzięki temu również stanowią nieocenioną pomoc.
HIERARCHIA ŚRODKÓW SŁUŻĄCYCH POPRAWIE BEZPIECZEŃSTWA
W tym kontekście integracja bezpieczeństwa oznacza przestrzeganie pewnych zasad mających na celu wyeliminowanie zagrożeń (a przy przynajmniej ich zminimalizowanie) w przewidywanym czasie życia maszyny, począwszy od jej montażu, po końcowy demontaż oraz, oczywiście, z uwzględnieniem normalnego trybu pracy automatycznej, ale także specjalnych trybów pracy, jak również z uwzględnieniem dających się przewidzieć okoliczności i możliwości nieprawidłowego użycia.
Wybierając najbardziej odpowiednie rozwiązanie, producent musi postępować według przedstawionych kroków:
1. Wyeliminować lub maksymalnie zmniejszyć ryzyko (bezpieczny projekt i budowa maszyny),
2. Zastosować konieczne środki ochronne dotyczące ryzyka, których nie dało się wyeliminować,
3. Poinformować użytkowników o ryzyku, które pozostało z powodu braków zastosowanych środków ochronnych; wskazać, czy wymagane jest specjalne szkolenie i określić konieczność stosowania osobistego sprzętu ochronnego.
Prawo wymaga przestrzegania powyższej kolejności działań. Stąd przykładowo instrukcja ostrzegawcza nigdy nie może zastąpić urządzeń blokujących jako ochrona operatorów przed niebezpiecznymi ruchami, a urządzenia stopu awaryjnego stanowić mają wyłącznie dodatkowy środek zabezpieczający.
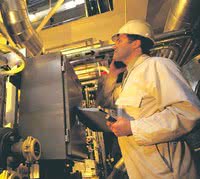
Fot.1.Wymagania UE dotyczące maszyn: budowa niestwarzająca zagrożenia dla osób w trakcie całego cyklu życia maszyny
OCENA RYZYKA I GRAF RYZYKA
W szczególności w przypadku stosowania środków ochronnych w postaci osłon zabezpieczających i innych urządzeń technicznych, np. stopu awaryjnego, konieczne jest rozważenie dodatkowo sytuacji, jakie mogą wystąpić w przypadku awarii lub niewłaściwego zadziałania tych środków. Jeżeli awaria lub zakłócenie mogą spowodować powstanie niebezpiecznej sytuacji, wówczas konieczne jest użycie dalszych środków, w zależności od ryzyka związanego z danym zastosowaniem.
Poprzez oszacowanie ryzyka należy określić odpowiedni poziom zapewniania bezpieczeństwa. Czynniki, które należy wziąć pod uwagę, obejmują:
– prawdopodobieństwo obrażeń lub szkód na zdrowiu (poważność obrażenia),
– częstotliwość i czas trwania narażenia na niebezpieczeństwo (czas i częstotliwość przebywania operatorów w strefie roboczej maszyny),
– możliwość uniknięcia zagrożenia przez operatora dzięki własnej reakcji.
Wynik tych rozważań jest wymagany obecnie dla osiągnięcia określonej kategorii bezpieczeństwa. Taką kategorią może być:
– CC – zgodnie z PN-EN 954-1:2001 – Maszyny – Bezpieczeństwo – Elementy systemów sterowania związane z bezpieczeństwem – Część 1: Ogólne zasady projektowania,
– poziom wydajności (PL) zgodnie z PN-EN ISO 13849-1:2008 – Bezpieczeństwo maszyn – Elementy systemów sterowania związane z bezpieczeństwem – Część 1: Ogólne zasady projektowania),
– poziom nienaruszalności bezpieczeństwa (SIL) zgodnie z PN-EN 62061:2008 – Bezpieczeństwo maszyn – Bezpieczeństwo funkcjonalne elektrycznych, elektronicznych i elektronicznych programowalnych systemów sterowania związanych z bezpieczeństwem oraz PN-
-EN 61508-1:2004 – Bezpieczeństwo funkcjonalne elektrycznych/elektronicznych/ programowalnych elektronicznych systemów związanych z bezpieczeństwem – Część 1: Wymagania ogólne.
CC, PL i SIL wskazują jakość funkcji bezpieczeństwa, np. ich odporność i tolerancję w przypadku niebezpiecznych awarii i zakłóceń, zachowanie w przypadku problemów, jak również działanie związane z wykrywaniem niebezpiecznych awarii w trakcie ich powstawania (przed wystąpieniem kolejnych awarii) oraz unikaniem kumulacji błędów.
ELEMENTY BEZPIECZEŃSTWA – STAN OBECNY
Z uwagi na duże znaczenie bezpieczeństwa maszyn pojawiło się kilku znanych dostawców, zapewniających szeroki asortyment elementów bezpieczeństwa spełniających europejskie wymagania prawne. Ponadto europejskie podejście do bezpieczeństwa i higieny pracy będzie coraz szerzej akceptowane na świecie, ponieważ ma ono jedną znaczącą przewagę, którą jest stopień konsolidacji sposobu radzenia sobie z zagadnieniem (a nie tylko wymaganie przestrzegania celów), jak również złożenie ciężaru odpowiedzialności na producentów (a nie pozostawianie go tylko na barkach użytkowników).
Jedną z nich jest Grupa Schmersal, dostawca elementów bezpieczeństwa i systemów zapewniających funkcjonalne bezpieczeństwo maszyn. Klienci mają do dyspozycji kompletny program urządzeń służących do ochrony operatorów przed niebezpiecznymi ruchami prawie każdej maszyny.
Klienci mogą wybierać urządzenia zgodnie z indywidualnymi wymaganiami, na przykład:
– do monitorowania ruchomych osłon bezpieczeństwa przez urządzenia wykorzystujące różne technologie, z blokadą lub bez,
– do wykrywania dostępu do niebezpiecznych obszarów za pomocą optoelektronicznych urządzeń ochronnych, np. kurtyn i barier świetlnych bezpieczeństwa lub skanerów,
– do unikania niebezpiecznych sytuacji dzięki stosowaniu naciskowych urządzeń bezpieczeństwa (maty i listwy) lub paneli dwuręcznych bezpieczeństwa,
– bezpiecznego przetwarzania sygnałów przez sterowniki PLC z funkcją bezpieczeństwa, systemy magistralowe (np. ASi) lub moduły przekaźnikowe bezpieczeństwa.
Artykuł autorstwa specjalistów z firmy Schmersal (www.schmersal.pl)