Przemysłowe sieci komunikacyjne zastępują konwencjonalne oprzewodowanie we wszystkich nowoczesnych instalacjach, ponieważ oferują zasadnicze korzyści: pozwalają oszczędzać czas i pieniądze, są o wiele łatwiejsze do zaprojektowania, gwarantują większą elastyczność i funkcjonalność (indywidualny dobór parametrów), a także umożliwiają szybką lokalizację i diagnostykę usterek.
Obecnie te same korzyści są dostępne w mniej skomplikowanych urządzeniach, które dotychczas były sterowane za pomocą tradycyjnego oprzewodowania umieszczonego w rozdzielnicach, a w przypadku instalacji zewnętrznej - nawet na zewnątrz. W tym artykule Heribert Einwag, menedżer produktu w Eaton, omawia, skąd bierze się przywiązanie do konwencjonalnego oprzewodowania.
Fot. tytułowa: Prowadzenie przewodów od punktu do punktu jest bardzo kosztowne i podatne na błędy |
MOŻLIWOŚCI OBNIŻENIA KOSZTÓW
Czas to pieniądz, jednak o ile koszty materiałów są względnie stałe, o tyle czas projektowania już nie. Można go skracać na różne sposoby, na przykład stosując znormalizowany układ lub zastępując elementy sterowania wyświetlaczem z ekranem dotykowym. Czas wykonywania połączeń znacznie się skraca również dzięki zastąpieniu typowych zacisków śrubowych zaciskami sprężynowymi typu cage clamp (bez śrub).
Montaż można przyspieszyć, stosując gotowe wiązki przewodów, których dodatkową zaletą jest znaczne zmniejszenie nakładu pracy i ryzyka pomyłek. Ponadto zautomatyzowanie powtarzalnych czynności, takich jak ściąganie izolacji i oznaczanie przewodów, może znacznie poprawić jakość i dokładność oraz oszczędzić czas. Wszystkie te strategie są szczególnie korzystne dla producentów standardowych (powtarzalnych) maszyn łączących się w jednym pulpicie sterowniczym.
OPRZEWODOWANIE KONWENCJONALNE - WYZWANIA
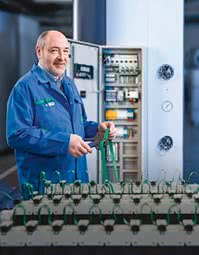
Fot. 2. Zastosowanie inteligentnych technologii oprzewodowania i komunikacji ułatwia wykonanie połączeń i zapewnia oszczędność miejsca
Aby elektromonter wiedział, jak połączyć moduły we/wy sterownika PLC z odpowiednimi stycznikami, zaciskami przycisków, czujnikami i inną aparaturą, nawet w przypadku stosunkowo prostej szafy sterowniczej, musi zwykle otrzymać schemat elektryczny. Przygotowanie takiego schematu może być bardzo czasochłonne dla projektantów, lecz zapewnia on zgodność instalacji w przypadku większej liczby szaf. Przy dużej liczbie przewodów poprowadzonych blisko siebie nietrudno jednak o pomyłkę.
Aby maksymalnie ograniczyć ryzyko przeoczenia połączenia, stosuje się często szczegółowe schematy oprzewodowania. Elektromonter wciąż jednak musi odczytywać schemat i zwykle zaznaczać na nim każde fizycznie wykonane połączenie. Jest to żmudna i czasochłonna, lecz niezbędna czynność, która pozwala uniknąć problemów na etapie prób funkcjonalnych.
Gdy przewody są podłączone do urządzeń sterujących umieszczonych na przykład na drzwiach szafy, wymagany jest dodatkowy czas na odpowiednie owinięcie i ułożenie przewodów w taki sposób, aby nie przeszkadzały w otwieraniu i zamykaniu drzwi, a sama wiązka nie była narażona na uszkodzenia.
Po wykonaniu połączeń wciąż jeszcze w ostatniej chwili mogą być wprowadzane zmiany, na przykład gdy klient zażyczy sobie dodania lub usunięcia komponentów, funkcji lub opcji. Zmiany te należy uwzględnić, zanim szafa opuści zakład produkcyjny producenta maszyny.
Nawet po zainstalowaniu szafy w miejscu przeznaczenia mogą wystąpić inne problemy. Technicy mogą wprowadzić zmiany w programie sterowania lub zainstalować dodatkową aparaturę, która będzie wymagać dodatkowego oprzewodowania we/wy albo doprowadzenia przewodów zasilających.
Zmiany oprzewodowania, układu i programu sterowania mogą nie być udokumentowane. W zależności od warunków umowy producent maszyny może jednak być nadal odpowiedzialny za szafę sterowniczą, niezależnie od zmian wprowadzonych w miejscu instalacji.
POPRAWA ŁĄCZNOŚCI SZAFY STEROWNICZEJ
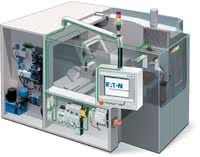
Fot. 3. Inteligentne rozwiązania zapewniają elastyczność konstrukcji maszyny wewnątrz i na zewnątrz szafy, skracając czas podłączenia, sprawdzenia i odbioru nawet o 85%
Bezpowrotnie minęły już czasy, kiedy - zanim wprowadzono sieci komunikacyjne / magistrale typu fieldbus - połączenie pomiędzy szafami sterowniczymi wymagało prowadzenia. Sieci komunikacyjne i zdalne moduły we/wy pozwoliły je wyeliminować, co spowodowało znaczny wzrost produktywności w układach i instalacjach sterowania. Pozostałe oprzewodowanie pomiędzy zdalnym systemem we/wy oraz podłączoną rozdzielnicą zostało znacznie ograniczone.
Sieć komunikacyjna (fieldbus) umożliwia połączenie jednym przewodem wielu urządzeń, dzięki czemu liczba przewodów pomiędzy szafą sterowniczą a urządzeniami znacząco spadła. Jednak wewnątrz szaf nadal stosuje się zwykłe oprzewodowanie, które można przyrównać bezpośrednio do rozwiązań starego typu. Dlaczego tak się dzieje?
Po części dlatego, że skoro ciągi połączeń przewodów zewnętrznych są długie i kosztowne w wykonaniu, potencjalne oszczędności wynikające z ich wyeliminowania były wyższe niż te, które można osiągnąć, eliminując konwencjonalne oprzewodowanie szaf. Wyznaczało to atrakcyjność systemów fieldbus w zastosowaniach poza szafami, nawet jeśli technologia ta była porównywalnie droga i skomplikowana w użyciu.
Pierwszą reakcją na to może być myśl o dostosowaniu istniejących sieci komunikacyjnych do użytku wewnątrz szafy sterowniczej. W praktyce tak się już robi w przypadku skomplikowanych urządzeń, takich jak układy łagodnego rozruchu, przemienniki częstotliwości i panele dotykowe. Technologia ta nie jest jednak stosowana w przypadku prostych urządzeń rozdzielczych. Wynika to z wysokich kosztów wykonania systemu fieldbus, a ponadto w większości przypadków jego pełna funkcjonalność nie jest potrzebna.
O wiele lepszym rozwiązaniem jest inteligentny system oprzewodowania i łączności, który opiera się na rozwiązaniach fieldbus i został opracowany specjalnie do użytku wewnątrz szaf, a z założenia umożliwia również podłączenie urządzeń zewnętrznych. Rozważmy sposób oprzewodowania szafy sterowniczej, który umożliwia podłączenie standardowych elementów sterowania silnikiem, eliminuje większość połączeń fizycznych, skraca czas projektowania, montażu, sprawdzania i rozruchu, a jednocześnie pozwala zmniejszyć rozmiary szafy i zapewnia połączenie z sieciami przemysłowymi.
Obecnie dostępne są systemy oprzewodowania urządzeń wykorzystujące inteligentne moduły, które łączy się z typowymi elementami sterowania silnikami, takimi jak styczniki, rozruszniki i inne urządzenia. Takie inteligentne moduły łączy się płaskim przewodem wielożyłowym z modułem bramki, który z kolei podłączony jest do standardowej sieci komunikacyjnej sterownika PLC.
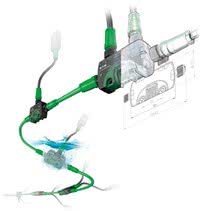
Fot. 4. Skomplikowane i podatne na błędy połączenia od punktu do punktu to już przeszłość - wszystkie urządzenia w maszynie można połączyć za pomocą prostych złączy wtykowych
Systemy oprzewodowania urządzeń z wbudowanym zasilaczem pozwalają wyeliminować większość połączeń przewodowych pomiędzy modułami we/wy PLC a rozrusznikami silnikowymi i urządzeniami obwodów sterowania. Można również wyeliminować instalowane dotychczas wejścia/wyjścia kojarzone zwykle ze sterowaniem rozrusznikami silnikowymi i urządzeniami sterowania.
Ponieważ do sprawdzenia jest tylko jeden płaski przewód, można znacznie skrócić czas montażu szafy i praktycznie wyeliminować czas potrzebny na próby. Wskaźniki diagnostyczne modułów komunikacyjnych mogą prezentować stan sieci, co jeszcze bardziej skraca czas kontroli i uruchomienia.
Z punktu widzenia utrzymania ruchu system oprzewodowania na poziomie urządzenia ma mniej połączeń, zatem regularne kontrole stanu połączeń trwają krócej. Inteligentne moduły przekazują informacje nie tylko cyfrowe, lecz również analogowe, a także bardziej specjalistyczne dane wspomagające diagnostykę i rozwiązywanie problemów.
Po połączeniu elementów sterowania za pomocą zintegrowanego systemu oprzewodowania wszelkie przeróbki i ingerencje w pierwotny układ szafy wymagają wiedzy i są od razu widoczne. Dlatego też mniejsze jest prawdopodobieństwo takich ingerencji, co pozwala chronić własność intelektualną producenta maszyny oraz zachować początkową fachowość i jakość wykonania szafy.
KONSTRUOWANIE INTELIGENTNIE STEROWANYCH MASZYN
Systemy oprzewodowania na poziomie urządzeń skracają czas projektowania, konstruowania, montażu i wykonania połączeń. Upraszczają również połączenia sterowania, rozszerzają możliwości diagnostyczne do poziomu urządzenia, zwiększają niezawodność, zgodność i elastyczność układu sterowania. Oszczędzają ponadto miejsce wewnątrz szafy sterowniczej, gdyż można znacznie ograniczyć liczbę przewodów i modułów we/wy.
Wszystkie te zalety i wiele innych korzyści oferuje inteligentny system oprzewodowania i łączności SmartWire-DT firmy Eaton. Stanowi on wygodną i ekonomiczną alternatywę dla konwencjonalnego oprzewodowania szaf, zapewniając nawet do 85% oszczędności finansowych i 40-procentową oszczędność miejsca, a także oferuje szeroką gamę zaawansowanych funkcji.
Eaton
www.eaton.pl